Perché l’integrazione dei robot e delle tecnologie avanzate nei contesti industriali rappresenta una soluzione innovativa e promettente per ottimizzare i processi interni e migliorare la sicurezza e la qualità del lavoro, eliminando attività ripetitive e faticose.
Oggi stiamo assistendo ad un’epoca di notevole trasformazione digitale e tecnologica nell’ambito dell’intralogistica, dove si sta sempre più diffondendo l’adozione di sistemi automatizzati per la gestione dei materiali all’interno degli stabilimenti produttivi.
L’integrazione di nuovi sistemi automatici nei processi aziendali ha il potenziale di rivoluzionare l’efficienza, la produttività e la sicurezza nell’ambito della logistica di magazzino e di produzione.
Nei contesti industriali, le operazioni richiedono la movimentazione tra diverse aree di oggetti caratterizzati da peso e dimensioni variabili e la gestione dinamica di variabili come spazi di stoccaggio e percorsi di trasporto.
L’evoluzione delle richieste del mercato, caratterizzata da una domanda sempre più diversificata e personalizzata da parte dei consumatori, evidenzia l’importanza crescente e le complessità sia nei processi di produzione che di distribuzione dei prodotti.
I produttori si stanno concentrando sulla riduzione dei lotti, sulla consegna diretta ai consumatori, sulla personalizzazione avanzata dei prodotti e sulla diminuzione dei tempi di ciclo. All’interno della logistica distributiva, l’obiettivo primario è migliorare la velocità e l’accuratezza delle consegne, al fine di ridurre al minimo gli errori durante il processo di prelievo.
Una mano dall’intelligenza artificiale
I robot logistici devono essere in grado di spostarsi tra luoghi diversi, trasportando oggetti di dimensioni considerevoli e affrontando condizioni mutevoli nel tempo che potrebbero ostacolare la loro navigazione. Questa necessità di flessibilità e adattabilità alle variabili esogene non rende in alcuni contesti più efficace il ricorso alla tecnologia piuttosto che all’impiego di operatori.
Tuttavia, è importante notare che negli ultimi anni, grazie al progresso nell’intelligenza artificiale e allo sviluppo di tecnologie di navigazione con visione 3D sempre più sofisticate, si è verificato un notevole aumento delle applicazioni anche nell’ambito intralogistico. Questi avanzamenti hanno contribuito a superare le sfide legate alla mobilità dei robot, consentendo loro di navigare in ambienti complessi, gestire ostacoli e adattarsi dinamicamente alle mutevoli condizioni operative.
L’implementazione di robot di ultima generazione nel campo dell’intralogistica fornisce la possibilità di gestire in modo più efficiente interi processi, permettendo un’integrazione sinergica delle attività e superando le limitazioni di spazio e aumentando l’efficienza complessiva delle attività.
L’assistenza tecnologica sta assumendo un ruolo sempre più cruciale nell’esecuzione delle operazioni manuali nell’ambito industriale, che vanno dal ricevimento delle merci allo stoccaggio dei pallet, dal prelievo dei colli e dei pezzi per l’asservimento delle linee, fino alla preparazione degli ordini di spedizione.
Nel contesto del prelievo e del trasferimento interno, i progressi tecnologici hanno giocato un ruolo fondamentale nel superare le sfide legate alla rigidità dei robot. Questi avanzamenti hanno consentito ai robot di manipolare oggetti con forme e pesi diversi, spesso troppo complessi da gestire manualmente dagli operatori. Questo ha comportato una riduzione dello sforzo richiesto agli esseri umani per queste attività, migliorando al contempo l’ergonomia e la qualità complessiva delle condizioni di lavoro.
Più sicurezza, ma non solo
Generalmente, le sfavorevoli condizioni lavorative costituiscono la causa principale dell’incremento del tasso di assenteismo nel personale. Inoltre, sono numerosi i rischi per gli operatori che possono scaturire da infortuni sul lavoro per la movimentazione di carichi pesanti e di considerevoli dimensioni da altre attività logoranti, quali il prelievo ripetuto di piccoli oggetti.
