Nelle applicazioni ingranaggistiche, i giunti scanalati vengono utilizzati per collegare ingranaggi e alberi e trasmettere una coppia (momento torcente) elevata [1]. Inoltre, gli accoppiamenti scanalati vengono utilizzati anche nei moderni motori aeronautici a turbina a gas per collegare gli alberi e compensare i disallineamenti [2]. La compensazione dei disallineamenti dell’albero porta ad una riduzione delle reazioni vincolari che si scaricano sulle parti circostanti della macchina [3]. Alla luce della riduzione delle sollecitazioni in conseguenza delle reazioni vincolari ridotte, il progettista è quindi in grado di ridurre il volume e il peso del sistema. Nel complesso, questo aspetto permette una riduzione dei costi di produzione grazie al downsizing e minor impiego di materiale. Inoltre, ciò ho un impatto diretto sull’efficienza del sistema e sulle emissioni [4].
La compensazione specifica dei disallineamenti dell’albero attraverso l’impego di giunti scanalati può portare a diversi vantaggi in molte applicazioni del gruppo propulsore. Vi è però un rovescio della medaglia: un crescente disallineamento all’interno dell’accoppiamento scanalato porta a crescenti velocità di strisciamento che, a loro volta, aumentano il rischio di usura e cedimenti per fatica superficiale [5]. Se tali danni (legati all’usura ed alla fatica) avvengono o meno dipende dal rapporto tra la sollecitazione in esercizio e la capacità di carico del materiale (sollecitazione ammissibile). Pur aumentando la sollecitazione del materiale a causa degli strisciamenti, è comunque necessario assicurare che la capacità di carico non venga mai superata. I fattori che influenzano la capacità di carico dei giunti scanalati includono il materiale ed il trattamento termico, la tecnologia di produzione, le proprietà superficiali (a seguito di trattamenti specifici) e le condizioni di funzionamento, tra cui lubrificazione e temperatura. Recenti ricerche volte a ridurre al minimo gli effetti dell’usura nei giunti scanalati ha portato allo sviluppo di trattamenti superficiali specifici, come il rivestimento PVD e la strutturazione laser [6].
Nel complesso, le performance richieste aumentano quando i giunti scanalati vengono utilizzati per la compensazione dei disallineamenti dell’albero. Al fine di consentire un funzionamento sicuro senza un eccessivo sovradimensionamento, non si può prescindere da una conoscenza dettagliata e una comprensione totale dei fattori di influenza sulla capacità di carico dei giunti scanalati in condizioni di disallineamento. Per poter studiare e valutare i fattori di influenza e le prestazioni di nuovi trattamenti superficiali per giunti scanalati sono necessarie prove sperimentali ad alta velocità di rotazione sotto carico ed in presenza di disallineamenti indotti e controllati. Considerando l’applicazione specifica, i.e. l’utilizzo dei giunti scanalati nei motori aeronautici delle turbine a gas, le prove sui componenti reali sono adatte per indagini di ricerca sistematica (in luce di costi eccessivi). Per ottenere risultati affidabili in modo più efficiente sia in termini di tempo che da un punto di vista economico, è essenziale la realizzazione di un banco prova dedicato. L’obiettivo di questo articolo è identificare e riassumere le diverse possibili configurazioni sperimentali per prove su giunti scanalati disponibili in letteratura e sulla base di quelle presentare un nuovo concept di banco prova, progettato per lo studio di giunti scanalati in condizioni di disallineamento, velocità di rotazione e coppie elevate ed in presenza di disallineamenti.
Analisi dello stato dell’arte
Gli accoppiamenti scanalati caricati in modo ciclico sono soggetti a fenomeni di fatica, fatica da contatto e usura [2]. Le campagne di caratterizzazione sperimentale della resistenza dei giunti scanalati a queste tipologie di danneggiamento, sono per lo più condotte su banchi prova che possono essere suddivisi in tre categorie:
- Test con provino semplice
- Test con giunti scanalati
- Test con giunti scanalati in condizioni di lavoro reali
Di seguito, vengono descritte diverse configurazioni sperimentali possibili (figura 1).
