Il flusso di lavoro del processo di costruzione nella manifattura additiva con polveri metalliche è molto ampio e richiede numerose competenze ingegneristiche che consentono di svolgere attività molto diverse tra loro, dalla preparazione dei dati alla gestione delle polveri, tenendo sempre alta l’attenzione per la corretta applicazione delle procedure di sicurezza. Ecco in particolare come preparare la macchina di stampa per realizzare componenti metallici tramite processo Laser Powder Bed Fusion
Lavorare nel mondo dell’Additive Manufacturing, non significa soltanto studiare il design for additive, le “strutture lattice” o l’ottimizzazione topologica, soprattutto quando si ha a che fare con i metalli. È sicuramente molto importante parlare di preparazione dei dati, scelta dell’orientamento di costruzione e di ottimizzazione del design per ridurre i tempi di stampa e quindi i costi, oppure per evitare urti e deformazioni del pezzo, generando e ottimizzando le strutture di supporto necessarie. È altresì fondamentale parlare anche di gestione dei materiali e di movimentazione delle polveri metalliche per effettuare il carico/scarico della macchina di stampa, al fine di garantire la totale sicurezza dell’operatore.
I passaggi di un ciclo produttivo
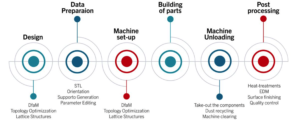
Nello schema mostrato nella Figura 1 è possibile osservare i vari step che permettono di aprire e chiudere un ciclo produttivo partendo dalla progettazione del componente desiderato, fino ad arrivare alla finitura e al controllo qualità sulla parte realizzata. Nel mezzo di questo ciclo troviamo le fasi che riguardano la preparazione della macchina di costruzione e che richiedono un’accurata gestione dei materiali e degli strumenti utilizzati. Prima di avviare un processo di costruzione spingendo il tasto Start è necessario predisporre la macchina all’avvio del processo.
Come prima cosa, è necessario caricare la polvere nel dispenser e svolgere le operazioni che consentono di avere la macchina pronta per costruire i componenti layer by layer. Tale operazione di carico richiede la movimentazione di contenitori pieni di polvere metallica che deve essere trasferita da un sistema all’altro e compattata manualmente dall’operatore. Successivamente è necessario caricare in macchina la piattaforma di costruzione che deve poi essere livellata e fissata in maniera opportuna per garantire stabilità e precisione del processo di costruzione. Ogni macchina che consente di realizzare parti mediante processo “a letto di polveri” può essere diversa e, dunque, può richiedere più o meno azioni manuali necessarie per prepararla all’avvio del processo di stampa.
Inizia la fase di stampa
Una volta che tutte queste operazioni sono concluse si può dar inizio alla fase di stampa durante la quale la macchina, a meno di problemi tecnici, risulta autonoma. Al termine del processo sarà nuovamente necessario l’intervento dell’operatore che dovrà scaricare la macchina rimuovendo la polvere inutilizzata e i componenti realizzati. Nell’esecuzione di queste operazioni è opportuno utilizzare strumenti adeguati come, ad esempio, un aspiratore venturi con il quale aspirare le polveri oppure un muletto per estrarre la piattaforma di costruzione con le parti prodotte sopra di essa.
Tutte queste fasi e operazioni possono sembrare all’apparenza molto semplici, ma nascondono una serie di rischi e pericoli relativi ai materiali e agli strumenti utilizzati che non devono essere sottovalutati e per i quali è bene essere preparati. Per poter operare su queste tipologie di macchine è fondamentale approfondire e conoscere tutta una serie di aspetti legati alla sicurezza. Inoltre, alle attività precedentemente descritte che possono essere definite ordinarie, se ne aggiungono delle altre straordinarie come, ad esempio, le attività di manutenzione da svolgersi sulla macchina movimentando filtri o sistemi accessori.
A tal proposito nei paragrafi successivi saranno trattati i concetti fondamentali per la sicurezza per poi analizzare quali sono i dispositivi di protezione individuale (DPI) necessari per operare a contatto con polveri metalliche. Inoltre, saranno analizzati i segnali che è possibile incontrare sui sistemi di produzione additiva (pericolo, warning, obbligo, etc.) e i rischi ai quali gli operatori saranno esposti durante lo svolgimento delle varie operazioni.
Le istruzioni di sicurezza
Le istruzioni di sicurezza servono fondamentalmente a evitare i rischi e a proteggere la nostra salute, la nostra vita e quella dei nostri collaboratori o di chi ci circonda. Nella produzione additiva metallica questo aspetto è fondamentale e dunque per poter lavorare è necessario considerare i seguenti aspetti.
In primo luogo, chiunque voglia operare su sistemi di metal AM deve aver seguito un training specifico e specializzato. Il training è necessario per spiegare e far comprendere quelli che sono i rischi, le dinamiche e il funzionamento della macchina. A tal proposito, è opportuno valutare le competenze di chi segue tale corso per attestare l’acquisizione delle conoscenze, la comprensione di tutti gli aspetti legati alla sicurezza e la capacità di operare in autonomia.
Inoltre, gli operatori devono seguire le istruzioni operative che vengono fornite dal costruttore e che sono illustrate sul manuale della macchina e devono conoscere e seguire i simboli di rischio e pericolo disposti sui materiali e sugli strumenti utilizzati. È fondamentale anche che chiunque lavori sulla macchina indossi i dispositivi di protezione individuale (DPI) e sapere quali indossare a seconda delle situazioni che si creano o a seconda delle operazioni che devono essere svolte.