I sistemi di prelievo robotizzato risolvono le sfide legate alla disponibilità di personale, alla sicurezza e all’ergonomia degli operatori. L’implementazione di soluzioni robotiche contribuisce a ridurre i tassi di assenteismo e a contenere i costi associati al lavoro notturno.
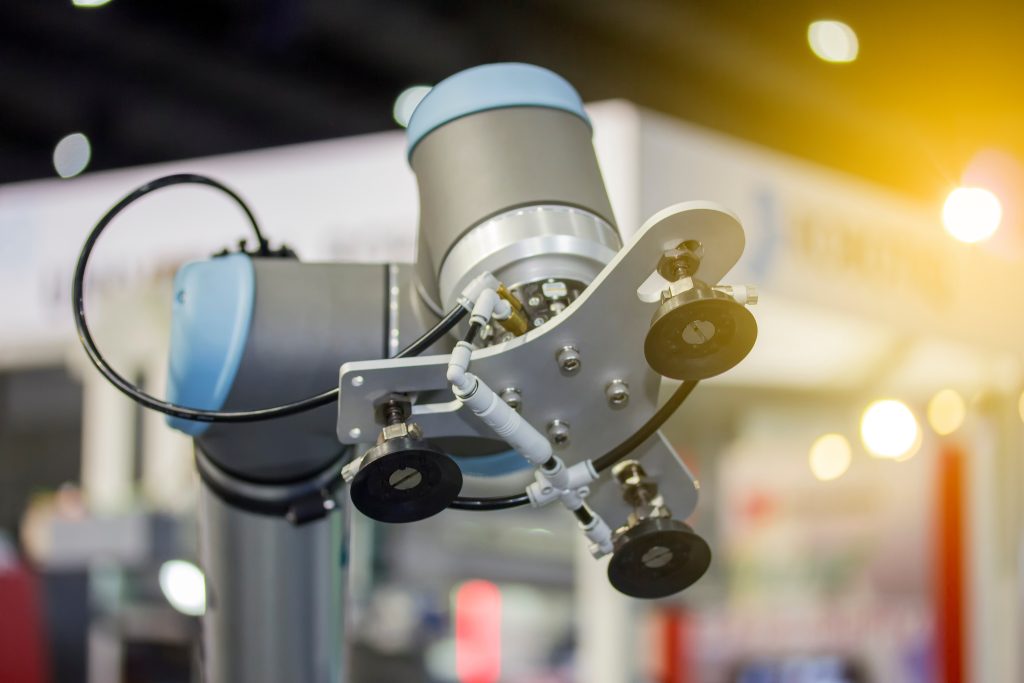
Un ulteriore elemento che richiede particolare attenzione riguarda il crescente invecchiamento della popolazione, il quale influisce direttamente sulla disponibilità di operatori capaci di svolgere compiti fisicamente impegnativi, come ad esempio la preparazione degli ordini. Il graduale abbandono di tali mansioni da parte dei lavoratori più anziani evidenzia la necessità di adottare alternative come i dispositivi di prelievo automatico, al fine di assicurare la continuità e l’efficienza delle operazioni aziendali.
La robotica può gestire compiti ed eseguire attività faticose e ripetitive mentre il personale necessita una formazione nella programmazione e nella manutenzione dei sistemi.
Tecnologie per una maggior efficienza globale
I sistemi automatici sono sempre più complessi e integrano più tecnologie dedicate a funzioni specifiche, come la gestione del carico in ingresso, lo stoccaggio, la movimentazione e il sequenziamento degli articoli destinati al processo di prelievo, come potrebbe essere un sistema AS/RS (Automatic Storage and Retrieval System).
