Il rapido aumento della produzione di veicoli a trazione elettrica ha cambiato lo scenario nel settore degli ingranaggi; nuove macchine, utensili sempre più sofisticati e software innovativi si fanno largo, ma la rettifica degli ingranaggi rimane sempre attuale.
Già da molti anni è iniziata una lenta ma inarrestabile trasformazione dei processi produttivi degli ingranaggi per il settore automobilistico e, più in generale, per ogni tipo di trasmissione.
Questa evoluzione ha interessato la meccanica, l’elettronica, e i software, spinta dall’esigenza, sempre più sentita, di rumorosità il più possibile ridotta, ed efficienze sempre maggiori.
Naturalmente si parla di ingranaggi sempre più precisi, con errori di elica e di profilo ridotti oramai all’ordine del micrometro.
Una buona trasmissione, specie per l’auto a trazione elettrica che deve essere molto silenziosa, richiede ingranaggi rettificati con tecniche molto sofisticate.
Oramai per questi ingranaggi non è più attuabile la finitura con la rasatura, che è un’operazione eseguita sul “tenero”, cioè prima del trattamento termico che inevitabilmente deforma in qualche misura i denti dell’ingranaggio.
La sostituzione della rasatura con la rettifica comporta una maggiorazione dei costi: macchine più costose, tempi ciclo più lunghi, rulli ravvivatori con alti prezzi di acquisto ecc.
Quindi, in parallelo con il perfezionamento dei mezzi produttivi si assiste ora anche a una modifica della tecnologia per ridurre i costi di produzione.
Si sono attuati perciò sviluppi sulle mole abrasive, sugli oli da taglio, sui rulli diamantati e anche sulla struttura delle linee di produzione e introdotti software più sofisticati.
Mole abrasive
Una buona parte dei miglioramenti dell’operazione di rettifica degli ingranaggi è dovuta al progressivo sviluppo delle mole abrasive. Bisogna distinguere intanto il sistema di rettifica, cioè se si tratta di rettifica per generazione con mola a vite o di rettifica di forma.
Nel primo caso si usano generalmente mole in ceramica che attualmente possono essere costruite con abrasivi sinterizzati che permettono di controllare la dimensione del grano e una distribuzione uniforme dei grani nel corpo della mola.
In questo modo si può gestire meglio la porosità ottimizzandola per facilitare lo scarico dei trucioli. Inoltre i grani di abrasivo vengono agglomerati con speciali leganti ceramici che aumentano l’efficienza della mola. I grani con dimensione costante permettono inoltre di aumentare la durata della capacità di taglio e quindi di ridurre il numero di ravvivature a vantaggio del tempo ciclo.
Nella rettifica per generazione con mole a vite, si possono utilizzare mole con un numero di principi molto alto, anche fino a 7, e di accoppiare in uno stesso mandrino mole con specifiche diverse per sgrossatura e finitura in uno stesso ciclo (fig. 2).
Nel caso di rettifica degli ingranaggi con il metodo di forma le mole hanno un profilo che corrisponde al profilo del vano tra i denti dell’ingranaggio. L’abrasivo dipende dall’entità dei lotti che si devono rettificare.
Se i lotti non sono molto grandi si preferisce un abrasivo ceramico, mentre se si tratta di rettificare grandi produzioni si usano mole al CBN. Queste mole infatti non richiedono frequenti ravvivature e quindi il tempo di rettifica è minore e inoltre si ha una maggior uniformità della qualità degli ingranaggi rettificati.
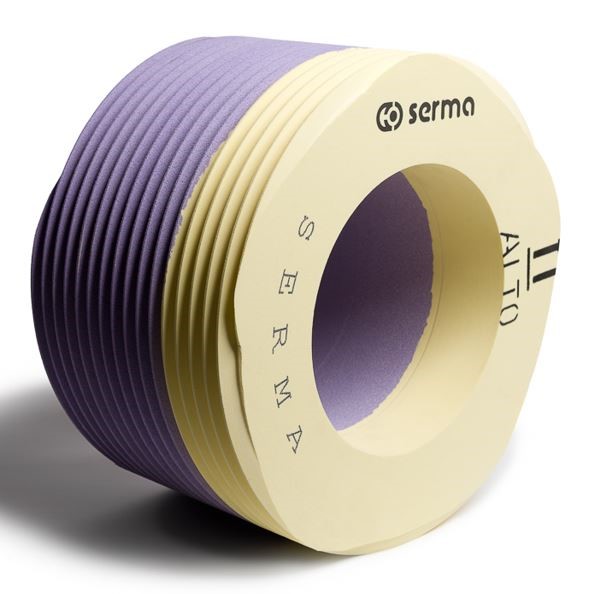
Rulli diamantati
La precisione della mola abrasiva e della sua efficienza dipende prevalentemente dal modo come viene profilata e da come viene ravvivata. Oggi i rulli diamantati che si usano per queste operazioni hanno raggiunto un grado di perfezionamento molto alto.
