Può sembrare un controsenso, ma dal punto di vista metallurgico questo processo non si riferisce a una saldatura in senso stretto. Scopriamo meglio questa innovativa tecnica di giunzione, che porta con sé molti vantaggi.
La saldatura per attrito a rotazione è un innovativo processo di unione dei materiali senza metallo d’apporto che sfrutta il contatto diretto tra i pezzi per creare una saldatura solida tra due o più parti. Questo metodo utilizza l’attrito generato dal movimento rotatorio e dalla pressione tra i materiali da unire, generando calore sufficiente per fondere le superfici e ottenere una fusione solida. Come spesso succede in ingegneria, la sua scoperta è frutto del caso.
La storia
Gli inizi della saldatura per attrito risalgono al XX secolo, con il metodo di saldatura ad attrito per rotazione, che rappresenta la più antica tra queste tecniche. Nel 1924, W. Richter brevettò il processo di saldatura ad attrito lineare (LFW) in Inghilterra, e nel 1929 nella Repubblica di Weimar.
Tuttavia, la descrizione del processo era approssimativa e H. Klopstock brevettò lo stesso procedimento in Unione Sovietica nel 1924. Fu solo nel 1956, in Unione Sovietica, che si registrarono i primi esperimenti sistematici e la prima descrizione precisa della saldatura ad attrito per rotazione, ad opera di un ingegnere meccanico di nome A. J. Chdikov.
Chdikov fece una scoperta fortuita mentre lavorava nella miniera di Elbrussky: a causa della mancata lubrificazione interna del mandrino del tornio, si accorse di aver saldato accidentalmente un pezzo al tornio stesso. Questo incidente lo spinse a considerare se potesse essere sfruttato per unire materiali, concludendo che era necessario lavorare ad alte velocità di rotazione (all’epoca circa 1000 giri al secondo), frenare immediatamente e applicare pressione ai componenti saldati.
Il processo fu introdotto negli Stati Uniti nel 1960, con aziende come Caterpillar, Rockwell International e American Manufacturing Foundry che svilupparono macchine per questo processo. Brevetti simili furono rilasciati anche in Europa e nell’ex Unione Sovietica.
I primi studi sulla saldatura per attrito in Inghilterra furono condotti dal Welding Institute nel 1961, e negli Stati Uniti nel 1962 da Caterpillar Tractor Company e dal MIT. In Europa, KUKA AG e Thompson lanciarono la saldatura a frizione rotante per applicazioni industriali nel 1966.
«La qualità della saldatura ottenuta tramite questo processo è spesso superiore in termini di resistenza meccanica e integrità strutturale rispetto ad altri metodi», ci dice Inga Akulauskaite-Manocchia, responsabile marketing di KUKA Roboter Italia S.p.A. «Questo fa sì che la saldatura per attrito a rotazione sia altamente apprezzata in applicazioni dove la robustezza e l’affidabilità sono fondamentali».
Questo processo di saldatura innovativo è stato quindi sviluppato per affrontare sfide specifiche incontrate con altre tecniche di saldatura tradizionali. La saldatura per attrito a rotazione si distingue per la sua capacità di unire materiali metallici eterogenei e dissimili, come alluminio, acciaio, titanio e leghe di magnesio.
È un vantaggio significativo in settori quali l’aerospaziale, l’automotive e la produzione di componenti industriali avanzati, dove la combinazione di materiali è spesso richiesta per ottenere prestazioni ottimali. Ce ne parla Nunzio Capelli di Scaglia srl, azienda lombarda nata nel 1938 e che dal 1979 usa questa tecnologia: «Uno dei principali vantaggi della saldatura per attrito a rotazione è la sua capacità di ridurre la zona di fusione rispetto ad altri metodi di saldatura.
Questo è particolarmente vantaggioso quando si lavora con materiali sensibili al calore, poiché si riducono le deformazioni e le alterazioni delle proprietà dei materiali circostanti alla zona di saldatura».
Il processo
Il principio di base di questo processo di saldatura coinvolge l’uso di due parti da unire, le quali sono posizionate in stretto contatto e messe in rotazione relativa una rispetto all’altra. La saldatura per attrito a rotazione si divide in 7 fasi.
