Giunti di trasmissione: criteri per la selezione, ottimizzazione e applicazioni in ambito industriale
I giunti sono componenti meccanici fondamentali, utilizzati nella maggior parte dei casi per il collegamento di due alberi. Nei sistemi di trasmissione l’utilizzo dei giunti è assai comune ed interessa diversi tipi di collegamento.
Le applicazioni industriali utilizzano regolarmente giunti rigidi e flessibili per il trasferimento della coppia da un albero all’altro. In particolare, i giunti rigidi forniscono una solida connessione tra alberi, garantendo estrema precisione ed il trasferimento di coppie elevate. Tuttavia, i giunti rigidi non sono adatti per compensare i disallineamenti durante il funzionamento. Non consentono quindi alcun movimento tra i due alberi e necessitano periodicamente di lubrificazione. Di conseguenza, per garantire un buon rendimento ed evitare dissipazioni e possibili rotture nell’installazione, non assorbendo le vibrazioni, entrambi gli alberi devono essere perfettamente allineati.
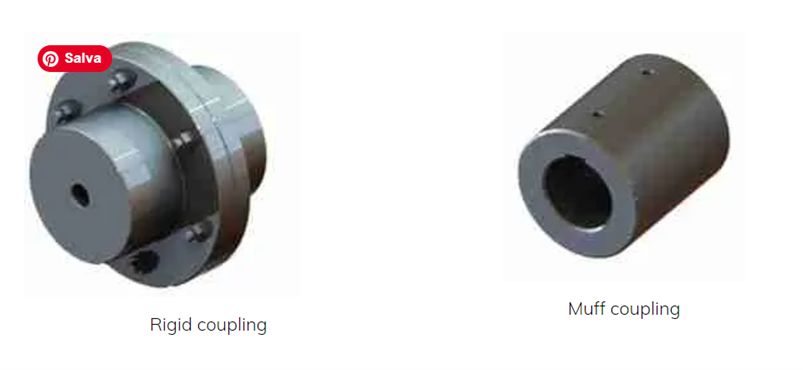
Semplici ed economici, i giunti rigidi sono disponibili in molteplici varianti costruttive che li rendono specifici per l’applicazione prevista. In figura 1 un esempio di alcune tipologie di accoppiamento rigido.
I giunti flessibili hanno un principio di funzionamento simile ai giunti rigidi, trasmettendo la coppia da un albero all’altro in modo che entrambi gli alberi si muovano all’unisono. La differenza principale è che i giunti flessibili compensano i disallineamenti, i movimenti circonferenziali relativi e gli angoli di flessione. In genere il disallineamento tra due alberi può raggiungere un valore massimo di 5° in direzione angolare, anche se sono disponibili diversi giunti in grado di gestire più disallineamenti in una combinazione di direzioni. I giunti flessibili sono decisamente consigliati in caso di avviamenti rapidi per compensare gli scompensi sugli alberi causati dalle inerzie dei componenti della trasmissione in rotazione. In generale, se confrontati con i giunti rigidi, questi forniscono un trasferimento di coppia minore, ma attenuano in modo significativo i picchi di carico dovuti a irregolarità di coppia, urti o vibrazioni.
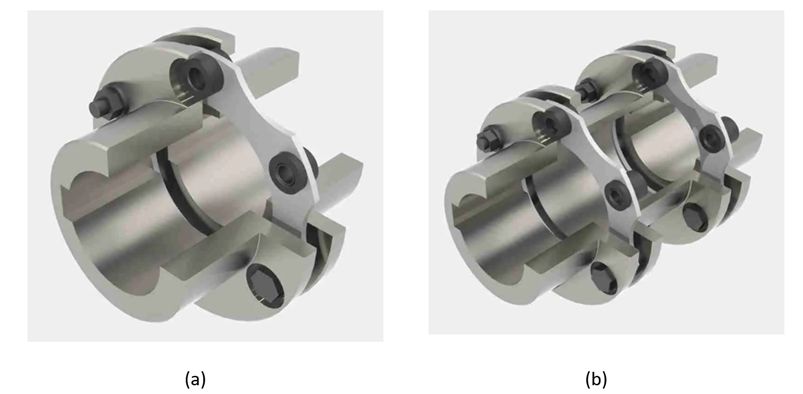
Rispetto alla coppia trasmissibile, è possibile comunque ottenere un ampio range di valori ammessi a seconda della tipologia di giunto: maggiore per i giunti flessibili metallici, minore per quelli con elementi flessibili polimerici. In figura 2 alcuni esempi di giunti flessibili metallici, in figura 3 alcuni giunti flessibili con elemento elastico polimerico.
