Analizziamo l’effetto dei trattamenti superficiali sulla resistenza a fatica di strutture sottili realizzate in additive manufacturing.
di Nicola Spignoli
L’obbiettivo di questo lavoro è stato quello di investigare l’influenza dei trattamenti post-processo sul comportamento a fatica di strutture a pareti sottili realizzate in manifattura additiva (AM). Allo scopo, la tecnologia di fusione laser selettiva (SLM) è stata impiegata per fabbricare campioni in AlSi10Mg con diversi spessori. Questi provini sono stati trattati poi in vario modo – tempra, micropallinatura e lavorazione meccanica a rugosità controllata – prima di essere sottoposti a prove di fatica meccanica. I risultati hanno mostrato come i trattamenti post-produzione siano in grado di migliorare la resistenza a fatica di oltre il 50% nel caso dei trattamenti meccanici e persino del 80% nel caso dei trattamenti termici. Le superfici di frattura sono state poi studiate attraverso microscopio elettronico, a scansione (SEM) e analisi metallografiche arrivando a concludere che, almeno nei casi analizzati, gli spessori in gioco non influiscono in modo significativo sulla durata a fatica dei componenti.
Stato dell’arte
L’interesse per la produzione di componenti fisici attraverso manifattura additiva (AM) del metallo sta crescendo esponenzialmente negli anni. Questa nuova tecnologia permette di ‘stampare’ in 3D sistemi funzionali con applicazioni che si sono dimostrate già valide in numerosi settori, quali automobilistico, aerospaziale e biomedico.
Tuttavia, per risultare davvero utile, la AM deve riuscire a garantire proprietà meccaniche paragonabili a quelle assicurate ai componenti dai processi di produzione tradizionali. Ciò non è sempre facile, proprio per le caratteristiche della tecnologia. Di conseguenza, sono piuttosto comuni gli studi rivolti a verificare la resistenza meccanica di componenti realizzati in AM, tanto rispetto a carichi statici che dinamici, inclusa la resistenza a fatica ad alto numero cicli.
Tra le diverse tecniche di AM disponibili, un posto particolarmente rilevante è riservato alla fusione laser selettiva (SLM). Uno dei suoi vantaggi principali risiede nella possibilità di ottenere forme molto complesse, create strato per strato da un fascio laser che è in grado di fondere selettivamente la polvere metallica. Ciò consente di produrre materiali piuttosto omogenei per quanto riguarda le caratteristiche chimico-fisiche, ma anche di farlo a fronte di forme molto complesse, inclusa la possibilità di creare strutture estremamente sottili. La realizzazione di strutture leggere e snelle è sempre ben vista, permettendo ai progettisti di rispondere in modo efficiente alle esigenze di garantire le corrette funzionalità a pesi e costi ridotti.
Numerosi studi, quindi, si sono già concentrati sulla verifica delle proprietà meccaniche di queste strutture sottili, investigando, ad esempio, la resistenza a snervamento, a rottura e fatica. Ciò è avvenuto soprattutto nel caso degli acciai. Si è concluso che, sebbene le proprietà meccaniche risultino spesso inferiori a quelle prodotte attraverso altre tecnologie più tradizionali, l’utilizzo di eventuali processi di post-trattamento potrebbero arrivare a ridurre tali differenze fino a renderle minime. Anche per tale motivo, sono già piuttosto diffuse (es., in ambito biomeccanico) soluzioni ultraleggere realizzate attraverso strutture reticolari sottili, in acciaio inossidabile o titanio. Queste strutture sono costruite in SLM per poi essere trattate allo scopo di migliorarne le caratteristiche meccaniche e funzionali.
Ma i benefici offerti dalla SLM non sembrano limitarsi ai soli materiali acciaio e titanio: anche nel caso dell’alluminio, infatti, con le sue ottime proprietà meccaniche e a fronte di un peso contenuto, sono molte le applicazioni che si stanno via via affermando nei più svariati settori.