- Preparazione: i pezzi vengono montati in due mandrini, uno fisso e uno rotante.
- Contatto e applicazione di pressione: le parti da unire vengono portate a stretto contatto tra loro. Una pressione adeguata viene applicata per assicurare una buona adesione tra le superfici dei materiali. Solitamente, il movimento in senso assiale è generato da un cilindro idraulico.
- Inizio della rotazione: Una volta che le parti sono a contatto e sotto pressione, inizia il movimento rotatorio. Le parti coinvolte vengono fatte ruotare una rispetto all’altra; la rotazione è generata da un motore elettrico e trasmessa ai pezzi tramite un mandrino. In questa fase, le irregolarità geometriche e superficiali vengono rimosse dall’attrito tra i pezzi.
- Generazione di calore per attrito: Il movimento rotatorio tra i materiali crea attrito tra le superfici in contatto. Questo attrito genera calore, portando gradualmente le superfici dei materiali alla temperatura idonea, solitamente al calor giallo. Contaminanti come vernici, ossidi e olii vengono bruciati o distrutti.
- Formazione della giunzione: Quando le superfici raggiungono la temperatura di saldatura, la rotazione si arresta e i pezzi vengono spinti uno contro l’altro per assicurare un’adeguata compenetrazione, creando una giunzione solida. Bolle d’aria, impurità e calamina vengono espulsi, concentrandosi nel cordone di saldatura.
- Raffreddamento e solidificazione: i pezzi vengono mantenuti fermi in posizione e la temperatura scende. Durante questa fase, la giunzione si solidifica e acquisisce le caratteristiche desiderate.
- Rifinitura: Dopo il raffreddamento, la giunzione può richiedere lavorazioni aggiuntive per ottenere le dimensioni e le proprietà desiderate. Queste lavorazioni possono includere la rimozione di eventuali imperfezioni superficiali o la rifinitura della giunzione stessa tramite asportazione di truciolo.
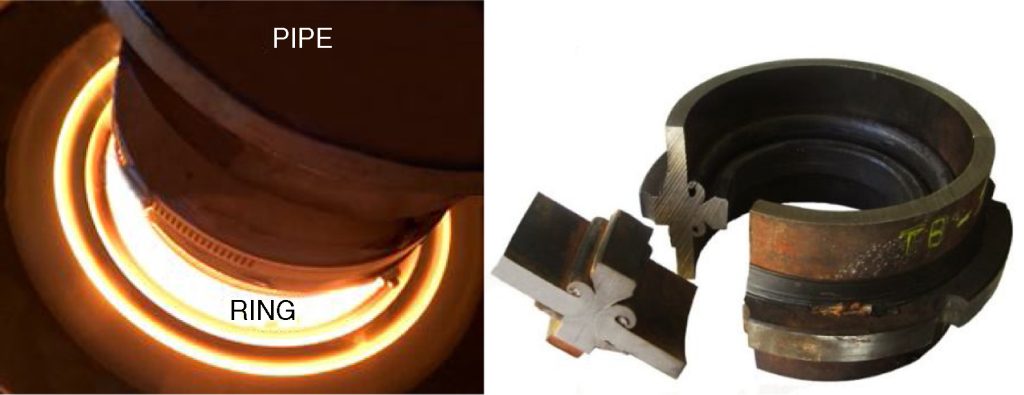
È interessante notare come la zona che diventa incandescente per attrito è estremamente ridotta, assicurando allo stesso tempo una minima Zona Termicamente Alterata. Questo approccio impedisce, ad esempio, la crescita del grano in tipologie di acciai speciali, come quelli ad alta resistenza trattati termicamente. «L’interfaccia tra le due parti diventa incandescente, e il processo stesso garantisce una stabilizzazione automatica della temperatura», ci dice Inga Akulauskaite.
«Il processo è quindi autoregolante: l’aumento della plasticità del metallo dato dal riscaldamento provoca una riduzione del coefficiente di attrito, che causa a sua volta la diminuzione della produzione di calore».
