Questa ricerca proposta dagli autori dell’università italiana mostra un interessante approfondimento sul processo di formatura superplastica: risulta infatti particolarmente importante approfondire la conoscenza anche di lavorazioni meno diffuse.
Il moderno contesto manifatturiero spinge e motiva tutti gli attori coinvolti ad evolvere dal punto di vista produttivo. Le richieste di componenti da parte dei clienti sono sempre più ambiziose: le geometrie sono complesse, gli standard qualitativi sono elevati e le tempistiche sono risicate. Questo sfidante contesto obbliga i produttori a valutare e studiare l’introduzione di nuove tecnologie in grado di soddisfare le ultime richieste. Ciò è importante non solo per attrarre nuovi clienti, ma anche per mantenere fedeli i propri, ampliando il portafoglio dell’offerta ed aumentando i vantaggi competitivi rispetto ai concorrenti.
Offrire processi innovativi non è chiaramente mai semplice, l’introduzione di nuove soluzioni implica la gestione di nuove sfide e la risoluzione di problemi. Il mondo della ricerca risulta però un valido alleato poiché spesso è già al lavoro da anni sui processi innovativi ed è quindi in grado di offrire valide soluzioni applicabili anche in ambito produttivo.
La formatura superplastica
Negli ultimi anni le richieste, specialmente nel campo dei trasporti (e.g. settore automotive o aerospaziale), sono evolute verso materiali strutturali leggeri come le leghe di alluminio. La necessità di assicurare elevati standard dal punto di vista della sicurezza e dell’efficienza energetica obbligano i produttori a trovare nuove soluzioni. Queste applicazioni implicano spesso il ricorso a geometrie complesse. Il processo di formatura superplastica (abbreviato come “SPF”) rappresenta una valida soluzione in grado di creare i componenti richiesti assicurando un’alta qualità dal punto di vista della finitura superficiale e dell’accuratezza di forma. Il processo di formatura superplastica sfrutta il fenomeno metallurgico della superplasticità per trasformare componenti metallici complessi. Il materiale viene scaldato alla giusta temperatura, diventando morbido e permettendo di essere lavorato con processi simili a quelli utilizzati per materiali plastici.
Solitamente un gas inerte ad alta temperatura viene introdotto nello stampo per trasformare la lamiera nella geometria desiderata (Figura 1). In questo modo è possibile lavorare componenti larghi e complessi in una singola operazione assicurando una qualità elevata. Inoltre non sono presenti difetti di ritorno elastico o stress residui poiché si lavora a caldo. Viene inoltre richiesta una ridotta energia per la trasformazione e non sono necessarie costose attrezzature. D’altra parte si tratta di un processo non particolarmente rapido, risultando quindi adatto per volumi produttivi medio-bassi. Un’altra caratteristica del processo è quella di produrre componenti dallo spessore non uniforme. Per minimizzare questo effetto risulta importante lavorare sul coefficiente d’attrito, così da gestirne gli effetti durante la lavorazione.
Coefficiente d’attrito
Per comprendere a pieno il processo di formatura superplastica, non si può prescindere dalla valutazione del coefficiente d’attrito (in inglese “coefficient of friction” o “COF”). Esso tiene in considerazione i fenomeni di attrito tra la lamiera e lo stampo ed è un parametro essenziale per ottenere risultati finali soddisfacenti dal punto di vista qualitativo e per preservare la vita dell’attrezzatura. Come accade per altri processi di formatura, l’attrito deve essere controllato durante la lavorazione per permettere di ottenere l’assottigliamento desiderato della lamiera. Spesso vengono utilizzati ricoprimenti superficiali per ridurre il più possibile gli attriti, ma bisogna considerare che in alcune aree gli effetti dell’attrito potrebbero essere benefici, ad esempio su angoli netti dello stampo. Inoltre l’eccesso di lubrificanti può causare danni ambientali e difetti estetici. Per il processo di formatura superplastica, a causa delle alte temperature utilizzate, i lubrificanti tradizionali a base oleosa brucerebbero a contatto con la lamiera, bisogna quindi impiegare lubrificanti solidi, solitamente a base grafite.
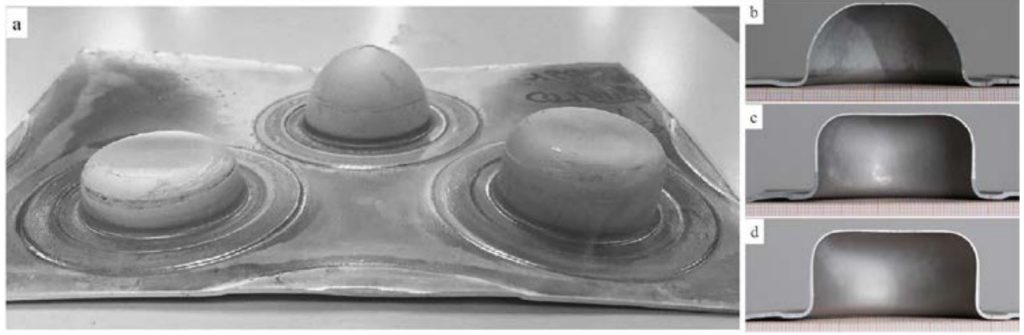
Tradizionalmente il coefficiente d’attrito viene assunto come costante durante l’intero processo di formatura. Questa semplificazione viene effettuata poiché risulta particolarmente complesso determinare il valore reale del coefficiente a causa della sua dipendenza da diversi parametri. Anche le metodologie di test tradizionali non risultano adeguate a valutare accuratamente tutti questi parametri. Per superare questo problema gli autori della ricerca propongono una nuova metodologia sperimentale per meglio valutare gli attriti.