Le macchine di produzione additiva sono dotate di sistemi in grado di garantire quanto più possibile la salute e la sicurezza dell’operatore. Ad esempio, ogni macchina è dotata di un fungo di emergenza, ossia un pulsante che, se azionato all’occorrenza, arresta la macchina bloccando le operazioni in fase di realizzazione, oppure di un sistema di chiusura in sicurezza che impedisce l’accesso a zone in cui la salute dell’operatore potrebbe essere messa a rischio. Oltre a questi sistemi, ogni macchina è caratterizzata da molti altri sistemi e sensori di sicurezza. Nonostante ciò, si possono creare situazioni particolari da gestire e per le quali è bene farsi trovare pronti.
Sicurezza e interventi di manutenzione
Tra le varie attività che devono essere svolte dagli operatori che lavorano nel metal additive manufacturing ce ne sono alcune che sono meno comuni e meno frequenti, ossia gli interventi di manutenzione. Tali operazioni, che possiamo definire straordinarie, richiedono dei dispositivi di protezione sostitutivi o aggiuntivi rispetto a quelli descritti precedentemente poiché ci sono rischi maggiori ai quali gli operatori sono esposti. Fondamentalmente le operazioni che implicano l’utilizzo dei DPI aggiuntivi sono quelle che richiedono la sostituzione e la movimentazione dei filtri.
Le operazioni di cambio filtri richiedono l’utilizzo di DPI avanzati perché c’è il rischio di incendio dovuto alla presenza di condensato. La polvere metallica vergine è un combustibile a rischio di incendio, mentre il condensato è polvere non combusta che però è stata esposta all’azione del laser e che dunque entra in uno stato altamente reattivo con l’ossigeno. Ciò che impedisce a questo particolato di realizzare la combustione è la mancanza di ossigeno dovuta alla presenza di Argon che inertizza i filtri. Nel momento in cui si effettuano le operazioni di sostituzione di quest’ultimi, il condensato entra in contatto con l’ossigeno e c’è il rischio che finisca la combustione. Poiché i filtri possono innescarsi reagendo con l’ossigeno, l’operatore deve indossare una maschera con visiera in grado di coprire interamente il viso, aumentando dunque la protezione dell’operatore rispetto a eventuali fiamme libere che potrebbero generarsi. Deve inoltre indossare guanti resistenti al caldo, necessari per evitare ustioni causate durante la manipolazione di oggetti che possono scaldarsi e salire di temperatura.
Il rischio chimico
Infine, c’è un ulteriore rischio che non è stato trattato finora, ossia il rischio chimico che può essere causato da due elementi differenti tra loro. Il primo è sicuramente relativo alle polveri metalliche, che costituiscono un pericolo per la salute a causa del possibile contatto con la pelle o con gli occhi. L’inalazione o la deglutizione delle polveri sono altamente dannose, in quanto le polveri sono cancerogene. Nel caso di contatto con le polveri è necessario lavarsi con acqua e sapone.
Abbiamo un rischio generico dovuto alle polveri di per sé e un rischio specifico di asfissia dovuto al particolato molto fine delle polveri, che può portare a irritazione della pelle e degli occhi. In caso di contatto con la pelle è consigliato il lavaggio con acqua e sapone. È fondamentale non disperdere le polveri nell’ambiente in cui si opera al fine di mantenerlo pulito ed evitare di incorrere in queste tipologie di rischi.
Un ulteriore rischio chimico è rappresentato dal gas inerte che si utilizza durante la realizzazione del processo di costruzione del componente. È possibile utilizzare diverse tipologie di gas a seconda del materiale processato come, ad esempio, l’azoto con gli acciai.
Il rischio chimico: il gas Argon
Nella maggior parte dei casi si utilizza gas Argon che può costituire un rischio chimico per una serie di motivi. L’Argon è un gas pesante e, quindi, sia quando le guarnizioni non sono perfette sia il tubo in arrivo dell’impianto presenta una perdita e scarica in ambiente, si favorisce il comportamento di tale gas a stratificarsi sul pavimento e a crescere dal basso verso l’alto, portando l’ossigeno in questa direzione. Quello che può succedere è che se, ad esempio, un operatore si abbassasse anche solo per allacciarsi le scarpe o per prendere “una boccata d’aria”, la sua saturazione scenderebbe molto rapidamente senza neppure rendersene conto e crollerebbe a terra.
L’Argon è un gas completamente inodore e insapore e pertanto i sintomi dovuti alla sua inalazione sono la perdita di mobilità e di cognizione. Le macchine di stampa lavorano sotto l’azione di gas inerte, sono equipaggiate con delle guarnizioni che sono soggette ad usura e sulle quali si ha poco controllo e ciò potrebbe favorire una perdita di Argon nell’ambiente in cui lavora l’operatore. È dunque opportuno rilevare costantemente la concentrazione di ossigeno presente, che solitamente è al 21%. Per fare ciò si utilizzano dei sensori sui quali è possibile impostare delle soglie di allarme, in grado di avvertire l’operatore nel caso in cui la concentrazione di ossigeno scendesse oltre un certo limite.
Conclusioni: sicurezza e procedure
Dunque, dopo aver visto tutti i rischi e i pericoli che si possono incontrare lavorando nel mondo del metal additive manufacturing, è facile pensare che sia molto complicato lavorare con tali tecnologie. In realtà, nel mondo industriale ogni tecnologia e processo presenta dei rischi che vanno evitati e/o gestiti. Per far ciò è necessario che gli operatori siano altamente istruiti, qualificati e consapevoli di tutto ciò che potrebbe accadere durante le varie fasi e operazioni che devono essere realizzate. È fondamentale operare utilizzando i dispositivi di protezione individuale che consentono di proteggere gli operatori dai vari pericoli ed è importante pianificare attentamente le varie fasi e operazioni che si intende realizzare, in maniera tale da rispettare tutte le procedure, le buone pratiche e i più elevati standard di sicurezza.