In particolare, per quanto riguarda il AlSi10Mg, sono diversi gli studi che tentano di comprendere meglio questa lega. Ad esempio, alcuni pongono in relazione le proprietà del materiale con i vari parametri del processo SLM, quali densità energetica del fascio, la velocità di avanzamento e la risoluzione spaziale. Da essi emerge, in generale, come le proprietà dei materiali migliorino in modo marcato qualora il materiale sia sottoposto ad un trattamento termico. Per questo, nella produzione mediante SLM, è sempre previsto una fase di rilassamento (o rinvenimento) delle parti prodotte.
La scelta dei parametri di processo resta comunque fondamentale e questo anche rispetto ad aspetti quali rugosità e difettosità superficiale, che, tra l’altro, intervengono in modo non certo trascurabile sulla resistenza a fatica del materiale. Ne consegue che, trattamenti post-processo indirizzati a migliorare la qualità delle superfici, riducendone, ad esempio, la quantità di difetti presenti, sono essenziali per aumentare la resistenza allo stress ciclico. Tra questi, processi come micropallinatura e trattamenti termici possono rappresentare una opzione importante per diffondere l’utilizzo della AM nell’industria. In tal senso, nel caso della tempra, diventa altresì fondamentale comprendere l’effetto della profondità del trattamento. D’altra parte, da un lavoro pionieristico (di Peterson) è emerso come spessori e volumi trattati non sempre risultano così importanti sulla vita a fatica, dimostrando l’importanza di continuare ad approfondire l’argomento.
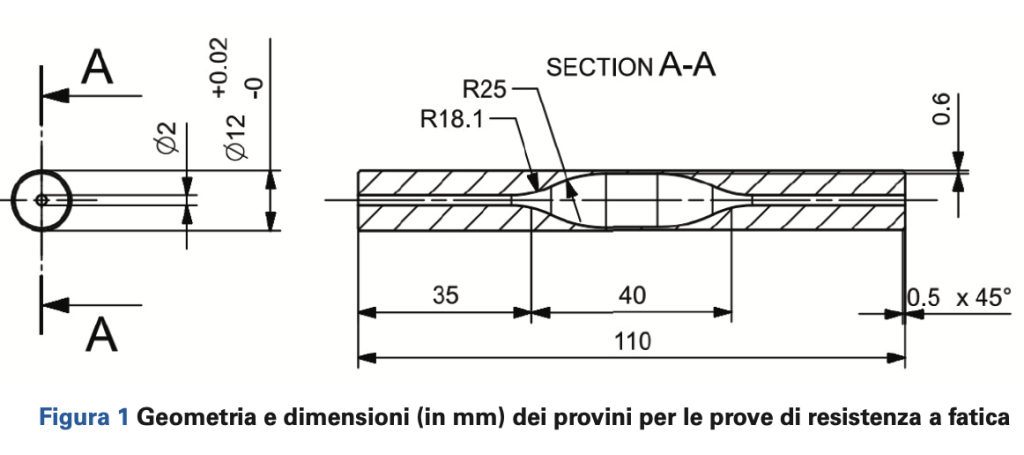
Materiali e metodi
Geometria dei campioni
Per analizzare l’influenza dello spessore della parete sulla vita a fatica dei componenti sono stati ideati provini delle forme e dimensioni specifiche, mostrate in Figura 1. Siamo in presenza di provini molto diversi da quelli che utilizzati di solito per questo genere di prove, ossia i cosiddetti provini “ad osso di cane”, a geometria solida. Questi campioni sono invece cilindrici, lunghi e stretti (12 mm di diametro), con una marcata cavità interna, realizzata proprio allo scopo di investigare gli effetti della concentrazione delle tensioni su strutture molto sottili. Questa cavità va, infatti, a modificare la sezione resistente allo scopo di rendere evidente come la resistenza a fatica varia al variare dello spessore di parete. Le dimensioni complessive del provino sono state definite in base alla geometria della macchina di prova mentre, per gli spessori di parete, sono state considerate tre distinte serie: 2,4 mm (Serie 3), 1,2 mm (Serie 2) e 0,6 mm (Serie 1), con quest’ultimo valore leggermente al di sopra dello spessore minimo realizzabile con tecnologia SLM. Nello specifico, la figura 1 mostra il campione con uno spessore di parete nella parte centrale di 0,6 mm. Le estremità sono state filettate per evitare possibili concentrazioni di sollecitazioni tra la zona indagata e le sezioni di presa caratterizzate dal foro di piccolo diametro necessario per il rilascio della polvere utilizzata per la stampa. Queste caratteristiche sono state poi verificate tramite analisi FEM.
