Una delle maggiori sfide per l’industria riguarda attualmente la sostenibilità ambientale, tema di massima importanza per tutte le organizzazioni socialmente responsabili
Per mantenere la competitività su scala globale, i processi di produzione aziendali devono essere allineati con le rigorose normative ambientali previste dai governi di tutto il mondo. L’industria manifatturiera, in generale, mira a migliorare la produttività e la qualità dei prodotti, nel rispetto dell’ambiente. Tale obiettivo viene raggiunto adottando tecniche di produzione sostenibili, che prevedono la minimizzazione delle fasi di produzione grazie all’impiego di metodi e tecnologie avanzate, l’utilizzo di lubrificanti e tecniche di lubrificazione a basso impatto ambientale in fase di lavorazione, la riduzione degli sprechi, la gestione attiva dei rifiuti, la riduzione dei consumi energetici, etc.
I produttori di ruote dentate sono tra i principali fornitori di servizi per tutti gli altri comparti industriali e manifatturieri. Dato il loro ruolo chiave, essi giocano un ruolo di primo piano per l’implementazione di tecniche mirate agli obiettivi di sostenibilità complessiva. Recenti sviluppi per il raggiungimento degli obiettivi di sostenibilità nella produzione di ruote dentate includono, ad esempio, la riduzione dell’uso di fluidi da taglio a base minerale, l’adozione di tecniche di lubrificazione alternative, come la lubrificazione MQL (minimum quantity lubrication) e la lavorazione a secco.
Altre soluzioni riguardano inoltre l’adozione di tecniche e processi che favoriscono il risparmio di materiale, la riduzione degli scarti, la minimizzazione del consumo energetico, il raggiungimento dell’efficienza economica, attraverso la riduzione del numero delle fasi di produzione (ottenuta eliminando, ad esempio, i processi di finitura), metodi avanzati come la rullatura, la laminazione e la elettro-erosione a filo WEDM (wire electric-discharge machining). Infine è possibile aumentare la produttività riducendo al minimo l’usura alle elevate velocità di taglio delle ruote dentate, grazie all’uso di materiali e rivestimenti alternativi.
Di seguito esamineremo più in dettaglio lo stato dell’arte della tecnologia per la produzione sostenibile di ruote dentate, considerando come sia possibile migliorare la produttività e la qualità, garantendo, al contempo, la sostenibilità ambientale.
Il concetto di produzione sostenibile
Il concetto di sviluppo sostenibile, comunemente indicato come sostenibilità, risale agli anni Settanta del ventesimo secolo. In particolare, una precisa definizione, riconosciuta a livello internazionale, è stata espressa nel 1987, dalla Commissione mondiale su Ambiente e Sviluppo dell’UNEP (United Nations Environment Program).
In questa occasione, Gro Harlem Brundtland, presidente della commissione “WCED” (World Commission on Environment and Development) istituita nel 1983, presenta il rapporto “Our common future” (Il futuro di tutti noi), formulando una linea guida per lo sviluppo sostenibile ancora oggi valida. In particolare, nel rapporto si definisce “sostenibile lo sviluppo idoneo a soddisfare le necessità della generazione presente senza compromettere la capacità di quelle future di rispondere alle loro.”
Secondo il rapporto Brundtland, le criticità e le problematiche globali dell’ambiente sono legate essenzialmente alla grande povertà dei paesi del sud del Pianeta in contrapposizione ai modelli di produzione e di consumo poco sostenibili dei paesi del nord. Il rapporto evidenziava quindi la necessità di attuare una strategia in grado di integrare le esigenze di sviluppo e sostenibilità ambientale, definita appunto di “sviluppo sostenibile”.
Nel rapporto sono inoltre presentati i tre pilastri della sostenibilità: economia, ambiente e sostenibilità sociale. Come mostra la figura 1, è chiaro come il fallimento di anche solo uno qualsiasi di essi possa contribuire a rendere instabile il sistema nel suo complesso. Fondamentalmente quindi, per favorire la sostenibilità globale, occorre adottare un approccio sistemico o multi-stakeholder.