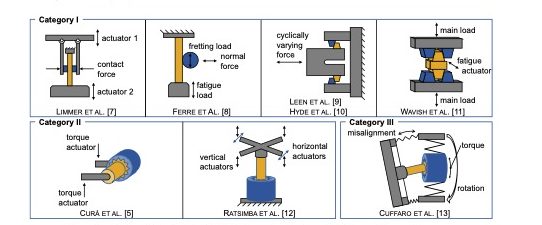
I. Test con provino semplice
Limmer et Al. affermano che l’utilizzo di macchine di prova idrauliche, quali semplici attuatori lineari, rappresenta un modo efficiente per ridurre i costi dei test, agendo sul costo di produzione dei campioni che per questa tipologia di prova risultano molto inferiori rispetto a quelli che prevedono l’impiego di giunti scanalati a grandezza naturale. Il provino viene bloccato tra due supporti, che vengono mossi su e giù. Le condizioni di contatto che si generano nei giunti scanalati in questa tipologia di test sono rappresentative del comportamento reale (figura 1). L’utilizzo di un attuatore permette la riduzione del tempo prova grazie alle elevate frequenze di lavoro [7].
Ferre et Al. hanno applicato un carico normale che, in combinazione al carico di un pulsatore, ha permesso di studiare la fatica da fretting. [8]
Hyde et Al. E Leen et Al. hanno utilizzato un campione scanalato rappresentativo dotato di fianchi dentati semplificati che permettessero di riprodurre le condizioni di contatto tipiche dei giunti scanalati. Con questa configurazione, Hyde et Al. e Leen et Al. hanno anch’essi condotto indagini di fretting [9, 10].
Wavish et Al. è andato oltre ed ha combinato un carico di serraggio normale ciclico a bassa frequenza e una sollecitazione da ciclico fuori piano e con frequenza più elevata. Ciò ha consentito indagini di fretting multi-assiali. [11]
II. Test con giunti scanalati
Curà et Al., utilizzato un pulsatore con un dispositivo a leva per la generazione della coppia, hanno condotto test direttamente su giunti scanalati. Per mezzo di questo dispositivo, è stato possibile condurre prove su componenti anche con carichi variabili. L’utilizzo del pulsatore permette test efficienti in termini di tempo [5].
Ratsimba et Al. ha studiato il cedimento a fatica e l’usura su una configurazione di prova che prevedeva più attuatori così da riprodurre anche carichi multi-assiali. Durante il test di un giunto scanalato, questo viene bloccato verticalmente e la coppia applicata per mezzo di due attuatori orizzontali montati su due leve opposte. Quattro ulteriori attuatori verticali, in combinazione con un sistema di leveraggi incrociati, permettono di riprodurre sia i carichi assiali, sia le forze di flessione rotanti che si hanno nei giunti scanalati in condizioni di disallineamento. Questa configurazione di test si è mostrata economicamente vantaggiosa [12].
Da un lato, i test con giunti scanalati consentono prove efficienti in termini di risorse e tempo grazie all’utilizzo di attuatori pulsanti e dispositivi a leva per la applicazione della coppia. D’altra parte, l’utilizzo di questi attuatori invece di giunti scanalati rotanti, comporta la non corretta riproduzione del moto del picco di pressione dovuto al contatto disallineato. Inoltre, la reale condizione di lubrificazione nell’ingranamento non viene riprodotta correttamente, principalmente a causa della mancanza delle forze centrifughe che invece si hanno nelle applicazioni reali (rotanti).
III. Test con giunti scanalati in condizioni di lavoro reali
Il collaudo dei giunti scanalati in condizioni di lavoro reali richiede una configurazione più complessa del banco prova in modo da tenere adeguatamente conto delle condizioni operative, i.e. della velocità di rotazione, del carico torsionale e del disallineamento dell’albero. CUFFARO ET AL. hanno presentato un banco prova per il test di giunti scanalati in grado di riprodurre in modo corretto tutti questi requisiti. Ciò è stato possibile installando un sistema di alberi coassiali divisi con ricircolo meccanico della potenza. A tale scopo, le due parti costituite da un albero interno ed uno esterno sono state collegate. Gli alberi interni sono stati collegati appunto mediante il giunto scanalato in prova, mentre gli alberi esterni mediante un giunto flessibile. Durante la rotazione di questo sistema di alberi, preventivamente caricato con la coppia di prova, il giunto scanalato opera nelle condizioni di lavoro più realistiche possibili. Per le prove in condizioni di disallineamento, le due parti del sistema possono essere inclinate l’una rispetto all’altra. Con questa configurazione di prova è stato possibile fornire una coppia massima Tmax = 5000 Nm e una velocità di rotazione massima nmax = 2000 giri/min. La temperatura massima è θmax = 60°C. In relazione a queste specifiche operative, le caratteristiche prestazionali del banco prova presentate da Cuffaro et Al. mirano ad applicazioni soggette ad elevate coppie ma con velocità di rotazione relativamente contenute [13].
