Viene illustrato un metodo di compensazione del percorso utensile basato sulla misurazione in-process, del profilo del fianco per la rettifica di un utensile per lo skiving
Esiste una forte e crescente domanda di frese skiving per la produzione di massa di ingranaggi. Rispetto al processo di taglio tradizionale, lo skiving elimina l’interruzione del taglio, offrendo nuove opportunità per un utilizzo di utensili anche in metallo indurito. Ciò apre nuove sfide:
1) le frese possono deviare dal profilo ad evolvente in modo anche significativo;
2) l’uso di mole diamantate rende la ravvivatura relativamente costosa e dispendiosa in termini di tempo. In questo contesto, abbiamo sviluppato due metodi complementari per affrontare questi problemi del processo di rettifica. In primo luogo, abbiamo sviluppato una “compensazione del percorso di rettifica” che consenta di correggere gli errori dell’angolo di pressione della fresa senza dover modificare il profilo della mola. Questa soluzione si è dimostrata efficace al punto tale che possiamo aggiungere una bombatura di oltre 10 micrometri utilizzando esclusivamente la compensazione (ndr: senza dover modificare il profilo della mola). In secondo luogo, abbiamo sviluppato una procedura di misura del profilo del fianco “in-process” (ndr: durante il processo di taglio), basata su dati provenienti da una sonda analogica a contatto. Questa procedura si avvale del controllo degli assi della macchina, consentendo di seguire un percorso non lineare con una precisione superiore al micrometro. La procedura calcola la geometria di riferimento per il profilo del fianco sulla base del profilo nominale della mola e del percorso di rettifica. Le deviazioni della geometria del fianco rispetto a quella di riferimento vengono misurate e compensate. Nel caso in cui la geometria di riferimento sia un profilo ad evolvente, il report di misura sarà direttamente paragonabile al rapporto prodotto da una tradizionale macchina di misura per ingranaggi. Quando si imposta la rettifica di una fresa per skiving, si può valutare se i fianchi rettificati corrispondano direttamente al profilo teorico, senza dover comprendere i complessi dettagli geometrici del progetto. Si può quindi valutare immediatamente quale compensazione si debba applicare per ottenere il risultato desiderato, senza rimuovere la fresa dalla macchina. Esiste una forte sinergia tra i due approcci, che semplifica l’altrimenti difficile impostazione della rettifica di queste frese.
Introduzione
Esiste una significativa e crescente richiesta di frese da taglio in metallo indurito. Queste frese sono utilizzate per la produzione di massa di ingranaggi [1]. A differenza dei creatori o delle frese per sagomatura, le frese per skiving non sono adatte per la produzione di diversi ingranaggi dello stesso modulo ma con un numero arbitrario di denti o una grande variazione dello spostamento del profilo. In genere, per la produzione di un particolare ingranaggio viene prodotta una fresa specifica. Le frese skiving rendono pratico il taglio di ingranaggi senza la necessità di una macchina utensile speciale, ad esempio il grezzo può essere tornito su un tornio CNC e poi finito con una fresa skiving.
Rispetto ai creatori, le frese skiving hanno il vantaggio di poter essere utilizzate per lavorare anche ingranaggi interni, così come ingranaggi piccoli realizzati di pezzo su alberi e vicini ad altri ingranaggi di diametro maggiore, soluzione tecnicamente non realizzabile mediante creatore. Rispetto alle frese shaper, il carico di taglio sul dente di una fresa skiving risulta minore all’interno e all’esterno del taglio, riducendo i problemi che tipicamente si hanno alla fine della lavorazione. Inoltre, permette una migliore finitura superficiale e l’uso di acciai cementati (relativamente fragili), al posto dell’acciaio ad alta velocità (HSS). Inoltre, il tempo di lavorazione con le frese per skiving è notevolmente inferiore a quello delle frese shaper. L’impiego del metallo indurito offre la possibilità di tagliare ingranaggi interni con l’acciaio in uno stato più duro rispetto a quanto possibile con frese in HSS.