Nel 1989, l’Assemblea generale dell’ONU, dopo aver discusso il rapporto, ha deciso di organizzare una Conferenza delle Nazioni Unite su ambiente e sviluppo. Un altro documento di fondamentale importanza per lo sviluppo del concetto di sostenibilità e per la definizione di direttive ambientali, è stato l’Agenda 21, firmata a Rio de Janeiro nel 1992 da 179 nazioni; in essa sono stati stabiliti indirizzi che impegnano i Paesi aderenti a ridurre l’uso di risorse naturali e la produzione di rifiuti. A questo protocollo d’intesa ne sono seguiti molti altri, a testimonianza del grande interesse che il tema continua a suscitare a livello mondiale.
Tuttavia la sostenibilità è ancor oggi una questione assai complessa, che coinvolge, in egual misura, questioni ambientali, economiche, sociali ed istituzionali. Un primo passo potrebbe riguardare lo sviluppo di una visione di società sostenibile corredata da indicatori che possano consentire la misurazione del progresso e della distanza dai traguardi prefissati.
In questo contesto, l’Agenda 2030, racchiude 17 obiettivi globali (figura 2) in un grande piano d’azione per le persone, il pianeta e la prosperità.
In particolare, l’obiettivo numero dodici mira a garantire modelli di consumo e produzione sostenibili, coinvolgendo tutti i paesi, a partire da quelli più sviluppati alle economie emergenti.
Ad oggi il fabbisogno di risorse richiesto dalla popolazione mondiale è più di quanto l’ecosistema sia in grado di fornire. Affinché lo sviluppo sociale ed economico possa realizzarsi in un quadro di sostenibilità, la nostra società dovrà necessariamente modificare in modo radicale i propri sistemi di produzione e abitudini di consumo.
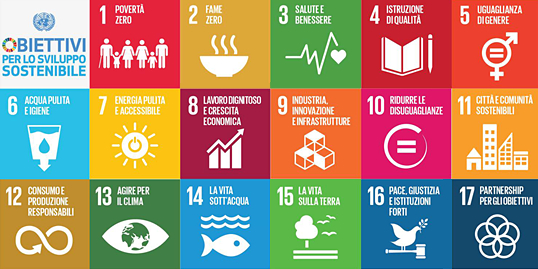
L’obiettivo dodici promuove l’attuazione del programma dell’ONU per un modello di consumo e di produzione sostenibile, in accordo con un utilizzo efficiente delle risorse naturali. Nello specifico, si mira ad adottare una gestione eco-compatibile di prodotti chimici e rifiuti durante il loro intero ciclo di vita, riducendo sensibilmente il loro rilascio in aria, acqua e suolo, per minimizzare l’impatto negativo sulla salute umana e sull’ambiente. Lo spreco di derrate alimentari dovrà essere dimezzato. Anche il volume dei rifiuti dovrà essere notevolmente ridotto, attraverso strategie di prevenzione e riciclo.
Le imprese, in particolare le grandi multinazionali, dovranno essere spronate per una gestione aziendale sostenibile ed anche gli appalti pubblici dovranno rifarsi ai criteri di sostenibilità conformi alle politiche e priorità nazionali. Tutte le persone, in ogni parte del mondo, dovranno avere a disposizione informazioni rilevanti e la giusta consapevolezza circa l’importanza dello sviluppo sostenibile e di uno stile di vita in armonia con la natura. Occorrerà poi supportare i paesi in via di sviluppo nel potenziamento delle loro capacità scientifiche e tecnologiche, per raggiungere modelli di consumo e produzione più sostenibili; sviluppare e implementare strumenti per monitorare gli impatti dello sviluppo sostenibile in un’ottica di turismo sostenibile, per nuovi posti di lavoro e la promozione della cultura e dei prodotti locali.
Manovre governative dovranno infine razionalizzare i sussidi inefficienti, eliminando le distorsioni del mercato, anche ristrutturando i sistemi di tassazione.