Fatica e propagazione della frattura
Nello studio dei fenomeni di fatica, il meccanismo di rottura più frequente consiste nella nucleazione di una cricca, molto spesso sulla superficie esterna oppure in corrispondenza di un difetto interno, che, una volta propagatosi, porta alla rottura. Grazie alla deposizione strato per strato e alla fusione selettiva della polvere, la SLM consente di fabbricare componenti interni cavi senza successive lavorazioni di taglio. La SLM riduce il rischio della presenza di difetti sulla superficie interna, che non potrebbero essere eliminati dai trattamenti superficiali, andando così a pregiudicare la durata a fatica. Inoltre, i ridotti spessori di parete e, di conseguenza, la minore quantità di materiale utilizzati, riduce il minor numero assoluto di difetti presenti nel campione nel suo insieme, con conseguente influenza sulla sua resistenza.
Produzione additiva
Per la loro produzione è stata utilizzata una stampante SLM, la EOSM280 (EOS GmbH Electro Optical Systems, Krailling, Germania), impostando il laser ad una potenza di 320 W e densità di energia di 41 J/mm3.
Una specifica attenzione è stata rivolta nella scelta della direzione di stampa. È ben noto, infatti, come i componenti prodotti in SLM mostrino una marcata anisotropia nelle proprietà dei materiali: le resistenze inferiori sono quelle relative alla direzione di accrescimento (lungo Z). I campioni, quindi, sono stati stampati verticalmente, con l’asse di costruzione lungo Z, permettendo così di investigare la situazione meno favorevole.
Trattamenti di finitura
Dopo la fabbricazione SLM, che ha incluso anche il rilassamento/rinvenimento (Trattamento A), alcuni campioni sono stati sottoposti a trattamenti di finitura quali micropallinatura (Trattamento B), finitura meccanica (Trattamento C) e tempra T6 (Trattamento D).
In generale, si può dire che sia la micropallinatura che la finitura meccanica di controllo della rugosità (con processi come la levigatura) rappresentano soluzioni molto utilizzate per migliorare l’aspetto e la superficie dei materiali. Entrambi, nel nostro caso, possono rivelarsi utili, riuscendo a rimuovere piccole imperfezioni e a rendere la superficie più liscia, con la micropallinatura che è in grado di offrire una finitura più uniforme.
La tempra, d’altra parte, come sicuramente noto, è un trattamento termico (non meccanico) che agisce sulle proprietà del materiale a livello strutturale e microstrutturale, migliorandone le caratteristiche meccaniche. La tempra T6 (T6 temper o aging), in particolare, è un trattamento termico specifico, utilizzato di frequente in presenza di leghe di alluminio per migliorarne le proprietà meccaniche e renderle più resistenti e durevoli. Si compone di due fasi principali:
- Fase di riscaldo (soluzione), durante la quale il materiale è riscaldato a una temperatura elevata, generalmente intorno a 500-540°C nel caso delle leghe di alluminio. Questo riscaldamento permette agli elementi di lega di diffondersi uniformemente nella struttura del materiale.
- Fase di invecchiamento (aging): durante la quale il materiale è raffreddato rapidamente, seguito da un secondo riscaldamento a una temperatura inferiore, tipicamente tra 160-180°. Questa fase di invecchiamento favorisce la precipitazione controllata di particelle di lega, che migliorano le proprietà meccaniche della lega, come resistenza, durezza e resistenza alla corrosione.
La tempra T6 può notevolmente aumentare la resistenza meccanica e la durezza delle leghe di alluminio, consentendo loro di essere utilizzate in una vasta gamma di applicazioni industriali, come parti aeronautiche, componenti automobilistici, strutture e altro ancora. La tempra T6, inoltre, è spesso scelta per ottenere un equilibrio ottimale tra resistenza e duttilità nelle leghe di alluminio.