Conclusioni sullo stato dell’arte
Come mostrato, la maggior parte dei banchi di prova per giunti scanalati descritti in letteratura sono stati costruiti come banchi di prova per analogia. I banchi prova con provino semplice riproducono una condizione di scorrimento tra i fianchi a contatto in modo semplificato. I vantaggi derivanti da test su banchi di prova con provini semplici vanno individuati nella semplicità di produzione del campione e in costi e tempo di prova contenuti grazie alle frequenze elevate degli attuatori lineare. Ciò consente test con valenza statistica in tempi e costi ragionevoli. Per contro, il principale svantaggio di siffatti banchi prova è da individuarsi nelle condizioni di lavoro che non riproducono in modo fedele quelle del componente in esercizio. La cinematica specifica del contatto del dente non è replicata sufficientemente bene neppure nei banchi prova che utilizzano veri giunti scanalati come provino. Infine, il movimento assiale della zona di contatto sul fianco del dente che è tipico dei giunti scanalati soggetti a disallineamento in esercizio, non può essere riprodotta sui banchi prova esistenti. Per esaminare a fondo i meccanismi di danneggiamento e i fenomeni di usura dei giunti scanalati in presenza di disallineamento, è dunque necessario testare i giunti scanalati nelle condizioni di lavoro reali. Un banco prova che può essere utilizzato per questo scopo è descritto da Cuffaro et Al.. La soluzione è però idonea solo per coppie elevate e velocità di rotazione e temperature moderate. Tuttavia, velocità di rotazione e temperature elevate sono caratteristiche dei motori aeronautici a turbina a gas. Vi è quindi un deficit nella capacità di testare giunti scanalati in condizioni di prova simili a quelle di esercizio. L’obiettivo di questo documento è quello di presentare un banco prova di nuova concezione ed una geometria di giunto scanalato che possa essere testata ad alta velocità di rotazione e ad alta temperatura anche in condizioni di disallineamenti. A tale scopo si è modificato un banco prova back-to-back. Oltre all’elevata velocità di rotazione, è ora possibile eseguire test a temperature (fino a un massimo di θmax = 120 °C) grazie all’iniezione controllata di olio nell’ingranamento.
Progettazione di un giunto scanalato per test sperimentali
Per studiare i fenomeni di usura dei giunti scanalati disallineati in condizioni di lavoro quanto più realistiche possibile – alta velocità di rotazione, coppia media e alte temperature di esercizio – sono stati progettati un giunto scanalato su scala reale e il relativo banco prova. Il progetto della geometria dello scanalato è mostrato in figura 2. Nel processo di progettazione, l’obiettivo è stato quello di generare le stesse condizioni di contatto che si hanno tra il fianco dei denti dei giunti scanalati che operano nelle turbine a gas dei motori aeronautici. Per poter effettuare i test sui banchi di prova esistenti, le dimensioni della scanalatura di prova sono state ridotte rispetto all’applicazione reale. Per garantire che le condizioni di contatto siano simili a quelle dell’applicazione reale, in fase di progettazione si è data enfasi alla pressione di contatto ed al rapporto tra le velocità di scorrimento.