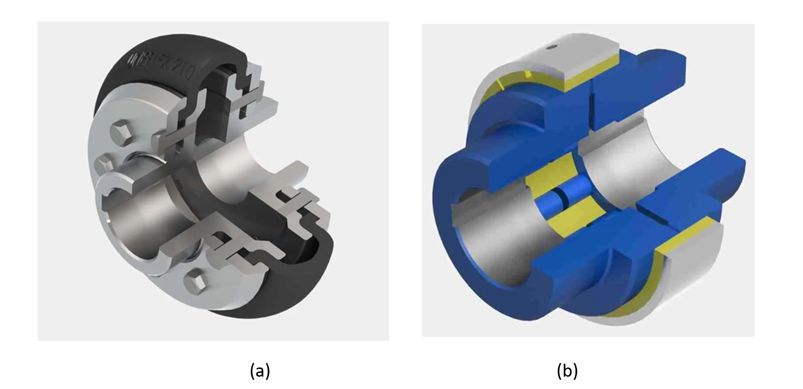
Siccome sono disponibili moltissime tipologie di giunto per la trasmissione di potenza, e considerando che ogni applicazione ha le proprie specifiche di progetto, è indispensabile conoscere, analizzare e verificare i requisiti richiesti al giunto per garantire una sua lunga durata in esercizio e un buon funzionamento del sistema. Si riporta di seguito una serie di aspetti da considerare nel processo di selezione di un giunto:
- Dimensionamento di base: rispettare i requisiti della geometria del giunto in relazione al tipo di alberi, al loro diametro e lunghezza. Alcune tipologie di giunti sono disponibili solo per alcune dimensioni di montaggio ed esistono tolleranze ottimali e limiti dimensionali per un corretto funzionamento. Verificare la massima coppia trasmissibile e la compatibilità del giunto.
- Requisiti ambientali: analizzare l’area, la temperatura alla quale sarà esposto il giunto, la presenza o meno di ambiente corrosivo.
- Accessibilità: lo spazio necessario per l’installazione potrebbe rappresentare un problema in fase di posizionamento e allineamento del giunto. In fase di progetto è bene considerare uno spazio aggiuntivo per queste operazioni, oltre all’ingombro fisico del giunto.
- Analisi del disallineamento: in presenza di un disallineamento tra gli alberi è necessario comprenderne la tipologia per scegliere correttamente il giunto, verificandone la componente predominante (torsionale, assiale, flessionale), la periodicità nel tempo e l’entità.
- Prestazioni desiderate: occorre comprendere e definire quali prestazioni devono essere ottimizzate nell’accoppiamento come, ad esempio, coppia elevata, velocità elevata, ripetibilità, livello di flessibilità, assorbimento e dissipazione, etc. La velocità di rotazione, ad esempio, è un parametro molto importante da considerare perché al crescere di questo valore alcuni giunti potrebbero non funzionare con la stessa efficienza che possiedono a basse velocità, a parità di coppia. Se il sistema richiede invece uno smorzamento delle vibrazioni durante il trasferimento di potenza attraverso gli alberi, occorre selezionare un sistema di accoppiamento adeguato per questo scopo. In generale, i giunti flessibili sono i più efficaci nello smorzamento delle vibrazioni, proporzionalmente al coefficiente di attrito dell’elemento flessibile interno.
- Costo a lungo termine: è bene considerare, oltre al costo del giunto e della sua installazione, anche i costi di manutenzione periodica. Fra questi sono da includere i costi per la lubrificazione, da eseguire in modo rigoroso.
Integrazione di giunti in sistemi complessi
Di seguito proponiamo una panoramica di alcune applicazioni industriali significative che utilizzano giunti rigidi o flessibili.
Accoppiamento rigido
- Macchine rotanti ad alta velocità:come turbine, pompe ad alta velocità e compressori, che richiedono in tutte le fasi di esercizio un costante e preciso allineamento, per evitare vibrazioni che potrebbero impedire il regolare funzionamento.