Il settore manifatturiero può contribuire in maniera significativa allo sviluppo sostenibile, in quanto è un importante driver di questi obiettivi.
Come noto, la sostenibilità ambientale rappresenta un vantaggio competitivo per le imprese: i prodotti, i processi e i servizi dovrebbero rispondere alle sfide non solo per quanto inerente funzionalità, prestazioni e costi, ma anche per quanto concerne l’ambiente e le questioni sociali.
Affinché un processo sia considerato “sostenibile”, dovrebbe avere quindi un impatto ambientale ridotto, dovrebbe rappresentare un beneficio per la società ed essere economicamente sostenibile. È quindi necessario che l’industria manifatturiera continui ad essere proattiva in questo senso.
In sintesi, la produzione sostenibile può essere definita come quel sistema che si avvale di processi in grado di ridurre al minimo l’impatto negativo sull’ambiente, riducendo gli sprechi di energia e risorse naturali, garantendo sicurezza per gli operatori, le comunità e i consumatori oltre a processi, al contempo, economicamente sostenibili. Se da un lato si fa riferimento alla produzione di prodotti sostenibili, dall’altro all’individuazione di un processo sostenibile per ogni prodotto. Gli aspetti principali nel primo caso riguardano la selezione di fonti di energia rinnovabile, prodotti ecologici, legati all’equità sociale, nel secondo, lo sviluppo e la creazione di processi produttivi efficienti dal punto di vista energetico, non inquinanti ed economicamente sostenibili.
I benefici della produzione sostenibile includono: riduzione dei costi di lavorazione, processi eco-sostenibili, minimizzazione dei consumi energetici, riduzione e corretta gestione dei rifiuti, salute e sicurezza operativa.
A livello globale, l’industria manifatturiera si sta focalizzando sull’implementazione di tecnologie avanzate di lubrificazione e raffreddamento, sull’uso di oli vegetali e altri fluidi da taglio ecocompatibili, sulla scelta di utensili avanzati e sull’impiego di processi di produzione avanzati e soluzioni ibride.
Produzione sostenibile di ruote dentate: criticità
Le ruote dentate sono componenti meccanici critici per la trasmissione di moto e di potenza per il corretto funzionamento di macchine, strumenti ed apparecchiature industriali. Esse giocano un ruolo chiave in numerosi settori industriali: basti pensare che, ogni anno, a livello globale, vengono prodotti miliardi di ruote dentate. I processi di produzione degli ingranaggi metallici possono essere classificati in tre categorie:
- processi di asportazione di materiale (lavorazione) come la dentatura, la fresatura, la sagomatura e la brocciatura;
- processi di formatura come lo stampaggio e l’estrusione;
- processi additivi come la pressofusione e la metallurgia delle polveri (PM).
Un processo di lavorazione tradizionale di una ruota dentata tipicamente parte dalle attività preparatorie inclusa la selezione del materiale, procede poi con il taglio dei denti, il trattamento termico, per conferire le appropriate proprietà meccaniche sia a livello superficiale che interne e la fase finale di finitura, che permette di ottenere la qualità desiderata (a livello di tolleranza, superficie, finitura).
Tuttavia, i requisiti delle operazioni di finitura hanno un impatto significativo sulla sostenibilità complessiva. I principali problemi associati alla produzione di ruote dentate mediante processi convenzionali possono essere riassunti come segue:
- Tutti i processi convenzionali per la produzione di ruote dentate richiedono processi di finitura (come rifilatura, rettifica, levigatura, brunitura, etc.) per ottenere componenti di qualità.
- Tali operazioni solitamente, a causa delle limitate prestazioni dei lubrificanti e del loro potere di raffreddamento, comportano un’usura spesso rilevante degli utensili, tale per cui gli stessi necessitano di essere rigenerati o sostituiti, con procedure dispendiose dal punto di vista energetico. Di conseguenza, aumentano gli oneri legati alla gestione, al riciclaggio e allo smaltimento dei rifiuti che fanno inevitabilmente lievitare i costi complessivi.