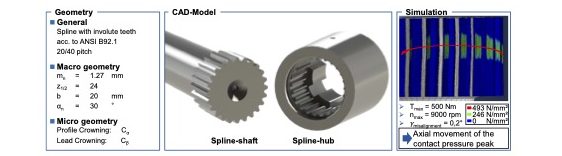
Definito un valore di riferimento per la pressione di contatto, la macro-geometria è stata progettata secondo ANSI B92.1 in modo da adattarsi alla coppia tipica dei banchi di prova back-to-back [14]. Inoltre, la micro-geometria ed il disallineamento γdisallineamento dell’albero sono stati scelti in modo da riprodurre al meglio la cinematica dell’applicazione reale. Le sollecitazioni in condizione di disallineamento sono state calcolate mediante simulazioni agli elementi finiti. Nel funzionamento in presenza di carichi e disallineamenti, i picchi di pressione si muovono assialmente (lungo i fianchi dei denti) in modo ciclico ad ogni rotazione. Lo spostamento della zona di contatto ottenuta mediante l’analisi statica è riportata in figura 2. Con questi dati e la velocità di rotazione, è stata calcolata la cinematica del contatto. Il movimento della zona di contatto può essere descritto da una funzione ciclica in funzione della velocità di scorrimento. Per il calcolo del movimento della zona di contatto serve considerare non solo la velocità di rotazione e la distanza tra le zone di contatto, ma anche la funzione che descrive la velocità di scorrimento. Per calcolare la massima velocità di scorrimento locale – e non solo la massima velocità di scorrimento globale – serve tenere conto della non linearità (comportamento sinusoidale) dello scorrimento in funzione di velocità. Sulla base di questo calcolo, il design dei profili scanalati può essere ottimizzato in modo da ottenere la pressione di contatto desiderata che riproduca le reali condizioni di esercizio.
Per valutare le capacità dei trattamenti superficiali di nuova concezione di aumentare la resistenza ad usura e fatica da contatto, i giunti scanalati per i test sono stati prodotti in acciaio da nitrurazione 32CDV1. Questo materiale è ampiamente utilizzato nelle applicazioni aerospaziali ed è stato scelto per soddisfare l’applicazione specifica di una turbina a gas per motori aeronautici. Per la produzione, il processo ha seguito gli step consueti tipici della produzione di ingranaggi, (figura 3).
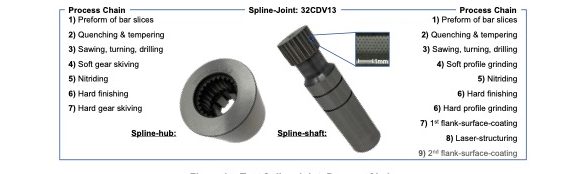
Dopo la tempra e il rinvenimento, vi è stata una prima lavorazione dei grezzi, seguita dal taglio dei profili scanalati. Successivamente, i campioni sono stati nitrurati al plasma e le superfici funzionali finite alle macchine utensili. Per la produzione dei profili dentati, è stato eseguito un processo di skiving. Solo a questo punto sono state applicate le diverse ottimizzazioni della superficie. A tale scopo sono stati utilizzati i rivestimenti e la strutturazione descritti da Stephen et Al. [15]. Sono state prodotte due diverse varianti in termini di deposizione fisica da vapore (PVD) per generare rivestimenti multistrato TiN + MoS2: Ti e TiN + DLC + MoS: Ti: C. Inoltre, è stata eseguita una strutturazione laser, in cui sono state generate ondulazioni con diametri compresi tra dstruct = da 40 a 80 μm su tutti i fianchi dei denti, come mostrato in figura 3. Infine, è stato applicato un secondo rivestimento con un lubrificante solido.
Siffatti giunti scanalati sono successivamente stati testati in termini di resistenza all’usura in condizioni di disallineamento. Al fine di realizzare condizioni di prova riproducibili in modo economico e veloce, si è sviluppato un banco prova specifico per questo tipo di indagini.
Progettazione di banchi di prova
Un metodo comunemente utilizzato nelle prove sotto carico degli ingranaggi consiste nell’utilizzare una configurazione che prevede il ricircolo di potenza (meccanica). L’idea alla base di questo approccio è quella di applicare e “intrappolare” una coppia statica in un circuito chiuso attraverso elementi cedevoli pretensionati. Un motore mette quindi in rotazione il sistema [16] che, grazie alla coppia statica intrappolata in precedenza, deve solo vincere le dissipazioni di potenza del sistema dovute agli attriti e non invece fornire la potenza di prova effettiva.
