Il mondo manifatturiero sta subendo una trasformazione epocale grazie alle innovazioni digitali. Questa rivoluzione copre potenzialmente ogni aspetto del processo produttivo: dalla progettazione e prototipazione fino alla produzione e alla gestione degli impianti.
Tra tutte le diverse tecnologie digitali in grado cambiare il settore una sta guadagnando larga diffusione: la simulazione. Questa tecnica permette di ricreare virtualmente un processo, così da poterne anticipare i risultati e ottimizzare le operazioni. Le simulazioni consentono alle aziende di testare e validare le idee in fase progettuale grazie all’ambiente virtuale prima di impegnarsi in costose produzioni fisiche.
Questo non solo riduce i costi e i tempi di sviluppo, ma consente anche di identificare e risolvere potenziali problemi prima che si verifichino nella realtà, migliorando così la qualità del prodotto finale e riducendo il rischio di fallimento.
Le simulazioni possono avvenire a diversi livelli e con diversi dettagli. È infatti possibile simulare processi produttivi analizzando i flussi, ma anche simulare processi manifatturieri andando a ricreare digitalmente la trasformazione fisica a cui è sottoposto il materiale.
Queste innovazioni digitali e la loro diffusione stanno ridefinendo il panorama manifatturiero, consentendo alle aziende di essere più competitive, flessibili e orientate al cliente. Tuttavia, per massimizzarne i benefici è essenziale un investimento continuo in competenze, insieme a una cultura aziendale orientata all’innovazione e alla sperimentazione.
Simulazioni di processo
Nel mondo della lamiera i processi di trasformazione tradizionali si basano sulla deformazione del materiale in seguito all’applicazione di forze. Le simulazioni in questo settore sono ben diffuse e giocano un ruolo chiave per ottimizzare la conoscenza e l’ottimizzazione del processo di deformazione.
Le simulazioni più diffuse si basano su tecniche “ad elementi finiti” (“FEM” o “Finite Element Method”). Questa tecnica sfrutta una divisione virtuale del materiale in tante piccole porzioni per poi studiarne l’interazione tra esse tramite equazioni matematiche. Si tratta di una soluzione in grado di prevedere e analizzare il comportamento del materiale sotto diversi carichi.
Tuttavia questa tecnica presenta anche alcuni svantaggi. Innanzitutto, nonostante siano stati fatti i passi da gigante da parte delle soluzioni software disponibili, è richiesta esperienza per una corretta implementazione data la complessità delle tecniche FEM. Inoltre i tempi computazionali possono essere particolarmente elevati, specialmente nel caso di grandi dimensioni e numerosi elementi. Dall’altra parte sta rapidamente prendendo piede la tecnologia delle “Deep Neural Network” (abbreviate come DNN).
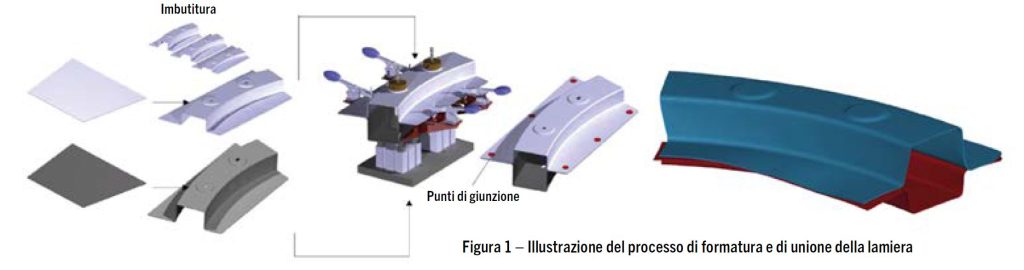
Questa tecnologia fa parte dell’Intelligenza Artificiale e utilizza strutture digitali che simulano l’architettura cerebrale, con diversi livelli di neuroni e sinapsi. Le Reti Neurali Profonde sono in grado di apprendere relazioni e modelli partendo da una grande quantità di dati. Nella fase di “training” vengono apprese le informazioni statistiche che permettono poi di predire i risultati.
Queste tecniche in generale si comportano bene in scenari inosservati interpolando i dati e generalizzando per predire il comportamento. Gli autori propongono un innovativo approccio per sfruttare le Reti Neurali al posto delle più tradizionali simulazioni FEM. Infatti le DNN, una volta addestrate, permettono di fornire predizioni in tempi rapidi e riducendo fortemente i tempi computazionali.
La sperimentazione
I ricercatori propongono un approccio basato sullo studio del processo di formatura e unione della lamiera (fig. 1). Lo studio parte da una sperimentazione dell’istituto Fraunhofer IWU che comprende 725 simulazioni di formatura e 321 di unione. Questo studio esplora i differenti parametri e la loro interazione. I parametri variati, per la formatura, sono diversi tra cui lo spessore della lamiera, la profondità della trasformazione, il gap e la forza del premilamiera. Ogni simulazione è composta da oltre 20.000 nodi.
