Le soluzioni digitalizzate in chiave 4.0 e i sistemi dotati di automazione sono ormai iscritti nel codice genetico delle imprese specializzate nella lavorazione della lamiera sulle dimensioni più imponenti e rappresentano la risposta alle esigenze di clienti che chiedono massima precisione in tempi rapidi.
Gli investimenti compiuti per dare vita ad ambienti di fabbrica pienamente interconnessi e i budget destinati all’automazione danno buoni frutti e consentono alle imprese specializzate nel taglio e nella lavorazione dei grandi spessori di accrescere la loro competitività sul mercato. E dimostrano tutto il loro valore strategico proprio in un momento in cui il forte accento sulla sostenibilità e la riduzione degli impatti supporta la crescita di settori-clienti come quello del trattamento dei rifiuti.
A darne testimonianza sono le esperienze fatte da due player dalla vocazione diversa e accomunate però dall’attenzione all’innovazione tecnologica e dal continuo arricchimento del parco-macchine.
Più efficienza e precisione: ma questo è solo l’inizio
Fabio Biguzzi è il general manager della cesenate Siderflange che da non molto ha tagliato il traguardo dei quarant’anni di attività nel comparto della lavorazione lamiere. L’azienda è stata infatti fondata nel 1981 e, dai suoi esordi come contoterzista, si è specializzata nei processi di taglio e piega per le aziende locali. Oggi conta circa 50 addetti e vanta un volume d’affari annuo pari a 20 milioni di euro, e sia le sue superfici sia il suo parco di tecnologie sono andati accrescendosi coerentemente negli anni.
«È infatti imminente», ha detto Biguzzi a Lamiera, «l’inaugurazione di un nuovo stabilimento adiacente, dotato di un reparto specificamente dedicato all’ossitaglio. Siamo fortemente focalizzati sugli spessori e le dimensioni medio-grandi grazie alla presenza di una linea laser con taglio sino a 12 metri con tecnologia bevel, una linea plasma da 50 metri con due portali, anche questi con taglio bevel, un reparto piega dove possiamo arrivare a lunghezze sino a dieci metri per mille tonnellate complessive, e infine un reparto calandratura con possibilità di lavorare lamiere fino a 50 millimetri per tre metri di larghezza.
Gli impianti sono tutti di ultima generazione e anche la divisione ossitaglio che partirà a marzo 2023 è dotata di tre nuovi impianti con possibilità di taglio bevel e teste con mandrino per la foratura. L’automazione ha da tempo fatto capolino nelle sedi di Siderflange in qualità di prezioso supporto per la gestione dei flussi di lavoro, in particolare in vista dell’ottimizzazione dei processi, della movimentazione delle merci e relativo attraversamento degli spazi. Le soluzioni 4.0 implementate consentono di rispondere alle mutevoli esigenze della clientela.
Quel che chiede il mercato
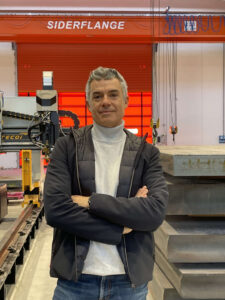
A un fornitore come quello di Pievesestina di Cesena il mercato chiede oggi di garantire «prodotti sempre più finiti» in ogni dettaglio, a testimonianza del fatto che, per competere sullo scenario attuale, «saper eseguire alla perfezione un semplice taglio a fiamma non basta più». Con frequenza crescente i committenti ricercano in un terzista un partner a 360° con la capacità di eseguire tutte le lavorazioni di taglio e deformazione oltre a realizzare fori di punta, lavorazioni meccaniche e di sabbiatura». Ma non solo: le specifiche richiedono sempre maggiori controlli sui materiali, prove meccaniche e certificazioni ultrasuoni.
È inoltre essenziale che, dall’inizio alla fine, il processo produttivo di una commessa sia completamente tracciabile. L’adesione convinta e piena alla filosofia della Quarta rivoluzione industriale è senz’altro un fattore agevolante quando la finalità è ottenere un monitoraggio totale su quanto si sta facendo, dalla ricezione merci fino allo stoccaggio del prodotto finito.
Sostenibili e digitalizzati
«Gli ERP e il gestionale di produzione tracciano la lamiera sin dall’accettazione, e seguono tutte le fasi del processo: dal nesting sino alla fine del ciclo», ha detto Biguzzi, «e gli operatori seguono nel loro lavoro le indicazioni fornite direttamente dall’ufficio tecnico. Gli impianti sono da noi cablati e interconnessi e riusciamo a monitorare lo stato di avanzamento delle commesse grazie a una piattaforma IT installata soltanto due anni fa, ma oggetto di continue migliorie e implementazioni».
