Questo ampio studio teorico-sperimentale, effettuato presso l’Università di Belgrado, ha avuto l’obiettivo di esaminare il contributo dell’ottone come tipo di catodo sulla durezza e sulla resistenza al creep dei rivestimenti in rame elettrodepositati mediante corrente pulsante (“PC regime”).
di Carlo Castello
In questo regime, la corrente elettrica applicata durante il processo di deposizione viene alternata in modo periodico tra valori massimi e minimi, andando a rappresentare un metodo che può essere utilizzato per controllare con precisione le caratteristiche dei rivestimenti metallici depositati, come la loro microstruttura, durezza e altre proprietà. Al fine di comprendere meglio il ruolo del substrato, i risultati ottenuti saranno discussi e confrontati con quelli osservati di recente con rivestimenti in rame elettrodepositati nelle stesse condizioni sul substrato Si(111), che appartiene al gruppo dei substrati molto duri. Il Si(111) è un substrato di silicio cristallino con una superficie esposta lungo un piano cristallografico specifico, noto come piano (111) del reticolo cristallino del silicio. In ambito scientifico e tecnologico, il silicio cristallino viene spesso utilizzato come substrato su cui depositare strati sottili di diversi materiali o rivestimenti mediante tecniche come l’epitassia o l’elettrodeposizione. Il piano (111) del silicio ha una specifica orientazione atomica e presenta determinate proprietà di superficie che possono influenzare le caratteristiche dei materiali depositati su di esso. Pertanto, il substrato Si(111) viene utilizzato in studi e ricerche per esaminare come i materiali interagiscono con questa specifica superficie cristallina.
Sarà dedicata particolare attenzione alla determinazione del limite preciso che separa l’area con la durezza assoluta del rivestimento da quella in cui deve essere preso in considerazione il contributo della durezza del substrato. Nonostante numerose indagini relative all’analisi della durezza dei rivestimenti depositati elettroliticamente, i risultati che definiscono il valore limite che separa queste due aree non sono riportati nella letteratura tecnica, e per questo motivo verrà anche suggerito il corretto modello da utilizzare. In tal senso, i rivestimenti di rame sono stati esaminati attraverso l’applicazione di due modelli compositi di durezza: i modelli Chicot-Lesage (C-L) e Cheng-Gao (C-G). Sono stati elettrodepositati rivestimenti di rame a grana fine spessi 10, 20, 40 e 60 µm sulla superficie di ottone utilizzando un regime di corrente pulsante con una densità di corrente media di 50 mA/cm² e sono stati caratterizzati mediante microscopi elettronici a scansione (SEM), microscopi a forza atomica (AFM) e microscopi ottici (OM). Applicando il modello C-L, è stato determinato un valore limite di profondità di indentazione relativa (RID) che separa l’area della durezza del rivestimento da quella con un forte effetto del substrato sulla durezza composita misurata. I valori di durezza del rivestimento nell’intervallo da 0.9418 a 1.1399 GPa, ottenuti mediante il modello C-G, hanno confermato l’ipotesi che i rivestimenti di rame sull’ottone appartengano al sistema di durezza composita “film morbido su substrato duro”. Gli esponenti di stress ottenuti nell’intervallo da 4.35 a 7.69 sotto un carico applicato di 0.49 N hanno indicato che il meccanismo dominante di flusso plastico è la deformazione per dislocazione e il salto delle dislocazioni. Le caratteristiche meccaniche ottenute sono state confrontate con quelle ottenute recentemente sul substrato di Si(111), e gli effetti delle caratteristiche del substrato come durezza e ruvidezza sulle caratteristiche meccaniche dei rivestimenti di rame elettrodepositati sono stati discussi ed esposti. Ma entriamo un po’ più nel dettaglio dello studio.
Materiali e Metodi
Elettrodeposizione
La elettrodeposizione del rame è stata eseguita da una soluzione di 240 g/L di CuSO4·5 H2O in 60 g/L di H2SO4 a temperatura ambiente in una cella elettrochimica di forma quadrata aperta. Per il processo di elettrodeposizione, è stato applicata, come detto una corrente pulsante, onda quadra a frequenza di 100 Hz, che presentava i seguenti parametri: jA = 100 mA cm-2, tc = 5 ms e tp = 5 ms, a cui corrisponde una densità di corrente media jav = 50 mA cm-2. Gli spessori del rivestimento in rame (δ) sono stati di 10, 20, 40 e 60 µm. Come catodo è stato utilizzato un pezzo di ottone (2601/2 hard, ASTM B36) con una superficie di 1,0 × 1,0 cm2, mentre come anodo è stato utilizzato un pezzo di rame con una superficie di 8,0 × 5,0 cm2. Il catodo era posizionato al centro della cella tra due piastre di rame parallele, con una distanza di 2,0 cm tra anodo e catodo. La preparazione degli elettrodi in ottone per l’elettrodeposizione è effettuata levigando con carta vetrata di SiC di grana #800, #1000 e #1200 e risciacquo in acqua. Successivamente, l’elettrodo è stato sgrassato a una temperatura di 70°C, per poi procedere ad un attacco acido (20% di H2SO4) a 50°C. Dopo ogni fase, i catodi sono stati risciacquati con acqua distillata. Per la preparazione dell’elettrolita sono stati utilizzati acqua distillata doppiamente e reagenti di grado analitico.
