Le trasmissioni per i veicoli elettrici non sono progettate solo per velocità e torsioni elevate ma risultano essere anche molto compatte. Questo vale per il settore automobilistico, ma soprattutto per applicazioni innovative quali le e-bike. Le trasmissioni piccole, ma di grande potenza, azionate elettricamente spingono i progettisti a trovare soluzioni creative. Spesso contengono componenti piccoli con criticità di ingombri che comportano nuove sfide per la produzione. Quando si tratta rettifica di precisione degli ingranaggi, il potenziale legate al processo vanno di pari passo con gli alti costi di produzione. La variante più economica è la rettifica a generazione, ma non tutte le rettificatrici sono adatte alla produzione di componenti compatti. Questo articolo ne descrive i requisiti e illustra le possibili soluzioni.
Piccole mole a vite, grande potenziale
Per la mobilità elettrica non è necessario reinventare il processo di produzione delle trasmissioni, ma ci sono alcune nuove sfide. Tra queste, in modo particolare, l’alta intensità di potenza e lo spazio di installazione compatto in cui deve essere inserita l’intera trasmissione. Le nuove applicazioni stanno creando nuove opportunità di vendita: le e-bike sono di gran moda perché migliorano notevolmente l’autonomia e le capacità di trasporto nella vita quotidiana e nel tempo libero. La domanda è di conseguenza elevata. I produttori e i loro fornitori, compresi i produttori di trasmissioni, ne ne traggono vantaggio. Che si tratti di due o quattro ruote, la tecnologia richiesta è sofisticata. L’attenzione si concentra sulla capacità di carico richieste e sul comportamento acustico degli ingranaggi a causa delle condizioni limite del motore elettrico – una torsione elevata quasi costante nell’intervallo di velocità da 0 – 18.000 giri/min. Tuttavia, i nuovi requisiti non si limitano ai pezzi finiti; ma riguardano anche il processo di produzione in sé. A causa della struttura compatta, nella progettazione dei riduttori compaiono sempre più spesso componenti con piani di spallamento. Gli utensili di grandi dimensioni con le consuete dimensioni della mole a vite raggiungono rapidamente i loro limiti nel vero senso della parola. Se non si vuole passare a processi più lunghi e quindi più costosi, è necessario miniaturizzare gli utensili.
Riconoscere e superare i limiti
Fino ad oggi, la rettificatura di precisione con piani di spallamento è stata realizzata principalmente tramite la rettifica discontinua o mediante honing.
Rispetto alla rettifica per generazione continua, entrambi i processi presentano diversi svantaggi in termini di produttività, efficienza economica o costanza della qualità. Il problema è che le comuni mole a vite a generazione con diametri di 300 mm sono troppo grandi per componenti con piani di spallamento. Mentre gli utensili più piccoli richiedono velocità più elevate per raggiungere alte velocità di taglio. Tuttavia il concetto delle macchine precedentemente progettate non era dotato delle necessarie caratteristiche dinamiche dell’azionamento dell’utensile e del pezzo. I nuovi tipi di mandrini ad alta velocità, in combinazione con un azionamento diretto dinamico dell’asse del pezzo, rappresentano una soluzione. Ciò consente di sfruttare i vantaggi offerti dalla rettifica a generazione, un processo che si caratterizza per tempi di lavorazione più brevi, costi utensile inferiori e un livello di qualità molto elevato. I due componenti selezionati, “car” e “bike” (figure 1 e 2) possono essere utilizzati per dimostrare l’efficienza economica della rettifica a generazione rispetto alla rettifica a profilo. Le tabelle corrispondenti (“car” e “bike”) illustrano i vantaggi in termini di tempo e di costi.
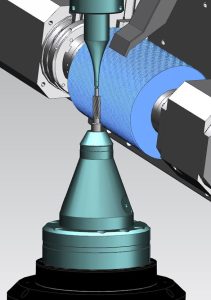
BIKE | Rettifica a profilo | Rettifica a generazione |
Dati utensile | ||
Diametro [mm] | 100 | 110 |
Materiale da taglio | CBN (galv.) | Corindone |
Nr. Principi | 1 | 5 |
Tempo terra/terra[s] | 75 | 20 |
Costi utensile per pezzo [€] | 0,17 | 0,04 |
Le macchine adatte
Il costruttore Kapp Niles, con sede a Coburg, specializzato in rettificatrici per ingranaggi offre due tipi di macchine per soddisfare le esigenze dei clienti. Entrambe le serie sono dotate di un azionamento altamente dinamico dell’utensile (a 25.000 rpm) e del pezzo (a 5.000 rpm) altamente dinamico.