I rulli della nuova generazione sono costruiti con una tecnica rivoluzionaria che accresce in maniera notevole la precisione della ravvivatura e la vita del rullo stesso riducendo in modo sensibile i costi dell’operazione di rettifica (fig. 3).
I diamanti sintetici, che hanno una dimensione uniforme, vengono posizionati sul corpo con un robot secondo un programma ben definito gestito dal controllo numerico.
I diamanti sono posizionati sul profilo in modo da garantire una perfetta bilanciatura durante il lavoro e un’omogenea distribuzione dello sforzo di ravvivatura della mola.
La distribuzione dei diamanti segue una traiettoria elicoidale scaricata che permette il ripristino della taglienza della mola senza renderla liscia, evitando quindi possibili surriscaldamenti localizzati.
I diamanti vengono saldati sul corpo con un processo particolare che permette ai diamanti di sporgere per oltre il 50% dalla superficie del corpo senza per questo perdere la stabilità del fissaggio. Questa particolarità aumenta almeno del doppio la vita del rullo.
Infine la deposizione elicoidale viene lappata in modo da garantire la perfetta forma del profilo e valori di rugosità che si stabilizzano sotto Rz 3,5 che è il parametro richiesto dalle nuove tecnologie sviluppate per le auto elettriche.
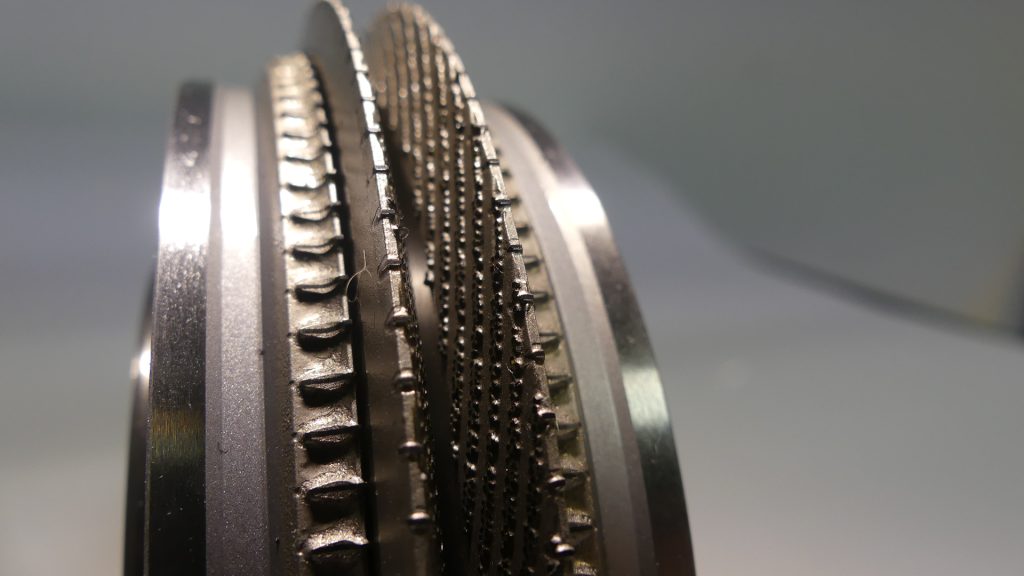
Lubrorefrigeranti
Nella costruzione degli ingranaggi si usano diverse macchine operatrici collegate a volte tra loro formando delle linee di produzione che, nelle realtà più moderne funzionano senza quasi l’intervento dell’operatore. Alcune macchine usano certi tipi di lubrorefrigeranti e altre usano liquidi diversi.
Ogni olio da taglio ha lo scopo di ottimizzare il rendimento della macchina in cui viene usato.
Per esempio i moderni lubrorefrigeranti per l’operazione di dentatura con creatore o con il coltello stozzatore sono basati sugli esteri vegetali che hanno innumerevoli vantaggi rispetto agli oli minerali.
In primo luogo sono biodegradabili e quindi evitano le sempre più rigorose e più costose norme cui gli oli minerali devono rispettare.
In secondo luogo, permettono condizioni di lavoro più spinte in quanto hanno un punto di infiammabilità più alto e un’azione lubrificante maggiore grazie alle molecole polari, che formano un velo lubrificante molto resistente nella zona di contatto tra la faccia tagliente e truciolo.
Nella operazione di rettifica invece si usano oli minerali con bassa viscosità che facilitano la pulizia nella zona di lavoro asportando velocemente i trucioli e i residui di abrasivo.
Inoltre asportano più velocemente il calore sviluppato durante l’operazione.
Anche questi oli da taglio hanno una formulazione particolare che impedisce la formazione di schiume e limita la fumosità. Una delle condizioni principali per ottenere delle superfici rettificate di ottima qualità è il tipo di filtraggio installato nella macchina rettificatrice.
