In questo studio i ricercatori italiani mostrano l’interessante applicazione di un’innovazione su processi tradizionali della lamiera. Soluzioni moderne applicate su processi tradizionali permettono infatti di sostenere lo sviluppo dell’industria nel complesso contesto odierno.
L’industria manifatturiera è un settore in continua evoluzione e trasformazione, che si sta adattando alle nuove tecnologie e alle esigenze del mercato. Le innovazioni recenti stanno cambiando il modo in cui le aziende producono e distribuiscono i loro prodotti, rendendo il processo più efficiente, flessibile e sostenibile.
La digitalizzazione e l’automazione sono alcune delle tendenze che guidano questi cambiamenti. L’utilizzo di tecnologie come l‘Internet of Things (IoT), la robotica avanzata e l’intelligenza artificiale (IA) stanno diventando sempre più comuni nei processi produttivi. Inoltre, la crescente domanda di prodotti personalizzati e la necessità di ridurre gli sprechi e le emissioni spingono le aziende ad adottare metodi di produzione più sostenibili e a ridurre l’impatto ambientale delle loro attività.
La produzione si sta infatti evolvendo verso un nuovo modello: più digitale, automatizzato e sostenibile, in grado di soddisfare l’evoluzione delle esigenze del mercato e del consumatore.
Riduzione scarti
La formatura a freddo è una tecnica di trasformazione della lamiera utilizzata per creare componenti e strutture metalliche di varie forme e dimensioni. Questo processo viene spesso impiegato, tra gli altri, nel settore automotive grazie ai notevoli vantaggi offerti. I costi unitari possono risultare ridotti e le caratteristiche del componente sono interessanti.
Tuttavia, la trasformazione della lamiera per formatura a freddo può generare scarti di processo. Essi possono essere causati da una varietà di fattori tra cui: errori di misura, problemi di allineamento o possono derivare da problemi di qualità della lamiera stessa.
Ridurre al minimo gli scarti di processo è importante quanto difficile. È infatti necessario utilizzare tecnologie avanzate e tecniche di controllo qualità. Una efficace strategia spesso adottata per ridurre gli scarti è l’utilizzo di un sistema di feedback. Esso può aiutare a identificare e correggere tempestivamente i problemi, migliorando così l’efficienza del processo e la qualità del prodotto finale.
Un sistema di feedback efficace, infatti, può aiutare a identificare e correggere i difetti, aumentare la precisione del processo e migliorare la qualità del prodotto finale.
Inoltre, l’utilizzo di un sistema di retroazione può anche aiutare a ottimizzare l’utilizzo delle risorse e a ridurre i costi, rendendo il processo più efficiente ed economico.
L’innovativa soluzione proposta dai ricercatori italiani è quella di basare la retroazione direttamente sul processo di stampaggio invece che focalizzando l’attenzione solo sulla pressa (ovvero il macchinario utilizzato). Questo permette infatti di assicurare un controllo più preciso sul processo, riuscendo a correggere la lavorazione in caso di anomalie e riuscendo ad assicurare risultati migliori.
La retroazione
Un processo produttivo sfrutta la retroazione (o feedback) quando le misure effettuate durante il processo consentono di valutarne l’andamento e di apportare eventuali correzioni per mantenerlo entro i limiti desiderati. Negli ultimi anni per la retroazione in ambito manifatturiero, è stato frequentemente utilizzato l’approccio MPC (Model Predictive Control). Questa tecnica utilizza un modello matematico del processo per prevedere il comportamento futuro del processo e definire i parametri ottimali per assicurare un risultato di qualità.
L’MPC combina modellizzazione e controllo per ottenere una produzione efficiente e affidabile. Questo approccio è in grado di formulare previsioni del futuro del processo per agire sulle variabili controllate, anticipando e correggendo eventuali problemi prima che diventino critici. In questo contesto è stato scelto di monitorare alcuni punti critici sulla lamiera e di variare appropriatamente i parametri di forza del premilamiera e di corsa del punzone (figura di apertura).
I ricercatori propongono due alternative soluzioni basate su MPC: il sistema di controllo basato su mono-MPC e quello multi-MPC. La prima soluzione (Figura 2) è adatta ad una pressa monolitica (ovvero con un singolo punzone e un singolo premilamiera) e utilizza un singolo controllore in grado di valutare il profilo di formatura degli n punti considerati e definire il controllo del macchinario.
La soluzione multi-MPC (Figura 3) è invece più complessa e permette di gestire una pressa differenziale con più possibilità di controllo. Questa soluzione è composta da diversi controllori: uno dedicato per ogni pressa ed è in grado di valutare individualmente i segnali di errore registrati durante il processo.
Caso studio
Per provare la validità dell’approccio proposto i ricercatori hanno deciso di applicare i modelli su un caso realistico di componente automotive (figura di apertura). In questo caso specifico sono stati selezionati tre punti critici sulla lamiera (in figura di apertura: D, F e I) da monitorare durante il processo di trasformazione. Il modello è stato tarato registrando le traiettorie di riferimento per i punti selezionati durante l’intero processo ed effettuando una regressione.
Il sistema di controllo MPC è stato implementato in Simulink ed è in grado, confrontando le misure ottenute dal monitoraggio con i valori di riferimento, di definire la forza da applicare al punzone e al premilamiera. Un approccio analogo è stato applicato, anche per permettere un efficace confronto, sia utilizzando il modello semplificato mono-MPC, che per quello più evoluto mutli-MPC.
I risultati dei sistemi di controllo presentati dagli autori offrono prestazioni interessanti. Entrambe le soluzioni sono in grado di seguire fedelmente il riferimento del modello, limitando quindi le variazioni che corrispondono a potenziali difetti e scarti di lavorazione.
