L’aerodinamica del veicolo permette di diminuire i consumi delle autovetture aumentandone l’efficienza, per questo gli sforzi progettuali si sono sempre concentrati sullo studio di forme e profili. Più raramente l’attenzione è stata posta, invece, sull’impatto della qualità delle superfici, magari non perfettamente rifinite, sull’efficienza delle autovetture.
di Cristiano Fragassa, Esteban Betancur, Massimo Mele
Diminuire i consumi nelle autovetture, aumentandone l’efficienza, rappresenta un elemento centrale per rendere la mobilità più pulita e sostenibile. In tal senso, al fianco di un utilizzo consapevole del veicolo da parte dell’utente (es., stile di guida calmo e attento, pneumatici ben gonfiati, manutenzione regolare per filtri e candele), sono diversi gli interventi tecnici che restano a carico della casa automobilistica (motori efficienti, pesi ridotti). Tra questi l’aerodinamica assume un ruolo fondamentale: si stima, ad esempio, che ad una velocità di 120 km/h, circa il 70% del consumo complessivo del veicolo sia legato all’attrito con l’aria. La parte restante è al contrario legata a fattori molteplici, molto meno controllabili, come la resistenza al rotolamento degli pneumatici, la dinamica del veicolo o le sempre più numerose soluzioni tecniche necessarie a garantire affidabilità e sicurezza.
Data questa sua importanza, sono notevoli da sempre gli sforzi rivolti a migliorare l’aerodinamica di veicolo. Ciò ha significato, soprattutto, la messa a punto di forme e profili che consentissero di minimizzare la resistenza dell’aria rispetto a ciascuna circostanza di marcia. Più raramente l’attenzione è stata posta, invece, sull’impatto della qualità delle superfici, magari non perfettamente rifinite, sull’efficienza delle autovetture.
Qualità superficiale e aerodinamica
In generale, la qualità delle superfici può influenzare in modo non marginale l’aerodinamica del veicolo con fenomeni quali:
- Rugosità superficiale: Una superficie ruvida causerà una separazione del flusso d’aria più precoce, creando una maggiore resistenza aerodinamica e turbolenza.
- Turbolenza: La presenza di irregolarità o asperità sulla superficie può generare turbolenza nel flusso d’aria, causando aumento della resistenza e perdita di efficienza aerodinamica.
- Separazione del flusso: Una superficie non liscia può favorire la separazione del flusso d’aria dalla superficie stessa, creando zone di bassa pressione e aumentando la resistenza aerodinamica.
- Vortici: Superfici aspre o non uniformi possono generare vortici di scia più grandi e persistenti, aumentando la resistenza aerodinamica e la perdita di energia cinetica.
- Disturbi locali: Irregolarità superficiali possono causare disturbi locali nel flusso d’aria, creando zone di alta pressione o depressione che influenzano negativamente il comportamento aerodinamico.
- Effetto di trascinamento: Una superficie aspra aumenta l’attrito tra l’aria e la superficie, generando un aumento dell’effetto di trascinamento che richiede più energia per superare la resistenza aerodinamica.
- Interferenza del flusso: Superfici non uniformi o con sporgenze possono interferire con il flusso d’aria attorno ad altre parti del veicolo, causando ulteriori turbolenze e aumentando la resistenza.
- Effetto di pressione: La qualità delle superfici può influenzare la distribuzione della pressione lungo la superficie del veicolo, che a sua volta può influire sulla portanza, sulla stabilità e sull’efficienza globale dell’aerodinamica.
Non sempre è possibile, quindi, trascurare questi fenomeni. E, per minimizzarne gli effetti negativi, è essenziale che le superfici siano lisce e uniformi, con tolleranze dimensionali e rugosità controllate.
Obbiettivi e metodi
In questo articolo si è pensato di studiare come il processo di produzione di una carrozzeria in fibra di carbonio potesse influenzare l’aerodinamica ed i consumi. Allo scopo si è scelto un caso particolarissimo di veicolo, una monoposto solare da competizione progettata e costruita in Italia. Di questo prototipo sono state scansionate le geometrie, poste poi a confronto con quelle previste a progetto. Sono state riscontrate deviazioni geometriche importanti e fenomeni superficiali inattesi che hanno portato a quantificare le perdite di efficienza legate al peggioramento dell’aerodinamica. Proprio qui i trattamenti di finitura potrebbero rivelarsi utili, molto più di quanto finora immaginato.
