Questo studio effettuato da ricercatori cinesi propone un interessante confronto tra modelli teorici, alla base delle simulazioni ad elementi finiti, applicato su diversi provini reali, con l’obiettivo di prevedere le fratture sui componenti in lamiera.
La rivoluzione introdotta da Industria 4.0 è un tema di particolare rilevanza ed attualità per diversi settori. Le fabbriche moderne sfruttano sempre di più le moderne tecnologie digitali integrando sensori e connessioni sui macchinari di produzione. Si parla infatti di “sistemi ciberfisici” ovvero sistemi informatici in grado di interagire con il sistema fisico circostante.
Questo concetto è ben applicabile al mondo produttivo e, più in particolare, al mondo della lamiera. Le moderne tecnologie di Industria 4.0 permettono, ad esempio, di monitorare i sistemi produttivi garantendone elevate prestazioni operative e permettendo una collaborazione tra operatore, macchina e strumenti. Un’altra interessante possibilità offerta dalle tecnologie digitali è quella della simulazione.
Un processo produttivo può essere ricreato nel mondo digitale, così da poter prevedere i risultati ed ottenere componenti di qualità riducendo le fasi di sperimentazione e la variabilità del prodotto finale.
La frattura
Le fratture (o rotture) sono disgregazioni del materiale dovute a sollecitazioni. Per quanto riguarda i metalli le fratture possono essere distinte per natura in due macro-categorie: fragili o duttili. Nelle fratture fragili (a volte chiamate “fratture di schianto”) non si hanno visibili deformazioni, la rottura avviene in campo elastico. Diversa invece è la situazione per le fratture duttili: in questo caso prima della rottura si può osservare una notevole deformazione del materiale.
Queste fratture possono accadere frequentemente durante i processi di deformazione plastica, specialmente su componenti ottenuti da lamiere sottili, a causa di eccessive deformazioni localizzate. Il tema delle fratture duttili è infatti di particolare interesse nella formatura di lamiere leggere.
In ambiente industriale è fondamentale riuscire a prevedere ed evitare rotture su prototipi o componenti di produzione. Per questo negli ultimi anni sono stati sviluppati diversi modelli e criteri per prevedere le fratture duttili. Lo scopo principale dei criteri di frattura è quello di predire il livello di deformazione in cui si verifica la rottura e il sito di inizio. Solitamente viene definito un parametro relativo al materiale durante la trasformazione, il raggiungimento di un valore critico del parametro indica il verificarsi della frattura. Questo valore critico viene solitamente determinato tramite sperimentazioni in condizioni standard.
Uno dei principali criteri per prevedere le rotture duttili è quello inventato dal matematico tedesco Freudenthal. Tale criterio si basa sul calcolo del lavoro di deformazione plastica per unità di volume. Se il valore del parametro supera una soglia critica si prevede l’insorgere della frattura. Vista la disponibilità di numerosi criteri, gli autori della ricerca si propongono di effettuare un confronto, in diverse condizioni operative, per valutarne pregi e svantaggi in applicazioni reali.
Sperimentazione
I ricercatori cinesi, per studiare e confrontare i criteri di frattura, hanno deciso di utilizzare una lamiera di alluminio 2219-O dello spessore di 2 mm. Questo materiale, poiché viene ottenuto dal processo di laminazione, presenta caratteristiche anisotrope, ovvero che dipendono dalla direzione.
L’alluminio 2219-O ha una buona saldabilità, resistenza alla corrosione e alle fratture, per questo viene spesso impiegato per serbatoi di combustibili o nell’aerospazio. Il materiale è stato caratterizzato tramite prove a trazione lungo diverse direzioni. Altre misure sono state effettuate sui provini tramite un sistema di correlazione di immagini digitali (“DIC” o digital image correlation). Queste prove sono state eseguite con l’obiettivo di determinare i parametri necessari per tutti i criteri di frattura da confrontare.
