Fino a non molto tempo fa un tipico stabilimento per la produzione di motori o trasmissioni per il settore automobilistico si serviva di diversi macchinari, ognuno dedicato a una serie specifica e ristretta di operazioni. Insieme, questo gruppo di macchinari dedicati faceva parte di una linea di lavoro e trasferimento dove un pezzo grezzo veniva inviato lungo la linea e ogni macchina eseguiva una serie ristretta di operazioni di fresatura, foratura o maschiatura, noto come ciclo di lavoro, trasformandolo in un componente finito. I cuscinetti per mandrini venivano ottimizzati in ognuno di questi macchinari per il ciclo di lavoro specifico.
Ad ogni modo, i tempi sono cambiati e lo stesso ha fatto lo stabilimento tipico. Gli stabilimenti odierni hanno sostituito le loro linee di processo con dei centri di lavorazione CNC flessibili per aumentare l’efficienza, per lotti di produzione più ridotti e per permettere cambi tipo più frequenti. Questi macchinari CNC possono essere dotati da tre a nove assi controllati (in genere cinque) e utilizzano cambi-utensili automatici, magazzini utensili, nastri trasportatori e sistemi robotici di manipolazione e movimentazione dei pezzi sia grezzi che lavorati per eseguire una miriade di operazioni, ridurre i tempi di ciclo e favorire la massima efficacia delle operazioni negli stabilimenti di tutto il mondo.
Tuttavia, nel mondo della lavorazione meccanica diverse attività prevedono esigenze differenti. Molti di questi diversi materiali e operazioni hanno esigenze diametralmente opposte, per esempio, sui mandrini porta-fresa e, di conseguenza, anche sui cuscinetti per mandrini porta-fresa. I materiali possono variare dai tradizionali acciai alto-legati e dalla ghisa alle leghe in alluminio, titanio e nichel. Il materiale da lavorare determina i carichi e le velocità che devono essere applicati comportando conseguenze sui cuscinetti.
Pochi singoli componenti incidono sulle prestazioni globali così radicalmente come i cuscinetti per mandrini porta-utensili. I cuscinetti ne definiscono la velocità, la capacità di carico, la precisione e la rigidità. I cuscinetti contribuiscono alla temperatura di esercizio, alle vibrazioni e al rumore durante il funzionamento del mandrino. Le macchine utensili devono essere estremamente precise, affidabili e capaci di offrire elevati livelli di produttività. La precisione di un cuscinetto influenza enormemente la capacità di operare in un ambiente produttivo piuttosto che in un altro. Quando il cuscinetto smette di funzionare come previsto, l’intera macchina deve essere fermata e riparata.
Le prestazioni ottimizzate dipendono moltissimo dalla scelta del giusto cuscinetto per la giusta applicazione. Sia che siate progettisti di mandrini per macchine utensili presso un costruttore di primo equipaggiamento o un’officina di manutenzione, riparazione e revisione, le esigenze dell’applicazione finale sono d’importanza cruciale quando si seleziona un cuscinetto.
Confronto sulle diverse esigenze per diverse attività
Nell’ambito di una determinata applicazione, le velocità, i carichi e altri fattori possono variare drasticamente. Le condizioni di taglio in fase di finitura vengono scelte per generare una superficie del pezzo di qualità superiore, con vibrazioni minime, mentre condizioni di sgrossatura devono permettere la rimozione della quantità maggiore di materiale nel più breve tempo possibile. I tagli in fase di finitura sono superficiali e precisi, vengono ottenuti utilizzando solitamente un diametro ridotto dell’utensile ad una velocità del mandrino molto elevata e con un avanzamento molto ridotta (velocità lineare dell’utensile sul il pezzo lavorato). Di conseguenza si generano carichi sull’utensile molto ridotti, ma richiedono che il mandrino funzioni correttamente a una velocità molto elevata. I tagli di sgrossatura sono profondi e ampi, con un utensile di grande diametro a una velocità del mandrino relativamente ridotta e con un tasso di avanzamento molto elevato, generando un carico significativamente maggiore sull’utensile e, di conseguenza, anche sui cuscinetti del mandrino.