Tu mi fai girar, tu mi fai girar…
La saldatura per attrito solitamente viene usata per la giunzione di pezzi a sezione circolare, o comunque dotati di simmetria di rotazione. In questa applicazione, come abbiamo visto, il pezzo viene fatto ruotare e messo a contatto con l’altra parte da unire. Questa rotazione può essere generata con due tecnologie differenti, a seconda del macchinario utilizzato.
Nella saldatura ad attrito ad azionamento diretto (chiamata anche saldatura ad attrito ad azionamento continuo) il motore di azionamento e il mandrino sono collegati. Il motore di azionamento aziona continuamente il mandrino durante le fasi di riscaldamento. Di solito si utilizza una frizione per scollegare il motore di azionamento dal mandrino e un freno per fermare il mandrino.
Nella saldatura ad attrito per inerzia, uno dei pezzi viene fissato al mandrino rotante, il quale è accoppiato ad un volano di peso determinato. Il pezzo viene quindi fatto ruotare a una velocità elevata per accumulare l’energia necessaria nel volano. Una volta che la rotazione ha raggiunto la velocità corretta, il motore viene disinnestato e i pezzi vengono forzati insieme da un cilindro idraulico.
L’energia cinetica immagazzinata nel volano rotante viene dissipata sotto forma di calore all’interfaccia di saldatura mentre la velocità del volano diminuisce. La forza viene mantenuta sui pezzi anche dopo l’arresto della rotazione, per consentire alla saldatura di consolidarsi.
Nella saldatura a vibrazione lineare i materiali vengono messi a contatto e sottoposti a pressione. Viene quindi applicata una forza di vibrazione esterna per far scivolare i pezzi l’uno rispetto all’altro, perpendicolarmente alla pressione applicata. I pezzi vengono fatti vibrare con uno spostamento relativamente piccolo, noto come ampiezza, tipicamente compreso tra 1,0 e 1,8 mm, per una frequenza di vibrazione di 200 Hz (alta frequenza), o 2-4 mm a 100 Hz (bassa frequenza), nel piano del giunto.
Questa tecnica è ampiamente utilizzata, tra l’altro, nell’industria automobilistica e soprattutto per i contatti elettrici. Una modifica minore è la saldatura a vibrazione angolare, che fa muovere i materiali con moto oscillatorio rotatorio di ampiezza pari a qualche angolo.
Applicazioni
Questa tecnica offre anche un’opportunità per unire materiali che potrebbero essere difficili da saldare con metodi convenzionali, come ad esempio le leghe di alluminio e acciaio. La sua capacità di lavorare con materiali dissimili apre nuove frontiere nell’ingegneria dei materiali, consentendo la creazione di componenti con caratteristiche specifiche e innovative. La saldatura per attrito rotante si presta a numerose applicazioni, tra cui:
- Parti di turbine a gas come: alberi di turbine, dischi di turbine, tamburi di compressori,
- Parti automobilistiche, tra cui assali e carcasse di autocarri in acciaio, valvole cave, pistoni cavi di motori, cerchioni di autovetture, convertitori per cambi automatici di autovetture,
- Turbine per motori aeronautici,
- Raccordi marini da monel ad acciaio,
- Cilindri idraulici,
- Connessioni elettriche rame-alluminio,
- Scambiatori di calore,
- Utensili da taglio,
- Tubi di perforazione per oil&gas,
- Ugelli e componenti in pressione,
- Giunti di transizione tubolari che combinano metalli dissimili (alluminio – titanio e alluminio – acciaio inox),
- applicazioni mediche e biomediche.
«Quando facciamo riferimento a questa tecnica usiamo comunemente il termine saldatura, ma si tratta di una denominazione impropria poiché il metallo non raggiunge la fase liquida. Il mancato raggiungimento del punto di fusione dei due metalli garantisce contro la formazione di pericolose aree porose e fragili, impurità, cricche e rotture. Tecnicamente, in realtà è una forma di forgiatura», precisa l’ing. Capelli.
