Descriviamo in che modo è stato progettato e costruito uno stampo progressivo per lo stampaggio a freddo di un dissipatore per schede elettroniche a elevato contenuto tecnologico.
All’interno delle automobili, specialmente quelle più evolute e moderne, possono esserci parti e componenti di piccole dimensioni, all’apparenza insignificanti, che in realtà sono veri e propri gioielli di tecnologia, e la cui ingegnerizzazione e produzione richiede il superamento di ostacoli e sfide di complessità d’ordine superiore. Al fine di proporre ai nostri lettori un esempio notevole di “pezzo sfidante”, abbiamo di recente visitato Nuova Simach, realtà che da oltre 47 anni si occupa di progettazione e costruzione di stampi e di stampaggio a freddo di particolari metallici.
Andrea Sanero, presidente e ceo della società, ci accoglie all’interno dello stabilimento produttivo di Torre Canavese (TO) con queste parole: «La nostra è una realtà in grado di realizzare piccole serie prototipali, sino alle produzioni da milioni di pezzi, per i quali occorrono naturalmente stampi di tipo progressivo, che risultano veloci e stabili a livello di processo». Per il nostro approfondimento, Sanero ci propone l’esempio di un dissipatore di calore e di corrente elettrica per schede elettroniche montate su vari modelli Porsche. «Si tratta – spiega – di un particolare ottenuto da una striscia di ottone pre argentato piegata innumerevoli volte e con tolleranze estremamente strette. Noi lo chiamiamo “ragnetto” per la sua forma molto particolare, per la quale sembra avere tante zampe».
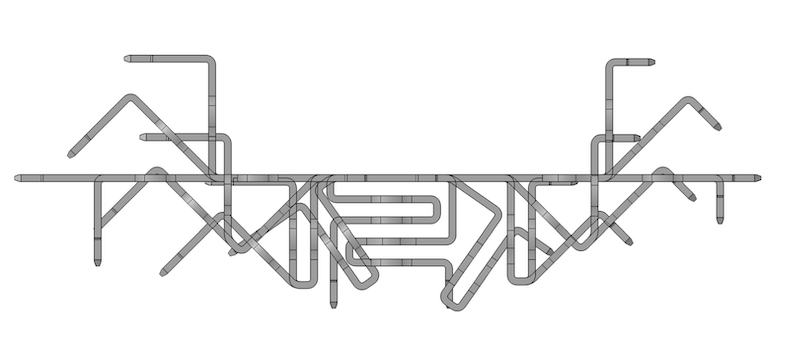
Una vera e propria sfida
Porsche propose all’azienda piemontese la propria idea, presentando una bozza del pezzo da realizzare sulla base delle proprie necessità funzionali, in particolare per la dissipazione di calore e di corrente elettrica nei circuiti elettronici delle proprie vetture. Danilo Battuello, project manager, e in questo caso anche progettista, dell’officina piemontese, entra nel dettaglio: «Il pezzo era veramente difficile da ingegnerizzare, in quanto il cliente richiedeva tolleranze dell’ordine del decimo di millimetro, non facili da assicurare a causa delle tante pieghe e dei relativi ritorni elastici del metallo. Inizialmente nutrivamo dubbi circa la fattibilità del pezzo; poi capimmo che potevano trovare una strada la giusta e accettammo la sfida».
L’ufficio tecnico di Nuova Simach è dotato di 5 terminali CAD/CAM, che dispongono del pacchetto Visi di Vero Solutions, e di stazioni che, attraverso il software Stampack, permettono di effettuare calcoli e simulazioni 3D molto accurate di tranciature e imbutiture profonde molto complesse. «In questo caso – riprende Battuello – ci affidammo alla nostra esperienza maturata in oltre vent’anni di lavoro senza il contributo della simulazione. Considerammo il tipo di materiale da lavorare, in particolare la durezza, i raggi e lo “strisciamento” delle pieghe e numerosi altri fattori, fino a definire completamente la geometria finale del pezzo, il numero e i tipi di pieghe da eseguire». Nuova Simach fornì al cliente diversi prototipi, con materiali e trattamenti diversi, in modo potesse verificare la reazione del “ragnetto” alla saldatura sulla scheda elettronica e la sua capacità dissipativa; quindi, una volta ricevuto il benestare definitivo di Porsche, fu avviato definitivamente lo sviluppo dell’attrezzatura.