La produzione di una fresa per skiving con un elevato standard di precisione richiede un’attenta impostazione e controllo del processo, nonché una ravvivatura delle mole molto precisa. Quando si producono frese per skiving in metallo indurito, in genere si utilizzano mole diamantate, per cui la ravvivatura è più lenta e più costosa. Per questo motivo, è importante cercare di eliminare la necessità di ripassare il fianco con una mola per portare il profilo entro la tolleranza specificata. In questa sede analizziamo la possibilità di misurare, direttamente durante il processo di produzione, il profilo del dente di una fresa a pignone [2], da utilizzare insieme alla compensazione del percorso di rettifica, per produrre frese per skiving di elevata precisione (DIN-AA [3]) senza dover ricorrere alla finitura del profilo mediante molatura (per ottenere la tolleranza desiderata). Ci limitiamo all’uso della rettifica a generazione (IGG).
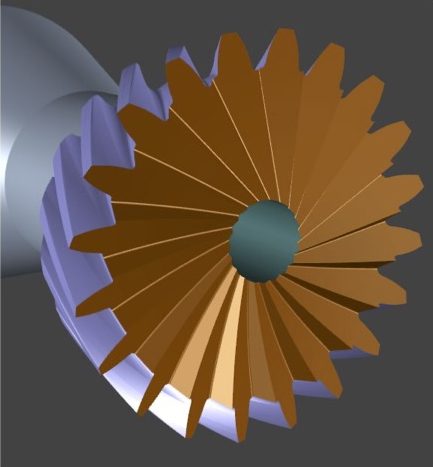
Produzione di frese per pignoni mediante rettifica a generazione
I metodi di taglio per generazione si basano sulla produzione di un ingranaggio utilizzando una mola che abbia anch’essa il profilo di un dente. Questo cosiddetto “dente da taglio” percorre lo stesso percorso del dente dell’ingranaggio, generando il profilo corretto imitando un ingranaggio reale che ingrani con quello da tagliare. Spesso, nel caso di un ingranaggio a cremagliera, si tratta di un semplice dente con profili lineari per le sezioni attive dei fianchi. Le frese a creatore e a pignone impiegano anch’esse metodi di generazione per tagliare gli ingranaggi. Anche gli ingranaggi vengono comunemente rettificati (dopo il trattamento termico) con metodi di generazione. Nel metodo IGG, la mola segue il contatto dato dall’ingranamento di un dente fittizio della cremagliera. La mola si muove avanti e indietro, trasversalmente al dente della cremagliera. Per comprendere il metodo IGG (figura 1) è utile visualizzare una cremagliera fittizia (a livello concettuale – non esiste fisicamente) a contatto con la fresa. Questa cremagliera, che ha un angolo d’elica corrispondente a quello della fresa, non ha gioco, cioè quando la fresa ruota, la cremagliera si muove in modo sincrono. Anche la mola è sincronizzata con la cremagliera (a tal fine, i fianchi della cremagliera sono invertiti) e quindi, mentre la mola oscilla avanti e indietro, la cremagliera può muoversi longitudinalmente (da un lato all’altro). A sua volta, anche la fresa ruoterà. Per realizzare le frese a pignone, è necessario introdurre un gioco laterale. Questo si ottiene mediante dentatura conica nella cremagliera fittizia; un modo semplice per farlo è quello di avere uno spostamento del profilo lineare lungo la direzione trasversale della cremagliera [4]. Di solito c’è un gioco tra la mola e lo spazio tra i denti della fresa, in modo che la prima si stacchi da uno dei fianchi della fresa (a destra o a sinistra) alla volta e venga poi sincronizzata con il lato da molare.
Se i fianchi attivi della cremagliera sono superfici piane, il profilo della mola che li rettificherà sarà rettilineo e il fianco della fresa sarà quindi ad evolvente [5, 6]. È pratica comune specificare questo profilo per ciascun fianco (destro e sinistro) mediante due parametri: il diametro di base e l’angolo d’elica di base [4, 7]. Se si desidera produrre un ingranaggio con un profilo nominale ad evolvente, la fresa da taglio avrà un profilo che si discosta molto poco da questo. Tuttavia, le anche minime deviazioni potranno essere efficacemente compensate utilizzando una bombatura. Per una fresa da skiving, questa deviazione può diventare più pronunciata, come nel caso di ingranaggi e frese di concezione più avanzata. Queste deviazioni vengono spesso gestite modificando leggermente il profilo della mola. Se la curvatura del profilo della mola, in combinazione con l’angolo di spoglia della fresa, risultasse troppo grande, il profilo del fianco cambierebbe con la progressiva usura dell’utensile (dovuta alla ripetuta affilatura). Per rendersene conto, si consideri la proprietà (unica) dei profili ad evolvente per cui, anche modificando la distanza tra una coppia di ingranaggi, la geometria del fianco non cambia e gli ingranaggi ingraneranno anche variandone l’interasse. Inoltre, si consideri che più il profilo della ruota risulta curvo, più ci si allontana dalla geometria ad evolvente. Ricordiamo che la mola riproduce una cremagliera che ingrana con la fresa e che (a causa del gioco della punta della fresa) la distanza tra questa cremagliera e la fresa cambia con la progressiva usura dell’utensile. Quindi, a differenza di un fianco ad evolvente, il profilo generato sarà sempre leggermente diverso a seconda dello stato di usura dell’utensile. Di solito, tuttavia, la combinazione di curvatura della mola e gioco di testa è tale da non costituire un problema significativo.
