La generazione di calore a seguito degli attriti che si hanno nei contatti tra denti spinge i progettisti a prevedere sistemi di raffreddamento attivi, e questo riduce ulteriormente l’energia netta a disposizione. È noto come una variazione della rugosità superficiale dei fianchi a contatto abbia un’influenza diretta sugli attriti. Le condizioni di lubrificazione mista sono molto comuni negli ingranaggi; in tali condizioni sia il contatto tra le asperità, sia la presenza stessa del lubrificante contribuiscono ad una dissipazione di energia. Finiture superficiali differenti delle superfici a contatto portano a interazioni tra le asperità molto differenti. I progettisti ed i produttori di ingranaggi devono riuscire a bilanciare in modo accorto i benefici dati da finiture superficiali sempre migliori con il loro costo di produzione. In questo studio viene descritta una metodologia basata su modelli di contatto, modelli statistici di micro-contatto e modelli reologici del lubrificante, volta a predire l’attrito nei contatti in condizione di lubrificazione mista e stimare così le perdite di potenza.
Come primo passo sono state raccolte un gran numero di misure profilometriche relative a varie finiture superficiali. Tali dati sono usati come input nel modello di previsione dell’attrito e delle perdite di potenza per diverse combinazioni di finiture (tipicamente utilizzate nel settore automotive) per i due fianchi a contatto. I risultati sono stati confrontati tra loro per stimare il potenziale delle diverse finiture superficiali su una riduzione delle perdite.
Introduzione
Le perdite meccaniche di potenza negli ingranaggi sono imputabili agli strisciamenti che si hanno nel contatto volvente per effetto degli attriti. Ciò porta ad una generazione di calore e dissipazione di energia.
Tale perdita di potenza non solo rappresenta uno spreco di energia ma implica anche maggiori costi legati alla necessità di prevedere sistemi di raffreddamento attivi volti a dissipare il calore generato nel contatto evitando così possibili cedimenti.
Pertanto, sia dal punto di vista economico che della durata (affidabilità), è di grande interesse pratico ridurre al minimo le perdite per attrito tra i denti.
I contatti lubrificati degli ingranaggi operano in regime misto elasto-idrodinamico (EHL), ovvero un regime in cui il carico è sostenuto principalmente dal film lubrificante sebbene vi possano essere contatti tra le asperità superficiali. La finitura superficiale dei fianchi a contatto influenza direttamente le interazioni tra le asperità. I progettisti e i produttori di ingranaggi cercano di bilanciare nel modo migliore i costi associati ai processi di finitura superficiale con un funzionamento ottimale della trasmissione. Questo studio utilizza un approccio in forma chiusa che combina un modello di distribuzione del carico, un modello statistico del micro-contatto e un modello reologico di lubrificazione per prevedere l’attrito in condizioni di lubrificazione mista e le relative perdite di potenza per attrito.
A tale scopo sono state raccolte numerose misure di rugosità del fianco, effettuate con un profilometro, su componenti realizzati mediante un’ampia gamma di processi produttivi differenti. I dati raccolti sono stati inseriti nel modello per la stima del coefficiente di attrito e delle perdite di potenza associate. La gamma di combinazioni di finiture superficiali presa in considerazione è rappresentativa delle diverse condizioni operative tipiche delle applicazioni automobilistiche.
