L’innovazione tecnologica ha portato notevoli cambiamenti durante gli ultimi anni nell’industria manifatturiera. L’introduzione di nuove tecnologie e l’evoluzione delle metodologie produttive hanno permesso di compiere passi da gigante.
Ora gli ausili informatici hanno preso un ruolo sempre più centrale, rivoluzionando anche i processi tradizionali ed offrendo nuove frontiere dal punto di vista dell’efficienza e della qualità dei prodotti finali. Tra le nuove possibilità in crescente diffusione, risulta particolarmente interessante la simulazione di processo.
Si tratta di software avanzati che, tramite complesse equazioni matematiche per modellare il processo produttivo, sono in grado di ricreare virtualmente il procedimento, così da simulare il risultato finale ed analizzare nel dettaglio tutte le fasi. Il mondo della ricerca è al lavoro per approfondire queste tematiche ed offrire interessanti spunti al supporto di innovazione e miglioramento continuo.
Friction Stir Welding
Il Friction Stir Welding (solitamente abbreviato come “FSW”) è un tipo di unione allo stato solido che permette di saldare grazie all’attrito senza raggiungere la temperatura di fusione (Figura 1). Si tratta di una tecnologia emergente dal basso impatto ambientale.
La saldatura viene creata da un utensile cilindrico che ruotando genera attrito, e quindi calore, così da plasticizzare il materiale e da unire i due metalli. Contestualmente alla rotazione, l’utensile viene movimentato trasversalmente per ottenere un cordone di saldatura. Il processo è composto da quattro fasi: avvicinamento, penetrazione, avanzamento e fuoriuscita.
I vantaggi di questa soluzione sono diversi: ridotte tensioni residue, deformazioni e porosità. Questo processo è infatti apprezzato per le leghe di alluminio: difficilmente saldabili con altre tecniche, ma può essere utilizzato su un’ampia varietà di materiali (e.g. acciaio, leghe di titanio, leghe di magnesio, …). Visti i numerosi vantaggi questa tecnica viene spesso applicata in campo aerospaziale, ma non solo.
Uno dei parametri principali per questo processo è la forza che agisce sull’utensile cilindrico durante la saldatura. Questo parametro, a differenza di altri come, ad esempio, la velocità di rotazione, di spostamento o la profondità dell’utensile è meno approfondito dallo studio della ricerca. La maggior parte dei macchinari per Friction Stir Welding infatti sono specifici ed hanno una sufficiente rigidità.
Tuttavia, la tecnica di unione “FSW” permette di ridurre costi ed aumentare la produttività, ed è quindi d’interesse per l’applicazione su robot industriali. Il problema sorge poiché questi robot sono solitamente meno rigidi e con capacità di carico limitate rispetto a macchinari dedicati. Inoltre, è importante conoscere le forze anche per determinare correttamente gli altri parametri di processo a seconda del materiale e dello spessore di lavoro.
Misurare le forze
Negli scorsi anni sono stati effettuati diversi sforzi per misurare le forze durante il processo “FSW”. La ricerca ha proposto principalmente due diverse metodologie: la prima è quella sperimentale, mentre l’alternativa si basa su simulazioni numeriche. La prima opzione utilizza sensori di forza direttamente applicati sul macchinario per riuscire a monitorare questo parametro in tempo reale. Questa soluzione permette di ottenere un’elevata precisione, ma aumenta significativamente i costi.
L’alternativa economica è quella di sfruttare simulazioni numeriche in grado di ottenere una stima, potenzialmente anche accurata, del processo. Queste simulazioni virtuali possono a loro volta essere di tipo termo-meccanico o semi-analitico. La prima opzione risulta la più diffusa, nonché semplice, per ottenere le forze desiderate. L’alternativa invece combina la metodologia analitica con i software ad elementi finiti per offrire un risultato di buona accuratezza.
Nonostante gli sforzi dei ricercatori entrambe le soluzioni attualmente disponibili offrono svantaggi importanti. Da una parte i maggiori costi per sensorizzare il macchinario e dall’altro i tempi computazionali che possono arrivare anche a diverse settimane. Per questo gli autori della ricerca propongono una nuova metodologia semi-analitica basata sulle temperature di lavorazione. In questo modo è possibile istallare termocoppie che, tramite un processo inverso ed una simulazione permettono di stimare le forze di processo.
Approccio semi-analitico
Il processo proposto dagli autori è di tipo inverso (rappresentato in Figura 2) composto da tre fasi. Si inizia disponendo diverse termocoppie nel componente per registrare i cicli termici durante la sperimentazione di Friction Stir Welding. Nella seconda fase viene effettuata una serie di simulazioni numeriche ipotizzando diversi flussi termici.
La terza fase è quella di confronto tra la simulazione e i risultati sperimentali nei punti di temperature di picco per identificare i parametri della simulazione più vicini al reale. Avendo determinato la simulazione che meglio approssima il processo reale è possibile sfruttare il modello teorico per stimare le forze agenti sull’utensile durante l’unione. Questa metodologia è economica, grazie all’utilizzo di comuni termocoppie, ed anche efficiente dal punto di vista computazionale dato che evita l’adozione di modelli più complessi.