Microstruttura dei rivestimenti
Per la caratterizzazione della microstruttura dei rivestimenti si è utilizzato:
- Microscopio elettronico a scansione (SEM), modello JEOL JSM-6610LV (JEOL Ltd., Tokyo, Giappone) – analisi morfologica;
- Microscopio a forza atomica (AFM), modello Auto Probe CP Research. TM Microscopes, Veeco Instruments, Santa Barbara, CA, USA – analisi topografica dei rivestimenti. I valori della rugosità media aritmetica assoluta (Ra) sono stati misurati dai dati dell’immagine media utilizzando il software SPLab (SPMLab NT Ver. 6.0.2., Veeco Instruments, Santa Barbara, CA, USA);
- Microscopio ottico (OM), modello Olympus CX41 collegato al computer – analisi della struttura interna (analisi della sezione trasversale). I rivestimenti di Cu sono stati immersi in un acrilato autoindurente (Veracril® New Stetic S. A., Antioquia, Colombia) utilizzando uno stampo. Per la miscelazione sono stati utilizzati tre parti di polimero autoindurente Veracril® e una parte di monomero autoindurente Veracril®. Il tempo di polimerizzazione autoindurente a temperatura ambiente è stato di 20 minuti. Dopo la polimerizzazione, i campioni sono stati rimossi dallo stampo in teflon e levigati meccanicamente con carta vetrata di SiC di grana #2000 e con emulsione di polvere di Al2O3 di diverse dimensioni di grana (1 e 0,3 µm). Dopo il risciacquo in acqua e l’asciugatura in flusso di azoto, è stata osservata la sezione trasversale al microscopio ottico e sono stati misurati gli spessori del rivestimento.
Proprietà meccaniche dei rivestimenti
Per la caratterizzazione della durezza dei rivestimenti si è utilizzato:
- un tester di microdurezza Vickers “Leitz Kleinert Prufer DURIMET I” (Leitz, Oberkochen, Germania) con carichi applicati e tempo di test dipendenti dal tipo di caratteristica meccanica sotto esame. Per l’analisi di durezza, sono stati applicati carichi (P) nell’intervallo da 0,049 a 2,94 N con un tempo di attesa di 25 s. Per le altre prove di indentazioni il tempo di attesa è stato fatto variare nell’intervallo da 15 a 65 s con carichi applicati di 0,49 e 1,96 N.
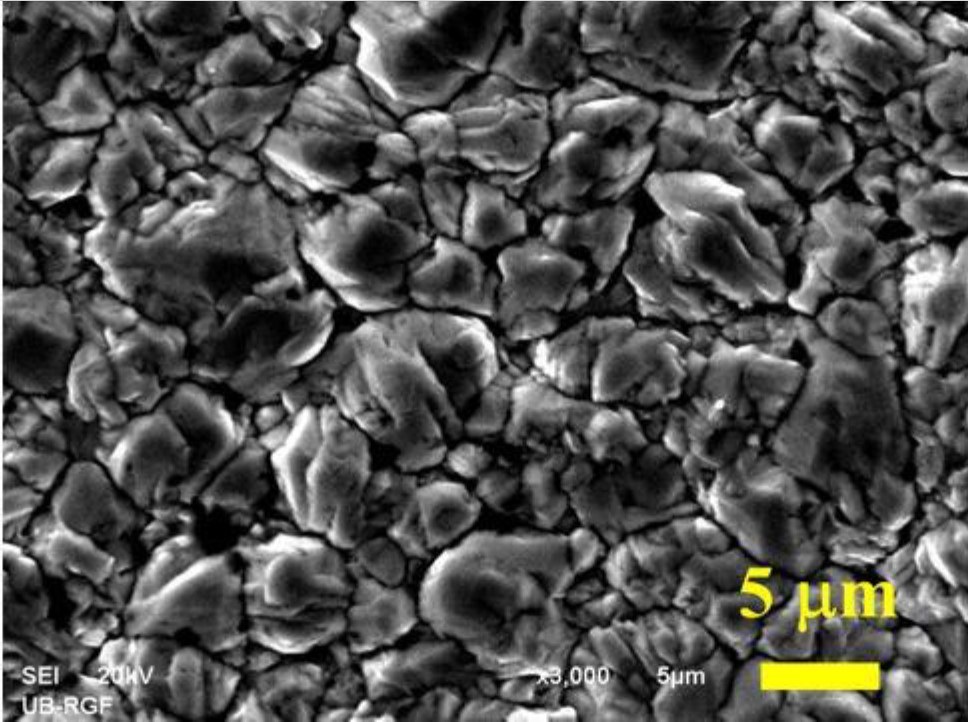
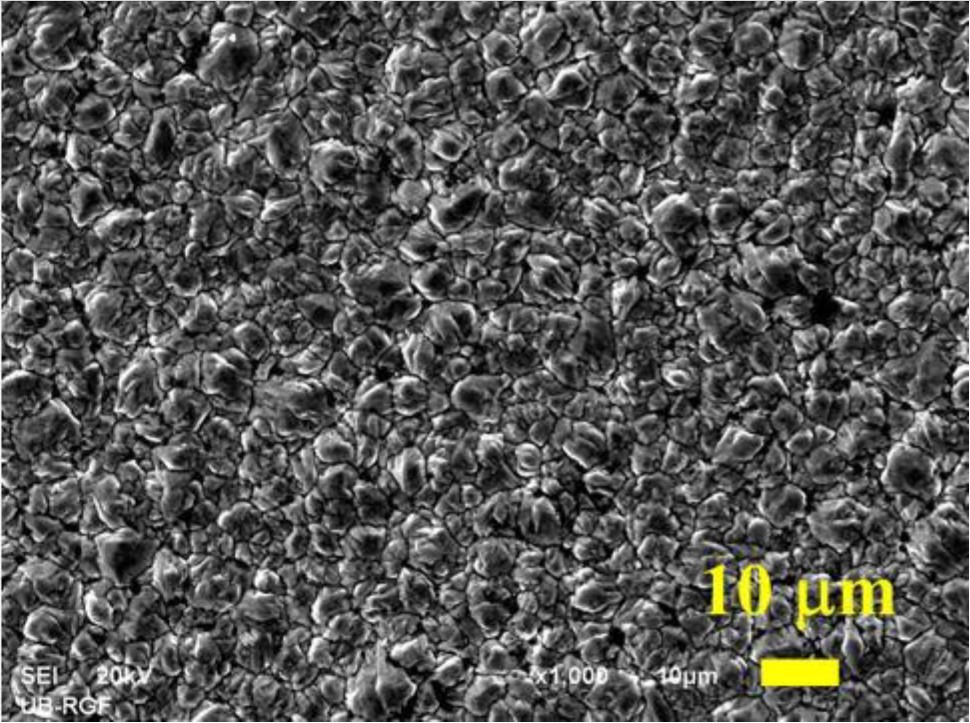
Risultati
Caratteristiche morfologiche
La Figura 1 mostra la morfologia del rivestimento di rame elettrodepositato alle condizioni descritte (jav = 50 mA cm-2, tc = 5 ms, tp = 5 ms e jA = 100 mA cm-2), per uno spessore (δ ) di 40 μm. A tali condizioni, a fronte di una sovratensione tra 290 e 350 mV emerge una situazione di inizio del controllo misto attivazione-diffusione che rappresenta la circostanza ottimale per la formazione di rivestimenti compatti e uniformi. La Figura 2 mostra invece una tomografia della superficie per spessori (δ) di 10, 20, 40 e 60 μm. I valori riscontrati di rugosità assoluta (Ra) sono indicati in Tabella 1 con dati presentati quali media ± deviazione standard per 12 punti di misura. È evidente come, con l’aumentare dello spessore, la rugosità cresce arrivando a circa sette volte. Un’analisi della sezione trasversale è poi presente in Figura 3 e mostra la struttura uniforme e compatta dei rivestimenti dello spessore previsto.