Sono stati introdotti anche disturbi sul segnale per valutare la solidità e l’affidabilità del sistema in ambiente prototipale e il sistema si è mostrato funzionale ed in grado di evitare rotture sulla lamiera in diverse situazioni. In generale l’approccio più evoluto, ovvero quello multi-MPC, presenta prestazioni superiori.
Tuttavia questa soluzione presenta una superiore complessità quindi, indirettamente, costi d’implementazione più elevati. Vista la ridotta differenza prestazionale tra i due modelli, risulta particolarmente interessante anche l’opzione mono-MPC, specialmente in alcuni casi di utilizzo, data la maggiore applicabilità in ambiente produttivo industriale.
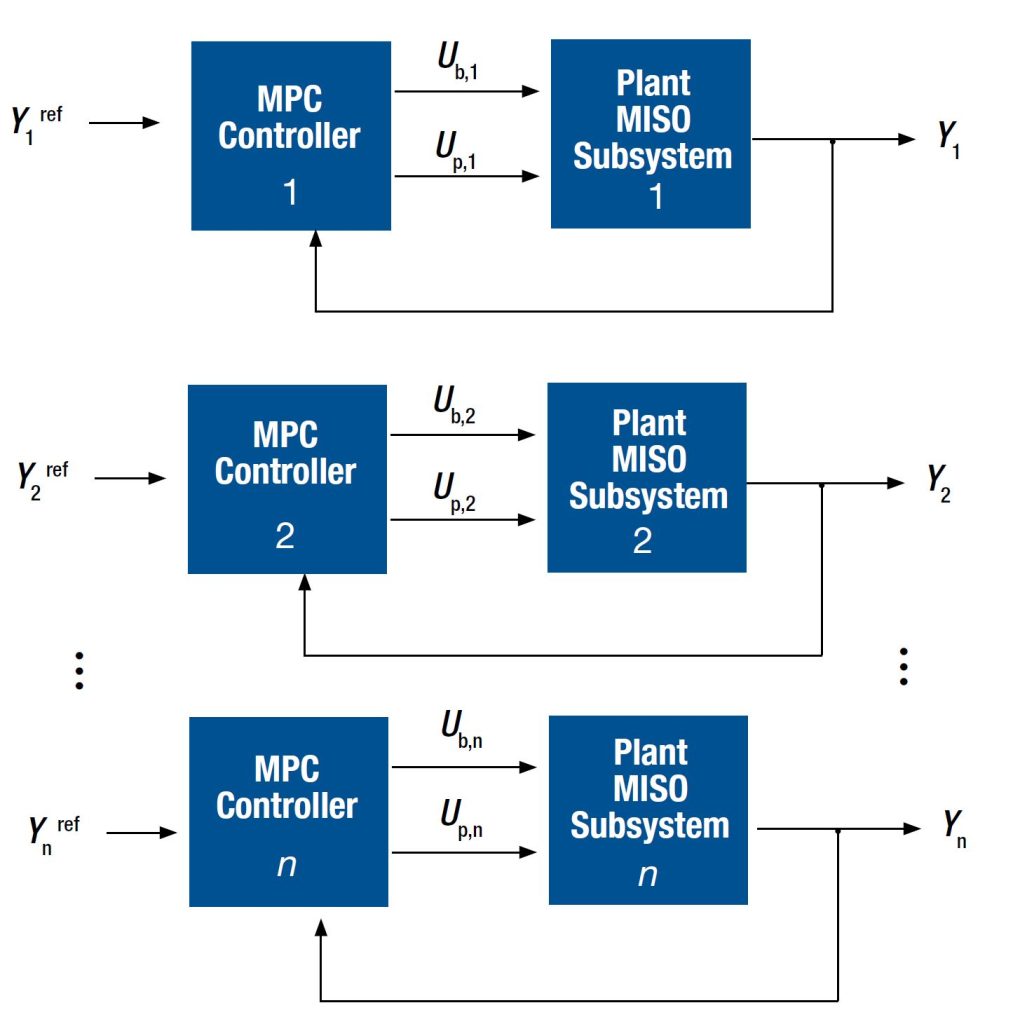
I contributi offerti dalla ricerca in questione sono diversi. Una prima brillante intuizione è quella di effettuare un feedback sul processo di formatura basato sul monitoraggio diretto del componente in lamiera. Questo approccio si contrappone rispetto alla soluzione, più tradizionale, di monitoraggio del macchinario utilizzato per la lavorazione.
La soluzione proposta dagli autori offre numerosi vantaggi tra cui la superiore precisione e correlazione con il prodotto finale. L’altra proposta innovativa è quella di utilizzare un processo di retroazione basato su un controllo MPC. Questo modello, una volta verificata l’affidabilità, può anche essere scalato per l’implementazione in reali applicazioni industriali. Il ridotto costo computazionale di questa soluzione è promettente per futuri impieghi.
I ricercatori italiani mostrano infatti l’interessante applicazione di un’innovazione su processi tradizionali della lamiera. Soluzioni moderne applicate su processi tradizionali permettono infatti di sostenere lo sviluppo dell’industria nel complesso contesto odierno.
A cura di Stefano Grulli
Fonte: Bozza, A., Cavone, G., Carli, R., Mazzoccoli, L., & Dotoli, M. (2021). An MPC-based approach for the feedback control of the cold sheet metal forming process. 2021 IEEE 17th International Conference on Automation Science and Engineering (CASE). https://doi.org/10.1109/case49439.2021.9551602