Misurazione del profilo del dente
La misura del profilo del dente viene effettuata con una macchina di misura per ingranaggi (GMM). Questa può essere considerata come una versione speciale di macchina di misura a coordinate, dotata di un asse rotante ad alta precisione, di una sonda di scansione analogica e di uno speciale software. Una GMM è particolarmente adatta a misurare i fianchi delle frese a pignone con una precisione molto elevata, inferiore al micrometro. Per garantire questa accuratezza, scansiona il fianco nel piano trasversale seguendo il profilo nominale ad evolvente definito mediante diametro di base e angolo d’elica di base [8]. La sonda, però, è spostata rispetto al dente. Anche in questo caso, possiamo immaginare che il contatto della sonda segua quello teorico tra l’ingranaggio e una cremagliera, ma in questo caso il diametro primitivo coincide con quello di base, i.e. l’angolo di pressione è pari a zero e l’angolo di elica risulta uguale all’angolo di elica di base. Poiché anche in questo caso il fianco della cremagliera è una superficie piana e poiché questa cremagliera fittizia non cambia orientamento durante la scansione, la direzione normale al fianco risulta costante per tutta la misura; in altre parole, la direzione di riferimento della macchina non cambia. In questo schema è implicito il presupposto che qualsiasi deviazione (errore) del fianco si verifichi senza modificare in modo significativo la direzione normale. Dal punto di vista geometrico, questa è una buona approssimazione per piccole deviazioni del profilo, mentre per deviazioni maggiori i risultati saranno deterministici, sebbene con una componente non lineare. Poiché la direzione della deflessione della sonda è costante per tutta la scansione, è molto semplice riportarla nel piano trasversale, ovvero dividendo la deflessione per il coseno dell’angolo dell’elica di base. Si noti che questo approccio permette una scansione del fianco in relazione ad una posizione di rotazione arbitraria (intorno all’asse di rotazione della fresa); in altre parole, il risultato è indipendente da qualsiasi errore di passo.
La nostra misura “in-process” estende l’approccio GMM classico. Invece di seguire il profilo nominale ad evolvente, seguiremo il fianco nominale risultante dai percorsi di rettifica CNC non compensati e dal profilo nominale della mola. D’ora in poi ci riferiremo a questo fianco nominale come modello del fianco. Per chiarire meglio, una volta specificati un insieme di percorsi di rettifica e un profilo della mola, il profilo del fianco risulta determinato in modo univoco e per calcolare questo profilo risultante utilizziamo i modelli matematici/computazionali standard sviluppati (con esempi) in [5]. Per come questi metodi possano essere utilizzati per ottenere la geometria di una fresa per skiving si vedano anche [9, 10]. Nel caso di un profilo ad evolvente semplice, il nostro percorso sarà uguale al percorso e alla misura GMM tradizionale. Quando il fianco nominale però non è ad evolvente, ci muoveremo ancora nel piano trasversale, ma calcoleremo il punto di contatto rispetto al fianco nominale per cui la direzione della deflessione nominale potrebbe cambiare leggermente durante la scansione. Per valori di deflessione piccoli, la misura sarà comunque lineare.
Estendiamo il modello del fianco per includere un offset della ruota (essenzialmente uno spostamento del profilo) che consente di misurare la fresa quando è ancora sovradimensionata.