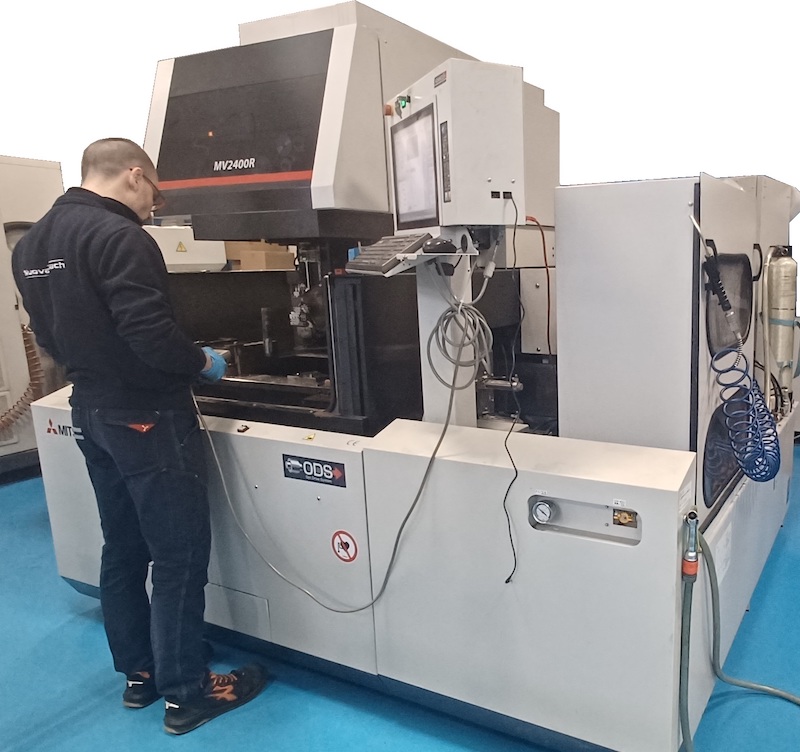
25 passaggi in uno stampo solo
Quello in esame è uno stampo progressivo molto complesso e di notevole lunghezza. Battuello: «Lo stampo è lungo all’incirca 2200mm, il che è davvero un dato rilevante considerando che il pezzo finale, cioè il dissipatore, ha un volume pari a un cubo di circa 1 cm di lato». Tale sviluppo in lunghezza spiega la complicazione del pezzo, in quanto ogni fase, che sia una piega, una tranciatura, una regolazione, necessita di spazio aggiuntivo all’interno dell’attrezzatura. In totale, lo stampo prevede 25 passaggi, grazie ai quali il nastro laminato in ottone pre-argentato, diviene “ragnetto”. La difficoltà nel progettare uno stampo progressivo del genere, che è composto complessivamente da 2.799 parti solide, è quella di prevedere tutti i passaggi in maniera sequenziale e coordinata senza creare incastri indesiderati o interferenze, senza dimenticare che l’ottone argentato è un materiale ostico da lavorare ad alto coefficiente di attrito e a rischio esfoliazione dell’argentatura. Battuello: «In totale, dallo studio del metodo all’ultimazione della progettazione dello stampo richiesero più di alcune centinaia di ore di lavoro: ogni passaggio fu valutato e ponderato in ogni aspetto, perché sbagliare un dettaglio significava buttare giorni di lavoro e ricominciare da capo. Tra gli aspetti più ostici da risolvere vi era quello di determinare il materiale e il trattamento termico superficiale delle lamelle, spesse 1 mm, che si inseriscono in opportune feritoie dello stampo e che vengono azionate automaticamente con leverismi ad ogni piega da realizzare. Il rischio era quello di scegliere materiali troppo o poco tenaci, quindi di innescare rotture o piegamenti indesiderati».