I veicoli solari, per quanto al momento non siano molto più di prototipi dimostrativi, possono rivelarsi essenziali quando si tratta di immaginare una mobilità pulita e sostenibile. Questi veicoli, infatti, sono i soli in grado di assicurare un trasporto ad emissioni zero, dove l’energia utilizzata è ottenuta per intero dai pannelli solari presenti. Ma non è solo questo a renderli tecnicamente interessanti.
Data la ridotta energia acquisibile, le auto solari rappresentano una occasione unica per sviluppare e mettere in prova soluzioni di efficientamento energetico all’avanguardia. Ed i risultati raggiunti sono degni di nota: la potenza necessaria ad un prototipo di auto solare per viaggiare a 100 km/h è pari a circa 1.5 kW, ossia quasi 10 volte inferiore a quella richiesta da un veicolo convenzionale. Tale risultato è permesso, in primo luogo, da un design estremamente aerodinamico, che rende questi strani veicoli un ottimo banco di prova per studiare miglioramenti anche minimi nella efficienza energetica.
Design aerodinamico e processi produttivi
La forza di resistenza aerodinamica (Fd) che l’aria esercita su un veicolo in movimento può essere stimata attraverso la nota relazione.
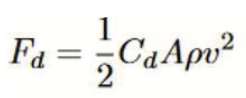
in funzione di densità dell’aria (r), velocità del veicolo (v), coefficiente di resistenza (Cd) e area frontale (A). È il prodotto di questi ultimi due fattori (Cd·A), entrambi legati alla forma dell’auto, a rivelarsi un primo parametro fondamentale nella ottimizzazione aerodinamica.
In una auto quale ad esempio la Tesla Model S, il valore di CdA è vicino a 0.58 m2. Ciò significa che ad una velocità costante di 100 km/h, la forza di resistenza è di 265 N e sono necessari circa 7.4 kW di potenza per superare questa resistenza aerodinamica. Per le auto solari, per riuscire ad essere autonome dal punto di vista energetico, il CdA deve essere inferiore alla metà.
L’efficienza aerodinamica può essere raggiuta attraverso una riduzione dell’area frontale (A), ma ciò ha senso nel presupposto di riuscire ad ottenere superfici di alta qualità (classe A). Ossia, una volta ottenuta a progetto l’aerodinamica desiderata, il processo di fabbricazione dovrebbe riuscire a garantire che questo profilo non venga modificato.
Tuttavia, le fresatrici a controllo numerico (CNC) comunemente utilizzate per la fabbricazione di modelli e stampi, da cui saranno poi prodotte le parti di carrozzeria, non possono fare a meno di introdurre una ‘certa imprecisione’ (in termini, ad es., di tolleranze e rugosità). Anche la successiva produzione delle parti, qui prodotte in fibra di carbonio, utilizza processi non perfetti. Tali fasi introducono modifiche non marginali nelle forme previste e, di conseguenza, nella aerodinamica di veicolo.
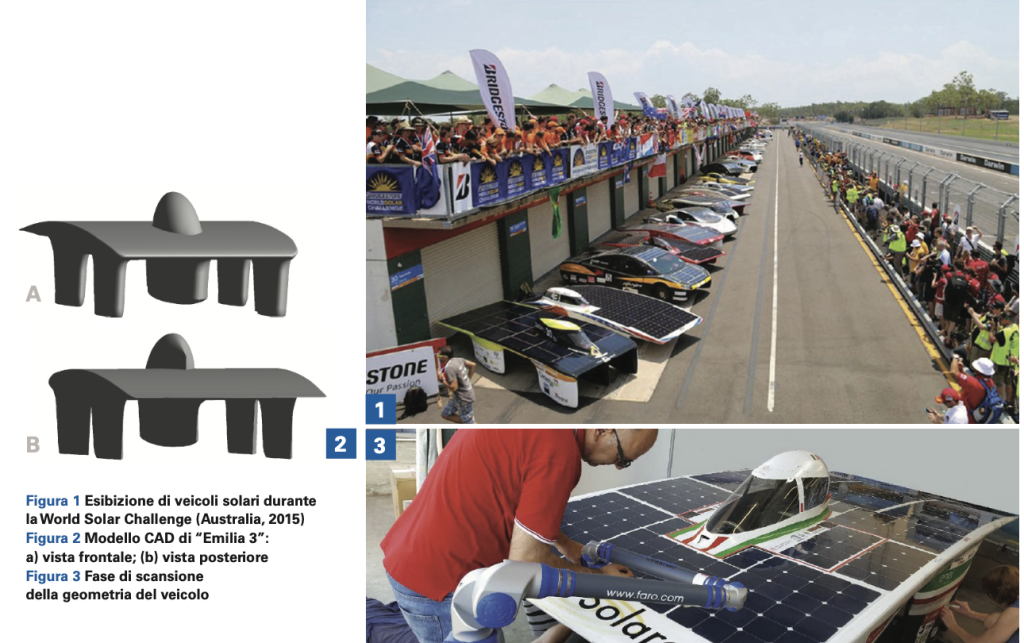
Prototipo sperimentale
Il veicolo solare utilizzato come base per questo studio è noto come “Emilia 3”: progettato e costruito dal team italiano Onda Solare ASD, è stato pensato per competere nel World Solar Challenge (WSC), la gara di auto solari più celebre e complessa (vedi Fig. 1). Si tratta di percorrere 3022 Km, ossia l’intera Australia dalla costa Nord a quella Sud, utilizzando la sola energia solare raccolta dal veicolo per la sua via. Ciò avviene grazie alla presenza di 6 m2 di pannelli di silicio monocristallino e 21 kg di batterie al litio, ma soprattutto tanta ingegneria, dove tutto va pensato per massimizzare l’efficienza.