Nello specifico dello studio, la micropallinatura è stata eseguita utilizzando sfere di vetro da 0,2 mm di diametro con una pressione di 4 bar, mentre il processo finitura con rugosità controllata è consistito nel levigare la superficie esterna dei cilindri fino ad arrivare a garantire lo stesso livello la rugosità ottenuto per micropallinatura, pari a circa 6 µm. Per la tempra T6, infine, è stato eseguito un procedimento standard, che ha considerato i seguenti parametri:
1. Solubilizzazione a 520 C;
2. Tempra in acqua;
3. Invecchiamento artificiale a 160 C per 6 h.
Sistema di prova
Le misurazioni sperimentali sono state condotte su una piegatrice rotativa Italsigma 2 TM 831 (ITALSIGMA, Forlì, Italia), con uno stress ratio di R = -1 e una frequenza di 60 Hz. In termini di sistemi di carico, mentre una estremità del campione è stata bloccata attraverso vincolo fisso, nell’altra è stata applicato un momento flettente.
La resistenza a fatica è stata valutata utilizzando il metodo ‘staircase’, secondo la ISO 12017. I provini sono stati sollecitati ciclicamente rispetto a certi valori di carico, ripetute fino alla rottura oppure fino a quando non venisse raggiunto un determinato valore massimo (di run-out), fissato a 2×106 cicli. Detti valori sono stati progressivamente aumentati durante la prova, considerando un incremento di 5 MPa tra due cicli consecutivi. Il limite inferiore della resistenza a fatica è stato calcolato per una probabilità di guasto del 10% e per un livello di confidenza del 90%. Questo standard è stato applicato a 15 campioni nel caso dei provini non trattamenti e a 6–8 campioni per i restanti casi. Il piano di prova è schematizzato in Tabella 1.
Una bilancia è stata utilizzata per determinare la densità dei campioni. Ciò è avvenuto sfruttando il Principio di Archimede e misurando la massa del campione in aria e acqua, fino ad arrivare al valore cercato. Per ciascuna situazione, si è valutata la densità del materiale come risultato dai valori medi misurati. Questi valori sono stati confrontati con quelli ricavati a partire dalla scheda tecnica delle polveri fornite dal produttore, considerate rispetto ai relativi contenuti percentuali.
Microscopia ottica e SEM
Le analisi preliminari della superficie di frattura sono state eseguite utilizzando uno Stereomicroscopio Zeiss Stemi 305 (Zeiss, Oberkochen, Germania) dotato di Axiocam 105 telecamere a colori (Zeiss, Oberkochen, Germania) con zoom disponibili fino a 4x. Le osservazioni sono state migliorate utilizzando un microscopio elettronico a scansione (SEM) (Zeiss, Oberkochen, Germania), che ha consentito uno studio dettagliato della superficie di frattura, la sua microstruttura e le sue peculiarità.
Le immagini sono state quindi acquisite con una Nikon Optiphot-100 (Nikon Corporation, Tokyo, Giappone) microscopio metallografico con zoom 5×, 10×, 20× e 50×, dotato di telecamera Moticam 3 da 3Mpx (MoticEurope, Barcellona, Spagna). Lo stesso strumento è stato utilizzato per acquisire le immagini necessarie per il calcolo della percentuale di porosità, che è stato eseguito con il software ImageJ (1.53k, NIH, Bethesda, MD, USA). Per evidenziarne meglio le caratteristiche superficiali, i campioni sono stati lucidati, trattati con il reagente di Keller (Antec Inc., Louisville, KY, USA) per circa 35s, e poi immersi in acqua calda per alcuni secondi.