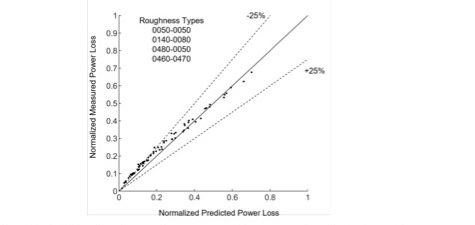
Modello di previsione della perdita di potenza degli ingranaggi
Il modello utilizzato per prevedere la perdita di potenza (media) degli ingranaggi è stato sviluppato da [1]. Tale modello riesce a calcolare le condizioni di carico dei fianchi utilizzando un modello di distribuzione del carico LDP [2]. Lo spessore del film nel contatto viene stimato utilizzando la formulazione di Dowson e Toyoda [3]. Lo spessore del film viene quindi utilizzato come parametro per il modello di micro-contatto di Greenwood e Williamson [4], noto come modello GW. Questo modello permette la stima dell’area di contatto tra asperità superficiali sulla base di un valore noto di separazione (ndr spessore del film). La rugosità è parametrizzata in funzione della densità delle asperità e del raggio di punta di queste, considerando una distribuzione stocastica delle altezze dei picchi. I parametri sono stimati a partire dalle misure 2D dei profili di rugosità, acquisite utilizzando il metodo proposto da McCool [5]. Il metodo McCool permette di separare il piano medio del profilo, correlato allo spessore del film, dal piano di vertice, necessario per impostare il modello GW. Sulla base del rapporto di contatto definito dal modello GW, il coefficiente di attrito può essere stimato tramite il metodo di Tallian [6] in modo tale che:
? = ???? + ?? ??
(1)
In cui:
μ è il coefficiente di attrito effettivo del contatto
μB è il coefficiente di attrito limite
μE è il coefficiente di attrito EHL (Couette)
PB è l’area di attrito limite del contatto
PE è l’area di attrito EHL del contatto.
Il coefficiente di attrito limite è stato ricavato da una misura empirica [7] e fissato al valore ?? = 0,1. Per quanto riguarda il coefficiente di attrito EHL, si ipotizza che questo sia principalmente legato alla componente di perdita per scorrimento (flusso di Couette) e alla perdita per rotolamento, assumendo l’isteresi elastica essere trascurabile. Il coefficiente di attrito EHL è quindi definito come:
μE = 1/PC ((?* VS)/(hmin))
?? è la pressione di contatto hertziana
?* è la viscosità effettiva di Ree-Eyring
?s è la velocità di scorrimento
ℎmin è lo spessore minimo del film di Dowson e Toyoda
Definito il coefficiente di attrito effettivo, la perdita di potenza può essere calcolata come lavoro dovuto allo scorrimento tra le due superfici. Per un ingranaggio, le velocità di scorrimento variano linearmente con l’angolo di rotolamento. La velocità media di scorrimento può quindi essere definita come:
??̂=[??(??,?)+??(??,?)]/4
in cui:
??,? è l’angolo di rotolamento alla fine del profilo attivo del pignone
??,? è l’angolo di rotolamento alla fine del profilo attivo della ruota.
Il lavoro medio dovuto all’attrito nell’ingranaggio può essere descritto come il lavoro medio compiuto in un ciclo di ingranamento.
??=?̂??̂??
Dove:
?̂ è il coefficiente di attrito medio
??̂ è la velocità di scorrimento media
Fm è la forza trasmessa.
La validazione del modello è stata eseguita utilizzando i dati misurati, in termini di perdite di potenza, per varie combinazioni pignone-ingranaggio (i.e. aventi ogni volta differente rugosità superficiale). Nell’analisi sono stati condotti test sia su coppie aventi stessa finitura (superfici lavorate allo stesso modo), sia dissimili (superfici finite in modo diverso). Le previsioni teoriche risultano strettamente correlate ai valori misurati per tutti gli accoppiamenti e le condizioni di prova. La figura 1 mostra i risultati di questo confronto, adattati da [1].
Matrice di simulazione e analisi del profilo di rugosità
Il modello di perdita è stato utilizzato per capire come la dissipazione di potenza meccanica media degli ingranaggi venga influenzata dalla finitura delle superfici a contatto. Sono stati testati sia accoppiamenti tra superfici simili (ad esempio, pignone e fianchi dell’ingranaggio rettificati dalla stessa rettificatrice), sia coppie aventi rugosità diverse (ad esempio, pignone rettificato accoppiato con un ingranaggio lucidato). I vari ingranaggi, finiti con vari processi, sono stati caratterizzati sperimentalmente tramite un profilometro Talysurf I-20 (profilo di rugosità 2D). Le misure sono state condotte in conformità alla normativa ISO 4288:1996 [8]. Le sei diverse misure coprono un intervallo compreso tra Ra=0,036 μm e Ra=0,450 μm. I profili sono riportati nella tabella 1.
