Le moderne rettifiche per alte produzioni usano generalmente dei rulli diamantati per ravvivare le mole eseguendo un profilo ben preciso. Questi rulli profilatori hanno subito notevoli miglioramenti a vantaggio di di rendimento e precisione.
Rulli diamantati di grande valore
Usato in molte lavorazioni nell’industria meccanica, il diamante è diventato un materiale di largo consumo, tanto che non sono più sufficienti i diamanti industriali estratti nelle miniere sparse nel mondo.
Attualmente perciò trovano un più largo impiego i diamanti sintetici che, tra l’altro, hanno caratteristiche fisiche migliori rispetto a quelli naturali.
Si possono distinguere i seguenti tipi di diamante per uso industriale:
- Diamanti naturali. Sono stati generati naturalmente nel mantello della Terra, molti geologi ritengono che siano stati formati da 1 a 1,6 miliardi di anni fa ad una profondità di circa 150 – 400 km. Hanno un reticolo monocristallino e una durezza Knoop 6000 – 9000. Possono essere usati in tutti i tipi di utensili diamantati
- Diamanti MCD. Sono prodotti comprimendo grafite ad una enorme pressione, cioè 7 GigaPascal (che corrispondono a circa 70.000 atmosfere) con temperature di circa 1600 °C. Hanno una struttura monocristallina come i diamanti naturali e una durezza Knoop di 8000 – 9000. Sono usati preferibilmente in profilatori stazionari (a punta singola).
- Diamanti PCD policristallini. Sono diamanti i cui cristalli, che hanno dimensioni da 2 a 25 µm, vengono aggregati attraverso un legante. La loro durezza è nettamente inferiore rispetto i diamanti naturali (Knoop 4000 – 5500) e vengono usati in prevalenza per parti soggette ad usura.
- Diamanti PCD monocristallini. Sono generati con un processo di deposizione CVD su un substrato di silicio. Hanno una forma molto regolare e la durezza molto costante di Knoop 8500 – 9000. Queste caratteristiche lo rendono idoneo per essere usato su rulli profilatori e su altri utensili dove sono necessarie forme regolari. Le barrette di questo tipo di diamante possono essere sagomate nelle dimensioni volute con un processo laser.
Metodi di costruzione dei rulli
La costruzione dei rulli diamantati può essere fatta in diversi modi che differiscono tra loro per la velocità di costruzione e per i risultati in termini di precisione, efficienza e durata.
Deposizione elettrogalvanica
Il più semplice e tradizionale sistema di costruzione è quello di deposizione elettrogalvanica che segue un ciclo rappresentato nelle figure 1 e 2.
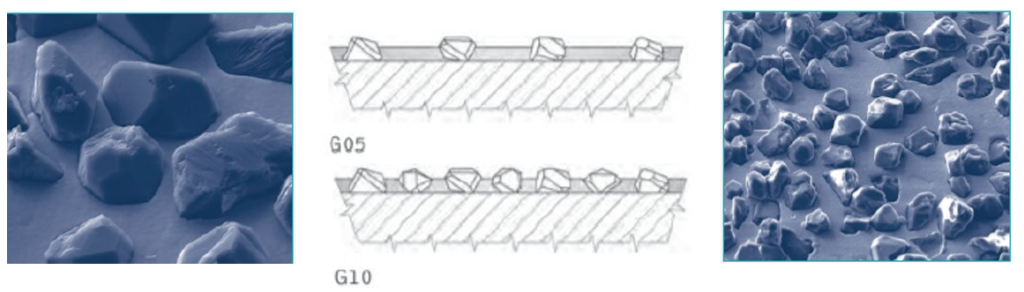
In pratica dopo la preparazione del corpo, che influenza in modo determinante la precisione del rullo, il corpo viene immerso in un bagno galvanico in cui un campo elettrico convoglia sul corpo stesso i grani di diamante. Questi vengono fissati sulla superficie con una distribuzione casuale e quindi le varie zone del rullo potrebbero avere diverse densità di diamanti, a volte in eccesso rispetto alle reali necessità. Successivamente, i grani vengono ancorati al corpo base tramite uno strato di Nichel, ma, poiché i grani hanno dimensioni e forme non uniformi, alcuni sporgeranno di più e altri di meno dalla superficie del corpo rendendo necessaria una rettifica finale o crashing per eliminare le irregolarità.
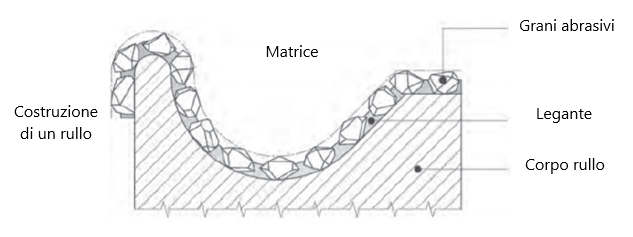
Con riferimento alla figura 1, la sigla G5 indica una deposizione monostrato, con elevata spaziatura per scaricare i trucioli, idoneo per granulometria > D/B 91. La sigla G10 indica invece una deposizione monostrato, (standard), idoneo per granulometria > D/B 91.