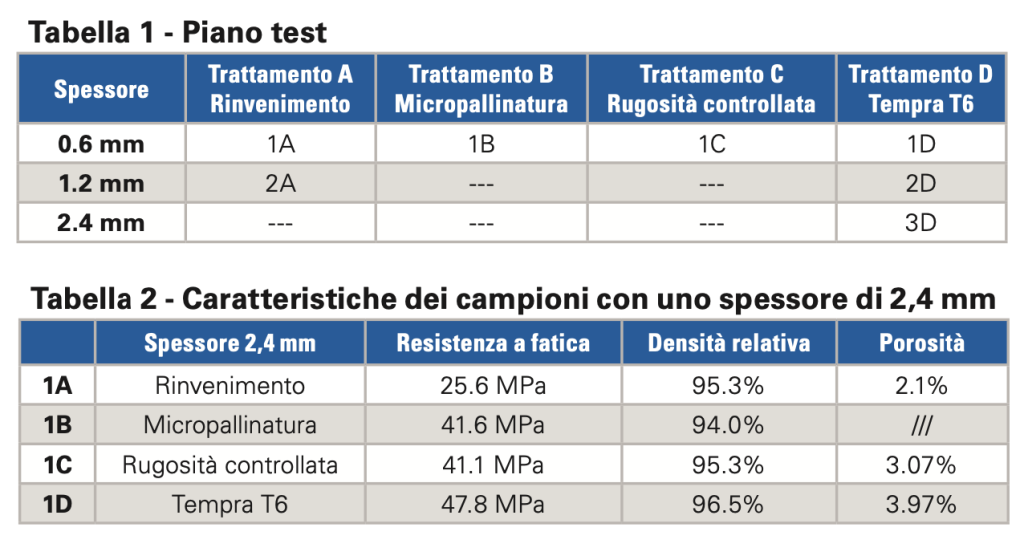
Risultati
Lo studio, in generale, è stato rivolto ad ottenere evidenze sperimentali rispetto alla resistenza a fatica (fino a 2×106 cicli), densità e porosità del materiale prodotto in SLM a fronte di diversi spessori. I risultati numerici ottenuti sono stati molti e qui di seguito saranno presentati solo i principali.
Per quanto riguarda la porosità, i dati sono stati ottenuti elaborando le fotografie prese al microscopio metallografico, mediando poi i risultati corrispondenti alla sezione trasversale del provino e alla sezione longitudinale. Per campioni con uno spessore di parete equivalente a 2,4 mm, con sezione resistente maggiore, i risultati sono riportati in Tabella 2. I risultati mostrano la presenza di numerose microporosità nel materiale che ne influenzano la densità e la porosità complessiva. Per i provini con spessore 1,2 mm, i dati sono invece mostrati in Tabella 3. Infine, in Tabella 4 sono disponibili i dati relativi ai campioni con parete da 0,6 mm. Come si può notare, non è stato possibile determinare la resistenza a fatica per i provini 3A in quanto presentavano cedimenti prematuri per l’effetto combinato di torsione, flessione e difettosità.
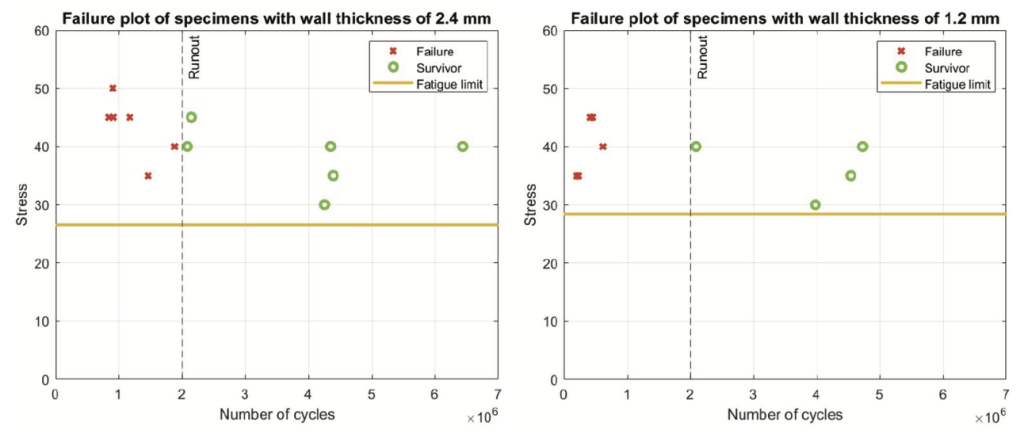
Discussione
Resistenza a fatica
I valori misurati mostrano come i provini in SLM presentino una resistenza a fatica inferiore rispetto alle leghe di alluminio fuso, ma che aumenta nel caso con l’esecuzione dei trattamenti.
