L’obiettivo di questa ricerca è quello di sviluppare un Modello Predittivo di Controllo (MPC) per il processo di imbutitura della lamiera, ottimizzandolo dal punto di vista qualitativo. La metodologia completa di sviluppo viene illustrata dagli autori, risultando valida ed estendibile anche in un contesto di produzione industriale. I classici controlli di processo, grazie alle nuove tecnologie e alla rivoluzione di Industria 4.0, possono ora essere superati da nuove e più prestanti soluzioni.
L’industria manifatturiera odierna si trova a dover fronteggiare numerose sfide dovute al competitivo contesto moderno. La rivoluzione introdotta da Industria 4.0 propone diverse innovazioni tecnologiche ed organizzative in grado di migliorare ed ottimizzare la produzione. Tra i diversi paradigmi introdotti risulta particolarmente interessante quello di produzione zero-difetti (“zero-defect manufacturing” in inglese). In diversi contesti produttivi, tra cui anche il mondo della lamiera, l’impatto di scarti, difetti e rilavorazioni può essere notevole. Oggi le materie prime e l’energia sono più che mai preziose, perciò è fondamentale puntare ad un uso oculato delle risorse, così da limitare i costi per le aziende.
Tradizionalmente il controllo qualitativo viene effettuato a campione su lotti di prodotto finito, richiedendo quindi un investimento in termini di tempi e risorse. Per migliorare la qualità dei componenti prodotti sono oggi disponibili innovative strategie per integrare qualità e produzione. Combinando queste due funzioni aziendali è possibile creare sinergie positive in grado di offrire vantaggi sia ai produttori che ai clienti.
Qualità dei componenti
L’imbutitura è un processo di lavorazione della lamiera a freddo largamente diffuso in ambiente industriale. Per questa lavorazione sono richiesti, solitamente, una pressa, uno stampo e un premilamiera. Questo processo è tipicamente caratterizzato da elevate pressioni e velocità, così da produrre componenti in tempi particolarmente ridotti. In questo modo i tassi produttivi sono elevati e poca manodopera è richiesta, tuttavia risulta difficile controllare il processo in tempo reale.
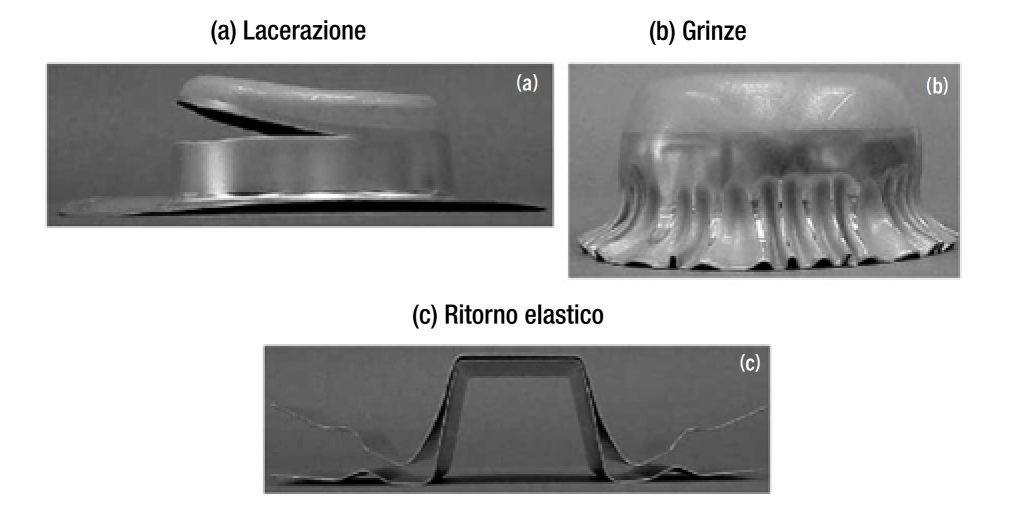
Per i componenti così stampati possono presentarsi alcuni problemi (Figura 1) ad esempio: lacerazioni, grinze o ritorni elastici. Durante le lavorazioni è però possibile identificare l’insorgere di difetti monitorando alcune variabili specifiche come, ad esempio, la forza del punzone, gli attriti e la forza del premilamiera.
Attualmente, nel processo tradizionale, i componenti vengono controllati al termine della lavorazione con l’elevato rischio di dover scartare numerosi pezzi nel caso siano presenti difetti. L’attuazione del paradigma di produzione zero-difetti è quindi ancora lontano dalla piena implementazione.
Controllo di processo
Il controllo di processo in tempo reale permette di compiere un grande passo verso l’obiettivo di riduzione dei difetti. Fortunatamente “Industria 4.0” introduce alcune tecniche di controllo automatiche classificabili in controllo del macchinario e controllo del processo. La prima soluzione concentra l’attenzione sul monitoraggio delle variabili della pressa (e.g. retroazione e controllo del premilamiera).