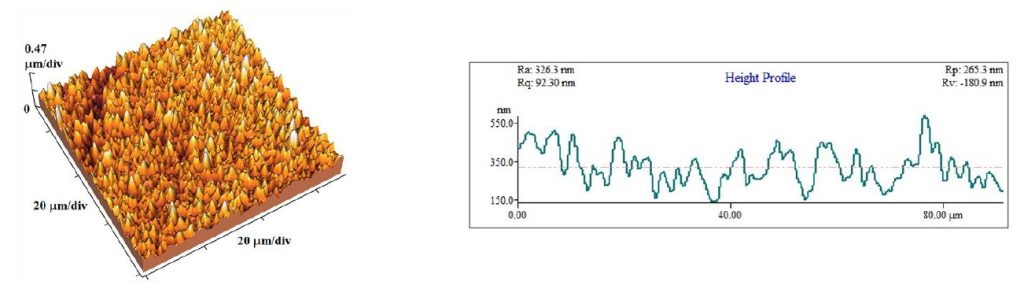
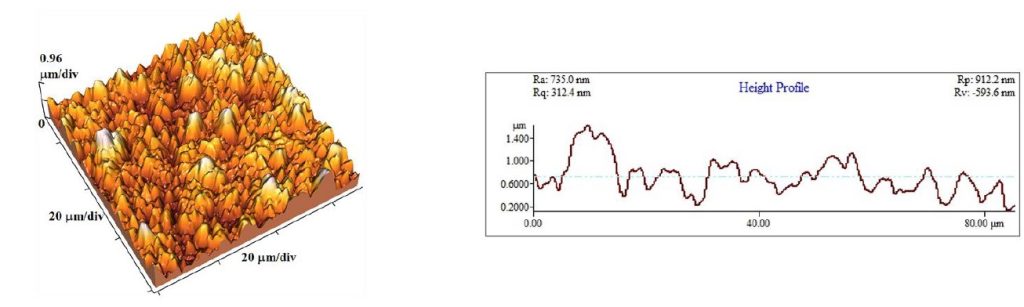
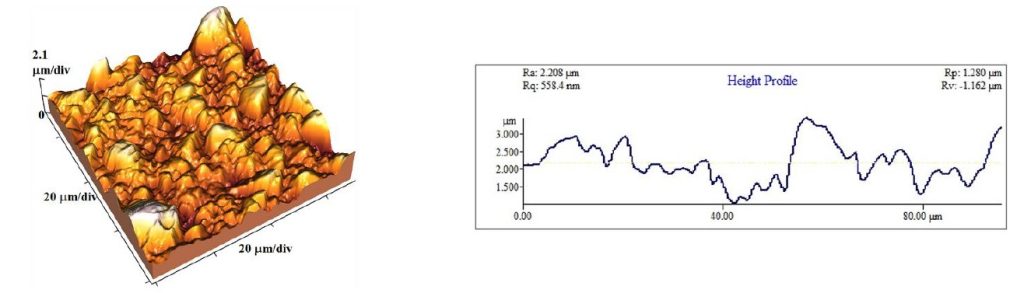
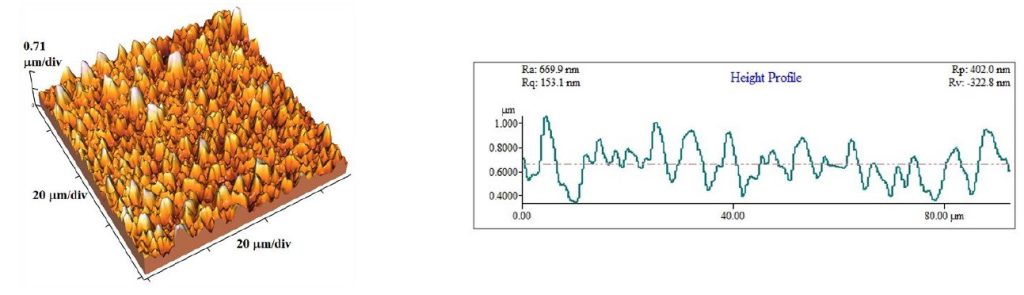

Caratteristiche meccaniche
Per andare a determinare la durezza composita (Hc) di un rivestimento attraverso un modello, il primo passo consiste nella misura vera della durezza assoluta di un substrato (Hcoat). La durezza composita dipende infatti dal carico applicato durante la prova e dalla dimensione della diagonale misurata. Considerato poi che il test di Vickers è normalizzato secondo gli standard ASTM E384 e ISO 6507, con misure in kgf e mm, e non in N, nella relazione si deve tenere in conto anche del fattore 9.8065.