In particolare, si può immediatamente riconoscere come il migliore trattamento, in termini di aumento della resistenza a fatica, sia la tempra T6 (Trattamento D), con incrementi superiori al 80%.
La massima dispersione dei valori numerici è stata registrata nel caso dei provini caratterizzati dal solo trattamento di rinvenimento (Trattamento A), privi cioè di qualsivoglia post-trattamento. La Figura 2 mostra proprio ciò, nel caso dei provini di spessore 2,4 mm e 1,2 mm, dimostrando come i trattamenti superficiali, non solo migliorano le caratteristiche dei materiali ma le rendono più uniformi. Tra l’altro, tale variabilità diventa minima (rappresentando, quindi, la migliore condizione riscontrata) proprio in presenza di un trattamento di tempra T6 (Trattamento D).
Anche gli altri trattamenti appaiono migliorativi della proprietà di resistenza a fatica del materiale aumentando del +57% e +55% nel caso di, rispettivamente, micropallinatura (Trattamento B) e lavorazione a rugosità controllata (Trattamento C).
Spessore e qualità delle superfici
L’estensione della vita a fatica è legata ad un miglioramento nella qualità delle superfici, come può essere osservato attraverso l’analisi SEM. In particolare, questa differenza risulta evidente osservando, in Figura 3 e Figura 4, la superficie dopo micropallinatura. Si evidenzia una diminuzione della rugosità che ha comportato un aumento della vita a fatica dovuto alla minore presenza di difetti sulla superficie del provino.
Questa nostra indagine ha anche dimostrato che non ci sono differenze significative nella vita a fatica considerando i diversi spessori. Infatti, a parità di trattamento effettuato, gli spessori di 2,4 mm e 1,2 mm, sebbene siano uno il doppio dell’altro, presentavano valori di resistenza a fatica molto simili. Entrando più nello specifico, si può osservare che, nel caso del Trattamento A (as-built), il rapporto tra la differenza dei valori di resistenza a fatica dei due spessori e la loro media è intorno al 7%, mentre nel caso del trattamento termico (T6) era intorno all’8%. In entrambi i casi i valori di resistenza a fatica sono leggermente superiori per lo spessore maggiore. L’effetto degli spessori sulla resistenza a fatica, quindi, può essere trascurata in termini pratici.
Il caso dei campioni di spessore 0,6 mm non è stato preso in considerazione per questa analisi a causa delle loro caratteristiche specifiche in relazione alle dimensioni dei difetti. Poiché nei provini più sottili era presente meno materiale, i difetti che avrebbero potuto portare alla successiva rottura del provino dovrebbero essere staticamente inferiori. A causa dell’elevata porosità del materiale, tuttavia, è stato possibile osservare che, per quanto numericamente inferiori, i difetti erano di notevoli dimensioni, con la conseguenza di non permettere di ottenere risultati affidabili. Ciò si può chiaramente osservare nel SEM di Figura 5, dove i difetti si estendevano lungo l’intera parete del provino, portando ad un drastico abbassamento del valore di resistenza a fatica. Una caratteristica solo in parte simile appare nelle osservazioni SEM dei campioni spessi 1,2 mm, rappresentati in Figura 6.
Caratteristiche delle fratture
L’aspetto generale della superficie della frattura prevede un’area liscia intorno al sito di propagazione iniziale, ad esempio nelle figure 7 e 8, dove è stata anche notata la presenza di difetti e trigger di frattura di dimensioni molto significative. Questi sono presenti principalmente sulla superficie esterna del provino, come nella Figura 7. Nella Figura 8, è possibile identificare più siti di origine della cricca da fatica a causa di una maggiore resistenza del materiale.
La parte finale di propagazione della sezione è simile nel caso del trattamento di rinvenimento (as-built), pallinato e rugosità controllata, e si presenta fragile, come, ad esempio, nelle Figure 9 e 10. Al contrario, la rottura affiora nei provini trattati con tempra T6 mostrano evidenti deformazioni plastiche, come si può vedere nelle Figure 11 e 12.