La sperimentazione
Le valutazioni sperimentali sono state effettuate con provini fisici ottenuti lavorando una lamiera in lega di alluminio 5XXX avente uno spessore iniziale di 1.3 mm. Lo stampo è riscaldato a 500 °C e la temperatura è controllata ad anello chiuso. Le geometrie sono state appositamente studiate per replicare diverse situazioni realistiche. Sullo stampo non è stato applicato nessun lubrificante e le superfici sono state pulite dopo ogni test. La pressione di lavorazione è stata impostata come costante a 0.7+0.01 MPa utilizzando valori tipici per la produzione di questo materiale. Per studiare l’evoluzione (Figura 2), il processo è stato interrotto in diverse fasi, valutandone i risultati sui componenti e confrontandoli con le simulazioni.
Una simulazione ad elementi finiti è stata effettuata per avere un preciso riscontro digitale del processo di trasformazione. Un modello assialsimmetrico in 2D è stato creato utilizzando il software commerciale ABAQUS. Il processo è stato ricreato digitalmente partizionando il componente in elementi di piccola dimensione (0.26 mm) e valutando l’interazione tra di essi. Un nuovo approccio è stato impiegato per stimare il coefficiente d’attrito in questo processo come dipendente dalla deformazione. I risultati della simulazione, ottenuti in diverse fasi del processo, sono poi stati messi a confronto con i risultati dei provini fisici così da ottenere un riscontro reale.
I risultati
Il confronto tra i provini fisici e le simulazioni digitali ha permesso di notare interessanti effetti. Innanzitutto è stato possibile notare che la deformazione della lamiera è localizzata nelle prime fasi del processo. Il tasso di deformazione è maggiore inizialmente, quando il materiale è libero di espandersi, mentre nelle fasi successive le deformazioni rallentano. Inoltre, il modello numerico (Figura 3) è stato adeguato definendo le costanti in grado di meglio approssimare i risultati. È stato svolto un confronto tra i risultati sperimentali e tra i modelli numerici con coefficienti d’attrito fissi e variabili seguendo il modello “SDL”. Questa soluzione offre i risultati migliori. Gli algoritmi alternativi a valore costante tendono invece a sottostimare lo spessore al centro dei componenti, mentre sovrastimano lo spessore nelle aree periferiche.
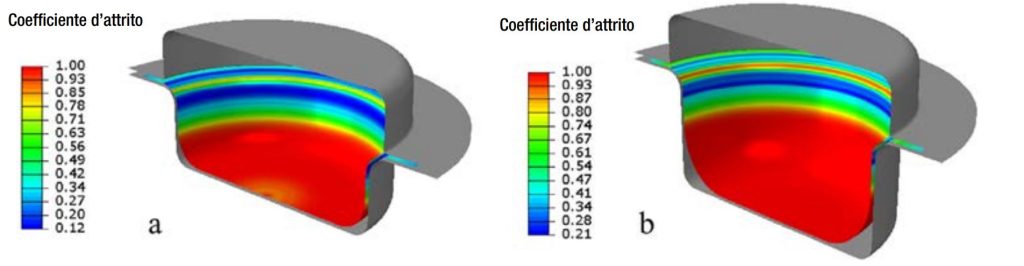
La ricerca proposta dagli autori dell’università italiana mostra un interessante approfondimento sul processo di formatura superplastica. Risulta particolarmente importante approfondire la conoscenza anche di lavorazioni meno diffuse. Dato il crescente interesse in nuovi processi, è fondamentale che il mondo universitario, insieme alle aziende, riesca a creare solide fondamenta della conoscenza. I moderni strumenti digitali, insieme alle conoscenze degli esperti, permettono di ottenere stime sempre più accurate sui processi manifatturieri. In un mondo in rapida evoluzione è infatti sempre più importante continuare a innovare e a proporre soluzioni per soddisfare clienti ed utilizzatori finali.
Fonte: Sorgente, D., Lombardi, A., Coviello, D., Scintilla, L. D., & Fontana, M. (2022). A strain-dependent model for the coefficient of friction in the tool-blank interaction in superplastic forming. Journal of Manufacturing Processes, 73, 791–798. https://doi.org/10.1016/j.jmapro.2021.11.050