Tabella 1 – Elenco dei parametri di rugosità dell’ingranaggio
Misure profilo | Ra | Rq | Rz |
0036 | 0.036 | 0.046 | 0.275 |
0122 | 0.122 | 0.151 | 0.510 |
0219 | 0.219 | 0.274 | 1.400 |
0258 | 0.258 | 0.321 | 1.643 |
0302 | 0.302 | 0.374 | 1.777 |
0450 | 0.450 | 0.579 | 3.4 |
La figura 2 mostra il confronto tra i differenti profili di rugosità (ingranditi). La scala è coerente tra tutte le misure. Le misure riportate fanno riferimento ad una lunghezza di 1,5 mm. Per i calcoli si sono invece utilizzate i valori relativi a tutta la lunghezza del profilo misurata. È importante notare come la parametrizzazione di McCool delle ampiezze di rugosità misurate presuppone che le ampiezze di rugosità siano di natura gaussiana, che i raggi di testa delle asperità siano tutti uguali e che la densità (dei picchi) sia costante.
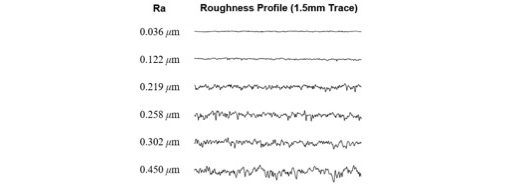
Queste ipotesi impediscono al modello di includere effetti locali (e.g. la presenza di graffi o pattern irregolari legati al processo di lavorazione) sulla perdita di potenza meccanica dell’ingranaggio. Le superfici utilizzate per la validazione del modello hanno tutte mostrato profili di rugosità ragionevolmente conformi ad una distribuzione gaussiana, con qualche eccezione per le asperità più marcate (outlier). La bontà dell’ipotesi sulla distribuzione è confermata dai grafici di probabilità normale. Se i dati risultano avere una distribuzione normale, seguiranno una linea retta. Le deviazioni da tale retta indicano un comportamento non normale (Gaussiano) del set di dati. I diagrammi di probabilità normale per le misure acquisite sono riportati in figura 3 per ciascuno dei sei profili di rugosità.
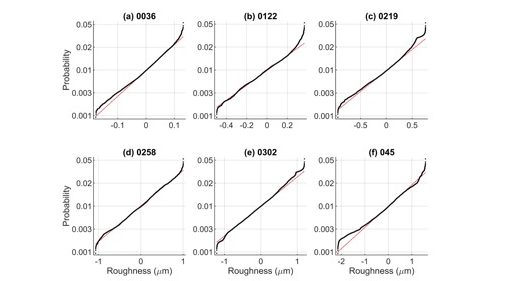
La maggior parte delle misure è risultata avere un comportamento ben approssimabile da una distribuzione gaussiana. Per tutti i profili misurati sono stati osservati diversi outlier che però sono risultati coerenti, per valore e quantità, con quelli presenti nei profili di rugosità utilizzati nella validazione del modello [1]. I profili di rugosità misurati non presentano dunque alcuna deviazione significativa dalla distribuzione normale ad indicare l’assenza di difetti superficiali o caratteristiche di asperità non ripetitive.
Sulla base delle sei superfici misurate è stata eseguita una serie completa di simulazioni utilizzando il modello di perdita di potenza meccanica precedentemente descritto: sono stati studiati 21 accoppiamenti di superfici, come indicato in tabella 2.
Tabella 2 – Accoppiamento tra superfici per le simulazioni
Misure profilo | 0036 | 0122 | 0219 | 0258 | 0302 | 0450 |
0036 | x | x | x | x | x | x |
0122 | x | x | x | x | x | |
0219 | x | x | x | x | ||
0258 | x | x | x | |||
0302 | x | x | ||||
0450 | x |
Le simulazioni sono state effettuate utilizzando le specifiche degli ingranaggi riportate in tabella 3.