Questi sistemi mostrano una notevole sinergia e integrazione, permettendo di ottimizzare l’efficienza globale delle operazioni logistiche, minimizzando i periodi di inattività e aumentando la precisione complessiva. L’integrazione costituisce un vantaggio significativo nell’implementazione dei robot nei processi di movimentazione. I robot possono essere agevolmente incorporati nelle tecnologie mediante il loro posizionamento in prossimità delle postazioni di picking, sostituendo così gli operatori umani. I sistemi di stoccaggio e prelievo dotati di una baia per il picking (o per l’ingresso della merce nel sistema) sono spesso predisposti per l’integrazione con un braccio robotizzato incaricato del prelievo degli articoli. Inoltre, i bracci robotizzati di dimensioni ridotte possono essere installati anche su navette AGV (Automated Guided Vehicle) o AMR (Autonomous Mobile Robot), veicoli autonomi che si spostano all’interno dello stabilimento per trasportare gli oggetti da un’area all’altra.
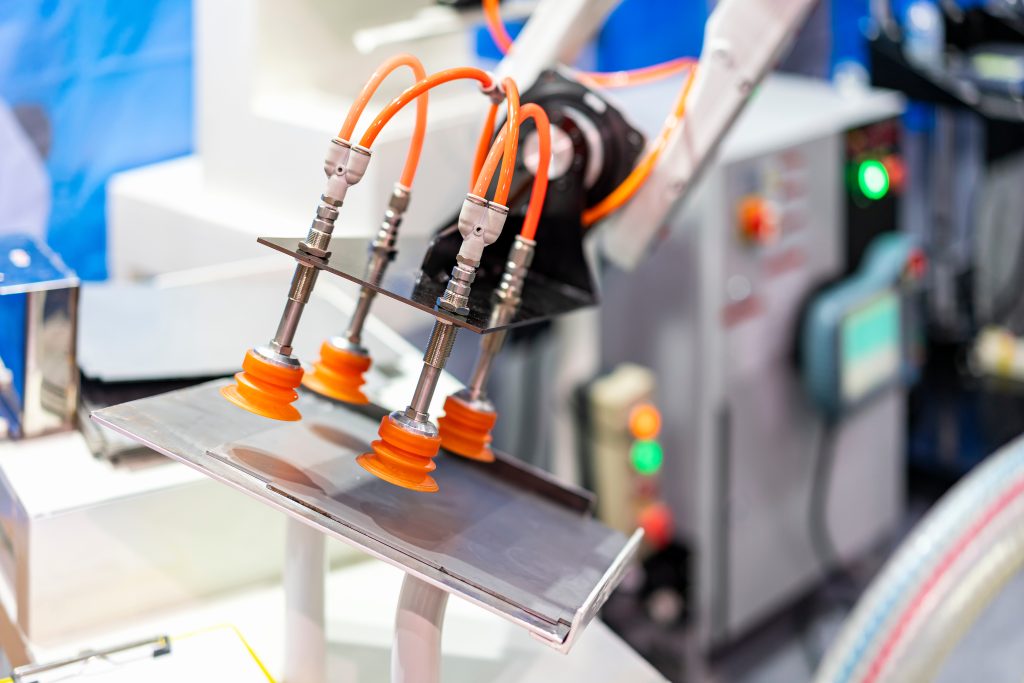
Un ulteriore beneficio derivante dall’implementazione del picking robotizzato è il miglioramento dell’efficienza operativa, che deriva dall’ottimizzazione della produttività. Questo è principalmente attribuibile all’eliminazione degli errori durante la fase di prelievo, che possono causare spedizioni errate e costi associati ai resi. I robot di ultima generazione dimostrano di essere intelligenti, ovvero sono in grado di correggere autonomamente eventuali imprevisti. Ciò permette di mantenere un flusso operativo ininterrotto, riducendo al minimo la necessità di intervento umano. Inoltre, l’integrazione dell’intelligenza artificiale nei dispositivi robotizzati facilita il processo di autoapprendimento, accumulando esperienza con ogni prelievo e adattandosi di conseguenza.
La tecnologia porta con sé vantaggi innegabili, affrontando sfide come la scarsità di manodopera e diminuendo il rischio di infortuni sul lavoro attraverso l’automazione di compiti ripetitivi e faticosi. Tuttavia, è fondamentale evidenziare che, insieme a tali vantaggi, l’adozione e la gestione di sistemi tecnologici avanzati richiedono investimenti di risorse significativi.
