La fresatura di spianatura è una delle operazioni più diffuse nelle lavorazioni meccaniche. Alcune considerazioni sulla formazione del truciolo, sulle forze in gioco e sullo sviluppo di calore, durante questa operazione
Per frese ad inserti si intendono quelle frese nelle quali gli elementi attivi sono costituiti da inserti pluritaglienti, non riaffilabili, staffati meccanicamente. Questo tipo di utensile è il risultato di una lunga evoluzione tutta tesa a ridurre i costi di produzione attraverso varie direttrici.
Le frese di grandi e medie dimensioni erano costruite, in origine (e parliamo ora quasi della preistoria degli utensili), con lame saldate sul corpo. Ben presto però si abbandonò questa soluzione, troppo costosa, perché una volta sfruttati completamente i taglienti bisognava gettare via la fresa sprecando la grande quantità di materiale del corpo.
Molto più razionale è la fresa a lame riportate, usata ancora anche se sempre meno. Essa permette infatti la completa utilizzazione delle lame, con un maggior numero di affilature ed una praticamente illimitata durata del corpo porta lame.
Da questo tipo di fresa alla fresa ad inserti il passo è stato breve, ma non per questo privo di difficoltà.
I motivi che hanno diretto le ricerche verso la fresa ad inserti sono, in sostanza, gli stessi per cui si è giunti a preferire i porta-inserti in sostituzione degli utensili a punta singola nella tornitura, anzi, nelle frese questi motivi sono ancora più determinanti e si possono così riassumere:
- Eliminazione delle riaffilature con conseguente minor perdita di tempo per il ripristino dei taglienti. Oltre al vantaggio dell’abolizione della spesa per la riaffilatura si ha il vantaggio di poter ridurre la scorta di corpi fresa con minor capitale immobilizzato.
- Eliminazione delle saldature che, specialmente per particolari tipi di leghe dure, sono difficoltose, in quanto quasi sempre le lame sono sottili e le fessurazioni sono facili.
- Migliore utilizzazione della lega dura con possibilità, tra l’altro, di variare rapidamente il tipo di lega impiegata adattandola al materiale lavorato ed alle caratteristiche di lavoro che si scelgono per le varie lavorazioni.
- I taglienti vengono ripristinati in pochi minuti, spesso senza smontare la fresa dalla macchina.
- Possibilità di avere sempre i taglienti ricoperti con TiN o altro, cosa questa di estrema importanza.
In progressi delle frese a inserti
Oggi si usano quasi esclusivamente le frese a inserti perché nel corso degli ultimi anni sono stati fatti enormi progressi in tutti quei particolari settori che sono coinvolti nella costruzione e nell’uso delle frese a inserti. Essi si possono così riepilogare:
- Precisione nell’esecuzione dei corpi. Il corpo porta inserti è oggi costruito con macchine a controllo numerico di estrema precisione, che consentono di avere le sedi precise in cui vengono posizionati gli inserti. È questo un elemento fondamentale per una precisione finale delle frese. Se ci sono errori di posizionamento delle sedi, è perfettamente inutile avere degli inserti super- precisi. La fresa avrà sempre errori di eccentricità o di planarità.
In più oggi si producono frese ad inserti anche di piccolo diametro e anche con forme del tutto particolari, come le frese di forma per la fresatura dei rotori per compressori o con altri profili complessi, grazie appunto alle lavorazioni con centri di lavoro a controllo numerico.
- Sviluppi nella tecnologia di sinterizzazione degli inserti. Oggi vengono prodotti inserti di grande precisione direttamente in sinterizzazione senza far ricorso ad operazioni di rettifica, e questo ovviamente riduce drasticamente i costi. Inoltre oggi, la quasi totalità degli inserti è dotata di sofisticati rompitrucioli, ottenuti per sinterizzazione, che consentono, caso per caso, la gestione del flusso dei trucioli, cosa questa alquanto problematica con le frese a lame riportate.
- Miglioramento nella tecnologia di produzione dei carburi sinterizzati. Oggi si producono metalli duri di gradi sempre più sofisticati, con caratteristiche tecniche molto migliori che in passato, questo anche grazie all’introduzione delle micrograne che conferiscono agli utensili una più alta tenacità.
- Ricoprimenti TiN, TiAlN, TiCN ecc. Questa tecnologia che si è sviluppata enormemente, specie negli ultimi vent’anni, ha in pratica rivoluzionato la filosofia di impiego degli utensili. E questo particolarmente vero nel campo della fresatura. Oggi gli inserti sono tutti ricoperti e permettono prestazioni che un tempo erano impensabili. Con una semplice operazione si girano gli inserti e si utilizzano nuovi taglienti, già ricoperti, senza bisogno di riaffilature.