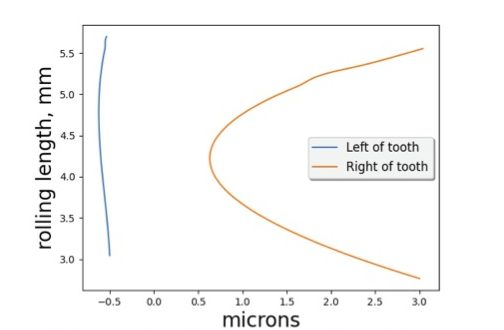
Compensazione del percorso
Abbiamo sviluppato un nostro approccio per la compensazione. Si basa sul calcolo del raggio del fianco della ruota nel punto di contatto con l’utensile. Ogni punto di contatto della ruota viene proiettato radialmente sul piano di misura trasversale. A ciascun punto viene quindi assegnato uno spostamento per adattare il risultato sul piano di misura al risultato desiderato. Questo spostamento viene poi trasferito ad ogni posizione lungo il percorso di rettifica in base al punto in cui si stima che la mola radiale tocchi. In questo modo, la regolazione sul piano di misura (bidimensionale) viene estesa al percorso di taglio (tridimensionale). In altre parole, il percorso di rettifica viene perturbato per simulare ciò che accadrebbe se il profilo della mola fosse regolato per correggere il risultato sul piano di misura. La compensazione del percorso si basa sulla presenza di uno spazio tra la mola e i fianchi della fresa, in modo tale che quando la mola sta tagliando un fianco, sia libera da contatti con l’altro fianco: in questo modo, i fianchi destro e sinistro possono essere compensati indipendentemente l’uno dall’altro. Abbiamo utilizzato questa compensazione in modo estensivo su un’ampia gamma di modelli di frese e rettificate da persone diverse dimostrandosi molto efficace.
Il problema
Quando si imposta l’affilatura di una fresa con fianchi non involuti, utilizzando il metodo IGG, la geometria del profilo del fianco cambia con l’offset della mola (spostamento del profilo), presentando una difficoltà significativa. L’ideale sarebbe misurare la geometria del fianco quando la fresa è ancora sovradimensionata. A volte è possibile farlo rendendo la mola più sottile e avvicinandosi alla geometria finale con un offset rotativo individuale applicato a entrambi i fianchi della fresa, nella posizione radiale finale. Ma questa non è sempre una soluzione praticabile, perché spesso non è auspicabile (o addirittura fattibile) rendere la mola sufficientemente sottile.
Per ovviare a questo problema, le misure vengono fatte con riferimento al modello del fianco sovradimensionato (non ancora finito), offrendo la possibilità di impostare con precisione la macchina per ottenere la tolleranza prima di raggiungere la dimensione finale. Questo è importante quando si tratta di rettificare un pezzo grezzo con fianchi non involuti (costoso), in quanto consente di valutare lo stato della rettifica quando c’è ancora abbastanza materiale per correggere eventuali problemi di precisione.
L’esperimento
Procedura sperimentale/specifiche
Il nostro approccio consiste nell’affilare una fresa in sovradimensionamento utilizzando la tecnica IGG. Il sovradimensionamento deve essere ottenuto spostando la mola verticalmente, lontano dalla fresa, di una quantità fissa (spostamento del profilo). Con la tecnica IGG, per un profilo non involuto, il profilo nominale del dente (misurato) cambierà con lo spostamento del profilo. Abbiamo progettato il nostro esperimento per testare la capacità di impostare efficacemente la compensazione per una fresa utilizzando la misurazione “real-time”, quando questa è ancora significativamente sovradimensionata, e quindi produrre una fresa con il profilo del fianco in tolleranza quando viene raggiunta la dimensione finale. Utilizziamo un grande spostamento del profilo, per esagerare l’effetto.
Abbiamo progettato una fresa per skiving che presenta un fianco essenzialmente ad evolvente sul lato sinistro del dente e con una significativa bombatura sul lato destro del dente. Abbiamo prodotto questa fresa con la tecnica IGG su una rettificatrice per utensili e frese a controllo numerico, utilizzando una mola in ossido di alluminio e un grezzo in HSS temprato (asta in HSS da 1″).
La mola è stata sottoposta a ravvivatura su macchina a controllo CNC (e un rullo di ravvivatura) a valle di una calibrazione ad alta precisione. Da qui in poi non è stato utilizzato alcun feedback di misura per la ravvivatura della mola; qualsiasi cosa facesse la macchina è stata accettata alla cieca. Con la fresa ancora significativamente sovradimensionata, i denti sono stati rettificati e misurati, uno alla volta, e la compensazione è stata regolata fino ad ottenere un risultato accettabile per quanto riguarda il profilo del fianco. Successivamente, la compensazione non è più stata modificata e la fresa è stata rettificata fino alla dimensione finale. Al termine della lavorazione, la fresa è stata misurata anche con una macchina GMM Klingelnberg P26, consentendo un confronto diretto con la misurazione “in corso d’opera”.