- Lavorazione CNC di precisione: le macchine a controllo numerico (CNC) utilizzano accoppiamenti rigidi per garantire precisione e ridotti giochi o disallineamenti, entrambi requisiti necessari nelle operazioni di taglio, fresatura e tornitura.
- Robotica e automazione: macchinari automatizzati e sistemi robotici utilizzano accoppiamenti rigidi per un controllo preciso del movimento e la sincronizzazione tra più assi.
- Sistemi di trasmissione di potenza: le applicazioni di trasmissione di potenza per carichi pesanti utilizzano giunti rigidi per il trasferimento di coppie elevate nei casi di collegamento tra alberi perfettamente allineati.
Accoppiamento flessibile
- Apparecchiature azionate da motori elettrici: i motori elettrici sono dotati di giunti flessibili per il collegamento a pompe, compressori, ventilatori ed altre apparecchiature per ridurre al minimo il trasferimento di vibrazioni dal motore stesso ai componenti fluidodinamici e per assorbire le coppie di spunto.
- Industria automobilistica: le trasmissioni e i sistemi di sospensione utilizzano giunti flessibili per ridurre al minimo le vibrazioni e gestire eventuali disallineamenti causati dai movimenti del motore.
- Sistemi HVAC (Heating, Ventilation & Air Conditioning): i sistemi HVAC utilizzano giunti flessibili per collegare i motori a sistemi di ventilazione ed altre apparecchiature, per ovviare a problemi simili a quelli citati nel primo punto.
- Applicazioni marine e offshore: i sistemi di propulsione marina, gli impianti di perforazione offshore e le attrezzature “ship-to-shore” utilizzano giunti flessibili per gestire i disallineamenti provocati dai movimenti della nave.
Re-design di giunti mediante additive manufacturing
Una delle basi tecnologiche che ruotano intorno al concetto di fabbrica intelligente, negli impianti di produzione, è l’utilizzo combinato di reverse engineering e produzione additiva (AM) per riprogettare e costruire parti di ricambio danneggiate. Tra queste troviamo senz’altro anche i giunti flessibili. In questo caso l’utilità della riproduzione, in alternativa all’acquisto del nuovo componente, si manifesta in caso di giunti speciali con lunghi tempi di approvvigionamento, in caso di urgenza di ripristinare l’impianto, in caso di sede operativa difficilmente raggiungibile, o altri motivi analoghi.
L’oggetto di partenza in questo caso è il componente originale, ad esempio un giunto in elastomero poliuretanico (TPU) prodotto mediante stampaggio a iniezione. Analizzando le sue dimensioni e proprietà, è possibile condurre uno studio di fattibilità riguardo la possibilità di riprodurlo mediante una tecnica di fabbricazione additiva.
Il primo passo per il reengineering di un componente industriale di questo tipo, o di altri, consiste nel selezionare i materiali ed il processo di produzione additiva migliore tra quelli esistenti. Si possono utilizzare per questo appositi database che contengono le proprietà dei materiali, la loro processabilità con determinate tecniche additive e le specifiche attese per il componente finale, come ad esempio rugosità superficiale, tolleranze dimensionali, tensioni limite di snervamento o rottura. La procedura per la selezione consiste in generale nei seguenti passaggi:
- analisi dei processi di fabbricazione additiva idonei;
- valutazione della fattibilità del componente sulla base delle caratteristiche del processo, delle macchine utilizzabili, delle dimensioni massime stampabili e dei materiali;
- scelta finale del materiale, del processo, degli eventuali trattamenti post-processo e analisi dei costi correlati, anche influenzati dal numero di parti da produrre.
Per ottenere un giunto flessibile, occorre tener conto dei seguenti requisiti: elevata resistenza a trazione e torsione, resistenza al taglio, flessibilità, resistenza alle sostanze chimiche e agli agenti esterni (umidità e condizioni operative comprese tra −40 °C e 80 °C). Inoltre, il materiale deve essere idoneo alla stampa 3D.
Nell’esempio citato in precedenza, per la riproduzione in additive manufacturing del giunto polimerico, è possibile utilizzare un processo di Fused Filament Fabrication (FFF) con poliuretano termoplastico (TPU). Nel passaggio successivo si esegue un modello 3D compatibile con la tecnica AM selezionata, come ad esempio quello rappresentato in figura 4 realizzato da Baladés et al. [Baladés et al.]. Il modello CAD può essere esteso ad un modello FEM (basato sul metodo degli elementi finiti) per il calcolo delle sollecitazioni e delle deformazioni in esercizio.