Ciò porta a un design del banco prova particolarmente economico in esercizio, poiché durante i test deve essere fornita solo l’energia che viene dissipata dal sistema per via degli attriti e non tutta la potenza che viene trasmessa dagli ingranaggi in prova. Un banco prova che disponga di un circuito di alimentazione e viene ampiamente utilizzato per questa tipologia ti test è il cosiddetto banco prova back-to-back, standardizzato secondo DIN ISO 14635 [17]. Questo banco prova è progettato specificatamente per studiare ingranaggi cilindrici. Nel seguito viene presentata un’estensione di tale banco prova back-to-back, per consentire il collaudo dei giunti scanalati, (figura 4). Sulla base della geometria degli scanalati di prova e della pressione di contatto desiderata, la progettazione del banco ha tenuto in considerazione i seguenti requisiti:
- Coppia di prova: Tmax = 500 Nm
- Velocità di rotazione: nmax = 9000 rpm
- Disallineamento albero dedicato: γdisallineamento = 0,2°
Al fine di coprire l’intero range di esercizio dei giunti scanalati analizzati, è stato utilizzato un banco prova back-to-back con un interasse a = 112,5 mm. Per i test, si è integrato un giunto scanalato nel circuito di alimentazione del banco prova. Pertanto, il sistema di alberi della configurazione standard è stato riconfigurato. Sul lato motore, per guadagnare spazio per la scanalati di prova, è stata rimossa la frizione originale, sostituita da una frizione assiale compatta e un albero torsionale. Sul lato motore, è stato montato un nuovo sistema di cuscinetti dati che la velocità di rotazione dei giunti scanalati è maggiore di quella per cui il banco back-to-back era stato progettato (nmax = 9000 giri/min). Sono inoltre stati progettati due nuovi alberi per integrare il giunto scanalato nel circuito chiuso. L’albero scanalato cavo è stato montato direttamente sul lato destro del banco: l’albero scanalato è stato fissato all’albero laterale sinistro con connessioni idrauliche albero-mozzo, che possono essere rimosse durante il montaggio. Per stabilizzare ulteriormente il giunto scanalato, si è introdotto un ulteriore cuscinetto di supporto. L’alloggiamento protegge il giunto scanalato durante il test, sigilla lo spazio di prova prevenendo trafilamenti di olio e consente il mantenimento di una temperatura di prova costante.
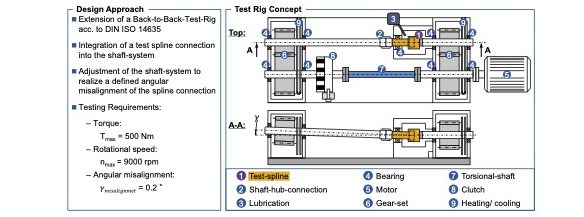
Per generare il disallineamento del giunto (γdisallineamento = 0,2°), il lato sinistro del sistema è stato inclinato verso l’alto attorno al centro del giunto scanalati, (figura 4). A tale scopo sono stati progettati boccole e cuscinetti speciali. Le sedi dei cuscinetti dell’albero laterale sinistro sono state allineate con la deviazione necessaria dall’asse dell’albero laterale destro così da generare il disallineamento richiesto. Per ottenere un’elevata precisione per le sedi dei cuscinetti, la lavorazione finale è stata eseguita in un unico afferraggio. Con questa procedura, il disallineamento angolare risulta molto preciso. Per modificare il disallineamento è necessario cambiare le boccole dei cuscinetti. Il vantaggio di questo design è che il disallineamento è fisso per l’assieme e quindi rimane lo stesso per tutti i test di una serie. Sono poi stati installati due set di ingranaggi cilindrici in modo dar collegare albero motore e scanalati e aumentare la velocità di rotazione del motore a quella di prova. Considerando il disallineamento angolare dell’albero scanalato, anche la micro-geometria degli ingranaggi di servizio è stata appositamente progettata per questa applicazione. Il disallineamento angolare degli ingranaggi di servizio è dunque compensato per evitare un aumento della pressione di contatto dovuto all’usura del bordo.
Infine, il banco è stato modificato anche per quanto riguarda l’approvvigionamento di olio così da garantire una portata specifica a una temperatura di iniezione controllata. Con questa estensione, il giunto scanalato può essere testato in condizioni di contatto lubrificate. Durante il funzionamento, l’olio viene costantemente iniettato nel giunto. Una tenuta aggiuntiva, il cui diametro interno è inferiore al diametro del giunto scanalato, crea un bagno d’olio che riduce il flusso di olio, (figura 5). Poiché la temperatura di iniezione dell’olio è controllata, sono possibili test a temperature fino a θmax = 120°C, il che consente di riprodurre le condizioni all’applicazione reale.