Tabella 3 – Parametri degli ingranaggi utilizzati per le simulazioni della perdita di potenza
Parametri degli ingranaggi | |
Numero di denti | 17 – 26 |
Modulo | 4.23 |
Angolo di pressione | 22.5 |
Ampiezza di faccia | 14 – 20 |
Diametro di passo | 71.97 – 110.07 |
Diametro base | 66.49 – 101.69 |
Le condizioni operative simulate sono quelle tipiche delle applicazioni automobilistiche. I parametri di viscosità dell’olio rappresentano un tipico fluido per trasmissioni. Per ciascuno dei 21 accoppiamenti tra superfici si è utilizzato un design sperimentale a fattoriale completo (full-factorial) con tre livelli di coppia (50, 100 e 150 Nm) e sei livelli di velocità (500, 1000, 1500, 2000, 2500 e 3000 giri/min.), come indicato in tabella 4. In totale sono quindi state simulate 18 condizioni di esercizio per ogni combinazione di accoppiamento tra superfici. Nell’ambito di questo studio sono state dunque simulate 378 condizioni diverse. Il tempo di calcolo necessario per eseguire queste simulazioni è risultato inferiore a 1 minuto.
Tabella 4 – Condizioni simulate
Coppia (Nm) | Velocità rpm) | |||||
500 | 1000 | 1500 | 2000 | 2500 | 3000 | |
50 | x | x | x | x | x | x |
100 | x | x | x | x | x | x |
150 | x | x | x | x | x | x |
Effetto dell’accoppiamento tra rugosità superficiali
I risultati della modellazione relativi all’accoppiamento tra superfici aventi stessa rugosità (0036-0036, 0122-0122, 0219- 0219, 0258-0258, 0302-0302, 0450-0450) sono illustrati in figura 4. I valori delle perdite di potenza sono stati normalizzati in modo da mettere in evidenza l’esistenza di una correlazione e il relativo trend piuttosto che dare enfasi ai valori specifici che sono funzione del design (arbitrario) degli ingranaggi. La correlazione generale tra la perdita di potenza e le variabili (coppia e velocità di funzionamento) risulta essere la stessa in tutte le configurazioni. Il picco di perdita di potenza si verifica, per tutti gli accoppiamenti, nelle condizioni di velocità e coppia più elevate. Con l’aumento della rugosità, la perdita di potenza aumenta.
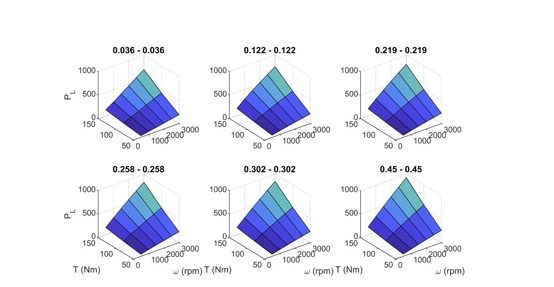
Analogamente, la figura 5 mostra la stima delle perdite di potenza meccanica per tutti gli accoppiamenti con il fianco levigato (0036-XXX). In questo modo è possibile valutare la correlazione tra perdita di potenza meccanica e combinazione di coppia e velocità nel caso di accoppiamenti simili (in termini di rugosità) e accoppiamenti di superfici dissimili. Anche in questo caso, la perdita di potenza mostra una tendenza simile al caso precedente al variare della coppia e della velocità.