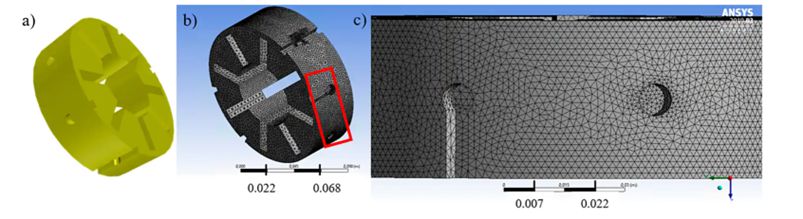
È necessario prevedere nel design alcuni dettagli per supportare la stampa:
- sono introdotte idonee strutture di supporto per consentire la stampa delle parti sospese o a sbalzo;
- viene modificato il riempimento del componente per controllarne densità e rigidezza, ad esempio utilizzando strutture reticolari apposite. Nel caso specifico, ad esempio, sono stati utilizzati due parametri di riempimento, rispettivamente al 60% e 80%. Lo spessore della parete è di 2 mm. Il materiale utilizzato è denominato FilaFlex™ con filamento da estrudere nella stampante avente diametro di 1.75 mm.
La quantità di materiale e di vuoti all’interno del componente sono parametri controllati dalla percentuale di riempimento. Parametri di processo come lo spessore dello strato, la percentuale di riempimento e la velocità di stampa influenzano la qualità finale del componente stampato e il suo comportamento meccanico. Allo stesso modo, la densità di riempimento dovrebbe essere compresa tra il 60 e il 100% per sostenere le massime sollecitazioni per quel dato materiale. In figura 5 il giunto stampato in 3D al 60% di riempimento.
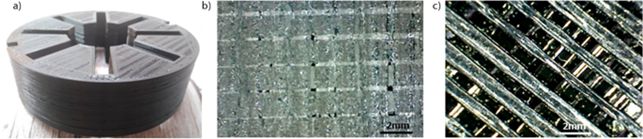
Dopo la stampa, le proprietà meccaniche dei prototipi possono essere confrontate con quelle del componente originale, mediante prove di compressione statica e ciclica.
I prototipi devono rispettare i requisiti prestazionali stabiliti e, a tal fine, sono eseguite:
- analisi dei requisiti geometrici a partire dalla scheda tecnica e dalle rilevazioni delle dimensioni del componente originale;
- prove specifiche per misurare le proprietà dei materiali;
- simulazioni statiche come metodo di validazione mediante analisi agli elementi finiti (FEM);
- eventuale ottimizzazione topologica tramite software dedicati (come nTopology o altri);
- eco-audit per conoscere e confrontare il consumo energetico e l’impronta di carbonio del ciclo di vita di ciascun componente, originale e prodotto mediante produzione additiva, in un’ottica di produzione sostenibile.
Analizzando questi due ultimi punti, per ottenere una distribuzione ottimale del materiale all’interno del componente, è possibile adottare un approccio di progettazione generativa. La riprogettazione guidata dalla simulazione consente di modificare la densità del materiale in aree critiche in cui le sollecitazioni sono maggiori, per aumentare la rigidezza e ridurre tensioni e deformazioni (figura 6).
Apportando questo tipo di ottimizzazione si piò conseguire una riduzione dei pesi significativa rispetto ai componenti originali, fino al 15-20% senza comprometterne le funzionalità. La riduzione dei pesi non è solo funzionale all’applicazione ma soprattutto alla riduzione dei tempi e dei costi di stampa. Alle condizioni operative attuali, i prototipi stampati in 3D sembrano essere una valida alternativa rispetto ai componenti originali.