I diversi denti della fresa sono stati rettificati a coppie con diversi spostamenti di profilo, in modo da permettere poi una misura sistematica dei risultati. Ogni coppia era composta da un dente compensato e uno non compensato. La coppia di denti più sovradimensionata aveva uno spostamento di 0,24 mm, vi era poi una coppia con 0,12 mm e infine una coppia a misura. Per ogni coppia di denti, abbiamo acquisito due serie di dati: la misura in-process rispetto al modello del fianco e la misura GMM rispetto al riferimento. I dati sono conclusivi e supportano fortemente la nostra tesi sulla bontà del processo.
Progettazione della fresa e dettagli
La fresa è stata progettata con il software ESCO PTM 5.0.1.0. La fresa è una fresa per skiving con un angolo d’asse di 30° (elica destrorsa), nessun angolo di inclinazione, un angolo di spoglia superiore di 10°, un angolo di spoglia di 5° (angolo di 30° con faccia a gradino) e 20 denti. Questa fresa è stata progettata per produrre (tagliare) un semplice ingranaggio cilindrico a 24 denti, con angolo di pressione pari a 20° e modulo pari ad 1 mm. La figura 2 mostra una simulazione della fresa. Il design geometrico della fresa per skiving determina una bombatura significativa sul lato destro del fianco del dente (~2,5μm con deflessione sul piano normale) e una bombatura molto ridotta sul lato sinistro (figura 3). La bombatura del fianco destro provoca effetti non invarianti durante la rettifica della fresa. In particolare, causa la variazione della deviazione dell’angolo del profilo fHα con l’avanzamento radiale in IGG. Questa variazione della geometria del fianco con lo spostamento radiale rende difficile l’impostazione dell’affilatura.
I risultati di scansione attesi
I risultati di scansione previsti per una misura del profilo del fianco mediante macchina GMM alla fine dell’utensile (EOT) sono mostrati nella figura 3. Abbiamo potuto misurare all’EOT perché abbiamo esteso i fianchi oltre l’EOT durante la produzione.
Per questo progetto abbiamo assegnato un modello elicoidale, con il fianco sinistro avente diametro di base db = 21,348 mm e angolo d’elica di base βb = 31,114°, il fianco destro diametro di base db = 21,5 mm e angolo d’elica di base βb = 25,158°, ottenendo così il rapporto di scansione nominale del fianco (GMM) mostrato nella figura 3. L’intervallo di misura [11] per i fianchi destro e sinistro è stato impostato nel range (diametro) tra 22,2 mm a 24,2 mm. Gli angoli d’elica non sono risultati essere parametri critici, ovvero i risultati delle scansioni del profilo del fianco non saranno sensibili ad essi.
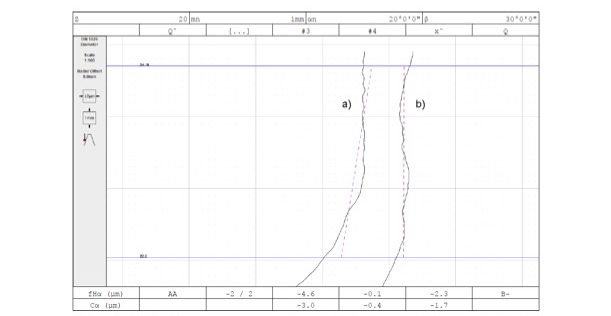
Risultati e discussione
Sinistra del dente, caso di involuzione
Il fianco a sinistra del dente presenta una bombatura molto ridotta ed è essenzialmente ad evolvente. Sebbene questo sia il lato più “semplice” del dente, consente un confronto diretto con i risultati GMM. I dati presentano alcuni punti interessanti da discutere. Ci aspettiamo che il profilo sia invariante in funzione dell’input (spostamento del profilo). Questo nonostante la presenza del rilievo del fianco, con la geometria che rimane ad evolvente, anche se con angoli di elica e di pressione modificati rispetto all’ingranaggio da tagliare. Si tenga presente che è solo approssimativamente ad evolvente, senza che nessuna circostanza geometrica imponga che lo sia esattamente.