La seconda opzione monitora invece i parametri di processo e controlla il macchinario conseguentemente (e.g. misurando la corsa del punzone e controllando in retroazione la forza sul premilamiera). È anche possibile combinare il controllo del processo e del macchinario per riuscire ad ottenere una maggiore stabilità in caso di disturbi. L’obiettivo dei ricercatori italiani è quello di contribuire alla definizione e alla validazione di un modello per il processo di formatura, così da poter introdurre un controllo sul processo.
Per sviluppare un sistema efficace, è fondamentale tenere conto nel modello di incertezze e disturbi di processo che possono anche essere correlati allo specifico caso di studio. Si può infatti avere impatti derivanti, ad esempio, dalle proprietà del materiale, dalla forma del componente, dalla pressa utilizzata o da altre variabili. E’ infatti importante essere in grado di assicurare un processo fedele indipendentemente da incertezze e disturbi. Per conciliare queste due esigenze i ricercatori propongono una innovativa soluzione in grado di offrire interessanti prestazioni.
Sperimentazione
Per validare la soluzione elaborata, gli autori propongono un caso studio basato su un componente a “T” di carrozzeria automotive. Questo particolare (dettagli in Figura 2) è realizzato in acciaio HR 440Y580T-FB-UC dello spessore di 2 mm utilizzando una pressa servoidraulica. In questo macchinario la parte mobile è movimentata sia da un azionamento idraulico che da un azionamento elettrico.
Nella fase di imbutitura i due attuatori idraulici da 1500 kN lavorano insieme, inoltre è possibile agire anche sull’azionamento elettrico per piccoli aggiustamenti fino a 280 kN. In questo contesto la pressa è stata migliorata tramite l’aggiunta di un controllore di processo. Il macchinario è stato equipaggiato con tre sensori laser in tempo reale per misurare lo spostamento dei punti critici A, B e C sulla lamiera (mostrati in Figura 2).
Questi punti sono stati scelti a seguito di un’ottimizzazione multivariata basata sia su esperimenti che su simulazioni numeriche. Per quanto riguarda il controllo di processo e del macchinario è stata introdotta un’architettura basata su approccio “Software-in-the-loop” (Figura 3). L’algoritmo basato su un Modello di Controllo Predittivo (MPC o “Model Predictive Control”) è stato implementato su un controllore PLC virtuale Siemens presente su computer (PC1).
L’altra piattaforma digitale (PC2) è stata dedicata al gemello digitale della pressa utilizzata per l’imbutitura. La comunicazione tra i due PC è stata effettuata tenendo conto della rapida dinamica del processo di trasformazione (meno di 10 secondi per il processo completo), così da poter riuscire ad assicurare il controllo in tempo reale.
Risultati e performance
Il sistema così composto è stato testato per valutare l’efficacia del sistema in retroazione ad anello chiuso. L’errore di scostamento rispetto alla traiettoria di riferimento è stato misurato in tutte le prove e disturbi esterni sono stati simulati al fine di valutare la solidità di questo approccio.
Le performance sono particolarmente promettenti dato che gli errori risultano limitati. Inoltre, è importante constatare che, nonostante la complessità computazionale del modello, questo approccio può essere implementato praticamente per un controllo in tempo reale anche su processi così rapidi.
Gli autori hanno svolto anche un confronto tra l’approccio di controllo PID, tradizionalmente diffuso in letteratura, e la proposta innovativa. Il processo PID richiede maggiore sforzo di affinamento dei parametri, richiedendo quindi una lunga fase di “trial-and-error”. In contrasto, l’approccio MPC da questo punto di vista è sicuramente più semplice. La soluzione innovativa proposta dagli autori è inoltre in grado di offrire prestazioni superiori mantenendo il risultato sempre in tolleranza.
La soluzione di implementare un Modello Predittivo di Controllo (MPC) per l’imbutitura della lamiera risulta particolarmente interessante. L’obiettivo di ottimizzare il processo dal punto di vista qualitativo è raggiunto a pieno.
La metodologia completa di sviluppo viene illustrata dagli autori, risultando valida ed estendibile anche in un contesto di produzione industriale. I classici controlli di processo, grazie alle nuove tecnologie e alla rivoluzione di Industria 4.0, possono ora essere superati da nuove e più prestanti soluzioni. La potenza di calcolo disponibile è sempre superiore ed è quindi possibile sfruttare appieno nuove tecniche in tempo reale per offrire un superiore controllo qualitativo.
Gli autori si impegnano a proseguire questo filone della ricerca per approfondire lo sviluppo di un sistema di controllo in grado di offrire vantaggi tangibili anche, un domani, nella produzione industriale.
Fonte: Cavone, G., Bozza, A., Carli, R., & Dotoli, M. (2022). MPC-based process control of deep drawing: An industry 4.0 case study in Automotive. IEEE Transactions on Automation Science and Engineering, 19(3), 1586–1598. https://doi.org/10.1109/tase.2022.3177362