I controlli non distruttivi delle saldature sono un vero miracolo della tecnica: rendono visibile ciò che normalmente è nascosto ai nostri occhi. Grazie a loro, i difetti di colata o di saldatura non sono più una pericolosa incognita.
Alcuni di voi ricorderanno il film La Sindrome Cinese del 1979, con Micheal Douglas, Jane Fonda e Jack Lemmon: la trama ruotava attorno al pericolo nascosto in una centrale nucleare in California. Un subappaltatore senza scrupoli aveva contraffatto le radiografie di controllo delle saldature di una pompa di raffreddamento. Non vi sveliamo altri dettagli, in caso voleste dedicare una sera a (ri)guardare una pellicola che ha fatto la storia del cinema. Oltre a mettervi curiosità, questa premessa ci serve per introdurre l’argomento di questo articolo: i controlli non distruttivi. Strumento fondamentale per determinare la qualità di una saldatura, dalla loro introduzione hanno fatto passi da gigante.
I difetti di getto e saldatura
La saldatura è un processo tanto importante quanto delicato e variabile. Nella maggior parte dei casi, il giunto si può considerare omogeneo e con caratteristiche di resistenza teoriche, determinate in precedenza tramite test distruttivi. Sono molti i parametri da tenere sotto controllo, e altrettanti i tipi di difetto che possono verificarsi. Le imperfezioni sono sempre dietro l’angolo o, per meglio dire, sotto il cordone. Già, perché il difficile sta proprio qui: come scoprire qualcosa che è invisibile ad occhio nudo, oppure inglobato sotto qualche mm (o cm) di metallo? I più comuni difetti presenti nei getti di fusione e nelle saldature sono:
- cricche e delaminazioni
- mancanza di penetrazione o eccessi di penetrazione
- incollature e inclusioni di scoria o ossido
- inclusioni di tungsteno
- cavità, bolle e inclusioni gassose
Un giunto non omogeneo ha una resistenza inferiore a quella prevista, inoltre le inclusioni sono punti di invito alla rottura, soprattutto con sforzi oscillatori. Ogni imperfezione, per quanto piccola, può estendersi sotto sforzo fino a causare il cedimento dell’intero giunto. Nella maggior parte delle applicazioni la saldatura è sufficientemente sovradimensionata da contenere gli effetti di queste irregolarità, soprattutto nelle applicazioni non critiche.
In certi ambiti i margini di sicurezza sono più ridotti, per non parlare di quando è davvero il caso di non correre rischi. Pensiamo al settore aerospaziale, oppure all’industria nucleare (per richiamare la nostra introduzione): qui dobbiamo essere certi dell’assoluta perfezione della saldatura. Per i pezzi colati, il discorso è analogo: all’interno del prodotto si possono nascondere bolle di gas o cricche causate da un raffreddamento troppo veloce o non omogeneo.
Certo, possiamo prendere un campione e sezionarlo per controllarne l’interno. Questo ci direbbe qualcosa solamente su quello specifico pezzo, ma non su tutti gli altri.
E come si fa quando il prodotto è unico, come un razzo? Fortunatamente, anche qui scienziati e ingegneri hanno trovato molte strade per rendere visibile l’invisibile.
Liquidi penetranti
Questa tecnica è tra le più collaudate, essendo stata sviluppata a cavallo tra le due Guerre Mondiali. Si effettua cospargendo la superficie del giunto con un liquido colorato dotato di grande capillarità, che gli consente di entrare anche nelle cricche più sottili. Successivamente, l’area viene pulita e cosparsa con un mezzo di contrasto detto rivelatore. Questa seconda sostanza fa affiorare il liquido penetrante dalle crepe e lo rende maggiormente visibile. In questo modo, i difetti di saldatura diventano evidenti. In casi particolari si illumina la zona con raggi ultravioletti, che aumentano la visibilità del colorante.