Inizialmente abbiamo impostato la macchina e compensato il percorso con l’ingresso impostato su 0,24 mm di sovradimensionamento (0,48 mm sul diametro). La misurazione “in corso d’opera” è stata effettuata con riferimento al modello del fianco. I risultati sono stati registrati per un dente con e uno senza compensazione, con un netto miglioramento del profilo misurato grazie alla compensazione. La compensazione è stata impostata con due cicli di molatura e misurazione, dopodiché non è stata più regolata. Questi risultati sono mostrati nella figura 4. La nostra misurazione in-process stima la deviazione dell’angolo del profilo fHα utilizzando una regressione lineare ai minimi quadrati sull’intervallo di valutazione e la calcola nel piano normale (vedi didascalia della figura 4). Il GMM calcola la differenza tra il punto all’inizio e alla fine dell’intervallo di valutazione e riporta il valore fHα nel piano trasversale. Per convertire i risultati dal piano normale al piano trasversale, si prende il valore misurato nel piano normale e lo si divide per il coseno dell’angolo d’elica di base, cos(βb).
Le linee di miglior adattamento risultanti sono mostrate nel grafico. Poiché non utilizziamo la stessa definizione di fHα usata nelle misure GMM, possono esserci discrepanze tra i nostri risultati e quelli ottenuti mediante GMM. Tuttavia, l’esperienza dimostra come con questo approccio sia possibile ottenere un buon accordo quando il valore di fHα è molto piccolo, il che rappresenta l’obiettivo.
Il risultato iniziale della rettifica non compensata presenta errori non trascurabili per quanto riguarda fHα (-4,6 μm) e la bombatura Cα (-3,0 μm). Con la compensazione, questi valori si sono ridotti rispettivamente a -0,1 μm e -0,4 μm. Quando si imposta la compensazione, un dente può essere compensato, rettificato a un determinato input e quindi misurato in-process. In questo modo, a un determinato avanzamento, è possibile rettificare e misurare un singolo dente alla volta, consentendo di regolare la compensazione passando al dente successivo senza modificare l’avanzamento.
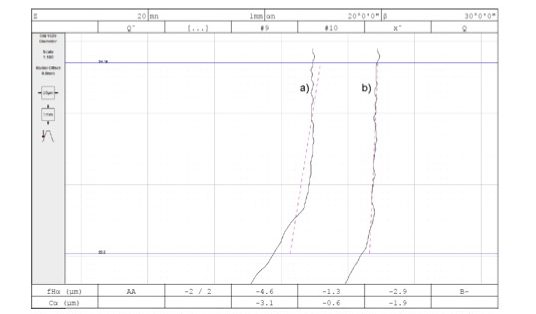
Successivamente, abbiamo rettificato la fresa e poi misurato i profili. Abbiamo continuato a lavorare su denti diversi, in modo che i fianchi che hanno prodotto la misura di cui sopra potessero essere ancora misurati in un secondo momento mediante GMM, dopo aver completato tutte le rettifiche; in questo modo la fresa è stata montata in macchina una sola volta, affidandosi alla misura in corso d’opera per ottenere il risultato richiesto. Abbiamo anche rettificato una coppia di denti con l’avanzamento impostato a 0,12 mm, ma non è emerso nulla di interessante. Nella figura 5 vediamo un risultato molto simile a quello ottenuto con l’offset di 0,24 mm. La differenza maggiore riguarda il valore di fHα per il fianco compensato, che ora è -1,3 μm, ancora ben al di sotto della tolleranza di grado AA di 2 μm [3] e persino della tolleranza informale AAA di 0,8 × AA = 1,6 μm. Sono molti gli elementi che potrebbero aver causato questa piccola differenza come l’usura delle ruote o la deriva termica, ma non abbiamo avuto modo di indagare su questo aspetto. Quando abbiamo finito l’affilatura, la fresa è stata rimossa dalla macchina e misurata sul GMM. I risultati sul GMM sono mostrati nella figura 6 e sono, entro 1μm, coerenti con i risultati delle misure in-process. Il risultato è molto buono: la combinazione di misura con compensazione in-process ha migliorato notevolmente sia l’errore di bombatura (Cα) che quello di angolo fHα, mostrando valori che rientrano nel range richiesto per una fresa con le tolleranze più strette, come misurato mediante GMM. Ciò consente di impostare in modo affidabile una fresa per l’affilatura secondo standard di precisione elevati, senza dover rimuovere la fresa dalla macchina per la misurazione.