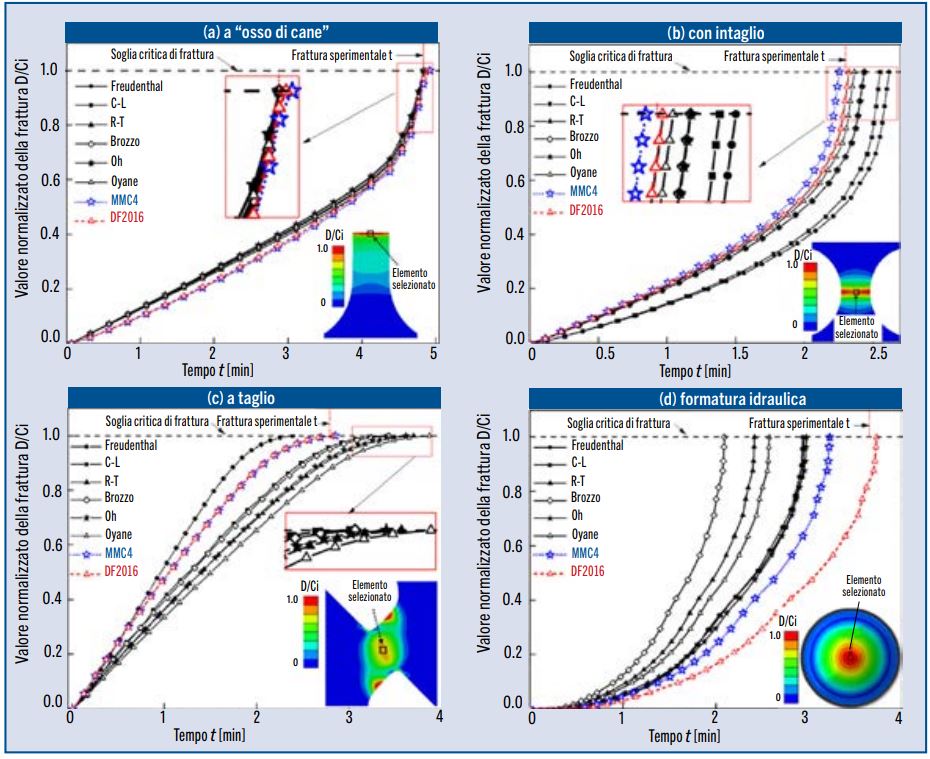
I modelli in grado di prevedere le fratture sui componenti necessitano infatti di parametri specifici relativi al materiale e la soluzione migliore, per ottenere stime affidabili e prossime alla realtà, è quella di caratterizzare il materiale studiato eseguendo tutte le prove necessarie. Per effettuare le simulazioni ad elementi finiti sono stati implementati modelli con i diversi criteri di frattura.
Questi modelli sono stati creati e tarati in ABAQUS/Explicit. Per effettuare un confronto in diverse condizioni operative sono stati sviluppati ed eseguiti diversi test su provini (mostrati in Figura 1).
Risultati
I principali otto criteri di frattura presenti in letteratura sono stati confrontati in una sperimentazione ibrida. Modelli teorici sono stati simulati a computer insieme a provini fisici sollecitati realmente. Il risultato è stato comparato dagli autori per riuscire a trovare vantaggi, svantaggi e il campo di applicazione ottimale per questi modelli teorici.
In Figura 2 è mostrato un confronto dei diversi criteri di frattura con il risultato sperimentale. Per quanto riguarda il provino a “osso di cane” i risultati proposti da tutti i criteri risultano essere simili e in accordo con il provino reale. Questo perché si tratta di un caso abbastanza semplice e spesso vicino alla definizione della soglia di frattura. Per il provino con intaglio i risultati teorici hanno maggiore variabilità. Il luogo della frattura è previsto correttamente, ma alcuni criteri meno evoluti (ad esempio il criterio di Freudenthal) presentano un ritardo.
Anche sui provini a taglio la posizione della frattura è identificata correttamente, ma solo i modelli più complessi ed evoluti sono in grado di predire accuratamente il momento della rottura. Sul componente ottenuto per formatura idraulica la frattura avviene al centro della lamiera. In questo caso solo uno dei criteri è in grado di effettuare una predizione valida. Tutti gli altri modelli teorici prevedono una frattura della lamiera che è anticipata rispetto alla realtà.
I risultati mostrano chiaramente le diverse prestazioni dei criteri di frattura. Infatti non è detto che un criterio sia valido in ogni condizione, accade piuttosto di avere modelli più o meno adatti alla situazione studiata. Trattandosi di modelli teorici il risultato dipende dalle assunzioni e dalle ipotesi che stanno alla base delle formulazioni. Chiaramente alcuni modelli più moderni e complessi (ad esempio quello qui indicato come “DF2016”) permettono di ottenere risultati migliori e più precisi.
Tuttavia per ottenere risultati più precisi è necessario utilizzare modelli di complessità crescente (anche dal punto di vista computazionale) e solitamente bisogna essere in grado di definire numerosi parametri. Risulta quindi necessario essere in grado di trovare il giusto compromesso tra la complessità della simulazione e la precisione dei risultati a seconda delle necessità specifiche.
Questo studio propone un interessante confronto tra modelli teorici, alla base delle simulazioni ad elementi finiti, applicato su diversi provini reali. Diverse soluzioni sono disponibili a seconda delle esigenze. I criteri più tradizionali risultano essere accurati per condizioni di trazione uniassiale. Per condizioni più complesse sono oggi disponibili altri criteri più evoluti in grado di offrire buone performance. In ogni caso è interessante notare la complessità e il lavoro che sta dietro ai moderni sistemi di simulazione.
La rivoluzione di Industria 4.0 ha permesso una grande diffusione di questi sistemi nel mondo industriale, ma non bisogna dimenticare i potenti sistemi che si nascondono dietro alle interfacce grafiche. Per questo è importante rimanere aggiornati e approfondire la conoscenza di questi sistemi per poterli sfruttare al meglio.
Fonte: Li, R., Zheng, Z., Zhan, M., Zhang, H., Cui, X., & Lei, Y. (2022). Fracture prediction for metal sheet deformation under different stress states with uncoupled ductile fracture criteria. Journal of Manufacturing Processes, 73, 531–543. https://doi.org/10.1016/j.jmapro.2021.11.023