- L’alimentazione e il pompaggio di quantità significative di fluido da taglio nella zona di lavoro durante le fasi di lubrificazione e raffreddamento convenzionali sono anch’esse procedure poco sostenibili e che possono influire negativamente sulla salute e sulla sicurezza degli operatori, nel caso in cui il fluido abbia proprietà tossiche.
- La gestione e lo smaltimento dei trucioli bagnati (scarti di taglio dei metalli) e del fluido da taglio sono compiti complessi da gestire, che possono avere anch’essi un impatto negativo sull’ambiente.
Con tali consapevolezze, ingegneri e tecnologi stanno cercando tecniche alternative ed avanzate per la produzione e la finitura degli ingranaggi, come la laminazione e la lavorazione WEDM (wire electricdischarge machining), con l’obiettivo di ridurre al minimo l’impiego e la quantità di fluidi da taglio nocivi. La tendenza è quella di privilegiare, inoltre, l’utilizzo di lubrificanti ecologici come oli vegetali, esteri sintetici ed altre soluzioni biodegradabili ed impiegare tecniche di lubrificazione sostenibili, quali, ad esempio, la lubrificazione a quantità minima (MQL), il raffreddamento criogenico e il taglio a secco, selezionando le condizioni di lavorazione ottimali, i materiali e i rivestimenti degli utensili di lavorazione più adatti. La figura 3 presenta una “roadmap” per il raggiungimento della sostenibilità globale nella produzione di ruote dentate.
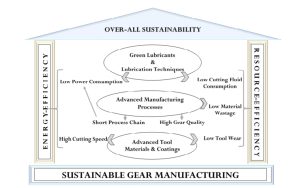
Rigenerazione delle ruote dentate
Abbiamo visto quanto sia cruciale risparmiare risorse e ridurre le emissioni di CO2 in un’ottica di sviluppo attuale e futuro di prodotti e come linee guida e normative sempre più stringenti richiedano processi di produzione e riciclo sempre più sostenibili ed efficienti.
In questo contesto, il riciclo dei componenti in acciaio si dimostra un approccio realistico per il risparmio di elevate quantità di energia, salvaguardando al contempo l’ambiente.
Le tecnologie di formatura sono per lo più utilizzate allo scopo di minimizzare i costi di produzione di componenti metallici dalle buone proprietà meccaniche. La crescente concorrenza internazionale con conseguente pressione sui costi, unitamente agli aspetti di sostenibilità ambientale, pongono oggi il focus sull’ottimizzazione e sullo sviluppo di nuove strategie e tecnologie di formatura. Una possibile soluzione per soddisfare questi requisiti è il riutilizzo dell’acciaio, materiale comunemente impiegato nella realizzazione di prodotti tecnici, che può essere riciclato ripetutamente senza l’alterazione delle sue proprietà.
Un modo per ridurre ulteriormente l’impatto ambientale di questo materiale è poi quello di riciclare i componenti in acciaio (riciclo di prodotto).
Grazie al passaggio dal riciclo del materiale a quello di prodotto, la catena di produzione di componenti in acciaio si accorcia, omettendo quelle fasi e processi più impattatati dal punto di vista energetico e ambientale (figura 4). Sulla base di queste considerazioni, il processo di ricondizionamento si dimostra particolarmente adatto per il riciclaggio di prodotti di massa come le ruote dentate.
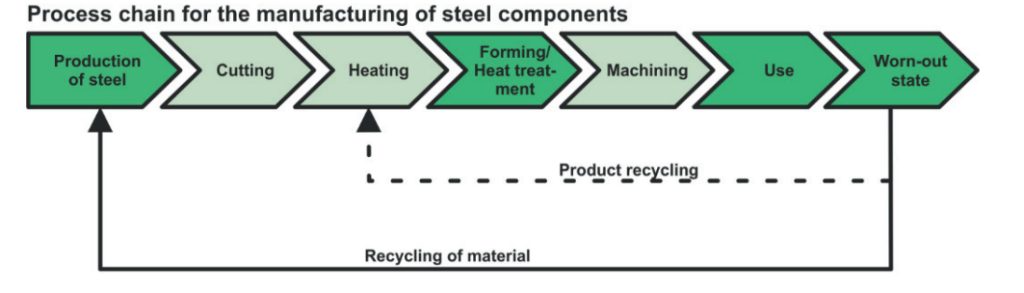
Il processo di ricondizionamento di ruote dentate parte dalle modalità di guasto. Le ruote dentate cedono generalmente per fatica, a causa degli elevati carichi meccanici e dei fenomeni tribologici di danneggiamento come usura e pitting.