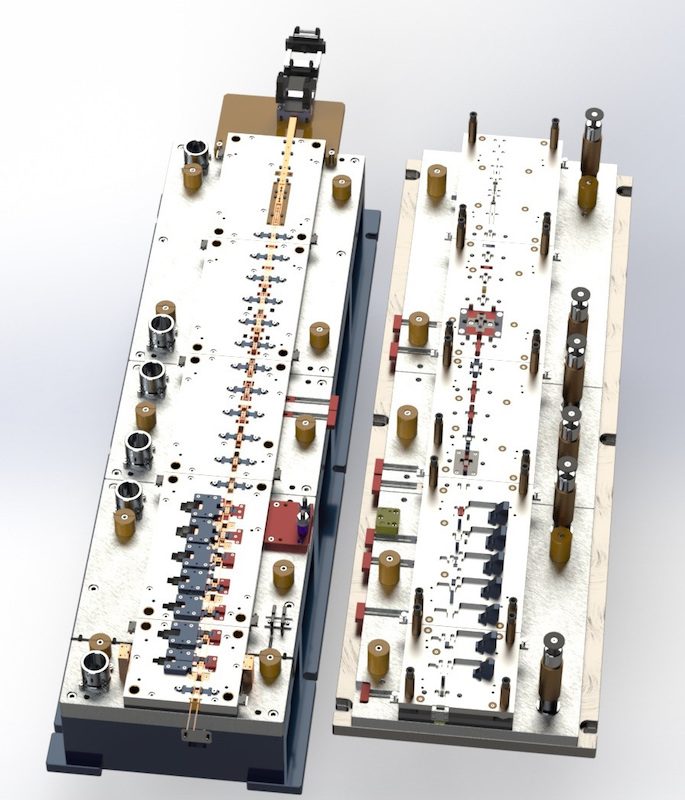
Tolleranze del centesimo
In attrezzeria, Nuova Simach dispone di macchine all’ avanguardia, fra cui diversi centri di lavoro a controllo numerico a 3 e a 4 assi, di cui uno appena installato della Hurco, oltre a macchine di elettroerosione a tuffo e a filo, l’ultima delle quali, di marca Mitsubishi, della massima precisione; completano la gamma una microforatrice CNC e macchine più tradizionali. Danilo Battuello: «Anche la costruzione richiese molto impegno, dato che lo stampo, realizzato con materiali di pregio e molto costosi, necessita di precisione dell’ordine del centesimo di millimetro. Per raggiungere tale risultato, il 90% delle lavorazioni fu eseguito sulla nostra macchina d’elettroerosione a filo Mitsubishi». Dopo circa due mesi per la definizione del pezzo e per la progettazione dello stampo, e altri quattro per la sua costruzione e assemblaggio, l’attrezzatura passò al reparto stampaggio per l’avviamento della produzione.
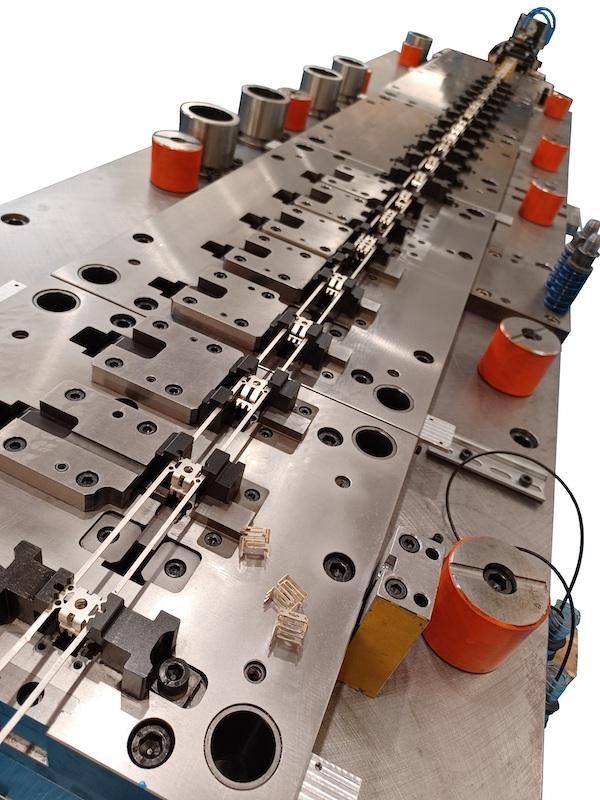
Stampaggio da nastro
Il reparto di stampaggio è dotato di 1 pressa idraulica da 200 tonnellate e 35 presse meccaniche da 16 a 400 tonnellate, di marche quali Benelli, Bruderer, Sapre Costruzioni, San Giacomo, tutte collegate con il sistema gestionale aziendale al fine di monitorare la produzione in tempo reale, come è chiesto a una vera Industria 4.0. Per quel che riguarda il dissipatore in esame, «la regolazione sotto pressa dello stampo non durò più di tre giorni, a dimostrazione del fatto che lo stesso era stato ben progettato e perfettamente realizzato. Inoltre, l’aver previsto una regolazione indipendente per ogni piega permette di intervenire puntualmente senza la necessità di smontare l’intero stampo: tale scelta accelerò senz’altro i tempi di messa in produzione, così come oggi sveltisce le operazioni di manutenzione». Occorre aggiungere che per stampare il pezzo, viste le dimensioni e lo spessore, sarebbe bastata una pressa da circa 50 tonnellate, ma per contenere uno stampo di dimensioni così rilevanti, i responsabili di Nuova Simach ricorsero a una pressa Pressix della Sapre Costruzioni da 400 tonnellate. Tale pressa, che nel caso in questione riesce a mantenere una cadenza di 40 colpi/min, viene alimentata automaticamente da nastro, previo passaggio attraverso una calandra; tale nastro, prima di entrare nello stampo, viene assistito da un ulteriore alimentatore, al fine di rendere più stabile e preciso l’intero processo.