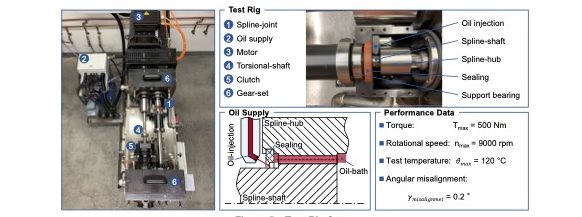
Per assicurarsi la correttezza del disallineamento dell’albero, è stata eseguita un’ulteriore misurazione delle sedi dei cuscinetti su una macchina di misura a coordinate. Nonostante la distanza tra le sedi dei cuscinetti fosse di ≈ 600 mm, le lavorazioni sono risultata precise è ciò è evidenziato dalla linea retta che attraversa i punti di misura, che riflette la posizione reale dell’asse del banco di prova. Inoltre, considerando l’allineamento di questo asse con l’asse generato dalle sedi dei cuscinetti già esistenti, il disallineamento angolare effettivo del banco prova è misurato a γmisura = 0,2006° con un punto di intersezione dell’asse dell’albero che si incontra al centro del giunto scanalato, (figura 6).
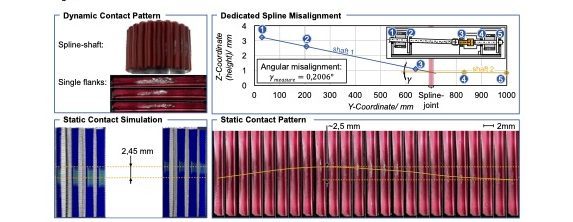
Il progetto del banco prova per giunti scanalati è stato testato anche per quanto riguarda movimento assiale del picco di pressione di contatto. Per la progettazione è stato utilizzato un modello di contatto statico. Per la verifica, la frizione del banco prova è stata bloccata ed è stata applicata una coppia ciclica per alcuni minuti. Sotto questo carico, l’oscillazione dei contatti laterali risultante dal disallineamento angolare diventa visibile anche nel modello di contatto statico. La distribuzione del contatto, segue una curva sinusoidale sulla circonferenza, (figura 6). Il confronto dei risultati della simulazione statica con quelli misurati è soddisfacente: la lunghezza del contatto calcolata è pari a ΔCL,simulazione = 2,45 mm vs misurata di ΔCL,misura ≈ 2,5 mm. Inoltre, tramite un modello di contatto dinamico si sono verificate le misurazioni precedenti in termini di disallineamento dell’albero. Per taratre il modello di contatto dinamico, l’albero scanalato è stato verniciato (con prodotti speciali) prima del montaggio ed è stato posto in rotazione sotto l’azione di una coppia moderata. Il modello di contatto dinamico mostra come i giunti scanalati reali in combinazione con il nuovo banco generano una zona di contatto centrata sui fianchi degli scanalati.
La messa in servizio del banco prova è stata completata con i test. La capacità del banco prova di generare fenomeni di usura e fatica su giunti scanalati disallineati è stata provata dal verificarsi di cedimenti del fianco dei denti, (figura 7). Un primo campione rettificato ha mostrato, durante l’analisi delle superfici di frattura, una zona di contatto con lievi cambiamenti nell’aspetto. Procedendo nel test, si è manifestato un danno con rimozione del materiale nella zona di contatto. In una seconda fase, è stato testato un campione rivestito così da validare la capacità della configurazione del banco prova di generazione un’usura del rivestimento. Poiché i diversi strati di rivestimento hanno colori diversi, l’usura del rivestimento è stata analizzata attraverso immagini microscopiche, (figura 7). Per questo rivestimento, lo strato superiore in MoS2:Ti risulta chiaramente visibile. Come strato intermedio, è stato utilizzato uno strato a-C:H:Ti (area nera), dove è stato rimosso il top-layer. Infine, lo strato inferiore TiN è diventato visibile nelle aree che appaiono dorate. Al verificarsi di un cedimento totale del rivestimento, anche il materiale del substrato è emerso ed appare con una tonalità grigia.
Il verificarsi di cedimenti del fianco ha dimostrato la capacità del banco prova presentato, in combinazione con la geometria del giunto scanalato utilizzato come provino, di portare a fenomeni di usura e fatica nei giunti scanalati in presenza di disallineamenti. A seguito dei test preliminari su diversi trattamenti superficiali e ottimizzazioni (e.g. rivestimenti e strutturazione laser), verranno eseguite ulteriori prove volte aumentare la capacità di carico dei giunti scanalati.