Una possibilità per il ricondizionamento di componenti in acciaio è l’uso di tecnologie di formatura dei metalli sfusi. Operazioni post formatura consentono di rigenerare la forma e la funzione di componenti in acciaio usurati, il componente è “riportato a nuovo” e può essere quindi riutilizzato.
Allo scopo di valutare la fattibilità del processo di ricondizionamento di ruote dentate in acciaio danneggiate con tecnologie di post formatura, vengono condotte una serie di analisi eseguite secondo la procedura illustrata in figura 5.
Per le analisi è stato scelto un ingranaggio cilindrico con 16 denti e un modulo di 4,5 mm.
Nella fase iniziale vengono progettati gli utensili di formatura per la forgiatura di precisione a caldo (fase 1). Successivamente, viene generato un modello 3D semplificato di una ruota dentata danneggiata, grazie alla combinazione di programmi CAD e Matlab (fase 2). Per il successo del riciclo di componenti in acciaio, la sfida maggiore riguarda andare ad individuare e sviluppare strategie di formatura adeguate per il processo di ri-forgiatura di precisione (fase 3). Dopo averle determinate, viene quindi sviluppato un sistema di utensili collettivi per la ri-fabbricazione delle ruote dentate a partire dal loro stato di usura (fase 4). La lavorazione degli ingranaggi normalmente richiede utensili specifici per realizzare ciascun profilo. Il sistema di utensili per la post-formatura di precisione di ingranaggi danneggiati, può essere utilizzato anche per la produzione di ingranaggi convenzionali.
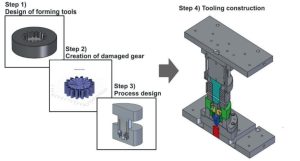
In sintesi, una possibilità per realizzare prodotti di elevata qualità tecnica, garantendo al contempo la tutela dell’ambiente, è il riciclo dei componenti danneggiati nei processi di forgiatura. Con la post-formatura locale a temperature elevate, i difetti del componente danneggiato possono essere riparati più rapidamente ottenendo un prodotto finito pari al nuovo, riducendo le fasi di produzione.
In futuri esperimenti di forgiatura, si pensa di valutare i limiti della post-formatura di precisione per poter prevedere le possibili prospettive di riciclo dei componenti in acciaio.
Produzione sostenibili grazie alle tecnologie additive
Come processo di produzione emergente, le tecnologie additive non solo hanno il potenziale per cambiare il panorama dello sviluppo del prodotto, della produzione e della logistica, ma possono anche contribuire a migliorare la sostenibilità in una varietà di settori tanto che, a lungo termine, potrebbero svolgere un ruolo significativo nel raggiungimento degli obiettivi di sviluppo sostenibile delle Nazioni Unite. La produzione additiva presenta quindi una serie di benefici per la sostenibilità sia a livello di processo produttivo sia a livello di prodotto.
Per quanto concerne i processi produttivi, soluzioni verso la sostenibilità mediante l’uso di tecnologie additive sono evidenti. Basti pensare, ad esempio, che la produzione di un ingranaggio per automotive necessita di 17 fasi di produzione con metodo di lavorazione sottrattiva, contro le sole 6 richieste da un processo di polvere di metallo. Si consideri che ogni passaggio in meno comporta un notevole risparmio nei consumi energetici.