La KNG 350 flex HS ha un design convenzionale monomandrino. È disponibile in due versioni per i lotti minimi e piccoli con caricamento manuale. Mentre per lotti più grandi è disponibile una versione automatizzata con un caricatore ad anello rapido. Con tale macchina si possono lavorare pezzi fino a 350 mm di diametro. È caratterizzata da tempi di allestimento brevi, ottenuti grazie a componenti intelligenti e ad un’ergonomia unica.
Per la produzione su larga scala, tuttavia, vale la pena considerare con attenzione i tempi non produttivi concettuali della macchina. La serie KX TWIN bimandrino con operazioni di carico e scarico in parallelo alla lavorazione offre un ulteriore potenziale di riduzione dei tempi di lavorazione. La rotazione dei componenti, direttamente in macchina a tempo zero, consente di soddisfare i requisiti di “Clean Factory” con tutti i concetti di automazione noti.
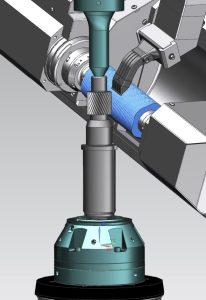
CAR | Rettifica a profilo | Rettifica a generazione |
Dati utensile | ||
Diametro [mm] | 80 | 80 |
Materiale da taglio | CBN (galv.) | Corindone |
Nr. Principi | 1 | 5 |
Tempo terra/terra[s] | 228 | 53 |
Costi utensile per pezzo [€] | 0,75 | 0,21 |
Ulteriori requisiti per la produzione
Oltre ai componenti compatti e con criticità di ingombri, gli ingranaggi per l’elettrico richiedono ulteriori requisiti per la produzione:
- il comportamento acustico della trasmissione quindi soprattutto per gli ingranaggi diventa sempre più importante.
- Con la continua evoluzione degli ingranaggi in termini di capacità di carico, la topologia del fianco del dente è sempre più importante. Durante il processo di rettifica a generazione, si verifica uno svergolamento naturale sui fianchi dei denti lavorati. Con l’innovativo software KN grind, questo fenomeno può ora essere preventivamente simulato, completamente eliminato o addirittura modificato in modo specifico.
- Un altro aspetto è la rugosità superficiale. Con un utensile standard, si possono ottenere valori di rugosità media Rz = 2,5 – 3 µm durante la rettifica a generazione in continuo. Per esigenze più elevate, Kapp Niles offre utensili combinati con due aree di lavoro diverse: una con grana standard e un’altra la rettifica di finitura o polishing, a seconda dei requisiti della superficie. Ciò consente di ottenere valori di rugosità Rz < 1 µm. L’aumento significativo del rapporto di contatto dei fianchi dei denti aumenta la capacità di carico massimo dell’ingranaggio. Un altro vantaggio di questo processo è che può essere integrato in catene di processo automatizzate con “one-piece-flow”, cosa finora non possibile.
Conclusione
La produzione di trasmissione elettrica richiede un know-how e soluzioni all’avanguardia maggiori rispetto allo standard delle trasmissioni per motori a combustione. Tuttavia, questo crea anche grandi opportunità per i produttori che hanno acquisito la padronanza dei più recenti metodi di produzione. La rettifica a generazione con utensili di piccole dimensioni è un tassello fondamentale. Oggi, Kapp Niles offre una vasta gamma di soluzioni che vanno ben oltre la classica produzione di macchine utensili. Il monitoraggio dei processi, la tracciabilità dei pezzi e l’assicurazione della qualità Inlinestanno diventando sempre più parte integrante dei moderni sistemi di produzione. In questo modo, anche i produttori altolocati sono in grado di reggere la concorrenza internazionale. Soprattutto in tempi in cui l’economia è diventata dolorosamente consapevole della vulnerabilità della produzione globalizzata, questa è un’enorme opportunità per contrastare le pressioni sui costi.
(Martin Witzsch, Ralf Dremel)