Nello specifico, il veicolo è stato ideato come una monoscocca di fibra di carbonio, di forma tale da combinare le esigenze aerodinamiche (minima forza di resistenza), funzionali (esposizione ottimale per i pannelli) e strutturali (es. resistenza e sicurezza). Per l’aerodinamica è stato importante non solo minimizzare i coefficienti di forma, ma anche garantire una portanza leggermente negativa (down-force), in grado di stabilizzare un veicolo nella sua corsa molto vicino al suolo (vedi Box 1). La Figura 2 mostra la silhouette finale.
A livello di processo, la carrozzeria è stata realizzata unendo 10 segmenti principali, ognuno creato a partire da un modello per poi passare allo stampo e al particolare finale. I modelli di maggiori dimensioni sono stati realizzati combinando lamiere di alluminio, prima tagliate, piegate e assemblate quali struttura ad arco, poi intonacate e rifinite per migliorare la finitura superficiale. I modelli più piccoli sono stati realizzati in alluminio, vetroresina, resina poliuretanica o persino legno, sagomando in CNC dal pieno.
A partire dai modelli, sono stati poi prodotti i relativi stampi: tutti in fibra di carbonio, ottenuti attraverso un processo di laminazione manuale e cura in autoclave. Durante la laminazione sono state introdotte anime preimpregnate in fibra di carbonio oppure pannelli di Nomex di vario spessore, a seconda delle differenti geometrie e necessità strutturali.
Il manufatto è stato posto messo in un sacco a vuoto e poi posto sotto pressione in modo da aspirare via l’aria e la resina superflua. La polimerizzazione in autoclave è stata eseguita rispetto, a temperature intorno a 100 °C e pressioni positive comprese tra 1.5 e 6.0 bar, con tempi di cura dell’ordine delle 24-36 ore. Questo processo di autoclave moulding è stato scelto allo scopo di garantire una maggiore stabilità dimensionale e qualità superficiale delle parti.
Dopo la produzione, i diversi segmenti del veicolo sono stati allineati ed assemblati insieme, anche grazie a strutture di supporto, dime e perni di fissaggio. La carrozzeria è stata infine lucidata ed incollata utilizzando colla bicomponente.
Terminata la progettazione e produzione, il veicolo è stato messo in strada dove ha evidenziato un consumo energetico superiore a quanto previsto.
Ingegneria inversa
Per indagare e risolvere questa discrepanza, si è pensato di rilevare le geometrie reali del veicolo. Allo scopo è stato utilizzato un braccio laser di misura portatile FARO, modello R, che ha garantito una scansione 3D con precisione del decimo di millimetro (Fig. 3). Sono state ottenute circa 800.000 coordinate spaziali rappresentative della sagoma di veicolo e che hanno permesso di valutare le deviazioni rispetto alla geometria originale. La Figura 4 illustra l’entità della deviazione: gli errori maggiori sono evidenti nella zona del tetto, che è stata rimaneggiata per migliorane le funzionalità, e delle carenature delle ruote, con differenze fino a ±50 mm. Il corpo alare principale (ossia la parte superiore ed il ventre) del veicolo è risultato meno soggetto ad alterazioni, con differenze geometriche inferiori a 10 mm rispetto al progetto originale.