Altro grande vantaggio delle tecnologie additive è che la produzione vera e propria può essere intrapresa localmente: la stampante può essere installata presso lo stabilimento di produzione (o nelle sue immediate vicinanze), in modo tale da doversi solo occupare del trasporto della polvere, riducendo drasticamente le operazioni di movimentazione e logistica. Inoltre, la produzione additiva riduce lo spreco di materiale: la stampa di un componente utilizza solo una parte della polvere impiegata nel processo, mentre la restante parte può essere riciclata in una nuova fusione, soluzione decisamente più ecologica rispetto ai sistemi di produzione tradizionali, dove vengono prodotte grandi quantità di scarti. In tal caso, sebbene i trucioli vengano comunque raccolti e riciclati, l’impronta ecologica risulta sostanzialmente più elevata, a causa di trasporti più pesanti e di una quantità molto maggiore di materiale da riciclare, con conseguente notevole impatto energetico. Tuttavia, nonostante i numerosi vantaggi della produzione additiva, che si dimostra perfetta per certe applicazioni, in casi specifici le tecniche di produzione sottrattiva risultano ancora preferite.
La produzione additiva è attualmente utilizzata principalmente per la produzione di componenti con design complessi o che traggono vantaggio dalla leggerezza, come le ruote dentate.
Le ruote dentate, nonostante siano da secoli impiegate in una varietà di applicazioni di uso quotidiano, possono risultare complesse da realizzare. Per garantire che durante la trasmissione della potenza venga generata la minore perdita di attrito possibile, è necessario prestare particolare attenzione alla loro progettazione. In quest’ottica, anche il materiale selezionato è un fattore critico per una trasmissione ottimale della potenza. Le tecniche di produzione tradizionali offrono margini limitati di ottimizzazione delle ruote dentate, dal momento che è assai costoso realizzare soluzioni personalizzate.
Ciò è dovuto principalmente al fatto che dovrebbero essere poste in essere diverse singole fasi e, se necessario, dovrebbero essere creati o acquistati strumenti adeguati. Un modo per aggirare questo problema è utilizzare la sinterizzazione laser selettiva (SLS), una possibile soluzione in quanto, attraverso i processi di manifattura additiva, le ruote dentate possono essere prodotte in un unico pezzo e senza strumenti aggiuntivi. I polimeri ad alte prestazioni “iglidur”, sviluppati dall’azienda igus, rendono possibile, ad esempio, la realizzazione di ruote dentate in plastica con elevato margine di personalizzazione. Queste ultime potrebbero dimostrarsi rivoluzionarie per una varietà di settori, grazie ad una maggiore durata e valori di attrito inferiori oltre ad una elevata efficienza, solo minimamente inferiore a quella degli ingranaggi in metallo lubrificati. In sintesi, i principali vantaggi legati a ruote dentate stampate in 3D con polimeri ad alte prestazioni iglidur riguardano:
- durata d’esercizio prevedibile, fino a 5 volte superiore alle ruote dentate lavorate a macchina o stampate ad iniezione con plastiche convenzionali;
- possibilità di realizzazione di qualsiasi geometria: dalle forme speciali ai pezzi di ricambio;
- geometria del fondo del dente ottimizzata per una maggiore durata d’esercizio;
- funzionamento a secco grazie ai lubrificanti solidi.
La libertà di progettazione ottenuta con la tecnica SLS può essere utilizzata, per ottenere una riduzione del peso, problema cruciale in alcuni settori, come l’industria aerospaziale, guidata sia dal costo del carburante che dall’impronta di carbonio. Basti pensare che ogni chilogrammo di peso in meno su un aereo, ad esempio, consente di risparmiare 3.000 dollari all’anno in carburante. Discorso simile vale poi per il settore automotive, per le macchine agricole e tutti gli altri veicoli adibiti al trasporto di merci o persone.
Rispetto alla produzione meccanica, ulteriori vantaggi in termini di costi possono essere raggiunti attraverso un uso più efficiente dei materiali e tempi di stampa ridotti. Inoltre, il design svolge un ruolo molto più importante nel prolungamento della vita utile del componente. Rispetto alla produzione meccanica o allo stampaggio a iniezione, le geometrie delle ruote dentate non devono essere semplificate, ma possono essere adattate in modo ottimale nel modello di stampa, ottenendo un prodotto finito più resistente.