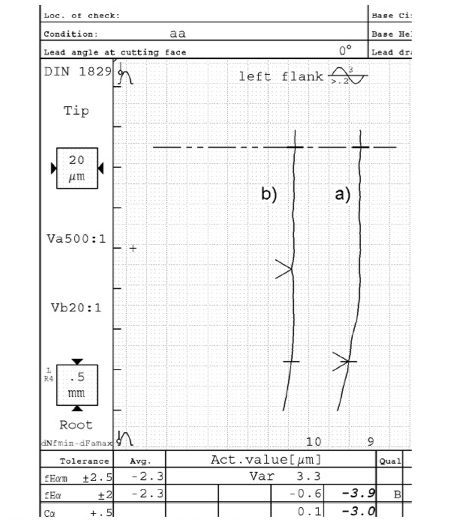
Fianco destro del dente, caso non ad evolvente
L’aspetto interessante del caso non ad evolvente è che c’è da aspettarsi che la misura del profilo del fianco cambi con l’avanzamento. Questo rappresenta una sfida durante l’impostazione della rettifica, quando il pezzo grezzo utilizzato per l’impostazione non può essere scartato. Anche se l’esempio qui utilizzato non è ad evolvente solo a causa della bombatura, esistono altre possibilità di deviazione dal profilo ad evolvente. Il nostro approccio per la misurazione in-process è abbastanza generico e può gestire altri tipi di deviazioni dal profilo ad evolvente.
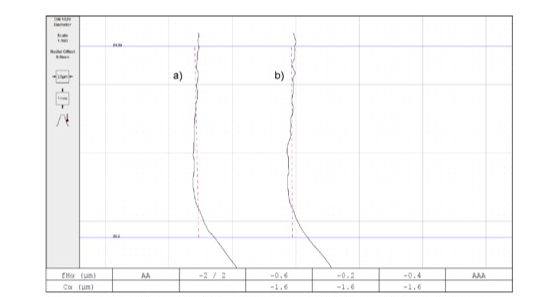
Il fianco sinistro e quello destro sono stati rettificati insieme. I risultati iniziali di sovradimensionamento di 0,24 mm sono mostrati nella figura 7. Sulla base di questi risultati, l’errore di coronamento su queste curve è stato giudicato accettabile (Cα = -1,6). Il valore di errore di angolo fHα è stato corretto con una compensazione che ha portato ad un miglioramento del risultato, anche se molto ridotto. Con il senno di poi, vale la pena notare come queste curve si discostino maggiormente dal profilo di progetto in prossimità del diametro più piccolo dell’intervallo di valutazione, e che questo è il problema principale alla base dell’errore d’angolo fHα. L’errore in prossimità del diametro più piccolo è dovuto a un problema di impostazione dei percorsi di rettifica. L’intervallo di valutazione non è stato spostato assieme l’alimentazione ed il contributo maggiore all’errore fHα proviene dalla deviazione più vicina all’estremità del diametro piccolo dell’intervallo di valutazione. Se si ipotizza che questo errore derivi da un errore nel profilo della ruota, allora lo spostamento dell’intervallo di valutazione con l’alimentazione risulterebbe la procedura corretta da seguire. Questo è confermato dal confronto tra la figura 7 e la figura 9. Nella figura 9, la deviazione verso il diametro inferiore è stata abbassata e una parte minore rimane nell’intervallo di valutazione. Questa deviazione si traduce in materiale extra nel diametro inferiore dell’intervallo di valutazione, riducendo il valore di fHα, ed è in gran parte responsabile della differenza di risultato tra i due valori di ingresso per la misura in-process.

Ora che stiamo considerando un fianco non ad evolvente, vale la pena di esaminare il risultato della GMM quando è ancora sovradimensionato. Questo ci permette di mostrare come la misura cambi con l’avanzamento (figura 8). Sia la bombatura (Cα ~ -5,4 μm) che l’errore di angolo fHα (~ -6,6 μm) sono considerevolmente maggiori rispetto alla misura in-process mostrata nella figura 7. Il GMM riporta la bombatura nel piano trasversale dell’angolo dell’elica di base, e quindi nel piano normale questo diventa -5,4 × cos(25,16) = -4,9 μm. La misura in corso d’opera è riportata direttamente nel piano normale e confrontata con il profilo di progetto. Ricordiamo (figura 3) che nel progetto è prevista una bombatura pari a -2,5 μm, quindi l’errore risulta, -1,6 – 2,5 = -4,1 μm. I risultati tra le due misurazioni sono dunque paragonabili.