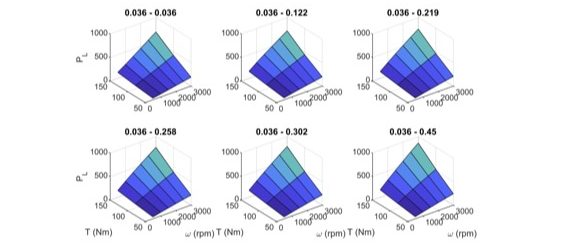
Una variabile di interesse che può essere stimata dal modello (oltre alla perdita di potenza meccanica stessa) è il rapporto di contatto area-asperità. Da questo coefficiente dipende il coefficiente di attrito effettivo tra attrito limite (?? = 0,1) e attrito EHL (approssimato come flusso di Couette). Tale coefficiente descrive il contributo relativo dei due fenomeni all’attrito effettivo.
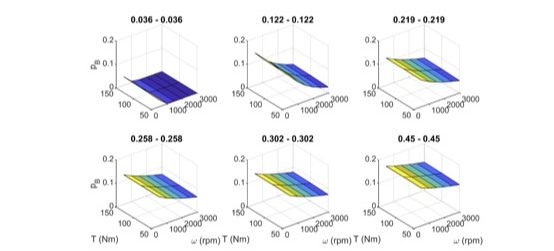
Le condizioni operative estreme in termini di spessore del film si verificheranno in presenza di coppia elevata e bassa velocità (basso spessore del film) e in condizioni di alta velocità e bassa coppia (elevato spessore del film). Ciò si rispecchia in differenti rapporti di contatto per entrambi i tipi di accoppiamento tra superfici (simili e dissimili) (figure 6 e 7).
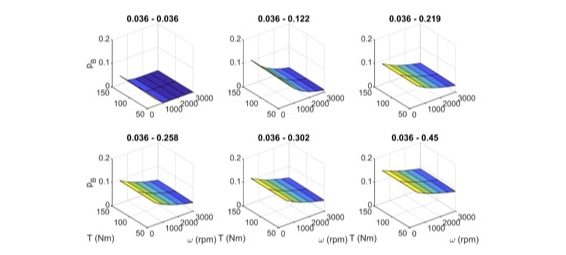
Per gli accoppiamenti tra superfici aventi rugosità molto differenti, come previsto, il rapporto di contatto risulta essere più basso rispetto a un accoppiamento tra superfici aventi entrambe elevata rugosità. Si nota inoltre come, nelle condizioni operative esplorate in questo studio, solo l’accoppiamento tra superfici lisce (0036-0036) non mostri alcun contatto tra asperità, sebbene ci sia da attendersi che anche l’accoppiamento 0036-0122 mostri, al crescere ulteriore della velocità, questa caratteristica. La rugosità composita è una metrica spesso utilizzata per valutare le condizioni del contatto EHL; in particolare spesso viene utilizzata per definire il parametro “spessore del film” ?.
La rugosità composita è definita come:
Ŕ?=√(??12+??22)
Le metriche di rugosità composita per i 21 accoppiamenti di superfici sono riportate in tabella 5.
Tabella 5 – Rugosità composita
Misure profilo | 0036 | 0122 | 0219 | 0258 | 0302 | 0450 |
0036 | 0.065 | 0.158 | 0.278 | 0.324 | 0.377 | 0.581 |
0122 | 0.214 | 0.313 | 0.355 | 0.403 | 0.598 | |
0219 | 0.387 | 0.422 | 0.464 | 0.641 | ||
0258 | 0.454 | 0.493 | 0.662 | |||
0302 | 0.529 | 0.689 | ||||
0450 | 0.819 |
Il parametro spessore del film ? è definito come:
?=ĥmin/???
In cui ĥmin è lo spessore minimo del film nel contatto.
La figura 8 mostra la perdita di potenza normalizzata in funzione della rugosità composita per ciascuna delle 378 condizioni simulate a (a) 50 Nm, (b) 100 Nm e (c) 150 Nm di coppia sul pignone (17T). In qualsiasi condizione operativa (coppia e velocità) – nell’ambito delle condizioni di lavoro qui utilizzate – esiste una relazione pressoché lineare tra la rugosità composita e la perdita di potenza meccanica. Dal punto di vista della progettazione, ciò significa che se le condizioni operative della trasmissione sono costanti, il progettista può approssimare la variazione della perdita meccanica in qualsiasi condizione operativa nota la perdita meccanica a due diversi valori di rugosità. Ciò consente di evitare costi inutili per test di efficienza. Tuttavia, la rugosità composita non fornisce alcuna informazione su come la perdita di potenza meccanica varierà al variare di coppia e velocità.