Il materiale selezionato rappresenta un ulteriore fattore che influenza la qualità, dal momento che non tutte le materie plastiche sono adatte in egual misura a specifiche applicazioni. Tornando ai materiali iglidur, essi hanno buoni valori di attrito e bassa usura grazie alle proprietà tribologiche, risultando perfettamente adatti per applicazioni in movimento, come le ruote dentate. Inoltre, tra le diverse opzioni iglidur, ad esempio, iglidur I3 è caratterizzato da una maggiore forza, particolarmente adatto per ingranaggi a denti dritti e a coppia conica, si può utilizzare anche per tutti gli altri tipi di ruote dentate resistenti all’usura; iglidur I6 ha proprietà di scorrimento ottimizzate ed è quindi ideale per ingranaggi senza fine o altre ruote dentate dove è richiesta la conformità agli standard per alimenti e iglidur I8-ESD è adatto in caso di ruote dentate con proprietà ESD (Electro Static Discharge).
Come noto, la vita utile di un componente dipende anche dai parametri dell’applicazione, per tale motivo è consigliabile che la scelta tra la produzione di ruote dentate mediante stampa 3D piuttosto che lo stampaggio a iniezione sia effettuata in base all’applicazione specifica. Come regola generale, può essere più economico produrre un ordine di 10.000 ruote dentate utilizzando uno stampo a iniezione. In questo caso, la stampa 3D può essere utilizzata per produrre i prototipi iniziali e fabbricare lo stampo, che può quindi essere utilizzato per produrre una grande quantità di ruote dentate con proprietà del materiale comparabili. Questa opzione è adatta anche per ruote dentate in plastica con proprietà speciali, ad esempio ignifughe.
Ruote dentate in tecnopolimero stampate in 3D sono utilizzate oggi, ad esempio, nella costruzione di prototipi per un sistema di ricarica per auto elettriche, nelle applicazioni automotive e per la costruzione di e-bike.
Conclusioni
Le stringenti normative ambientali in vigore in tutto il mondo e la crescente competitività a livello internazionale stanno costringendo le imprese ad adottare sistemi sempre più efficienti ed ecologici. Nell’articolo sono state esaminate diverse tecniche per la produzione sostenibile di ruote dentate che includono l’impiego di materiali, lubrificanti e tecniche di lubrificazione sostenibili, processi di rigenerazione degli ingranaggi danneggiati, tecnologie di produzione avanzate come la manifattura additiva, etc. Sono stati registrati miglioramenti significativi in termini di produttività, costi, durata degli utensili, qualità, consumi energetici, produzione e strategie di gestione dei rifiuti, etc. Tuttavia, occorrono ulteriori sforzi e ricerche per sviluppare via via soluzioni ancora più ecologiche non solo a livello di prodotto ma anche di processo produttivo allo scopo di garantire elevata integrità e qualità delle ruote dentate, efficienza energetica ed economica, un ambiente pulito, sicuro e sano o semplicemente per la sostenibilità generale.
Riferimenti
Kapil Gupta, R.F. Laubscher, J. Paulo Davim, N.K. Jain, Recent developments in sustainable manufacturing of gears: a review, Journal of Cleaner Production, Volume 112, Part 4, 2016, Pages 3320-3330, ISSN 0959-6526, https://doi.org/10.1016/j.jclepro.2015.09.133.
Kuwert, P., Brunotte, K., Behrens, BA. (2019). Process Development for the Remanufacturing of Geared Components. In: Wulfsberg, J.P., Hintze, W., Behrens, BA. (eds) Production at the leading edge of technology. Springer Vieweg, Berlin, Heidelberg. https://doi.org/10.1007/978-3-662-60417-5_5
Giorgio De Pasquale, Dipartimento di Ingegneria Meccanica e Aerospaziale, Politecnico di Torino, Smart Structures and Systems Lab,
Elena Perotti, Senior data analyst