Dopo le prove di rottura a fatica, sono state eseguite le analisi per rilevare l’effettiva densità dei provini. Dai valori riscontrati e riportati nelle Tabelle 2-4 si può osservare che anche questi sono stati influenzati dal trattamento effettuato.
Manifattura additiva e difetti
Come previsto dai precedenti calcoli di porosità, i difetti nei provini si sono rivelati vari e di dimensioni significative. La presenza di valori di elevata porosità è probabilmente dovuta all’uso di bassa densità di energia. Confrontando i valori utilizzati in simili studi rispetto alla stessa energia, è stato possibile verificare che le cavità presenti sono risultate della stessa dimensione, confermando la validità di questa analisi. In particolare, le cavità nel campione erano, in molti casi, dovute a mancanza di polvere o fusione impropria della polvere. Questo fenomeno è stato successivamente osservato attraverso indagini al microscopio metallografico. Come si può vedere in Figura 13, che rappresenta l’intera sezione di un provino di spessore 1,2 mm, i pori maggiori di 100 µm sono circondati in molti casi da scie di micropori dovute proprio all’insufficiente energia di fusione delle polveri.
In Figura 14 è mostrata la sezione longitudinale dello stesso provino. È possibile vedere che la distribuzione della porosità è piuttosto disomogenea. Di conseguenza, la densità del provino è debolmente correlata alla sua resistenza a fatica, che dipende maggiormente dalla porosità misurata localmente. Inoltre, la polvere non fusa intrappolata nel materiale contribuisce alla densità ma viene rimossa nelle operazioni di lucidatura necessarie per eseguire l’analisi metallografica.
Un’analisi più approfondita dei pori sopra descritti è stata successivamente effettuata mediante immagini ottenute dal microscopio metallografico. Mediante l’attacco acido del campione con il reagente di Keller, sono stati registrati i difetti nei bordi dei melt pool tipici del processo di manifattura additiva, come nelle Figure 15 e 16. Infatti, osservando le forme comuni del processo additivo, diventa evidente una differenza di grani tra l’interno del bagno di fusione