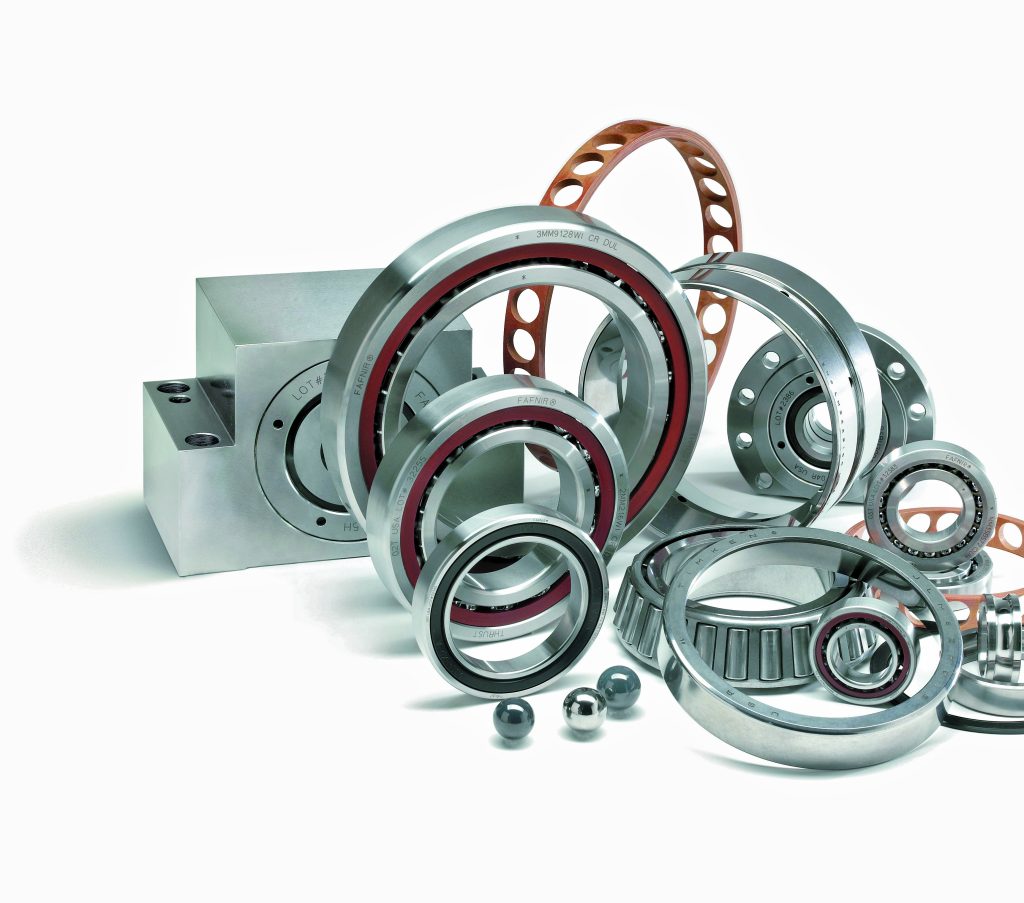
Quando le prestazioni di un centro di lavoro dipendono dai cuscinetti
Ognuna delle diverse condizioni di lavoro descritte precedentemente definisce esigenze specifiche relative allo stesso cuscinetto scelto per supportare l’albero del mandrino portautensile.
Si consideri che le esigenze di un’operazione di sgrossatura rispetto a quelle di finitura sono opposte e richiedono rispettivamente prestazioni del cuscinetto diverse (bassa velocità/carichi elevati contro alta velocità/carichi ridotti). Ecco perché: man mano che in un’applicazione la velocità aumenta, lo stesso accade per la forza centrifuga su ciascuna delle sfere del cuscinetto.