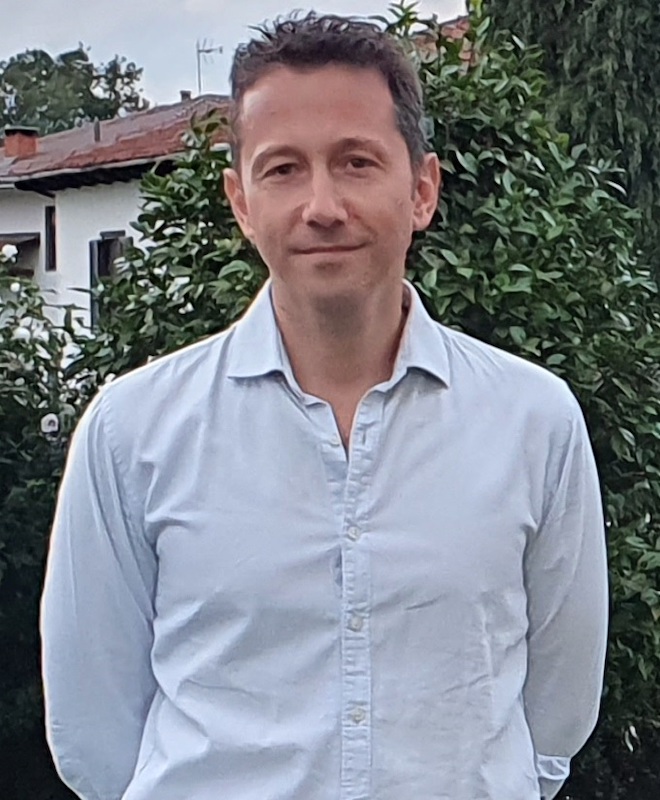
Massima soddisfazione
Lo stampo è in produzione da ottobre 2023 con una cadenza produttiva di circa 70.000 pezzi/mese. La soddisfazione di Porsche, che ha potuto constatare la qualità del risultato finale, decisamente maggiore in termini di tolleranze, funzionalità e affidabilità, rispetto ad analoghi manufatti realizzati in Paesi come la Cina, è davvero elevatissima. Andrea Sanero conclude: «Quando decidemmo di accettare la commessa tra i nostri tecnici aleggiava un po’ di tensione: si trattava di uno dei pezzi più ostici mai ingegnerizzati dalla nostra impresa in tanti anni di storia, e sapevamo che altre aziende avevano rinunciato. Arrivare al risultato prefissato, individuando per il cliente la soluzione migliore sia dal punto funzionale sia economica, è stato per noi realmente gratificante».
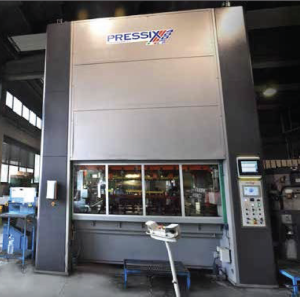
Stampi trancia e stampaggio a freddo
Nuova Simach (Torre Canavese, TO), attiva dal 1977 nello sviluppo di stampi e di stampaggio a freddo di particolari metalli, lavora con clienti italiani ed esteri di rilevanza internazionale principalmente nel settore automotive, ma opera anche in altri ambiti, come quello aerospaziale, elettronico/informatico, degli elettrodomestici… L’azienda, che attualmente si avvale di 70 dipendenti, assiste il cliente nelle fasi di ingegnerizzazione dei pezzi da produrre, suggerendo soluzioni e tecnologie tali da assicurare non solo la massima qualità possibile, ma anche risparmi in termini di tempi, di materiali e manutenzione. Nuova Simach dispone di un ufficio tecnico con software evoluti, di un’attrezzeria con macchine di ultima generazione, e un reparto stampaggio in cui vengono lavorati metalli di varia natura (acciaio, acciaio inox, rame), leghe (bronzo, ottone, alpacca) e composti speciali quali trimetalli, alpacca ecc., con spessore da 0,07 mm a 6 mm. In supporto allo stampaggio, l’attività dispone anche di macchine per la saldatura laser, per la rasatura, per il lavaggio, l’asciugatura e l’imballaggio sotto vuoto dei particolari stampati; senza dimenticare il reparto metrologico che opera a valle delle lavorazioni meccaniche e della produzione.