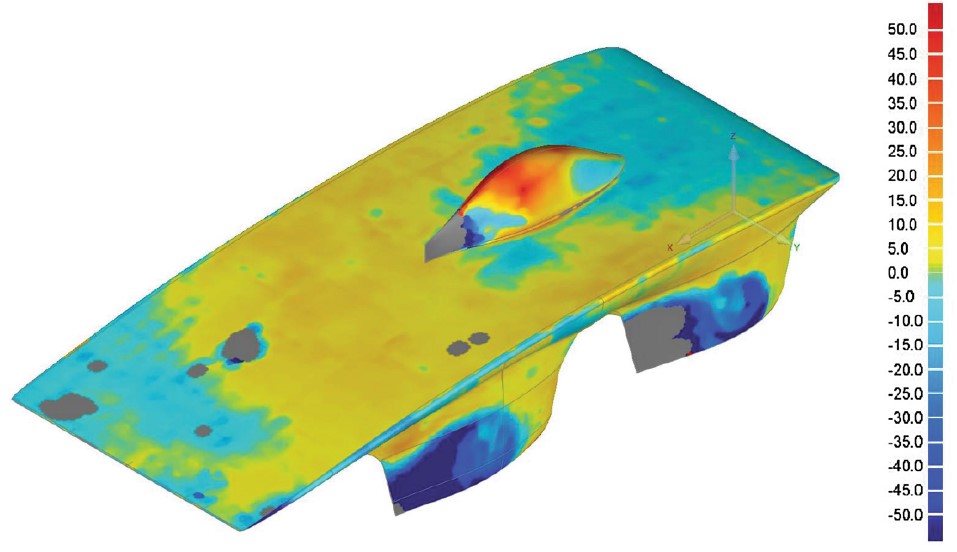
Risultati e comparazioni
Dai dati di scansione, è stato generato un nuovo profilo CAD tridimensionali, utilizzato poi per nuove analisi aerodinamiche (CFD). Sono state considerate le stesse condizioni utilizzate in fase di progettazione iniziale (es. direzione di avanzamento, modello di turbolenza, condizioni al contorno, ecc.), trascurando di investigare situazioni complesse (es. vento trasversale, imbardata o beccheggio). È stata calcolata la forza di resistenza totale (pressione e resistenza viscosa), calcolando il CdA attraverso la citata Eq. 1.
Il confronto ha lasciato emergere diverse considerazioni:
- la superficie totale è differente: 24.15 m2 nella versione originale e 24.92 m2 nel veicolo reale, per una differenza del +3.2%.
- la distribuzione della pressione sulle superfici, nonché le linee di flusso appaiono analoghe (Figura 5) lasciando intendere uno stesso comportamento aerodinamico generale.
- in nessuno dei casi emergono regioni di controflusso o grandi vortici o altre strane entità: tutto ciò è positivo in termini aerodinamici.
- la differenza principale è stata osservata nella regione superiore con un troncamento eccessivo presente sulla geometria reale che genera piccoli vortici a valle (e che possono essere meglio apprezzati in Fig. 5b).
Una comparazione tra la forza di resistenza alle diverse velocità è mostrata in Fig. 6a. La Figura 6b riporta invece il CdA per entrambe le geometrie, evidenziando una differenza marginale (+0,9% nel veicolo reale) di queste grandezze.
L’impatto di tali differenze in termini di consumi energetici, che è quello che realmente interessa, può essere calcolato tenendo conto di un peso della vettura di 280 kg (batteria e pilota incluso), coefficiente di rotolamento degli pneumatici di 0.005, efficienza della trasmissione del 90% e una strada pianeggiante. La tabella 1 illustra queste stime alle diverse velocità, con una perdita di efficienza dell’ordine di 1%. Per quanto questa perdita possa apparire minima, nella concretezza analizzata equivale a trovarsi 30 km indietro, 20 minuti in ritardo, al traguardo.