Questa forza centrifuga agisce radialmente allontanandosi dal centro di rotazione del cuscinetto (ipotizzando una struttura rotante di riferimento), con la pista esterna che impedisce alle sfere di uscire dal cuscinetto. Man mano che aumenta la forza centrifuga, il risultato è uno stress da contatto elevato tra la pista e le sfere. L’aumento della forza centrifuga inoltre guida il punto di contatto della sfera con la pista esterna verso la parte più profonda della pista. Tuttavia, l’esatto contrario si verifica tra la sfera e la pista interna, causando angoli diversi di contatto con le due piste interna ed esterna. Questo fenomeno è indicato come spostamento dell’angolo di contatto. Dal momento che la sfera è un corpo solido, essa può presentare solo un asse di rotazione, pertanto un maggiore spostamento dell’angolo di contatto causa slittamento, maggiore generazione di calore, temperature di esercizio più elevate e maggiore usura della superficie sulle sfere.
Un metodo per ridurre al minimo l’impatto degli effetti della maggiore forza centrifuga è semplicemente ridurre al minimo il peso delle sfere. Ci sono due modi per fare ciò: 1) ridurre la dimensione della sfera e/o 2) passare dall’acciaio alla ceramica, poiché le sfere in ceramica, a parità di dimensioni, sono il 40% più leggere rispetto alle controparti in acciaio. Le sfere più leggere generano una forza centrifuga ridotta che non compensa completamente lo stress di contatto più elevato derivante dal modulo di elasticità maggiore della ceramica. Tuttavia, la forza centrifuga più bassa riduce lo spostamento dell’angolo di contatto, il che comporta una inferiore generazione di calore causata dallo slittamento.
Un secondo metodo è aumentare il raggio della pista. Il rapporto tra il raggio della pista e il diametro della sfera è indicato come curvatura della pista ed è descritto matematicamente come il raggio della pista diviso per il diametro della sfera espresso in percentuale. Ad esempio, in caso di raggio della pista di 0,5 mm e con una sfera del diametro di 1 mm, la curvatura della pista è del 50 percento. Una curvatura della pista del 50 percento comporta un contatto linea su linea e il cuscinetto non ruoterebbe liberamente, quindi le curvature sono sempre maggiori del 50 percento. Le curvature sotto il 54 percento sono considerate chiuse, mentre quelle maggiori sono considerate aperte. I cuscinetti con curvature chiuse sono migliori in termini di capacità di carico, ma generano maggior calore, mentre i cuscinetti con curvature aperte possono raggiungere velocità maggiori, ma hanno capacità più ridotte.
Adottare di una di queste due misure per aumentare la possibilità di rotazione più veloce del cuscinetto, può ridurre drasticamente l’abilità del cuscinetto stesso di supportare i carichi e quindi ridurre la capacità del mandrino nelle operazioni di sgrossatura. In genere, sono disponibili due o tre design per una specifica serie dimensionale ISO che incorpora diverse dimensioni delle sfere e curvature delle piste, ciò per ottimizzare le prestazioni di un particolare profilo di taglio. Ecco perché è importante considerare il ciclo di lavoro previsto di un macchinario per poter scegliere il design e il materiale delle sfere ottimale.
Alcuni esempi
Sgrossatura e massima rimozione del metallo. I mandrini progettati per carichi pesanti agenti sull’utensile devono avere cuscinetti con sfere in acciaio più grandi possibile, ma che si inseriranno nella sezione trasversale del cuscinetto (> 50 percento della sezione del cuscinetto), nonché una curvatura della pista chiusa per ridurre lo stress da contatto tra la pista e la sfera. L’elevato diametro della sfera e la curvatura chiusa si adattano ai carichi pesanti e alle velocità ridotte associate alle operazioni di sgrossatura che possono variare tra 500 giri/min e 1500 giri/min a seconda del diametro dell’utensile, della velocità di rimozione del materiale e del materiale del pezzo lavorato. La maggior parte dei mandrini per sgrossatura utilizza grasso come metodo di lubrificazione e presenta valori compresi tra 3500 e 7500 giri/min a seconda della dimensione della macchina.