Siderflange ha adottato un cruscotto intelligente per la verifica costante degli indicatori di prestazione, i cosiddetti Key performance index o KPI e ha l’obiettivo di arricchirne via via la gamma delle funzionalità, aggiungendone di nuove. Fra gli obiettivi c’è per esempio quello di mettere a budget le ore destinate alla piegatura, analogamente a quel che avviene per il taglio, in vista di una più accurata preventivazione dei tempi di attraversamento. «In generale», ha riflettuto Fabio Biguzzi, «vorremmo ottenere un surplus di efficienze e di efficacia anche nella programmazione e questo sempre in un’ottica di soddisfazione della clientela, che chiede e deve avere da noi risposte certe e precise.
«Le soluzioni 4.0», ha osservato l’intervistato, «ci hanno consentito di ottenere un maggior controllo di produzione, che riguarda sia i singoli processi, sia una tracciabilità precisa dei materiali lavorati e delle rimanenze, basti pensare che ogni particolare finito reca tutti i dati di identificazione: sia quelli del cliente sia quelli del certificato e colata di origine del materiale.
Questo, unito alla varietà delle lavorazioni che siamo in grado di eseguire, a un magazzino lamiere che spazia dagli strutturali agli alto-resistenziali, fino all’antiusura con spessori che arrivano a 300 millimetri è per noi il vero significato dell’essere partner del cliente e non un semplice fornitore».
Bando agli sprechi; via libera a formazione e ricerca
Automazione ed efficienza vanno a braccetto in casa Siderflange ma anche la sostenibilità ha sempre avuto un ruolo fondamentale e per certi versi si può dire che tutti questi aspetti si supportino reciprocamente. L’azienda sin dal 2008 si è dotata di un importante impianto fotovoltaico che attualmente raggiunge i 500 kilowatt e che, oltre ad abbattere i consumi interni, alimenta un impianto di autoproduzione dell’azoto necessario ai tre impianti di taglio laser.
Siderflange vanta una consolidata collaborazione con SSAB, essendo qualificata come HARDOX wearparts, e questo le ha consentito di maturare una notevole esperienza nella lavorazione di questo materiale e averne un ampio magazzino sempre a disposizione. È divenuta così fornitrice privilegiata dei player del riciclo, che lo utilizzano per i loro impianti. È un business che cresce d’importanza e affianca quelli storici dello oil &gas, del movimento-terra e del sollevamento. Siderflange conta di acquisire a breve una ulteriore pressa piegatrice da mille tonnellate per acciai alto-resistenziali, potenziando così un reparto dove l’automazione sta diventando fondamentale.
«Lo vediamo anche nelle fiere di settore, ove i costruttori», ha concluso Biguzzi, «espongono modelli dai controlli a bordo macchina sempre più intuitivi e fruibili che interagiscono con accompagnatori ed estrattori agevolando e migliorando sia la qualità del lavoro svolto sia la sicurezza sul posto di lavoro. Gli investimenti importanti di questi anni vanno infine di pari passo con la formazione dei dipendenti; particolare attenzione è data a questo aspetto, in quanto sono loro il vero motore dell’azienda.
Già da diversi anni vengono organizzati corsi di formazione in base alle mansioni, per creare sempre maggior consapevolezza del ruolo di ognuno e avere una partecipazione attiva nei processi produttivi».
Un sorso d’innovazione
Nata nel 1902 come fornitrice di impianti enologici la emiliana Officine Meccaniche Buzzi – sede a Novellara, terra d’origine della celebre band I Nomadi – si è col tempo orientata alle tecnologie di essiccazione per gli oleifici e le distillerie. Dall’inizio degli anni 2000, con l’acquisizione dei sistemi di taglio laser il range dei suoi servizi si è ampliato andando a includere le lavorazioni conto terzi per i settori del recupero dei rifiuti e della pulizia stradale.