Per avviare e gestire con successo tali nuovi sistemi automatizzati, è necessario un team di operatori specializzati in grado di comprendere, monitorare e intervenire su tecnologie complesse come robotica, automazione, e sistemi informatici integrati. Le aziende sono chiamate ad impegnarsi nella formazione del personale o a reclutare professionisti del settore, generando così costi aggiuntivi.
L’integrazione dei robot e delle tecnologie avanzate nei contesti industriali rappresenta una soluzione innovativa e promettente per ottimizzare i processi interni e migliorare la sicurezza e la qualità del lavoro, eliminando attività ripetitive e faticose.
Automazione per una carpenteria efficiente
Nel settore della carpenteria metallica, l’evoluzione tecnologica ha conosciuto significativi progressi, con particolare attenzione alla ricerca di soluzioni innovative per automatizzare i processi logistici complessi associati alla gestione di oggetti di notevoli dimensioni, quali barre, tubi e lamiere.
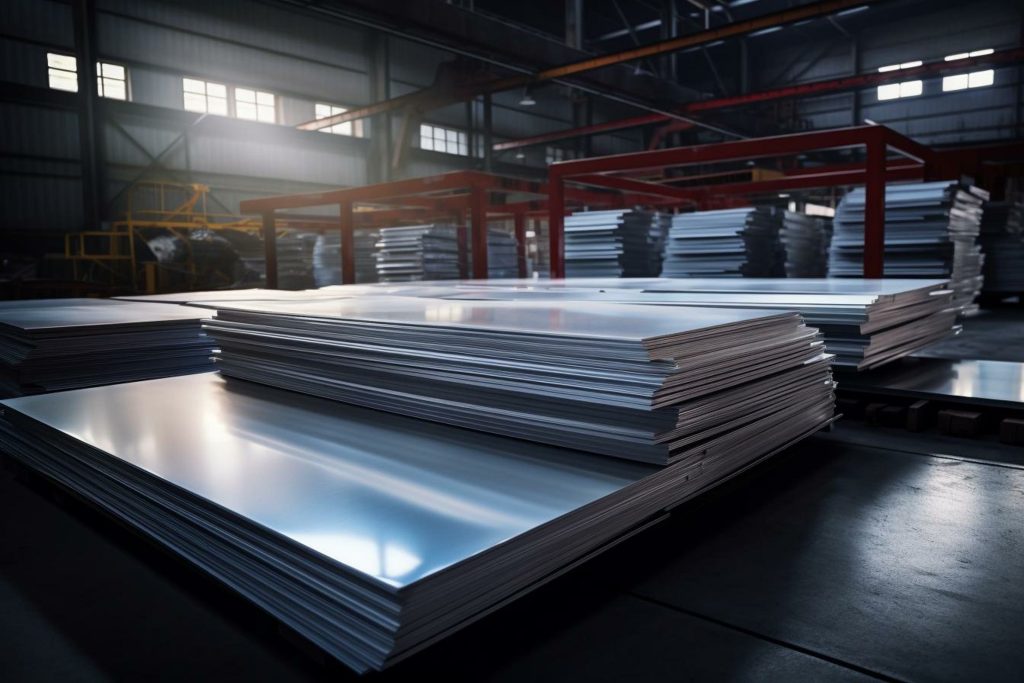
Alcune imprese del settore hanno introdotto magazzini automatici dotati di cassetti traslanti o sollevati, in grado di gestire contemporaneamente più referenze di varie dimensioni come barre, tubi o lamiere con lunghezza variabile tra i 3 e i 7 metri e un limite di peso pari a 4 tonnellate.
L’unità di stoccaggio principale di questi magazzini è il cassetto, che può essere integrato con uno o due elevatori collegati a baie di carico e scarico frontali o laterali.
A seconda delle esigenze, le baie possono essere equipaggiate con dispositivi, come carroponti o gru a bandiera, per agevolare il sollevamento degli oggetti dal cassetto, semplificando notevolmente le attività di movimentazione degli operatori.