e il bordo. A causa di una diversa velocità di solidificazione, si ottiene una grana più grossolana nella parte più esterna rispetto a quella interna. Questa differenza nel processo di solidificazione è una delle cause della comparsa dei pori, insieme alla presenza di polvere non fusa. Mentre l’effetto dei pori mostrato in Figura 15 è minimo per quanto riguarda la vita a fatica, le cavità simili a quella mostrata in Figura 16, raffigurante una sezione trasversale, possono agire come una cricca intergranulare preesistente, che è molto dannosa.
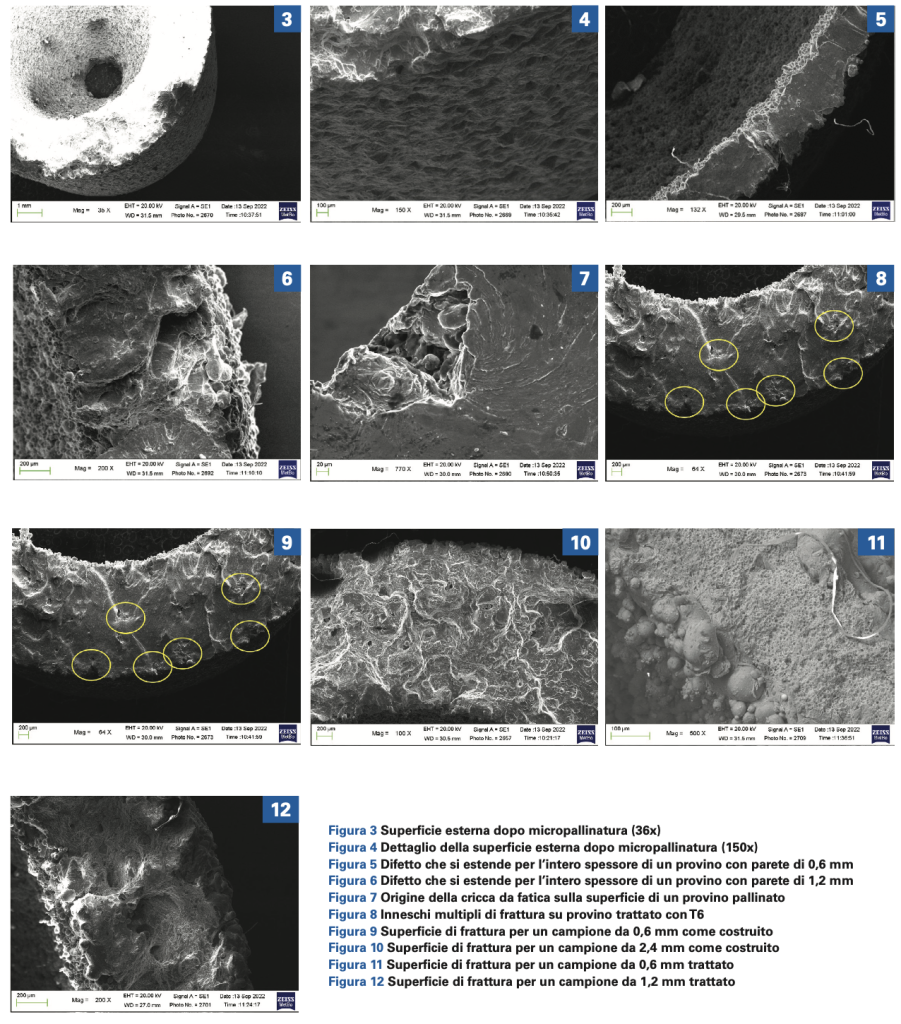
Conclusioni
In questo studio, è stato studiato il comportamento a fatica di una lega di alluminio da manifattura additiva (la AlSi10Mg). Allo scopo sono stati utilizzati campioni, di geometria non convenzionale, con spessori sottili e variabili, creati attraverso fusione laser selettiva (SLM). I risultati hanno mostrano che la resistenza a fatica è sostanzialmente indipendente dallo spessore del materiale. Questo risultato, controintuitivo, può essere associato alla presenza di porosità di dimensioni rilevanti. Certamente la quantità di difetti può essere ridotta intervenendo sui parametri di stampa, ma resta difficile alterare in modo marcato i processi di fusione e solidificazione della polvere metallica all’interno dei campioni. Allo stesso tempo, un miglioramento significativo nel comportamento a fatica del materiale è stato ottenuto grazie all’aggiunta di trattamenti di post-produzione. Tra i diversi processi considerati (inclusi micropallinatura, rettifica), la tempra è quella che appare offrire i migliori risultati. Nel futuro sarà di particolare interesse investigare l’effetto sul comportamento a fatica di alcuni parametri di produzione, quali la potenza e l’orientamento del fascio laser, specialmente in presenza di strutture caratterizzate da piccolissimi spessori.
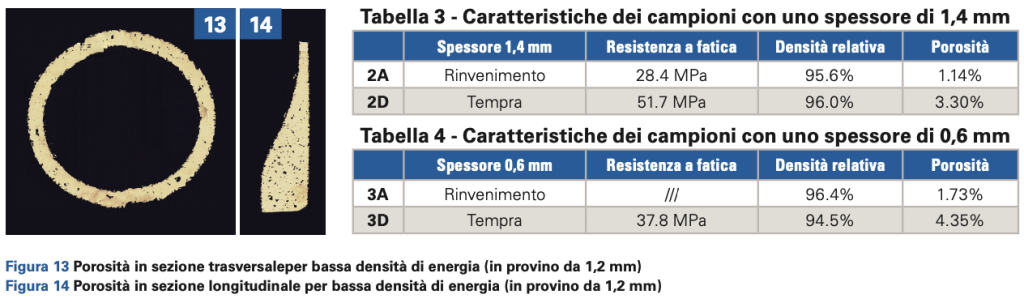
Approfondimenti
- Spignoli N, Minak G. “Influence on Fatigue Strength of Post-Process Treatments on Thin-Walled AlSi10Mg Structures Made by Additive Manufacturing”. Metals 2023, 13, 126. https://doi.org/10.3390/met13010126