Per il nostro scopo, si è utilizzato il modello “PSR” (resistenza proporzionale del campione), ampiamente utilizzato nella determinazione della durezza assoluta del substrato. Secondo questo modello, il carico applicato (P) e la dimensione della diagonale dell’impronta misurata (d) sono correlati attraverso un carico critico, ossia quel carico applicato al di sopra del quale la microdurezza diventa indipendente dal carico. La Figura 4 mostra la dipendenza del rapporto tra carico applicato e diagonale di impronta, da cui è stata innanzitutto calcolata una durezza assoluta (Hs) del substrato in ottone B36 pari a 1.41 GPa.
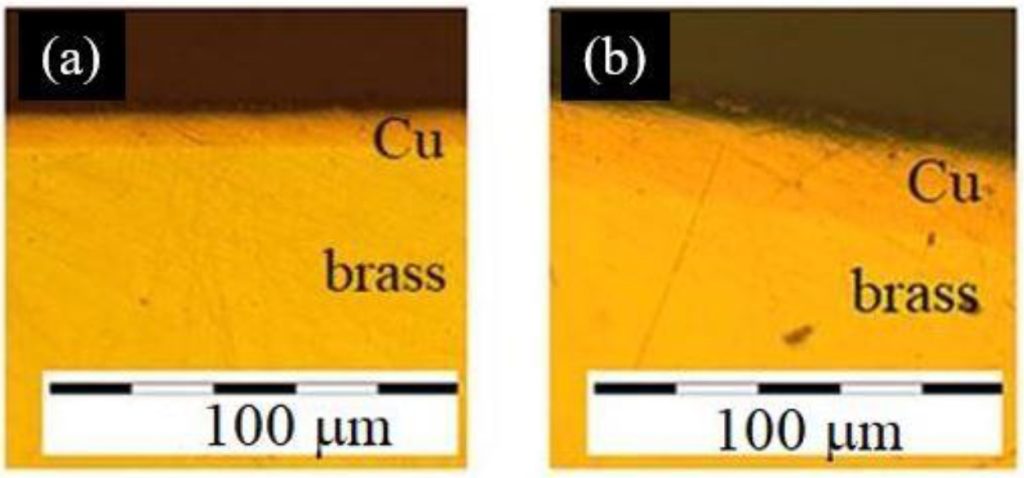
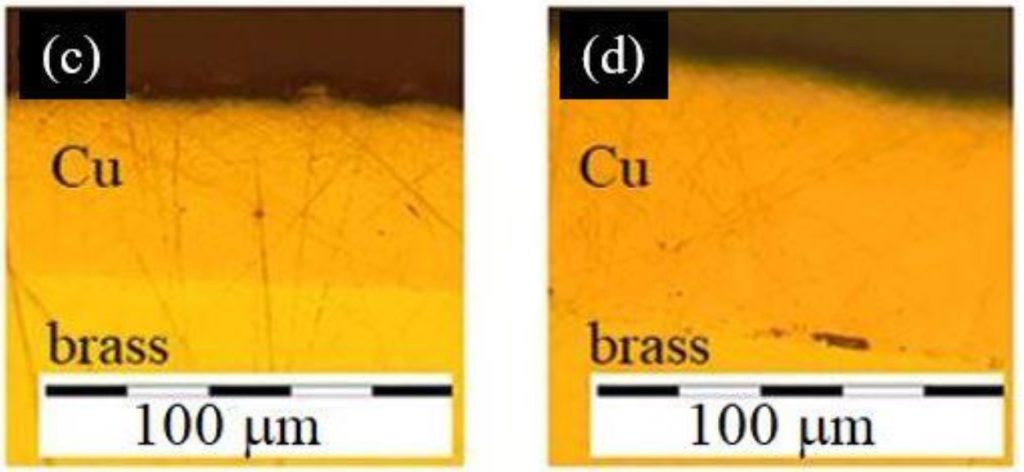
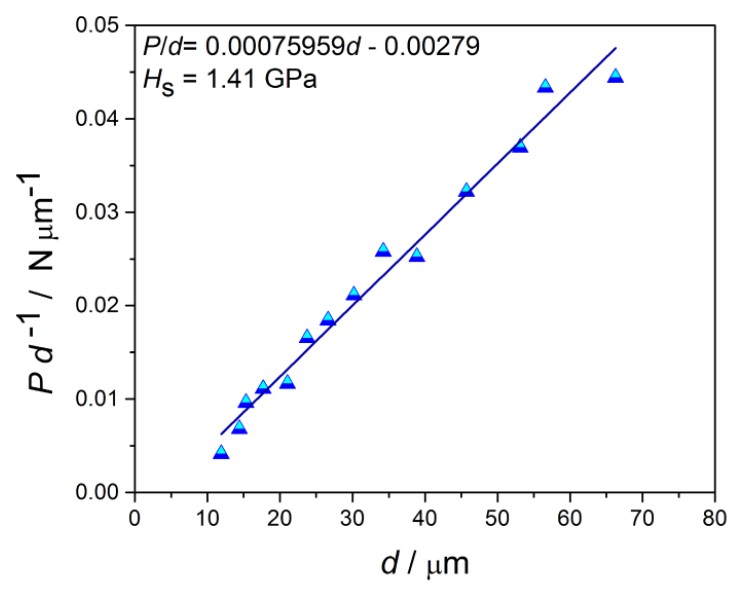
La dipendenza della durezza composita (Hc) dalla profondità relativa di indentazione (RID) per i rivestimenti di Cu con spessori (δ ) di 10, 20, 40 e 60 μm è mostrata in Figura 5a. Il RID è definito come il rapporto tra la profondità di indentazione (h) e lo spessore del rivestimento (d), e i valori RID compresi tra 0.01 e 0.1 indicano l’effetto dominante della durezza del rivestimento sulla durezza composita. Per valori RID compresi tra 0.1 e 1, sia il substrato che il rivestimento contribuiscono al valore composito, e infine, valori RID superiori a 1 indicano l’effetto dominante della durezza del substrato sulla durezza composita. La profondità di indentazione è correlata alla diagonale misurata (h = d/7).