Talvolta non ci si rende conto che la posizione della fresa rispetto il pezzo può influenzare in maniera pesante il rendimento della fresa stessa e la qualità della superficie lavorata.
I fattori che limitano la vita dei taglienti sono essenzialmente l’usura e le scheggiature.
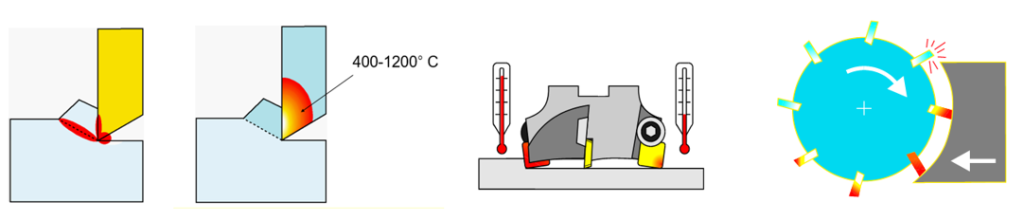
L’usura dipende da moltissimi fattori ma un ruolo non secondario è la temperatura raggiunta nel punto di contatto tra pezzo, truciolo e tagliente. In primo luogo si può dire che le temperature possono raggiungere valori molto elevati che, in presenza di materiali taglienti e ricoprimenti non adeguati, riducono in modo drastico la durata dei taglienti.
Il calore sviluppato durante l’asportazione del truciolo viene dissipato per 80% con i trucioli, per il 10% attraverso il pezzo in lavorazione e per il 10% attraverso l’inserto
Le temperature elevate raggiunte nell’area immediatamente vicina al tagliente calano rapidamente quando il tagliente non è impegnato, e questo comporta un susseguirsi di riscaldamenti e raffreddamenti che danneggiano il materiale del tagliente.
A questi continui shock termici si aggiungono gli urti che il tagliente deve assorbire ogni volta che viene in contatto con il pezzo (figura 1).
Poiché la quantità di calore che viene trasmesso dal truciolo al tagliente dipende tra le altre cose dall’area della superficie con cui avviene il contatto, si provvede a ridurre l’entità di questa superficie con degli opportuni rompitrucioli (figura 2).
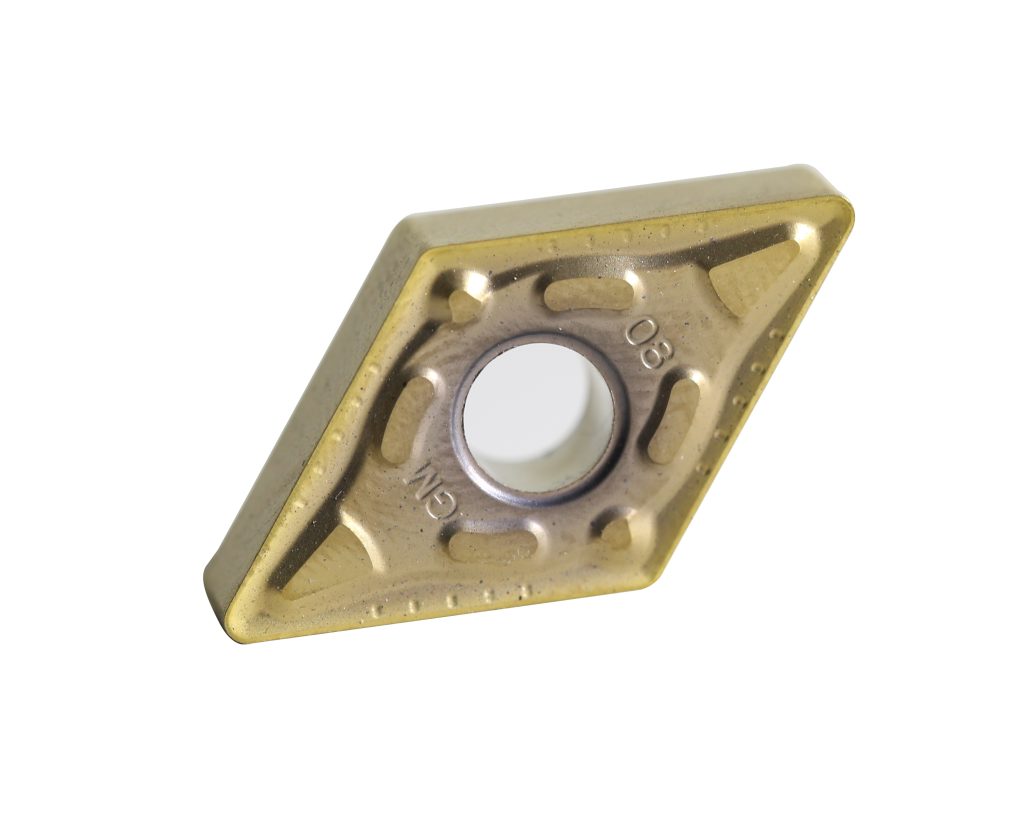
Naturalmente la quantità di calore dipende dalle forze in gioco che a loro volta dipendono
dalle condizioni di lavoro, dalla conformazione e materiale del pezzo lavorato, dalla geometria della fresa e da altre cause di minore importanza.