Questi magazzini consentono di ottimizzare lo spazio e semplificare notevolmente l’attività degli operatori, grazie all’integrazione tra il sistema gestionale dell’azienda e il Warehouse Management System (WMS) della soluzione. Quando viene inserita la lista di carico nel sistema, la piattaforma del magazzino si attiva automaticamente, presentando all’operatore il cassetto contenente gli articoli richiesti.
Questo processo automatizzato riduce il rischio di errore umano e agevola notevolmente il lavoro degli operatori.
Cosa si intende per sistemi AS/RS
Un sistema AS/RS (Automated Storage and Retrieval System) è un impianto di stoccaggio e prelievo automatizzato per unità di carico di varie dimensioni (esempio: cassette, cartoni, vassoi, pallet) costituito da una serie di corridoi con scaffalature a singola o doppia profondità, all’interno dei quali operano delle macchine automatizzate in grado di eseguire contemporaneamente movimenti lungo l’asse orizzontale e lungo l’asse verticale.
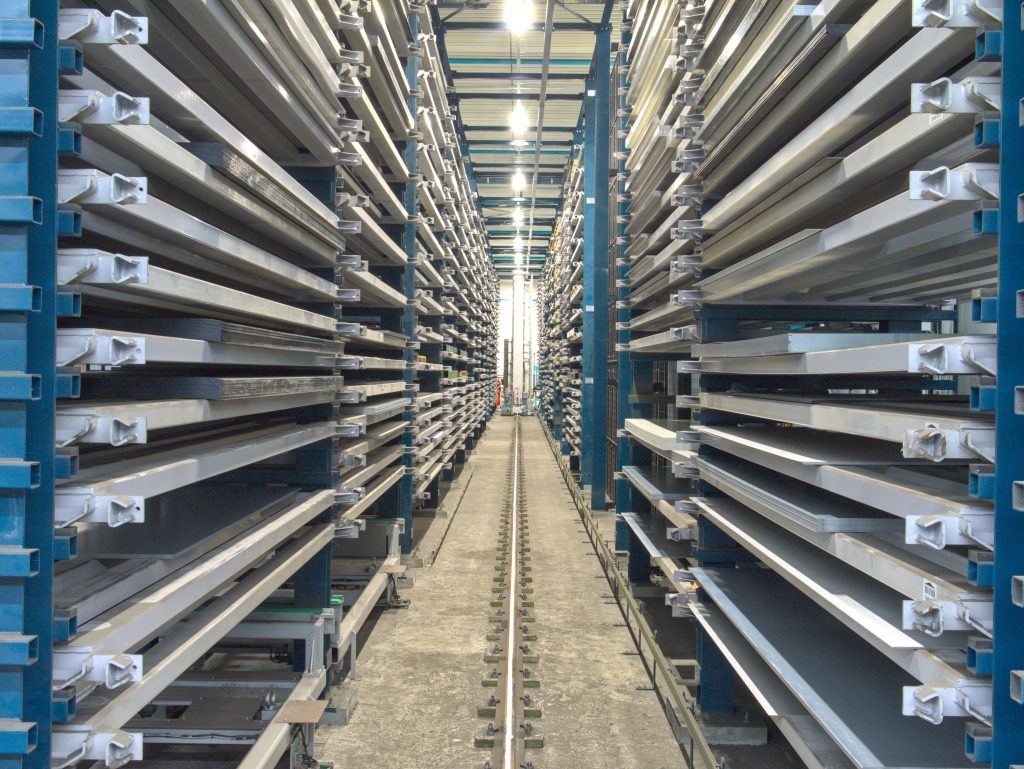
Queste macchine, non solo gestiscono il deposito delle unità di carico all’interno del sistema, ma possono anche essere integrate con stazioni di prelievo, sia manuali che automatiche, per la distribuzione delle merci immagazzinate.
In sintesi, oltre a stoccare i prodotti in entrata, queste macchine sono in grado di integrarsi con altre tecnologie per prelevare e distribuire le merci quando necessario.