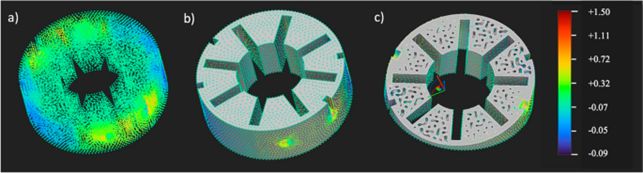
Figura 6. (a) Campo scalare di sollecitazione (MPa) ottenuto con FEA. (b) Campo scalare allineato al componente. (c) Densità di riempimento ottimizzata del componente. Fonte: [Baladés, N. et al]
Un eco-audit, eseguito ad esempio mediante il software ANSYS Granta Edupack, può stimare il consumo energetico e l’impronta di carbonio del ciclo di vita dei giunti: mentre il consumo di energia e le emissioni di anidride carbonica nella fase di utilizzo erano simili sia nei componenti originali che riprogettati, in fase di produzione si può osservare un risparmio di energia del 74% (con riempimento di stampa all’80%) e del 76% (con riempimento di stampa al 60%). La stessa percentuale è stata ottenuta nelle riduzioni delle emissioni di CO2. I giunti stampati in 3D contribuiscono ad una riduzione delle emissioni di CO2 del 4% (nell’accoppiamento con il 60% di riempimento) e del 7% (nell’accoppiamento con l’80% di riempimento) nel loro ciclo di vita totale.
Giunti intelligenti per la fabbrica del futuro
La sensorizzazione dei componenti soddisfa appieno i requisiti dettati dalla digitalizzazione, dall’automazione e dall’Industrial Internet of Things (IIoT). Soluzioni intelligenti sono oggi in grado di generare e trasmettere informazioni essenziali per lo svolgimento efficiente del processo produttivo, in un’ottica di ottimizzazione delle risorse, condition monitoring del componente, sia in condizioni operative che per le esigenze di manutenzione predittiva ordinaria e straordinaria, per la diagnostica e la manutenzione.
L’azienda R+W, in risposta alla crescente domanda di componenti intelligenti, ha progettato la tecnologia di azionamento AIC (Artificial intelligence Coupling – figura 7).
Nata per soddisfare la richiesta di componenti in grado di auto-monitorarsi e di monitorare il funzionamento della macchina, dalla manutenzione a un controllo delle prestazioni in tempo reale, oggi la tecnologia AIC è applicata a una gamma sempre più ampia di giunti. Grazie alla sensoristica integrata nel giunto stesso, è possibile rilevare alcuni parametri di esercizio (come temperatura, coppia, vibrazioni, velocità di rotazione, accelerazioni sui tre assi, spinte assiali, etc.). In questo modo è possibile registrare e prevedere le condizioni operative ed eventuali sovraccarichi.
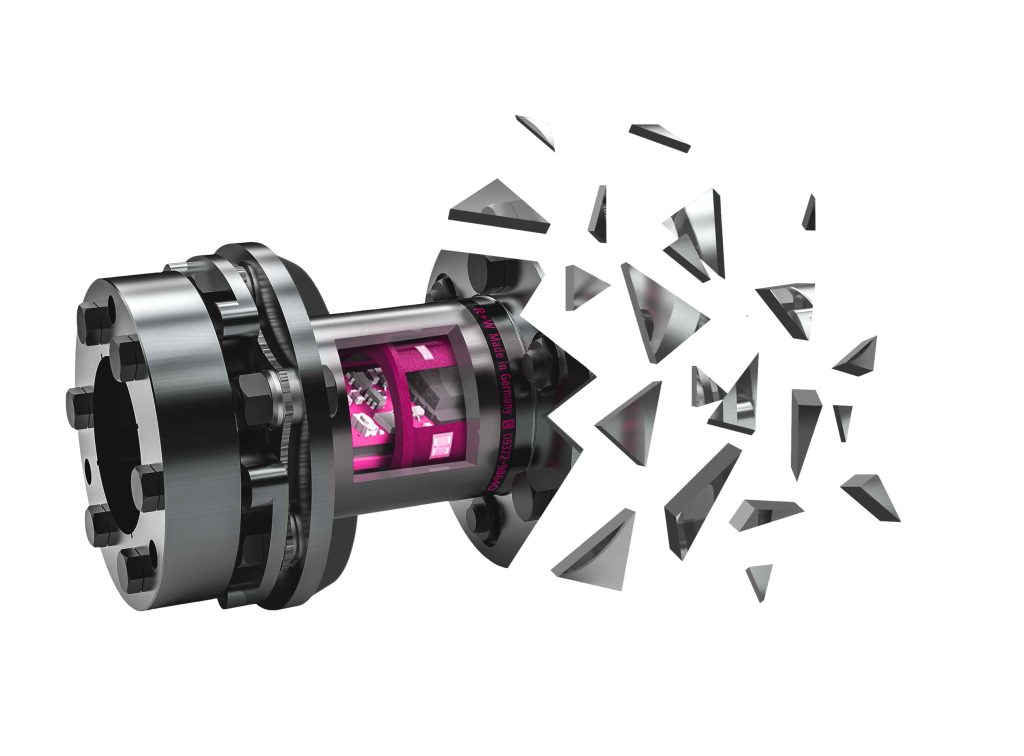
L’acquisizione di dati precisi sulle prestazioni direttamente all’interno della linea di trasmissione fornisce informazioni utili e preziose per la realizzazione di macchine sempre più efficienti, precise ed in grado di controllarsi in tempo reale per prevedere e prevenire eventuali guasti che andrebbero a impattare negativamente sulla produttività.