Il rullo così formato risulta con taglio più aggressivo rispetto a quelli prodotti con altri metodi.
Quando il rullo non taglia più perché i diamanti si sono consumati, è possibile fare un decoating e recuperare il corpo attraverso una nuova fase di deposizione.
In questo processo di deposizione galvanica esiste il problema che le cariche elettriche tendono ad accumularsi negli spigoli. Più sono acuti gli spigoli e più le cariche si concentrano in quei punti.
Ne consegue che anche il nichel si accumula prevalentemente sugli spigoli, coprendo a volte tutti i diamanti. Questo inconveniente, che riduce l’azione abrasiva dei grani, può essere risolto adottando una deposizione del nichel con un processo chimico che garantisce una eccellente uniformità dello strato. Questo processo necessita però di una operazione di tempra (di indurimento) del ricoprimento, cosa questa non necessaria nella elettrodeposizione.
Deposizione inversa o in negativo
Il secondo sistema è detto a deposizione inversa (o in negativo) (figura 2).
Si prepara il negativo del corpo in un materiale che potrebbe essere l’alluminio, con una alta precisione e poi vengono depositati al suo interno i diamanti.
I diamanti possono essere depositati sulla matrice interna con un processo galvanico e, in questo caso, avranno una disposizione casuale, oppure possono essere depositati a mano secondo uno schema definito.
In ogni caso il vantaggio principale è che all’esterno i diamanti risultano tutti allo stesso livello e quindi non necessitano di una successiva rettifica. Il rullo risulta quindi con una grande precisione.
La sua durata è migliore rispetto ai rulli con deposizione diretta.
Deposizione dei diamanti in modo casuale o manualmente
Il terzo sistema consiste nel depositare i diamanti o in modo casuale o manualmente in una matrice che è il negativo del rullo e poi sinterizzare.
Come si può vedere nella figura 3, il posizionamento manuale dei diamanti permette una distribuzione più uniforme dei grani con un vantaggio nell’azione di taglio e nell’evacuazione dell’abrasivo.
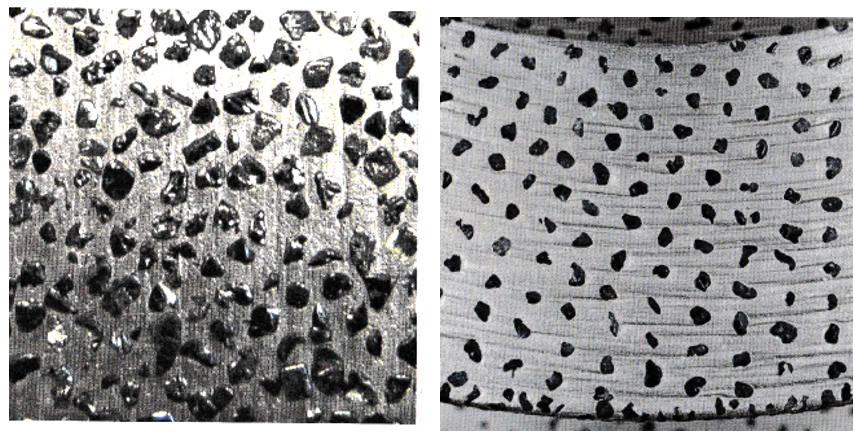
La polvere sinterizzata blocca i diamanti in modo sicuro limitando le deformazioni in caso di sollecitazioni anormali, sempre naturalmente entro certi limiti.
Il rullo di tipo sinterizzato, a causa del processo di fabbricazione, in cui una matrice di polveri metalliche e diamanti fissata all’interno di uno stampo viene portata ad una temperatura di circa 1000 °C, deve essere progettato tenendo conto del ritiro che si verifica durante il processo, in modo da ottenere il profilo finito a misura.
È evidente che stimare con esattezza l’entità del ritiro, anche su rulli con semplici profili, non é facile, per cui è quasi sempre necessario effettuare una ripassatura del profilo asportando qualche millesimo di millimetro.
I grani di diamante, che normalmente sono quelli sintetici monocristallini (CVD), sono immersi profondamente nel materiale di sinterizzazione e quindi permettono un certo numero di rigenerazioni con rettifica del profilo. Operazione questa detta anche “lapping” che richiede un tempo molto lungo, ma garantisce il rispetto delle tolleranze costruttive e la ripetibilità dei profili.