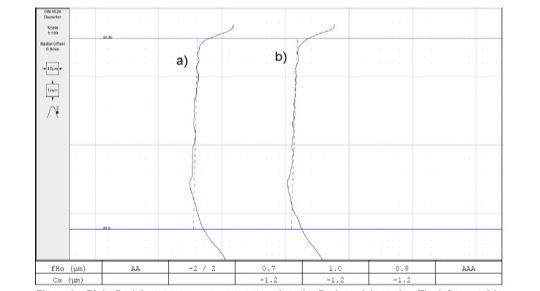
Una delle caratteristiche principali derivanti dal fatto che la misura in-process sia relativa al modello del fianco, è la possibilità di indirizzare il risultato della misura a seconda dell’alimentazione. Riportiamo quindi una serie di misure analoghe a quelle sopra, ma con un’alimentazione pari a zero (cioè la fresa è ora “a misura”). Il risultato per la misura in-process è mostrato nella figura 9 e le misure GMM nella figura 10. Un’analisi simile a quella fornita sopra mostra come la bombatura ottenuta con i due metodi sia confrontabile. La bombatura nel piano trasversale, come si evince dalla figura 3, dovrebbe essere di circa -3,5 / cos(25°) = -3,8 μm, ma secondo il rapporto GMM, figura 10, il risultato è di -4,6 μm. La misura in corso d’opera tiene conto di -1,2 / cos(25°) = -1,3 μm, lasciando -3,3 μm, che risulta ben allineato con il valore previsto di -3,8 μm. I risultati delle misure di fHα sono molto buoni, e confrontabili tra i risultati in-process e quelli GMM. La misura in-process per il caso non ad evolvente si è dimostrata molto efficace, consentendo di impostare la compensazione della traiettoria mentre la fresa è ancora sovradimensionata e di ottenere un buon risultato finale senza dover rimuovere la fresa dalla macchina per misurare durante l’impostazione.
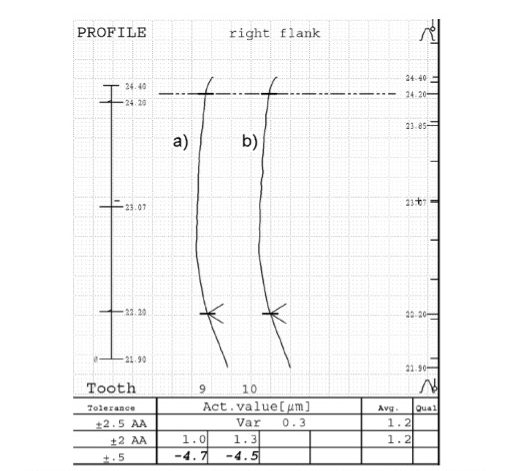
Conclusioni
Abbiamo testato la combinazione di compensazione del percorso e misurazione in-process per controllare il profilo del fianco durante l’impostazione della rettifica di una fresa a pignone con la tecnica IGG. La misura in-process è relativa a un modello del fianco che la macchina deve rettificare non specificato tramite il profilo ad evolvente teorico. Una caratteristica interessante del modello del fianco è che può essere facilmente utilizzato quando la fresa è ancora fuori misura. Ci siamo concentrati su un processo sistematico per fornire una serie di dati, mostrando come l’approccio possa essere utilizzato per ottenere il risultato desiderato (validazione mediante confronto con valori misurati su una macchina GMM). Questa analizza la deviazione dell’angolo del profilo fHα rispetto a due punti all’inizio e alla fine dell’intervallo di valutazione, mentre noi l’abbiamo analizzata utilizzando una regressione ai minimi quadrati. Tuttavia, siamo stati in grado di fornire un percorso chiaro e inequivocabile verso la geometria desiderata. Non solo la misura in-process è risultata adatta per la messa a punto della fresa, senza dover sacrificare un pezzo grezzo, ma ha anche mostrato un ottimo potenziale per mantenere l’accuratezza durante tutta la produzione. Il sistema risulta così ottimale, ad esempio, per un impiego da parte di aziende che si affacciano per la prima volta sul settore ingranaggistico, e che non ha ancora a disposizione un costoso sistema GMM.
Stephen R. Williams, Xiaoyu Wang, ANCA Machine Tools