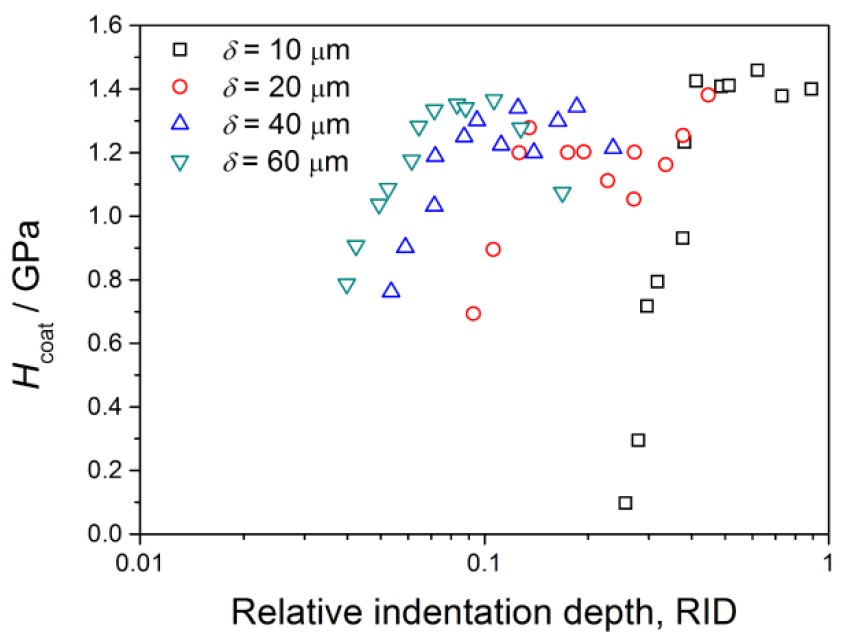
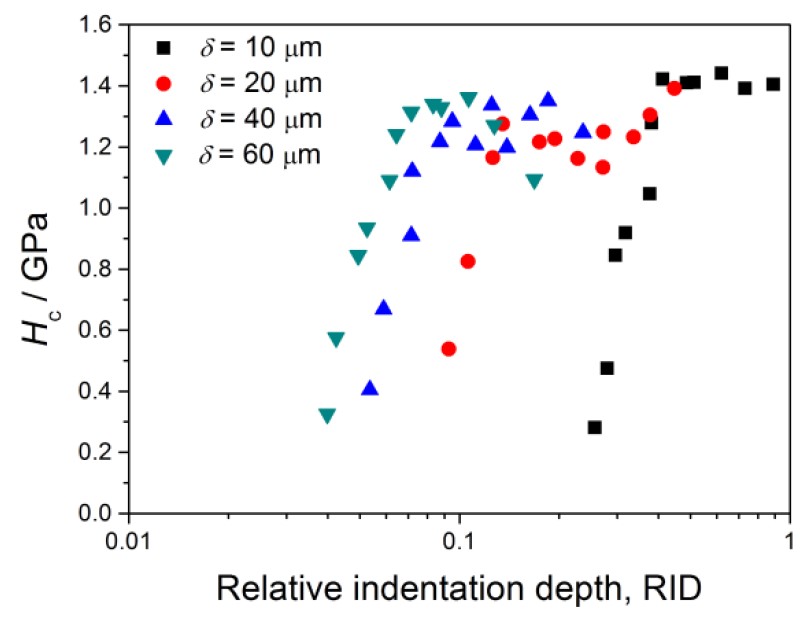
Per i rivestimenti con spessori di 10 e 20 µm, i valori di RID erano compresi tra 0,1 e 1, indicando un contributo congiunto sia dell’ottone che del rame alla durezza composita. Con l’aumentare dello spessore del rivestimento, il contributo del rivestimento alla durezza composita (RID < 0,1) aumenta, come evidente in Figura 5a. Allo stesso tempo, il maggiore valore di durezza composita emerge nel rivestimento di rame di 10 µm. La Figura 5b mostra le dipendenze della durezza del rivestimento (Hcoat) dal RID calcolato secondo il modello Chicot-Lesage (C-L). È stata poi osservata una forma simile delle dipendenze rispetto a quelle ottenute per la durezza composita sul RID. È stata poi condotta un’analisi aggiuntiva con l’obiettivo di stabilire un preciso limite di applicabilità del modello C-L, ovvero di stabilire un limite oltre il quale inizia un forte contributo del substrato alla durezza composita. A tal fine, sono state misurate e sono mostrate nella Figura 6 le dipendenze del (d/d)m dal RID per i rivestimenti di rame con spessori di 10, 20, 40 e 60 µm. L’esponente m rappresenta l’indice composito di Meyer-Brinell per un sistema composito e viene calcolato dalla regressione lineare eseguita su tutti i punti sperimentali per il sistema di rivestimento-substrato esaminato. I valori dell’esponente m con i valori R-quadrati sui grafici ln(P)-ln(d), ottenuti per i rivestimenti di diversi spessori e 12 punti di carico applicati, sono riportati nella Tabella 2.

Per determinare i veri valori di durezza del rivestimento, è stato applicato un modello di durezza composita. Le forme delle dipendenze della Hc dalla RID mostrate nella Figura 5a, così come il valore della durezza dell’ottone di 1.41 GPa, indicano che i rivestimenti di rame sull’ottone appartengono al tipo di sistema di durezza composita “film morbido su substrato duro“. Per questo motivo, è stato preferito il modello Cheng-Gao (C-G) per la determinazione della vera durezza del rivestimento dalla durezza composita misurata. Il modello C-G è stato sviluppato per questo tipo di sistema composito, ed è stato utilizzato con successo per determinare la durezza dei rivestimenti di rame ottenuti per elettrodeposizione mediante il regime PC su un substrato Si(111) molto duro. Il modello C-G fornisce una correlazione esponenziale inversa tra la durezza composita e la profondità di indentazione sono parametri di adattamento. Per il sistema di durezza composita “film morbido su substrato duro”, il valore di detto esponente (n) è 1.8. Successivamente, la durezza del rivestimento (Hcoat) è stata calcolata attraverso una analoga relazione arrivando ai valori Tabella 3.