Una nuova generazione dei rulli diamantati
La tecnologia di elettrodeposizione diretta o inversa, che è stata utilizzata fino a pochi anni fa, non è più proponibile in quanto ha dei limiti di durata dei rulli troppo ridotta e non garantisce una superficie rettificata che rispetti le caratteristiche meccaniche e di rugosità superficiale richieste dalle applicazioni attuali.
I rulli ricoperti con questo vecchio sistema si usurano troppo velocemente sul diametro esterno e la rugosità a rullo nuovo risulta troppo alta, mentre a rullo usurato si corre il rischio di generare bruciature o surriscaldamenti che possono provocare la rottura dei denti dell’ingranaggio sottoposto alle condizioni di lavoro per cui è progettato. Le mole, infatti, non vengono ” ravvivate ” ma risultano lisciate e producono calore eccessivo durante l’operazione di rettifica.
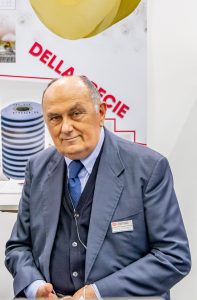
L’azienda bolognese Serma Srl, guidata dal Presidente Gianni Giovannini, adotta un nuovo metodo di posizionamento dei diamanti sul corpo di base che rivoluziona i metodi tradizionali, permette di allungare di due o tre volte la vita di questi costosi utensili e, nel contempo, di migliorare la qualità dell’operazione di rettifica.
I rulli di nuova generazione, commercializzati da Serma, presentano una corona di barrette in CVD sul diametro esterno che garantisce una più lunga vita dell’utensile; e sul profilo uno strato consistente di diamante con una deposizione geometrica definita per garantire la ravvivatura della mola e valori di rugosità ridotti e controllati.
Il diamante viene fissato tramite un processo di posizionamento gestito da un controllo numerico che garantisce la perfetta bilanciatura durante il lavoro e una omogenea distribuzione dello sforzo di ravvivatura della mola (figure 5 e 6).
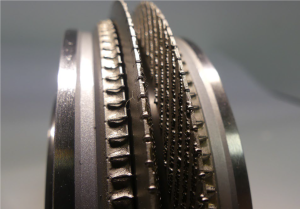
Anche sul profilo i diamanti sono posizionati e saldati con un processo robotizzato che garantisce la perfetta divisione e la forma elicoidale del riporto. Questa deposizione elicoidale scaricata garantisce il ripristino della taglienza della mola senza che la stessa venga lisciata e induca quindi surriscaldamento.
Infine, la deposizione elicoidale viene lappata in modo da garantire la perfetta forma del profilo e valori di rugosità che si stabilizzano sotto Rz 3,5 che è il parametro richiesto dalle nuove tecnologie sviluppate per le auto elettriche.
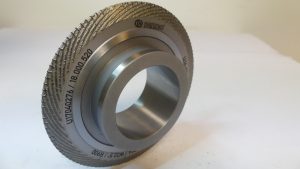
I diamanti vengono saldati sul corpo con un processo particolare che permette ai diamanti di sporgere per oltre il 50% dalla superfice del corpo senza per questo perdere la stabilità del fissaggio (figura 7).
La deposizione, come si è, detto viene gestita dal controllo numerico che colloca i diamanti lungo traiettorie ben definite e studiate per ottenere la massima copertura in fase di rettifica.
Dopo il posizionamento automatico i diamanti vengono lappati per uniformare la superficie, ma – come si può osservare nella figura 7 – tra un diamante e l’altro viene lasciato un ampio spazio che può contenere i grani di mola asportati durante la ravvivatura.
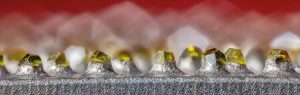
Inoltre, questi ampi spazi consento al liquido refrigerante di pulire tutta la zona che viene interessata dall’operazione. Tutto ciò aumenta notevolmente la durata del rullo e garantisce la taglienza delle mole.
I diamanti sono distribuiti come tante gocce contenenti cristalli molto piccoli, in funzione della grana della mola da ravvivare, la successiva lappatura garantirà valori di rugosità bassi e costanti nel tempo. Le varie “gocce“ garantiranno la taglienza tramite gli spigoli periferici.
In un rullo costruito con i metodi tradizionali non c’è spazio fra i cristalli per far lavorare gli spigoli taglienti e la situazione peggiora quando gli spigoli dei cristalli si arrotondano.
Questo provoca la lisciatura della mola, (effetto glazing), e il successivo surriscaldamento della zona di contatto con il pezzo, fino al rischio bruciature.
Come si può capire non sempre molto diamante significa lunga durata, anzi può essere deleterio.
La scelta della dimensione e della numerosità dei cristalli, unita alla geometria della deposizione, sono la base di questa nuova generazione di rulli.