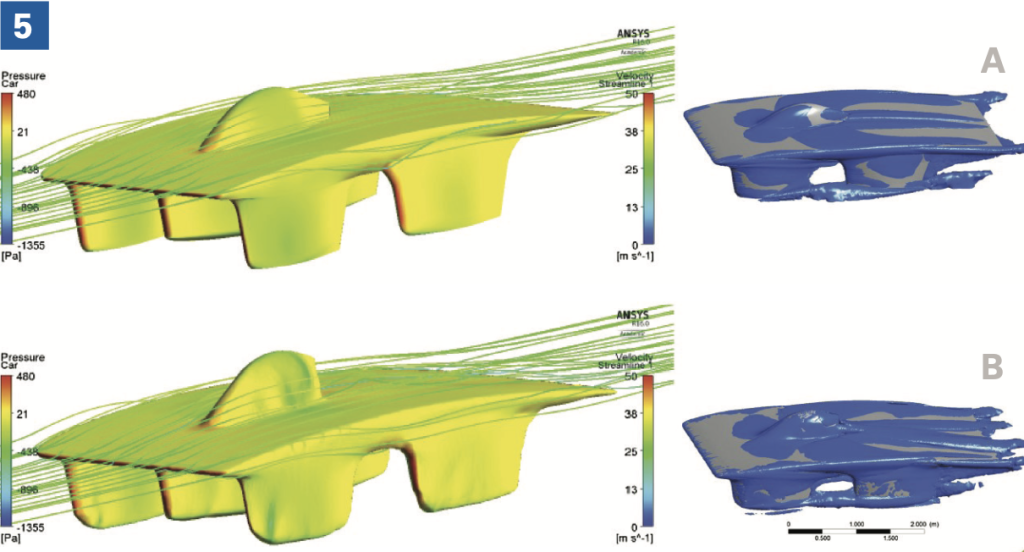
Discussione
Il processo di produzione di una auto in fibra di carbonio comprende una serie di passaggi che generano chiaramente cambiamenti nella geometria e nelle dimensioni. Nel caso in studio, rispetto alla geometria iniziale sono state misurate differenze geometriche fino a 50 mm. Su un veicolo lunga 4.5 m, queste deviazioni sono visivamente impercettibili ma possono avere un impatto negativo sulle prestazioni aerodinamiche.
Da una analisi semplificata è emerso un incremento nel consumo energetico di qualche punto percentuale (1-2%). Tale valore può sembrare marginale, ma è anche inutile rinunciare a porci rimedio. In questo senso, i trattamenti superficiali possono tornare d’aiuto.
Il grafico dell’elicità sul CAD originale mostra la generazione di vortici nella parte frontale della chioma, producendo una separazione anticipata del flusso e, quindi, uno strato limite turbolento. Per questo motivo le piccole variazioni di forma non hanno effetti importanti sul comportamento del flusso.
Oltre alle prestazioni aerodinamiche, è necessario prestare particolare attenzione alle variazioni di forma risultanti dal processo di produzione per l’integrazione di tutti i sistemi, come il pannello solare, l’ergonomia del conducente e le sospensioni.