Validazione sperimentale
Una sperimentazione dedicata è stata creata per validare la nuova metodologia proposta. Come materiale è stato utilizzato una lamiera in lega di alluminio AA6061-T6 delle dimensioni di 200 x 100 x 6 mm. Un macchinario dedicato è stato utilizzato per la saldatura (Figura 3), aggiungendo sia i sensori di forza (per confronto), che le termocoppie.
La simulazione numerica è stata effettuata sul software ABAQUS. Il confronto tra le misure delle termocoppie e la simulazione ottimale è ridotto e consistente. Questo significa che la deviazione tra reale e simulato è minima (nell’ordine di qualche punto percentuale) e i risultati sono confrontabili in diversi punti. Anche la stima della forza sull’utensile risulta essere buona, soprattutto quando il processo è a regime. L’accuratezza di questa metodologia permette di offrire interessanti valori da utilizzare come guida per la progettazione di macchinari, fissaggi dei componenti da lavorare e utensili.
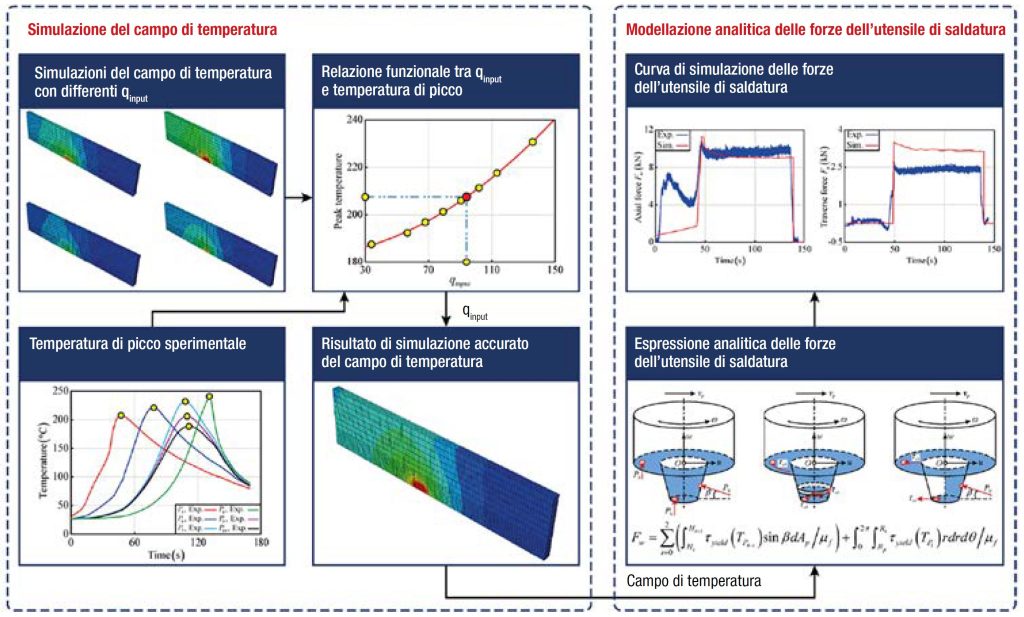
La sperimentazione è infatti in grado di confermare la validità dell’approccio proposto per la simulazione, introducendo un grande potenziale per lo sviluppo della tecnologia di unione Friction Stir Welding.
L’approccio sistematico ed innovativo proposto dai ricercatori cinesi offre un interessante spunto di riflessione riguardo alle potenzialità delle nuove tecnologie digitali nel mondo industriale. Le simulazioni numeriche sono strumenti eccezionali che, grazie alla sempre crescente potenza computazionale, possono godere di una notevole diffusione e sviluppo.
Tuttavia questi strumenti devono essere correttamente sfruttati per lavorare vicino ai processi industriali, così da ottenere risultati affidabili e prossimi alla realtà. L’abbinamento di approccio sperimentale e di simulazione permette infatti di ottenere risultati più veritieri ed affidabili, riducendo il ricorso a modelli complessi o a computazioni eccessivamente onerose.
Importante quindi sfruttare le innovazioni tecnologiche e il mondo virtuale delle simulazioni, ma senza distaccarsi dal contesto reale ed industriale che è poi l’obiettivo e l’applicazione finale delle simulazioni. Risulta quindi interessante poter apprezzare esempi dal mondo della ricerca di come reale e virtuale possano collaborare ad una vera e propria evoluzione tecnologica.
Fonte: Yue, W., Liu, H., Meng, S., Xiao, J., & Huang, T. (2023). An Approach for Predicting the Tool Forces in Friction Stir Welding of AA6061-T6 Aluminium Alloy. The International Journal of Advanced Manufacturing Technology, 126(9-12), 5289-5305. https://doi.org/10.1007/s00170-023-11474-2