Conclusione e sviluppi futuri
Lo stato dell’arte mostra come esistano varie configurazioni per lo studio dei fenomeni di usura e fatica dei giunti scanalati. Nella maggior parte delle configurazioni esistenti, vengono condotti test con provini semplici o giunti scanalati reali per generare le condizioni di contatto tipiche delle reali condizioni di esercizio. Soprattutto per quanto riguarda le pressioni di contatto che si generano nei giunti scanalati rotanti e disallineati, l’impiego di banchi di prova tradizionali porta a trascurare alcuni aspetti, di fatto non riproducendo appieno le condizioni al contorno nel contatto. Pertanto, diventa evidente come per un’indagine completa, debbano essere eseguiti test sui componenti scanalati in condizioni operative realistiche. CUFFARO ET AL. hanno presentato un banco prova per lo studio di giunti scanalati in condizioni di disallineamento. Il banco è progettato per indagini ad alta coppia, velocità di rotazione limitata e basse temperature [13]. Per studiare giunti scanalati disallineati ad alta velocità di rotazione, coppia media e temperature di prova elevate, sono necessarie configurazione di prova alternative.
Nel presente studio è stato presentato un nuovo design di giunto scanalato che, in combinazione a un banco prova back-to-back modificato, consente il collaudo di giunti scanalati ad alta velocità di rotazione, coppia media, alta temperatura di prova e in presenza di disallineamenti angolari. L’approccio progettuale si basa su una simulazione delle condizioni di contatto con particolare attenzione alla pressione e alla cinematica di contatto. Inoltre, è stata presentata l’estensione di un banco prova back-to-back che consente l’integrazione di un giunto scanalato nel circuito di potenza del banco prova. Il banco modificato consente la riproduzione di disallineamenti angolari. La combinazione del nuovo banco prova con il giunto scanalato sviluppato è in grado di generare i carichi tipici che si hanno in esercizio nei giunti scanalati disallineati. Pertanto, il banco prova può essere utilizzato per test con fedele riproduzione delle condizioni reali di esercizio. I cedimenti che si sono verificati durante la messa in servizio del banco prova hanno mostrato la capacità della configurazione di generare fenomeni di usura e fatica nei giunti scanalati disallineati ad alta velocità di rotazione, coppia media e temperature elevate.
In futuro, i giunti scanalati saranno testati sul banco prova sviluppato al fine di valutare i fenomeni di usura e fatica che si verificano in diverse condizioni di esercizio. I benefici dati dai trattamenti superficiali speciali, quali rivestimenti e strutturazione laser, saranno valutati al fine di dimostrarne il potenziale per applicazioni industriali. Inoltre, è possibile progettare nuove geometrie der i giunti scanalati in modo da riprodurre diverse condizioni di contatto sfruttando il banco prova esistente. Pertanto, nel breve futuro sono previste ulteriori indagini sulle variabili di influenza sulla capacità di carico del giunto scanalato, tra cui materiali diversi, trattamenti termici, condizioni superficiali e ottimizzazioni, lubrificazioni, temperature di prova o micro-geometrie. Da questa ricerca si spera di riuscire a identificare nuove soluzioni che consentano un aumento della densità di potenza permettendo di ridurre i margini di sicurezza grazie ad una maggiore conoscenza dei fenomeni di cedimento e alla disponibilità di maggiori dati a riguardo. Raggiungere questo obiettivo, permetterebbe un miglioramento dei sistemi che a sua volta consentirebbe una riduzione dei costi di produzione e del consumo energetico delle moderne turbine a gas per motori aeronautici.
Riconoscimento
Questo documento fa parte di un progetto che ha ricevuto finanziamenti Clean Sky 2 nell’ambito del programma di ricerca e innovazione Horizon 2020 dell’Unione europea sotto sovvenzione accordo n. 821344. Inoltre, gli autori desiderano ringraziare il DFG per il finanziamento di una macchina sperimentale (DFG-State Major Instrumentation INST 222/1251-1 FUGG).
(Gerrit Hellenbrand, Dieter Mevissen, Jens Brimmers, Christian Brecher, Laboratorio di Macchine Utensili e Ingegneria di Produzione (WZL), RWTH Università)