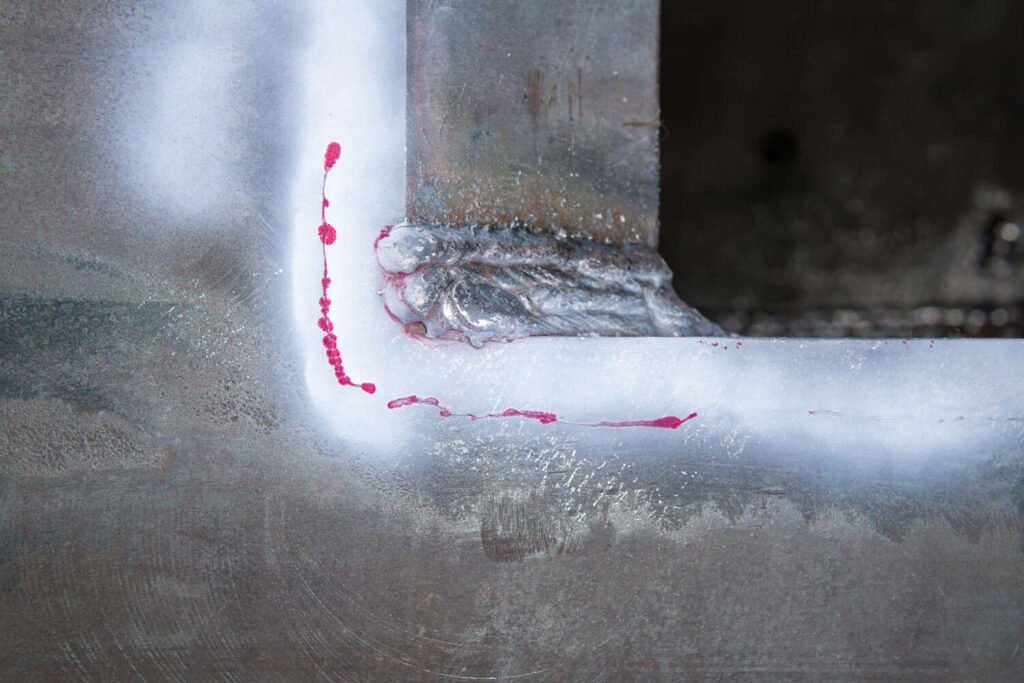
Questa tecnica è estremamente economica e veloce, ma vanno usate determinate precauzioni poiché sia i liquidi che il mezzo di contrasto possono comportare rischi per gli operatori. Il principale svantaggio dell’indagine con liquidi penetranti è ovviamente che può evidenziare solamente i difetti che sfociano in superficie, ma non fornisce nessuna informazione su crepe interne al materiale. Inoltre, non è utilizzabile con materiali porosi o chimicamente sensibili a queste sostanze.
La radiografia
Sin dalla scoperta dei raggi X, apparve chiaro come questa radiazione potesse trovare applicazione in ambito tecnologico. Un generatore di raggi X, oppure una sorgente naturale di raggi gamma (Cobalto-60, Iridio-192 o Cesio-137) produce fotoni ad alta energia che attraversano la zona da controllare. Dall’altro lato, un convertitore rileva l’intensità delle radiazioni trasmesse. Inizialmente si usava una pellicola sensibile, come per le radiografie mediche, ora sostituite da rilevatori elettronici.
Il metodo neutronico sfrutta invece un flusso di neutroni prodotto da un elemento radioattivo o da un acceleratore di particelle. I neutroni attraversano il pezzo e vanno a colpire una lastra di materiale apposito, il quale diventa temporaneamente radioattivo. Questa lastra viene quindi posta a contatto con un rilevatore sensibile ai raggi gamma, convertendo indirettamente spessore e densità del pezzo in una sorta di fotocopia radiografica.
In tutte e due le tecniche, la presenza di vuoti come cricche o pori all’interno dell’oggetto provoca una minore attenuazione del fascio di particelle rispetto ai punti dove il metallo è compatto. Un occhio esperto è in grado di capire tipologia e profondità del difetto. Se la cricca è perpendicolare al fascio non influenzerà in modo significativo la trasmissione delle radiazioni e perciò non sarà visibile nella radiografia.
Al contrario, un’imperfezione attraversata dalle radiazioni nel senso della lunghezza comporterà un’attenuazione minore e quindi una traccia più evidente. Per questo motivo, dove possibile e richiesto, si consiglia di effettuare più fotografie in modo ortogonale. L’uso di generatori di raggi X o di radionuclidi rappresenta un rischio intrinseco per gli operatori; richiede quindi personale esperto e procedure rigorose. Il suo uso è sempre più limitato a casi particolari, poiché non presenta vantaggi importanti rispetto ad altri metodi più sicuri e versatili.
Gli ultrasuoni
Anche le fondamenta delle tecniche di indagine tramite ultrasuoni sono state gettate tra le due Guerre. Il principio di funzionamento si basa su un generatore di onde a frequenza ultrasonica e un trasduttore piezoelettrico posto a contatto con il pezzo. La superficie dev’essere prima levigata, e va usato un gel o un olio apposito per assicurare il corretto accoppiamento acustico. È possibile usare lo stesso trasduttore per rilevare l’onda riflessa, oppure un altro sensore per rilevare l’onda che attraversa il materiale.