«Grazie a questo fatto riusciamo ad ottenere una serie di vantaggi che altri metodi non consentono. In primis, non viene alterata la struttura cristallina e la dimensione dei grani del metallo, preservando le caratteristiche metallurgiche iniziali. Non c’è generalmente neanche la necessità di creare un’atmosfera inerte intorno al punto di contatto: il processo, per sua natura, protegge la zona di giunzione».
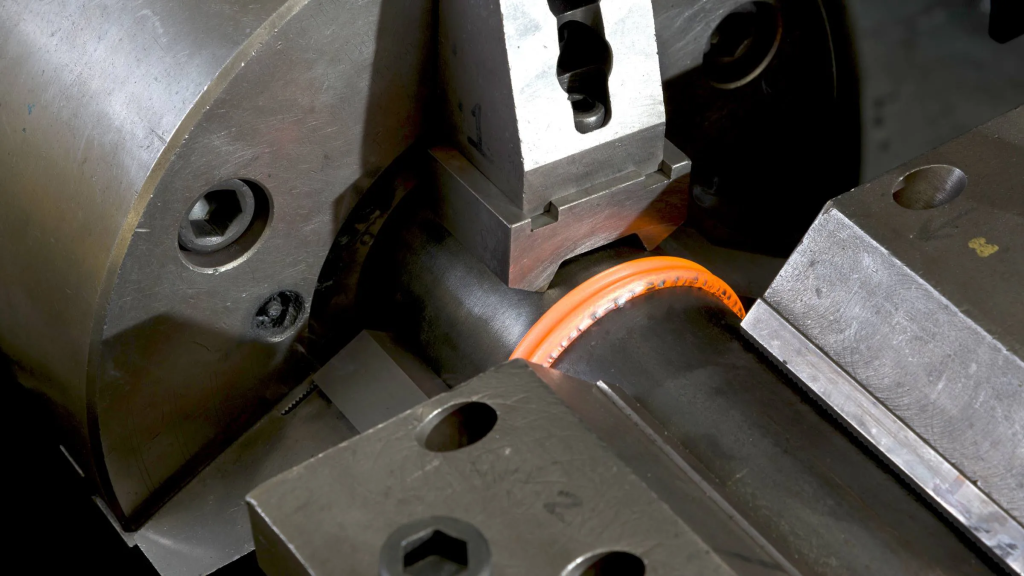
I parametri di processo
È importante notare che la saldatura per attrito a rotazione richiede un controllo preciso dei parametri di processo, come velocità di rotazione, pressione applicata e temperatura. A questo scopo sono nate macchine utensili dedicate, dotate di CNC.
Esistono inoltre metodi di simulazione numerica in grado di modellizzare e prevedere il comportamento dei pezzi e di definire i parametri da usare per una giunzione ottimale. Il metodo computerizzato degli elementi finiti (FEM) viene utilizzato per prevedere la forma del cordone e dell’interfaccia, non solo per la saldatura a frizione rotante (RFW), ma anche per la saldatura a frizione lineare (LFW).
Modifiche sostanziali nei parametri possono produrre saldature con strutture diverse, con variazioni nella larghezza, nella zona termicamente influenzata (ZTA) e nella zona plasticamente influenzata (PAZ).
I parametri di saldatura variano in base ai materiali e alle dimensioni dei pezzi coinvolti. La rotazione, solitamente tra 400 e 1450 giri/min (a volte fino a 10000 giri/min), è scelta in base al materiale e alle dimensioni. Il tempo di attrito varia da 1 a diverse decine di secondi; chiaramente anche qui i parametri possono differire notevolmente al variare delle dimensioni dei componenti. A livello di ricerca e sperimentazione, sono state raggiunte e testate anche velocità di rotazione di 25000 giri/min con tempi di forgiatura inferiori al decimo di secondo su pezzi di piccolo diametro.
I VANTAGGI PER PUNTI
Alta qualità di saldatura
- Struttura a grana fine e assenza di porosità.
- Minimo indurimento e distorsione del componente grazie all’apporto termico uniforme.
- Massima riproducibilità e tracciabilità della qualità grazie alla costanza dei parametri di saldatura.
Elevato risparmio
- Eliminazione dei materiali di consumo.
- Riduzione dei costi unitari grazie ai tempi di ciclo più brevi.