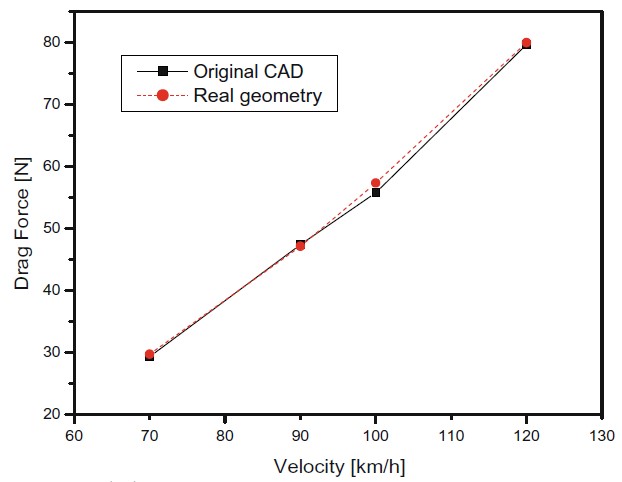
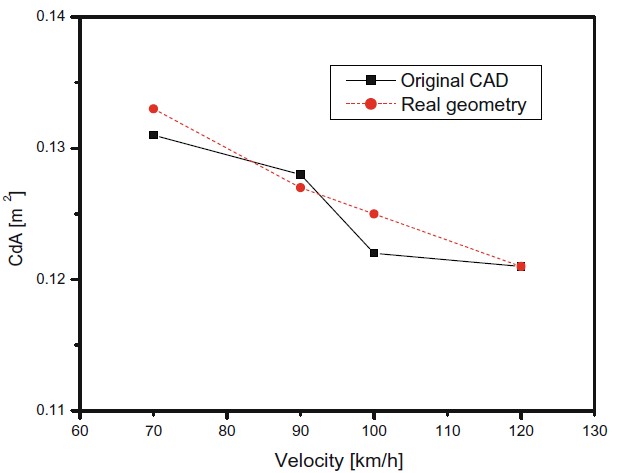
Intervenire sulle superfici
Persino una leggera rugosità superficiale inattesa può aumentare significativamente la resistenza aerodinamica ed è per questo che è necessario intervenire sulle superfici (Fig. 7). Ad esempio, uno studio di alcuni anni fa ha dimostrato che una rugosità superficiale di soli 50 micrometri può causare un aumento della resistenza aerodinamica del 5-10% su un corpo cilindrico. Inoltre, un aumento della rugosità superficiale può aumentare notevolmente l’effetto di trascinamento. Ad esempio, un aumento di rugosità del 100% può portare a un aumento dell’effetto di trascinamento del 10-20%.
Le superfici ruvide possono poi causare la separazione del flusso d’aria più precocemente rispetto a superfici lisce favorendo le turbolenze. Questo può portare a una ridotta portanza e a una maggiore resistenza aerodinamica. Il controllo delle separazioni del flusso è fondamentale per l’ottimizzazione dell’aerodinamica. Per tale motivo, non è solo sufficiente, come spesso accade, valutare l’effetto di pressione e di distribuzione della pressione sul veicolo, per quanto questi aspetti possano restare essenziali. Una distribuzione non uniforme della pressione, infatti, potrebbe arrivare ad influenzare la portanza e la stabilità con effetti seri non solo sulla efficienza ma anche sulle prestazioni e guidabilità di veicolo.
Resta infine scontato come le tolleranze dimensionali e imperfezioni di accoppiamento delle superfici possono causare interferenze del flusso. Ad esempio, il design di un’auto dovrebbe minimizzare le interferenze del flusso tra la carrozzeria principale e i componenti aggiuntivi come specchietti retrovisori o alettoni. Queste interferenze non solo impattano sull’efficienza, ma possono anche portare ad effetti indesiderati più evidenti (es. rumori, vibrazioni e risonanze).
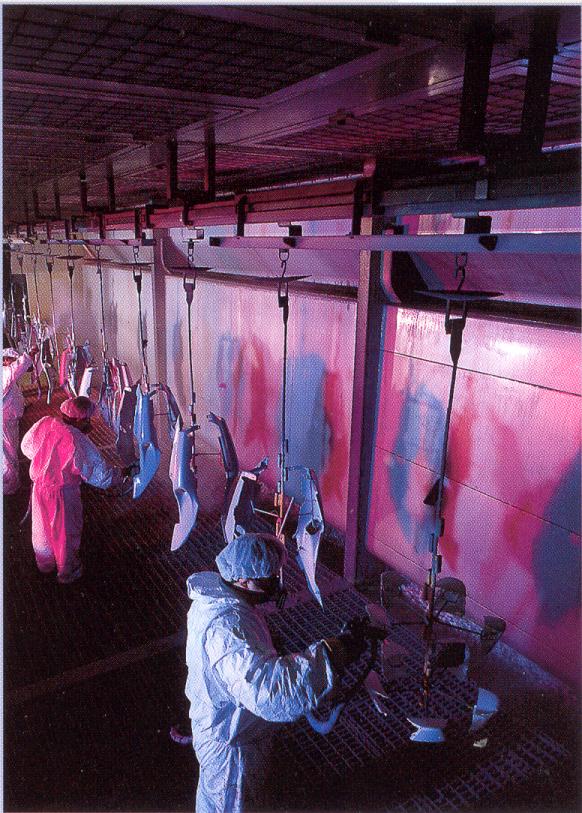
Fig. 7. Linea di verniciatura per parti automobilistiche