Diverse opzioni di alimentazione (batteria ricaricabile integrata, induzione, recupero dell’energia cinetica associata alla rotazione) rendono il giunto intelligente estremamente versatile. Inoltre, può essere integrato in un giunto esistente, senza la necessità di ulteriore spazio di installazione né costruzioni ausiliarie, con facile retrofit del sensore negli accoppiamenti preinstallati.
Conclusioni e scenari futuri
I giunti sono dispositivi meccanici impiegati per la connessione di due alberi. Consentono il trasferimento di potenza e coppia, garantendo un funzionamento senza interruzioni per varie applicazioni industriali. Progettati per compensare il disallineamento, ridurre le vibrazioni e prevenire danni, i giunti hanno un ruolo chiave nel garantire il buon funzionamento e l’efficienza di macchinari e attrezzature, risultando componenti essenziali in svariati settori: dall’automobilistico e aerospaziale all’industria petrolifera, del gas e manifatturiera. A seconda della specifica applicazione, sono disponibili diverse tipologie di giunti, ciascuno con le proprie caratteristiche uniche, tra cui si ricordano i giunti dentati, a disco, a griglia, a ganascia ed elastomerici. Il mercato dei giunti industriali è in rapida evoluzione tecnologica per la crescente domanda di efficienza ed affidabilità in svariati settori. Progressi tecnologici nella progettazione, nei processi di produzione e nei materiali, che consentono un prolungamento della durata di vita utile dei giunti ed un miglioramento in termini di affidabilità e prestazioni, sono fattori trainanti. Si pensi ai giunti flessibili, che consentono una compensazione del disallineamento e una maggiore durata. Inoltre, l’adozione dei principi dell’industria 4.0 e la crescente automazione nei processi industriali sta favorendo l’espansione della domanda di componenti affidabili e ad alta precisione, per garantire una trasmissione efficiente e continua di potenza e coppia nei macchinari automatizzati, al fine di migliorare la produttività e ridurre al minimo i tempi di fermo macchina e le relative conseguenze negative di un monitoraggio inadeguato. L’efficienza energetica e la sostenibilità ambientale sono oggi obiettivi cruciali per le industrie di tutto il mondo. In quest’ottica, è incoraggiata l’adozione di giunti con caratteristiche avanzate, come il basso attrito e la trasmissione di potenza ottimizzata, in grado di minimizzare le perdite di energia e migliorare l’efficienza complessiva. Infine, oggi il mercato si sta muovendo verso soluzioni alleggerite e compatte, per soddisfare i requisiti dei moderni macchinari. Si stima che nel prossimo futuro le principali evoluzioni nei giunti riguarderanno:
- design alleggeriti e compatti per dare spazio alle necessità di efficienza, riduzione di ingombro e riduzione del peso di macchinari e sistemi;
- crescente personalizzazione: soluzioni di accoppiamento su misura per applicazioni e requisiti industriali specifici;
- sostenibilità: le imprese stanno riducendo la loro impronta di carbonio e sono alla continua ricerca di soluzioni, tecnologie e materiali a basso impatto ambientale;
- integrazione di tecnologie intelligenti nei giunti, come soluzioni sensorizzate per il condition monitoring, la manutenzione predittiva e la diagnostica remota.
Giorgio De Pasquale, Dipartimento di Ingegneria Meccanica e Aerospaziale, Politecnico di Torino, Smart Structures and Systems Lab