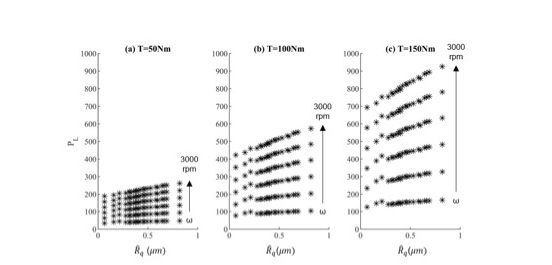
La perdita di potenza meccanica stimata con il modello è riportata, in funzione del parametro del film ?, in figura 9. La perdita di potenza meccanica mostra bande corrispondenti alle condizioni di coppia e velocità simulate. Per qualsiasi condizione di coppia e velocità, lo spessore medio minimo del film previsto da Dowson e Toyoda risulta essere uguale. Ciò significa che, in qualsiasi condizione operativa, ? risulta essere funzione della sola rugosità e aumenta al diminuire di quest’ultima.
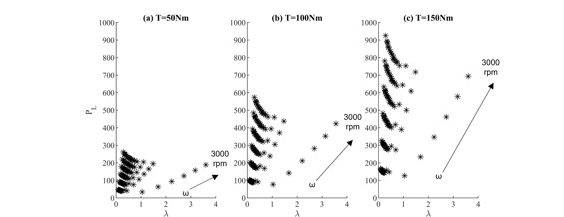
In qualsiasi condizione operativa in cui lo spessore del film è sufficientemente elevato da soddisfare la condizione ?>1, la perdita di potenza meccanica prevista mostra una diminuzione minima all’aumentare del parametro del film (?). Ciò indica che, dal punto di vista dell’efficienza, oltre quella soglia, un ulteriore miglioramento della finitura superficiale non comporterebbe grandi vantaggi.
Esiste tuttavia una dipendenza di ? dalla velocità, che si osserva chiaramente come linee parallele nel grafico. Velocità operative più elevate comportano valori più alti del parametro del film.
Anche il parametro del film presenta le stesse limitazioni della rugosità quando utilizzato come indice per la stima della perdita di potenza meccanica. Il parametro del film, infatti, non mostra alcuna correlazione con la perdita di potenza al variare della coppia e della velocità e risulta essere influenzato solo dalla rugosità (per una singola condizione operativa). Ciò nonostante il parametro del film tenga conto delle variazioni dello spessore effettivo del film dovute alle condizioni operative.
I rapporti di contatto per le condizioni operative e le ampiezze di rugosità considerate, erano ben lontani da dagli estremi (0: nessun contatto asperità; e 1; contatto puramente asperità), indicando come i denti dell’ingranaggio operassero in condizioni di lubrificazione mista. Dalla figura 8 si osserva come l’andamento lineare tra perdita di potenza e rugosità, si abbia solo nella condizione di lubrificazione mista.
Se la rugosità continuasse ad aumentare ben oltre Ŕ? = 1, il parametro del film si avvicinerebbe a zero (? → 0) e il rapporto di contatto si avvicinerebbe a 1 (?? → 1) ad indicare un contatto quasi puro tra le asperità.
In queste condizioni, il coefficiente di attrito effettivo dipende quasi esclusivamente dal coefficiente di attrito limite. Inoltre, aumentando ulteriormente l’ampiezza dei picchi di rugosità, il coefficiente di attrito non risulterebbe, secondo il presente approccio modellistico, influenzato. Ciò significa che, oltre un dato valore di rugosità, la tendenza all’aumento lineare della perdita di potenza all’aumentare della rugosità si interrompe e la perdita di potenza prevista rimane uguale anche a seguito di un’ulteriore crescita dalla rugosità.