Finitura e ottimizzazione della velocità. Quando si progetta un mandrino per velocità elevate e tagli di finitura specifici, ridurre al minimo la generazione di calore deve essere il principio guida e il cuscinetto con sfera grande/curvatura chiusa, come sopra descritto, diventa meno preferibile a causa dell’eccessiva generazione di calore caratteristica di questo design. La scelta di un cuscinetto con sfere piccole (< 50 percento della sezione del cuscinetto) e con curvatura aperta genererà meno calore e pertanto una minore temperatura del mandrino. I mandrini per finitura ad alta velocità operano tra 7500 e 24000 giri/min ed usano aria/olio dosati come metodo di lubrificazione. I mandrini di finitura specifici possono raggiungere velocità comprese tra 15000 e 30000 giri/min, a seconda della dimensione della macchina.
Applicazioni polivalenti ottimizzate per carico e velocità. Se l’obiettivo del design è un mandrino che può eseguire sia tagli pesanti a velocità ridotte che tagli delicati a velocità elevate, la scelta di un cuscinetto che possa gestire entrambe le opposte esigenze è indispensabile. Tali esigenze, e tutto ciò che sta in mezzo, sono comuni per i centri di lavoro verticali. I progettisti devono ricercare un cuscinetto di precisione con capacità equilibrate che possa colmare il divario. Un cuscinetto con un design medio della sfera (~ 50 percento della sezione del cuscinetto), con una curvatura moderatamente aperta, produrrà una generazione di calore ridotta e una discreta capacità di carico. I centri di fresatura, ad esempio, che devono eseguire sia operazioni di sgrossatura che di finitura possono richiedere di lavorare a velocità che vanno da appena 500 giri/min a ben 12500 giri/min e utilizzano grasso o aria/olio dosati come metodo di lubrificazione. I mandrini universali presentano in genere valori di velocità raggiungibili compresi tra 7500 e 15000 giri/min, a seconda della dimensione della macchina.
Sfere in ceramica. Le sfere in ceramica vengono scelte generalmente quando il ciclo di lavoro del mandrino è soprattutto composto da operazioni di finitura ad alta velocità. Oltre a densità e peso minori, le sfere in ceramica hanno un modulo di elasticità più alto rispetto alle sfere in acciaio, il che produce un’ellisse di contatto ridotta (la forma dell’area di contatto tra la sfera e la pista causata dalla deformazione elastica della sfera e della pista di rotolamento dell’anello del cuscinetto). Più è piccola l’area di contatto, maggiore è lo stress da contatto tra la sfera e la pista sotto lo stesso carico. Se il carico esterno non produce uno stress eccessivo tra la sfera e la pista, il cuscinetto genererà meno calore a causa dell’inferiore area di contatto.
Il ruolo di Timken
La configurazione del cuscinetto che raggiunge il miglior equilibrio tra le dinamiche operative nell’intero ciclo di lavoro per una specifica applicazione è la soluzione di cuscinetto ottimizzata. Presso Timken Company sono stati eseguiti numerosi test e analisi sui cuscinetti e le loro diverse geometrie interne per aiutare i clienti a compiere le scelte più informate possibili. La gamma di cuscinetti Timken, con le loro diverse opzioni, ha dimostrato di offrire le prestazioni desiderate per un’ampia varietà di applicazioni di macchine utensili e i nostri esperti sono lieti di assistervi nel corso del processo di selezione, sia presso i produttori di mandrini per macchine utensili, che presso le officine di riparazione e ricondizionamento ovvero a livello di utilizzatore finale.
(Eric Faust, Application Engineering Specialist, The Timken Company)