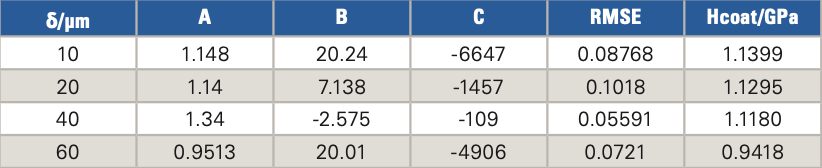
Il principale parametro che definisce le caratteristiche di resistenza al creep dei rivestimenti è un esponente di “stress” (μ) che può essere determinato mediante l’applicazione del modello Sargent-Ashby. Secondo questo modello, esiste una dipendenza (esponenziale inversa) tra la durezza composita (Hc) ed il tempo di permanenza (hold/dwell time) (t) che caratterizza il fenomeno di creep, legata proprio a questo esponente (μ). Valori intorno a 1 indicano che il creep presenta un meccanismo dominante di diffusione, vicino a 2 che si manifesta uno scorrimento dei bordi di grano, e nel caso di valori compresi tra 3 e 10, emergono dislocazioni e una loro salita in superficie. Detto valore può essere determinato sulla base della dipendenza lineare dei logaritmi naturali Hc e t, dove la pendenza di una retta corrisponde a un esponente di tensione negativo inverso (-1/ μ) (Figura 8). I valori ottenuti degli esponenti di tensione sono riassunti nella Tabella 4.
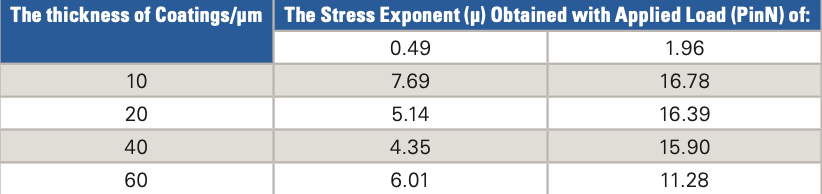
Per un carico applicato di 0,49 N, l’esponente dello sforzo diminuisce con l’aumento dello spessore del rivestimento da 10 a 40 µm. Dopo aver raggiunto il valore minimo con lo spessore del rivestimento di 40 µm, si è osservato un aumento del valore di questo esponente. D’altra parte, con il carico applicato elevato (1,96 N), gli esponenti dello sforzo per i rivestimenti con spessori di 10, 20 e 40 µm erano vicini tra loro e considerevolmente più alti rispetto a quelli ottenuti con un carico di 0,49 N. Il valore ottenuto con il rivestimento di rame spesso 60 µm era più basso, ma comunque significativamente più alto rispetto a quelli ottenuti con il carico più basso. Di conseguenza, con il basso carico applicato di 0,49 N, il meccanismo dominante è il creep per dislocazione e la salita delle dislocazioni. Con il carico applicato elevato, i valori dell’esponente dello sforzo che sono elevati e vicini tra loro indicano l’esistenza di qualche altro fenomeno, che verrà discusso in seguito.
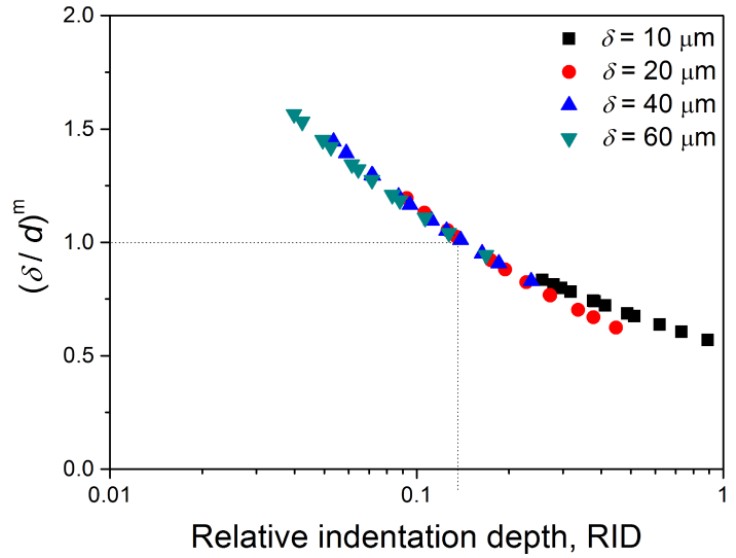
Discussioni e conclusioni
I valori di durezza dei rivestimenti in rame (Cu) nell’intervallo di 0,9418-1,1399 GPa ottenuti mediante l’applicazione del modello C-G erano inferiori alla durezza dell’ottone (= 1,41 GPa), confermando l’ipotesi che i rivestimenti in rame su ottone appartengono al sistema di durezza composita “film morbido su substrato duro”. I valori della durezza del rivestimento erano anche inferiori a quelli ottenuti per i rivestimenti in rame su Si(111) prodotti nelle stesse condizioni di elettrodeposizione. Per i rivestimenti in rame con spessori di 10, 20, 40 e 60 µm, i valori di durezza su Si(111) ottenuti mediante l’applicazione del modello C-G erano rispettivamente 2,119, 1,914, 1,5079 e 1,164 GPa. Confrontando i valori della durezza del rivestimento di questi due substrati, è chiaro che la differenza tra di loro diminuisce con l’aumentare dello spessore del rivestimento. La differenza maggiore è stata ottenuta per i rivestimenti con spessore di 10 µm (circa il 46%), mentre la differenza minore è stata ottenuta per quelli con spessore di 60 µm (circa il 19%). Ciò indica chiaramente che la differenza nei valori di durezza dei rivestimenti può essere attribuita al tipo di substrato utilizzato, ovvero alle diverse contribuzioni della durezza del substrato alla durezza determinata del rivestimento. Ad esempio, sebbene entrambi i substrati, Si(111) e ottone B36, appartengano alla categoria dei substrati “duri” rispetto ai rivestimenti in rame, la durezza del Si(111) era circa cinque volte maggiore rispetto a quella dell’ottone B36 (7,42 GPa contro 1,41 GPa, rispettivamente). Inoltre, i valori della durezza composita misurati del substrato Si(111) erano fino a 0,70 GPa più grandi rispetto a quelli dell’ottone B36, con una tendenza a diminuire all’aumentare dello spessore del rivestimento. Per il rivestimento in rame con spessore di 60 µm, questa differenza era di soli circa 0,050 GPa. La diminuzione della differenza nei valori di durezza composita con l’aumentare dello spessore del rivestimento è un’altra prova dell’influenza significativa della durezza del substrato, ovvero del tipo di substrato, sul valore misurato della durezza dei rivestimenti.