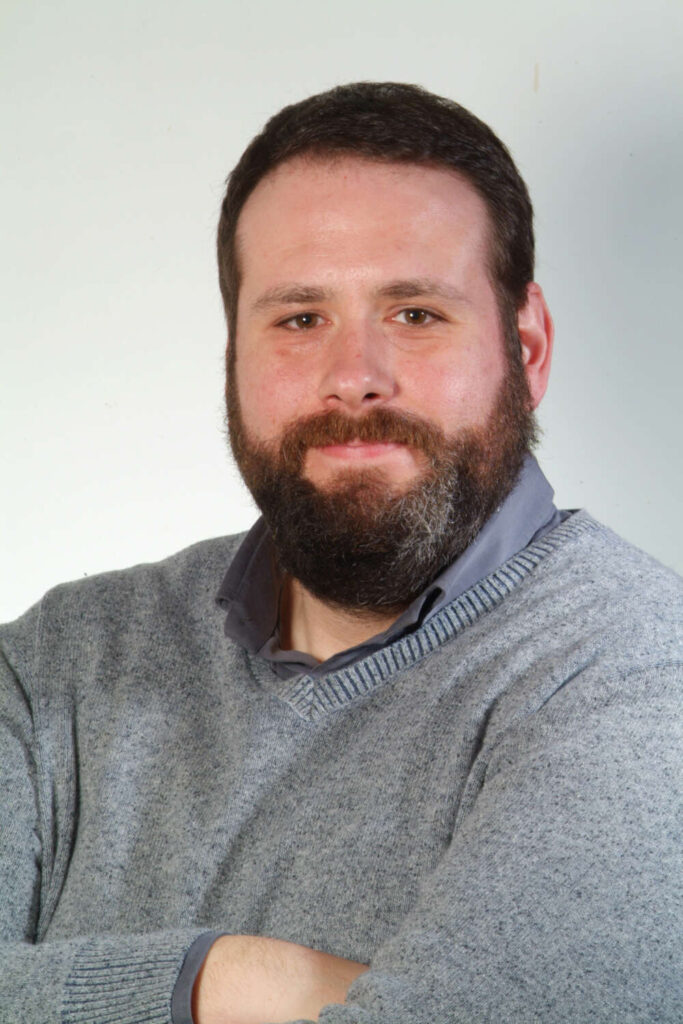
Non meno importante l’impegno sullo smontaggio gomme, d’interesse per via della vicinanza del polo nazionale del settore a Correggio (città natale, invece, di Luciano Ligabue) e per ciò stesso di un ricco e folto indotto. «Degli spessori che solitamente trattiamo», ha detto uno dei responsabili dell’ufficio tecnico Tiziano Taffurelli, «i più sottili vanno dagli otto ai dieci millimetri, mentre i pezzi più grandi arrivano alle 50 tonnellate di peso, con quel che ne consegue in termini di dimensione.
Si tratta di parti strutturali o spesso contrappesi per macchinari enormi, con una stazza da 800 chilogrammi e lamiere da 50 millimetri. Con l’ossitaglio lavoriamo grandezze sino a 150 millimetri; e ai 30 invece col plasma». Quello compiuto da Officine Meccaniche Buzzi sul terreno dell’automazione è stato un percorso graduale ed è il tipico work in progress destinato ad arricchirsi e completarsi con il tempo.
«Abbiamo tenuto il classico basso profilo», ha raccontato Taffurelli, «ma stiamo cercando di introdurre il maggior grado di automazione possibile sulle lavorazioni laser dai 15 ai 20 ai 25 millimetri, tenendo conto anche delle criticità date dalle lamiere più imponenti. Devono essere movimentate con carriponte, sollevate ed estratte con magneti per esser portate sul piano di taglio».
Dalle tecnologie alle strutture
L’azienda reggiana ha sposato la causa di Industry 4.0 solamente in parte: non su ossitaglio e taglio laser o al plasma, bensì su piegatrici e laser a tubo. Ha investito su un telaio pneumatico a ventose per il sollevamento dei fogli più leggeri, se così si può dire, perché quelli più pesanti continuano a essere spostati mediante magneti, carriponte e bilancini.
Il taglio inclinato è entrato a far parte della dotazione tecnologica aziendale in tempi relativamente recenti grazie all’arrivo di un bevel di seconda mano. E se Industria 4.0 è un percorso ancora da completare, pure su quel che è stato fatto il giudizio è positivo. «La complessiva efficienza è di gran lunga migliorata», ha commentato Tiziano Taffurelli, «perché migliore è anche il dialogo fra le macchine e le piattaforme IT.
Il prossimo passo da compiere riguarda l’allargamento delle strutture, dei capannoni, per avere delle campate dedicate proprio al taglio dei grossi spessori, con muletti e carriponte di grande portata. In programma ci sono altresì un nuovo magazzino con automazione e un superiore ricorso al laser sugli spessori medi compresi fra uno e 25 millimetri. Le automazioni implementate», ha aggiunto il responsabile dell’ufficio tecnico, «ci danno modo di gestire più efficacemente gli stock e le materie prime.
L’automazione applicata ai magazzini ci permette per esempio di conoscere sempre con esattezza quali e quante siano le giacenze contribuendo a dare efficienza ai processi: la disponibilità delle materie prime, i piani di produzione e le eventuali modifiche sono sempre chiari e noti a tutti».
Innovazione tecnologica e risparmio energetico vanno di pari passo: un impianto fotovoltaico è, mentre scriviamo, in fase di ultimazione, ed è una risorsa per alimentare il parco delle macchine laser, le più energivore, destinato a ospitare in futuro i soli sistemi a fibra in luogo di quelli a CO2.