- Ottimizzazione dei componenti per un risparmio di materiale.
- Ottimizzazione dei costi attraverso la saldabilità di materiali compositi.
- L’automazione del processo non richiede personale esperto.
Altri vantaggi del processo
- Assenza di fumi e bagliore: non richiede aspirazione, schermature o DPI speciali.
- Nessuna emissione di raggi UV o campi elettromagnetici.
- Riduzione degli schizzi di saldatura.
- Minore rischio di incendio.
- Nessun uso di gas costosi o pericolosi.
Applicabilità
Come per tutte le tipologie di saldatura, anche la saldatura a rotazione per attrito comporta dei limiti di utilizzo. Se da un lato consente di unire anche metalli dissimili altrimenti incompatibili, dall’altro la generazione di fasi intermetalliche fragili può precludere questa tecnica.
La saldatura ad attrito è adatta per metalli e leghe come acciaio dolce, acciaio inossidabile austenitico e altri metalli che non reagiscono negativamente tra loro. Le caratteristiche meccaniche nella zona di saldatura influenzata dal calore non subiscono eccessive alterazioni, presentando invece una raffinazione dei grani dovuta al calore generato dall’attrito.
«Per le leghe di acciai trattati termicamente, come acciai temprabili e leghe di alluminio invecchiate artificialmente, le proprietà meccaniche possono essere influenzate dal ciclo termico durante la saldatura, ma possono essere ripristinate tramite un trattamento termico adeguato dopo la saldatura per ripristinare la duttilità, la tenacità o la resistenza a seconda delle esigenze», ci spiega Inga Akulauskaite.
«Quando si verificano combinazioni di materiali che formano leghe fragili o con strati intermetallici nell’interfaccia di saldatura, lo strato intermedio può essere generalmente controllato a uno spessore di pochi micron. Questo fenomeno si osserva, ad esempio, nella saldatura tra alluminio e rame o tra alluminio e acciaio. La giunzione risultante è eccellente e trova applicazioni in settori dove la riduzione del peso è cruciale».
Tuttavia, alcune combinazioni di materiali non producono buoni risultati. La presenza di certi costituenti, come scaglie di grafite nelle fusioni di ghisa grigia o inclusioni e porosità in altri materiali, può compromettere la qualità della saldatura. Il contenuto eccessivo di inclusioni può ridurre le proprietà meccaniche della giunzione, specialmente per quanto riguarda il ri-orientamento del flusso dei grani durante la saldatura.
E per quanto riguarda gli aspetti meccanici? Quali sono i fattori geometrici e dimensionali da tenere in considerazione? «Le tolleranze accettabili per il pezzo da saldare dipendono dalla precisione iniziale dei singoli componenti durante la preparazione per la saldatura. Se i componenti sono accuratamente lavorati prima della saldatura, è possibile ottenere un disallineamento entro 0,2 mm durante la saldatura, con un errore angolare aggiuntivo di 0,001.
Un vantaggio del processo è il mantenere l’errore nella lunghezza del pezzo saldato entro 0,3 mm rispetto a un errore complessivo dei due pezzi prima della saldatura entro i due millimetri”, continua Nunzio Capelli. “Le dimensioni delle sezioni saldabili generalmente vanno da 6 a 120 mm di diametro esterno per pezzi solidi e da 10 a 250 mm per pezzi tubolari, con un’area della sezione saldabile variabile da 10 a 20.000 mm²».
In conclusione, la saldatura per attrito a rotazione rappresenta una tecnologia innovativa che ha rivoluzionato il settore della saldatura industriale.
La sua capacità di unire materiali dissimili, ridurre la zona di fusione e garantire saldature di alta qualità la rende una scelta preferita in settori ad alta tecnologia. Con ulteriori sviluppi e raffinamenti, questa tecnica potrebbe continuare a evolversi, offrendo nuove soluzioni e applicazioni nei settori industriali più diversi.
Fonti: https://en.wikipedia.org/wiki/Rotary_friction_welding
Si ringraziano Inga Akulauskaite di KUKA e Nunzio Capelli di Scaglia srl