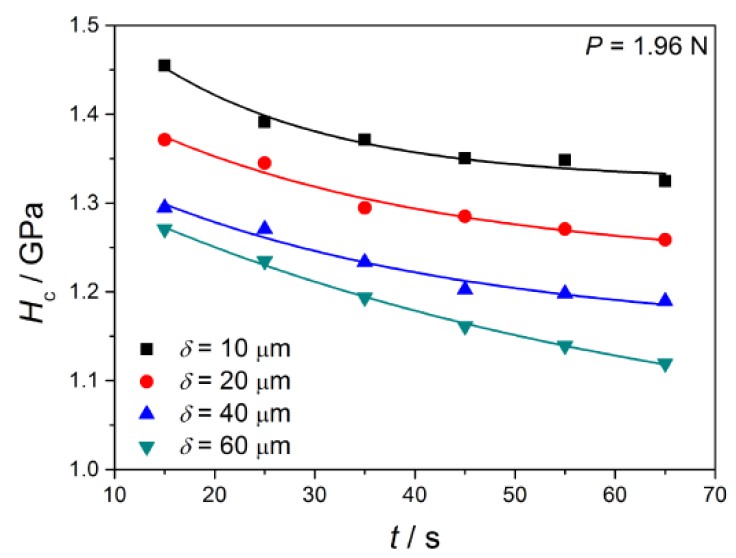
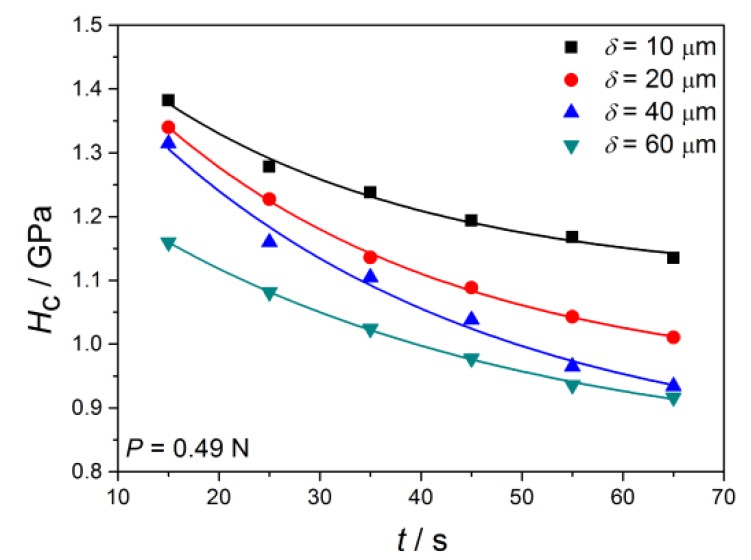
I valori ottenuti per la durezza del rivestimento sono risultati così in linea con quelli riportati in letteratura per i rivestimenti in rame depositati elettroliticamente. I valori tipici per la durezza dei rivestimenti in rame prodotti mediante regimi galvanostatici di elettrodeposizione variavano tra 0,70 e 1,65 GPa. L’applicazione dell’elettrodeposizione a un tasso periodicamente variabile ha portato alla formazione di rivestimenti in rame leggermente più duri rispetto a quelli ottenuti.
Sono stati poi utilizzati modelli di durezza composita, come il modello Chicot-Lesage (C-L) e il modello Cheng-Gao (C-G), per determinare la durezza dei rivestimenti in rame (Cu) a partire dalla durezza composita misurata. È stata considerata anche la meccanica della resistenza al creep. Sulla base dei risultati ottenuti, sono state tratte le seguenti conclusioni:
- Applicando il modello C-L, è stato determinato il valore limite di RID di 0,14 per l’intervallo di carico applicato. Per RID > 0,14, è necessario applicare il modello di durezza composita per determinare la durezza assoluta o reale del rivestimento. Per RID < 0,14, la durezza composita corrisponde alla durezza del rivestimento;
- La quantificazione dei valori di durezza del rivestimento è stata effettuata mediante l’applicazione del modello C-G. I valori ottenuti tra 0,9418 e 1,1399 GPa hanno confermato l’ipotesi che i rivestimenti in rame su ottone appartengano al sistema di durezza composita “film morbido su substrato duro”;
- Gli esponenti di sforzo tra 4,35 e 7,69 ottenuti con un carico applicato di 0,49 N indicano che il meccanismo di creep dominante è il creep per dislocazione e la salita delle dislocazioni;
- Mediante il confronto delle caratteristiche morfologiche e meccaniche ottenute per i rivestimenti in rame con quelle ottenute sul substrato in silicio (Si(111)) nelle stesse condizioni di elettrodeposizione, è stata ulteriormente spiegata e discussa l’influenza delle caratteristiche del substrato sulla durezza dei rivestimenti e sul comportamento della resistenza al creep dei rivestimenti.