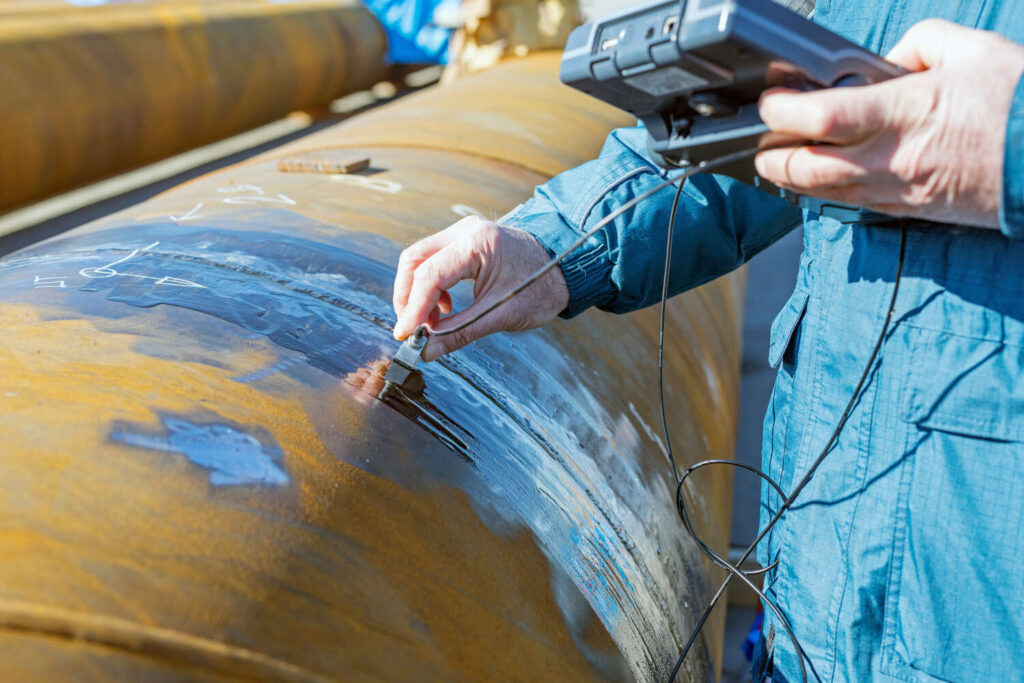
I difetti, sia cricche che pori, causano riflessioni o differenze nell’intensità del segnale, che possono quindi essere rilevati. Recentemente sono stati sviluppati i trasduttori EMAT (Electromagnetic Acoustic Transducer), in grado di generare onde ultrasoniche nei materiali conduttori anche senza essere fisicamente a contatto. Tramite una combinazione di magneti e bobine, fanno vibrare il metallo sfruttando la forza di Lorentz o la magnetostrizione. Questa proprietà consente di effettuare i test anche quando la superficie del pezzo non può essere levigata o quando le condizioni non consentono l’applicazione del gel di contatto.
I trasduttori possono essere disposti in configurazioni multiple (array), per generare una mappa più precisa dell’interno del componente. Grazie a tecniche di beam steering, pilotando in sequenza gli elementi possiamo rilevare la posizione delle imperfezioni senza dover effettuare più misurazioni distinte.
I controlli a ultrasuoni permettono di avere un riscontro immediato del test, senza dover attendere i tempi di sviluppo delle lastre radiografiche. Inoltre, non richiedono l’uso di pericolose sostanze radioattive e possono essere usati anche lavorando su un solo lato del componente. Per contro, necessitano di un’adeguata preparazione della superficie, possono generare risultati poco attendibili e hanno scarsa efficacia con materiali non omogenei o di forma irregolare.
Magnetoscopia
Questa tecnica di indagine prevede la magnetizzazione del pezzo; ciò avviene facendo circolare al suo interno una corrente elettrica di elevata intensità, oppure applicando un magnete permanente. In condizioni normali le linee del campo magnetico rimangono contenute all’interno del metallo. La presenza di irregolarità come cricche e pori genera una perturbazione nella distribuzione delle linee di forza, costringendole a disperdersi all’esterno. Cospargendo la superficie dell’oggetto con polveri magnetiche, queste tenderanno ad accumularsi in corrispondenza di questo flusso magnetico disperso. In questo modo il difetto nella saldatura o nella colata diventa visibile.
Le polveri magnetiche possono essere a secco oppure in sospensione in un mezzo liquido. Come per l’indagine con liquidi penetranti, le polveri magnetiche possono essere colorate oppure fluorescenti. Nel primo caso l’ispezione avviene in luce naturale, nel secondo il pezzo viene illuminato con raggi ultravioletti. Dopo il controllo, se necessario il pezzo viene fatto passare in un tunnel di smagnetizzazione per eliminare il campo magnetico. Questa tecnica non è applicabile su metalli amagnetici, come il rame o certi acciai; può essere difficile smagnetizzare completamente il materiale.
Correnti indotte
Nella sua forma più semplice, una bobina di filo conduttore viene alimentata con una corrente elettrica alternata. Quando la bobina si avvicina a un materiale conduttore, nel materiale vengono indotte correnti opposte a quelle della bobina, dette correnti indotte o correnti parassite. Le variazioni della conduttività elettrica e della permeabilità magnetica dell’oggetto in esame e la presenza di difetti provocano una variazione delle correnti parassite. Ciò genera una corrispondente variazione di fase e ampiezza, la quale può essere rilevata misurando le variazioni di impedenza della bobina rispetto al metallo omogeneo, indicando in modo indiretto la presenza di difetti.
Questa tecnologia è estremamente sensibile e può rilevare anche cricche molto sottili. Non richiede preparazione del pezzo e funziona anche al di sotto di vernice o ruggine. Tuttavia, permette di diagnosticare difetti solo nella zona superficiale: a causa dell’effetto pelle i campi elettromagnetici alternati si concentrano sulla parte esterna degli oggetti in metallo.
A differenza della radiografia o degli ultrasuoni, il controllo per correnti indotte si può usare solo sui materiali conduttori.
Martino Barbon