Analogamente, al diminuire della rugosità, il parametro del film si avvicinerà all’infinito (? → ∞) e il rapporto di contatto dell’area limite andrà a zero (?? → 0) indicando come il coefficiente di attrito effettivo sia puramente dominato dal taglio (secondo le ipotesi di questo modello). Questo coefficiente di attrito sarà inoltre costante per ogni condizione operativa e ulteriori riduzioni della rugosità non comporteranno variazioni significative della perdita di potenza meccanica. Anche in questo caso, la tendenza lineare della perdita di potenza con la rugosità del composito si interrompe per valori di rugosità molto bassi e la perdita di potenza prevista risulterebbe costante al diminuire della rugosità. Ciò suggerisce come la perdita di potenza meccanica sia in relazione lineare con il rapporto di contatto limite. Ciò appare in modo evidente nei diagrammi di figura 10. Si nota come la maggior parte dei contatti operi in una condizione di lubrificazione mista. Questa condizione di assenza di contatto tra le asperità si ha per l’accoppiamento 0036-0036 a 1500 giri/min e oltre e per qualsiasi livello di coppia.
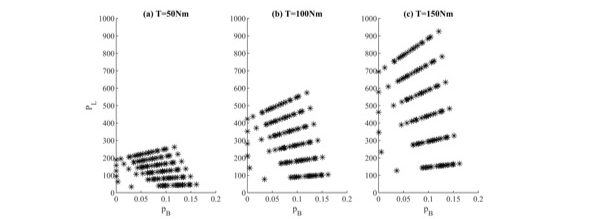
Sintesi e conclusioni
Il modello sviluppato da [1] per la previsione della perdita di potenza meccanica degli ingranaggi è stato utilizzato per analizzare 378 condizioni operative tipiche, costituite da 21 diverse combinazioni di rugosità superficiale per i due fianchi in presa. La coppia applicata variava da 50 a 150 Nm, mentre la velocità operativa da 500 a 3000 giri/min. I profili di rugosità superficiale variavano da Ra=0,036 μm (Rq=0,046 μm) a Ra=0,450 μm (Rq=0,579 μm). Le ampiezze dei profili di rugosità si sono dimostrate conformi a una distribuzione gaussiana, condizione necessaria per l’applicabilità del modello di perdita di potenza.
È stato dimostrato come la perdita di potenza aumenti quasi linearmente con la rugosità in qualsiasi condizione operativa di coppia e velocità. Tuttavia, la rugosità da sola non descrive la relazione tra la perdita di potenza e la combinazione di coppia e velocità. Ciò sposta l’attenzione sulla necessità di prove sperimentali per un’ampia gamma di coppie e velocità operative.
Per quanto riguarda il parametro del film, si osserva che oltre ? = 1, in qualsiasi condizione operativa, la perdita di potenza meccanica non mostri più riduzioni evidenti anche per aumenti significativi di ?.
Ciò significa che un ulteriore miglioramento della finitura delle superfici non porterebbe a un sostanziale aumento dell’efficienza. Tuttavia, la correlazione tra la perdita di potenza e le condizioni operative non può essere determinata dal parametro del film ed è necessaria ulteriore sperimentazione o modellazione.
Metriche semplici come la rugosità o il parametro del film possono essere utili per determinare la perdita di potenza meccanica relativa ad una condizione operativa fissa. Tuttavia, per comprendere l’effetto delle condizioni operative sono richiesti test dedicati o modelli avanzati. Il modello presentato funziona bene con profili di rugosità caratterizzati da una distribuzione normale, ma si raccomanda cautela quando si hanno trame superficiali dovute alla presenza di difetti o irregolarità della superficie. In circostanze normali, il modello è in grado di fornire risultati per migliaia di accoppiamenti di condizioni operative e profili di rugosità con un minimo onere computazionale, rendendolo utile per le una scelta ponderata del design già nella fase iniziale della progettazione.
(Isaac Hong, Emily Aneshansley, David Talbot, The Ohio State University)