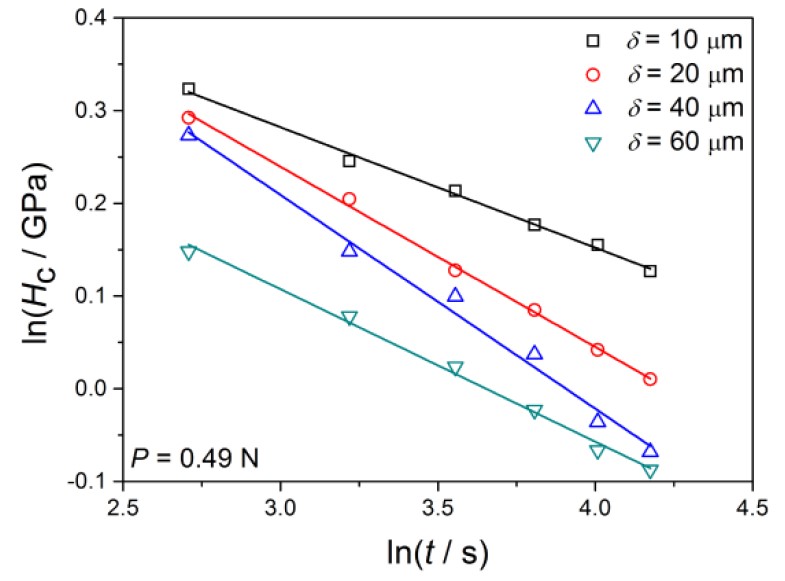
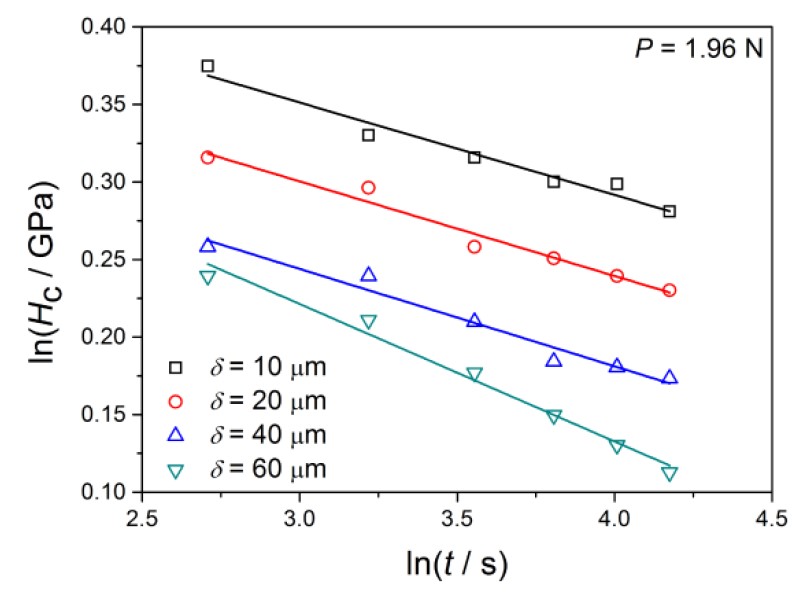
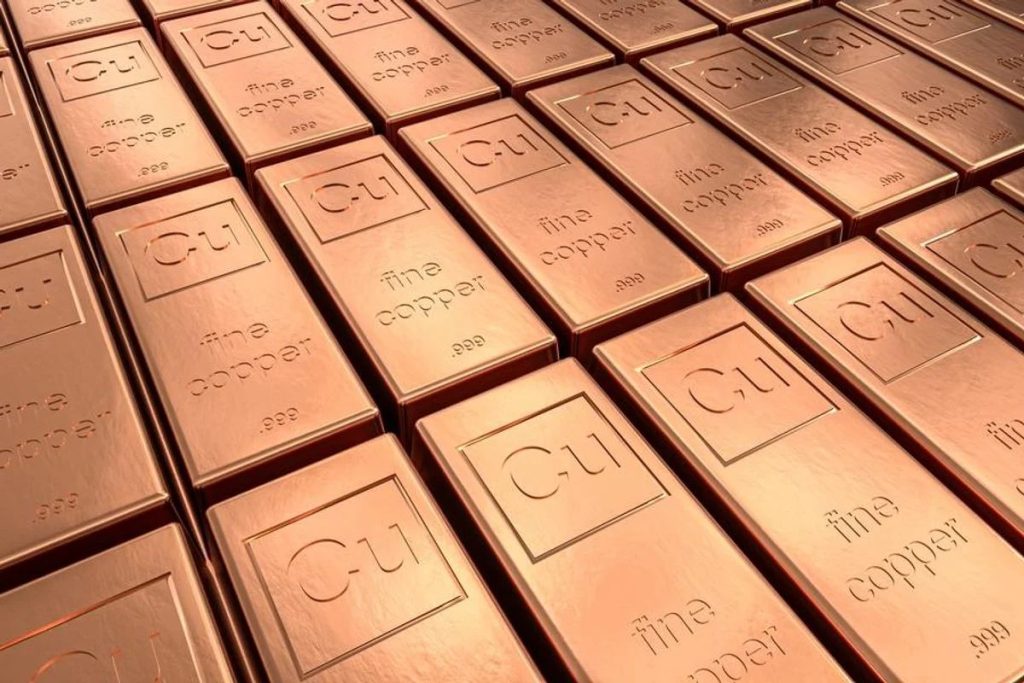
Riferimenti
L’elettrodeposizione del rame e i diversi studi sperimentali sono stati realizzati presso l’Istituto di Chimica, Tecnologia e Metallurgia e la Facoltà di Tecnologia e Metallurgia dell’Università di Belgrado. Per ulteriori approfondimenti:
- Mladenovic I. O. et al., “Application of the Composite Hardness Models in the Analysis of Mechanical Characteristics of Electrolytically Deposited Copper Coatings: The Effect of the Type of Substrate” in Fragassa C. et al., “High-Performance Applications of Metals and Alloys: Material Properties, Behaviour Modeling, Optimal Design and Advanced Processes”. Metals 2021, doi:10.3390/met11010111.