Oggi le macchine moderne usano filtri che asportano dall’olio usato le particelle fino a dimensioni di qualche micrometro, a tutto vantaggio della qualità della superficie rettificata.
Macchine rettificatrici
Oggi moltissimi produttori di rettificatrici propongono dei modelli che possono rettificare con i due metodi, per generazione con mola a vite e con mola di forma. Questa soluzione permette di ottimizzare i tempi ciclo sfruttando le principali caratteristiche dei due sistemi e di avere alla fine precisioni maggiori sia sul profilo che sull’elica.
Molte macchine hanno strutture con cemento polimerico che è composto da un agglomerato minerale unito da un legante che lo rende molto stabile e resistente. Ha un eccellente smorzamento delle vibrazioni ed è termicamente stabile.
Un altro materiale per basamenti di macchine utensili è composto costituito da un insieme di graniti di differenti granulometrie selezionate, legati da resina epossidica e da un reagente.
Le macchine con struttura in acciaio o in ghisa, pur essendo molto rigide, sono soggette a deformazioni dovute a differenze di temperatura nelle varie aree. Anche per questo una rettifica degli ingranaggi di qualità deve avere il controllo della temperatura del lubrorefrigerante.
Le macchine moderne hanno anche speciali mandrini supportati da cuscinetti in ceramica che risentono meno delle variazioni di temperatura e riducono eventuali vibrazioni.
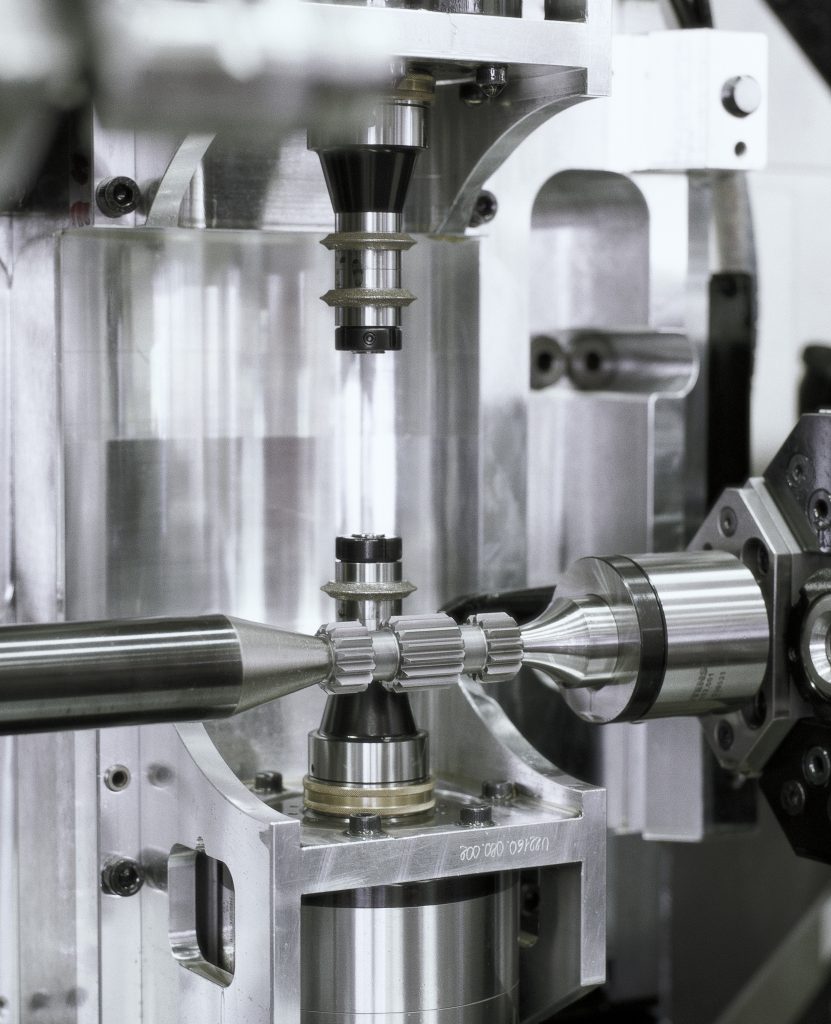
Uno dei problemi delle rettifiche per generazione con mole a vite è la difficoltà di lavorare ingranaggi “sotto battuta” cioè vicini a rasamenti o ad altri ingranaggi. È problematico usare mole a vite di piccolo diametro e in genere si usano mole di forma sia in ceramica sia in CBN (fig. 4).
Allo scopo di ridurre il tempo ciclo, nelle linee più moderne le rettificatrici hanno due stazioni di cui una è utilizzata per il carico e scarico degli ingranaggi da rettificare durante la fase di rettifica. Si tratta di un carico e scarico in “tempo mascherato”, cioè che non incide sul tempo ciclo.