Uno sguardo all’automotive
Andrea Sanero ci offre il suo punto con riguardo al settore automotive, comparto in cui Nuova Simach è attiva per il 60% del proprio fatturato: «In questa fase, “l’ambito delle macchine sportive di lusso è tra quelli più in salute, mentre il settore delle auto “tradizionali” cioè delle vetture a motore termico, è in lento ma progressivo rallentamento. I motori termici vengono costantemente rimpiazzati da motori elettrici o ibridi, e oggi i prodotti più richiesti sono per l’appunto quelli che permettono la cosiddetta mobilità ibrida: parliamo di schermi, connessioni, barre flessibili… Di recente, inoltre, sono in discussione i primi prototipi di veicoli con motori a idrogeno, che sono un’applicazione molto interessante per il futuro. In generale, è questa una fase transitoria in cui occorre differenziare i settori di sbocco; occorre cioè guardare anche oltre l’automotive per mantenere l’azienda in crescita».
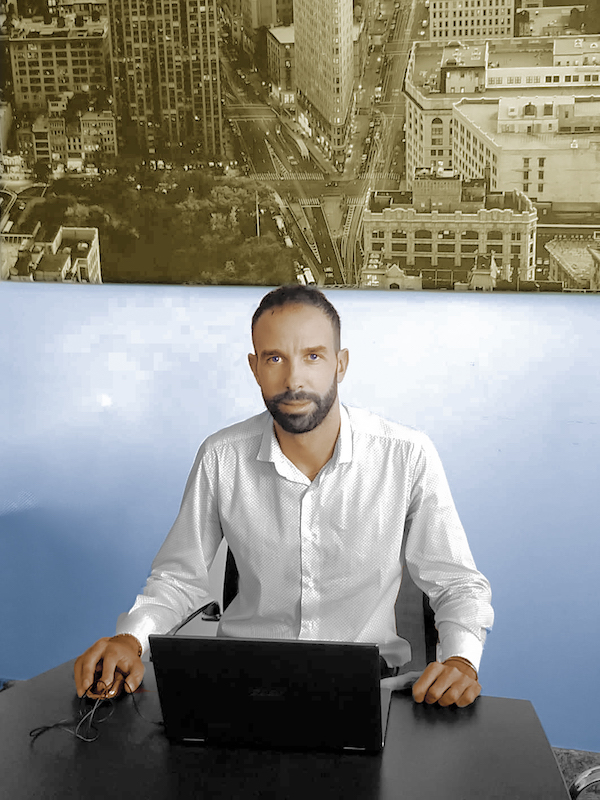
Stampo: carta d’identità
Pezzo stampato: dissipatore di calore/corrente elettrica di schede elettroniche
Cliente: Porsche
Dimensioni pezzo stampato: 14,6x11x15,1 mm
Materiale pezzo stampato: ottone (CuZn37 R410) argentato (Ni+Ag)
Costruttore stampo e stampatore: Nuova Simach, Torre Canavese, Strada Preie n.7 (TO)
Stampo: progressivo Cx1
Dimensioni e peso stampo: 2200x700x525 mm; 3.007 kg
Tonnellaggio stampo: 50 t
Larghezza striscia: 20 mm
Passo striscia: 88 mm
N. passi stampo: 25
Numero di pieghe/regolazioni + passi trancia: 18 + 5
Solidi disegnati all’interno dello stampo: 2.799
Parti attive di piega/trancia: 169
Numero di normalizzati: 653
Tempo sviluppo e costruzione stampo: 2 + 4 mesi
Stampaggio: su una pressa Pressix di Sapre Costruzioni da 400 t
Produttività: 50.000 pezzi/mese
Vittorio Pesce