Due diversi modelli di reti neurali sono stati proposti per ottenere quanto desiderato. Interessante il fatto che questi modelli siano stati creati includendo il minor numero possibile di parametri, così da non accrescere inutilmente i carichi computazionali.
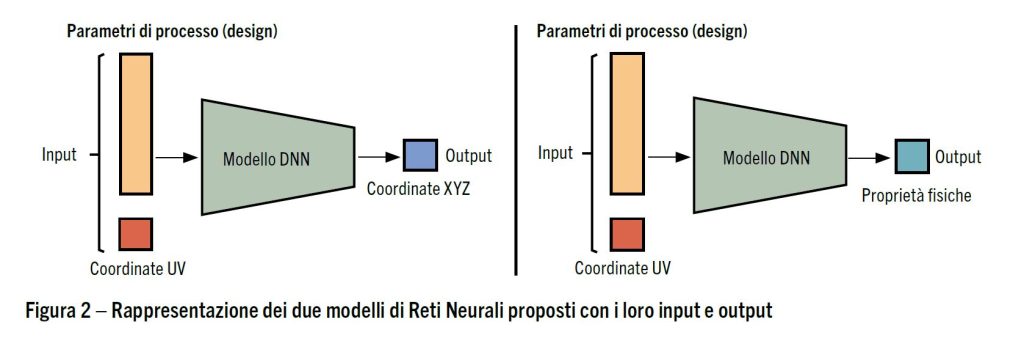
Invece di trattare ogni simulazione FEM come campione unico per il training, il modello implicito si basa sull’apprendimento di quantità rilevanti per ogni nodo di ogni simulazione. In questo processo sono state create due reti neurali (fig. 2) entrambe aventi come input i parametri di processo e le coordinate del singolo nodo.
L’output della prima rete è la posizione spaziale dal nodo, mentre la seconda predice lo spessore, l’assottigliamento e lo sforzo. Il dataset di partenza è stato diviso in 725 esperimenti per training e test, mentre altri 75 esperimenti sono stati utilizzati per la fase di validazione.
I risultati
I modelli proposti sono in grado di convergere presentando risultati molto buoni confermati anche nella fase di validazione. Sia per il processo di formatura che per quello di unione i risultati sono interessanti (fig. 3). Viene confermata anche la capacità di generalizzare delle reti neurali provando a simulare esperimenti non visti in precedenza.
Questo approccio basato su intelligenza artificiale è in grado di gestire dati irregolari e non strutturati relativi a processi di trasformazione individuandone relazioni nascoste e riuscendo fornire previsioni riguardo al risultato.
Le tradizionali simulazioni FEM richiedono aggiustamenti manuali e spesso necessitano di una rifinitura delle mesh. Al contrario le reti neurali sono in grado di apprendere da un dataset e potenzialmente anche generalizzare ad un nuovo scenario senza dover nuovamente suddividere lo spazio in piccole porzioni (mesh). Questo permette di risparmiare costi, tempo ed energia. Permettendo così agli utilizzatori di ottenere stime rapidamente, ma non per questo meno affidabili e precise.
Sebbene secondo gli autori rimangano degli sviluppi da effettuare prima di poter vedere soluzioni del genere applicate su larga scala, le premesse sono ottime. Nonostante il continuo aumento e l’accessibilità delle potenze computazionali spesso il tempo è una risorsa limitata. Per questo riuscire ad accorciare i tempi di simulazione può risultare interessante.
Da apprezzare anche la possibilità di applicare le nuove tecniche di intelligenza artificiale in ambiti più tradizionali, come quello delle simulazioni ad elementi finiti, per offrire confronto e supporto, così da portare vantaggi agli utilizzatori finali. Il mondo della ricerca infatti ha il compito di proporre e approfondire tecnologie che potenzialmente entreranno in ambito industriale tra qualche anno.
Inoltre, lo sviluppo dell’industria verso un modello sempre più digitalizzato e connesso ben si concilia con soluzioni Smart in grado di sfruttare le informazioni provenienti da diverse sorgenti.
Le fasi di progettazione, di produzione e di qualità, grazie alle nuove tecnologie possono avvicinarsi sempre di più, così da ridurre le tradizionali barriere e portando all’ottenimento di un prodotto migliore e più competitivo.
Fonte: Farahani, A., Atoofi, P., Vitay, J., Hamker, F.H., 2023. Implicit neural representations for deep drawing and joining experiments, in: Engineering for a Changing World: Proceedings : 60th ISC, Ilmenau Scientific Colloquium, Technische Universität Ilmenau, September 04-08, 2023. Presented at the Ilmenau Scientific Colloquium. Technische Universität Ilmenau ; 60 (Ilmenau) : 2023.09.04-08, ilmedia, Ilmenau.