A sua volta la forza di taglio influenza la potenza richiesta, incide sulle vibrazioni e di conseguenza sulla durata dell’utensile.
Si possono distinguere tre componenti della forza totale: forza assiale, forza radiale e forza tangenziale, le quali sostanzialmente dipendono in valore e direzione dagli angoli di spoglia e dell’angolo di attacco.

Con un angolo di attacco di 45° si riduce la componente radiale Fz e aumenta la componente assiale Fx, mentre se l’angolo di attacco è 0° la componente assiale si riduce di molto a scapito della componente radiale. Bisogna notare che con un angolo di attacco di 45° lo spessore del truciolo, a parità di avanzamento, si riduce, come risulta evidente dalla figura 4.
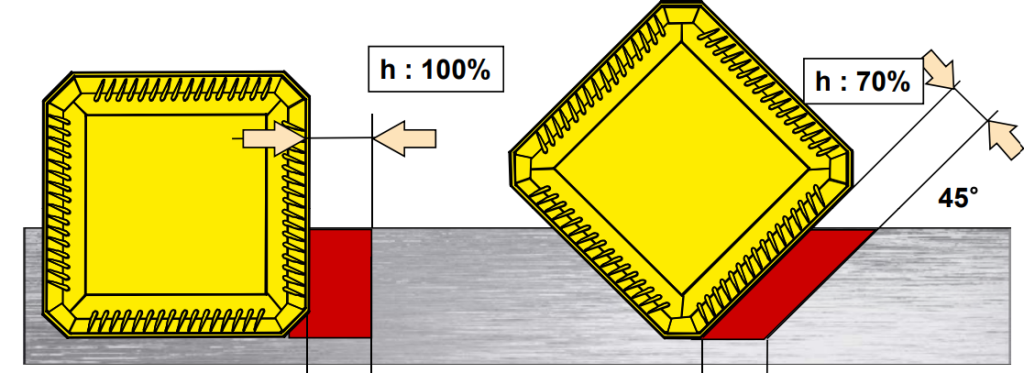
Ma come si è detto le forze non dipendono solo dall’angolo di attacco, anzi una buona parte dello sforzo totale è determinato dagli angoli di taglio radiale ed assiale.
Se essi sono positivi si ha una rimozione più dolce del truciolo con una minore forza assiale, mentre se sono negativi la forza assiale aumenta con possibilità di innesco di vibrazioni.
Con angoli di taglio negativi il truciolo si forma con più difficoltà e richiede una maggior forza per essere rimosso. Se il particolare da lavorare ha uno spessore piccolo, si hanno errori di planarità dovuti alla flessione del pezzo. In questi casi deve essere posta la massima attenzione a come il pezzo appoggia sulla tavola.
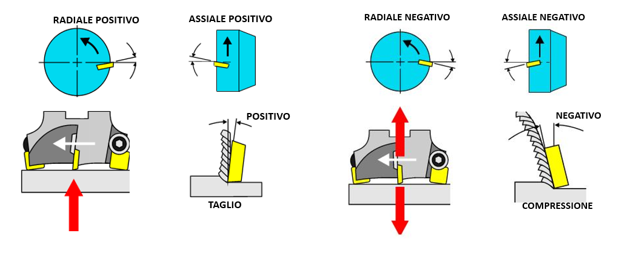
Se molta importanza ha l’aumento della temperatura nella zona di contatto agli effetti della durata dei taglienti, altrettanta ne ha la direzione dell’avanzamento.
Ripetiamo qui il concetto fondamentale di fresatura in concordanza e fresatura in opposizione, anche se è una nozione oramai nota agli addetti ai lavori, tanto più che è valida anche nella dentatura con creatore.
Nella fresatura in opposizione il tagliente comincia a toccare il pezzo quando lo spessore del truciolo è nullo, questo significa che prima di poter iniziare la vera e propria azione di taglio, striscia comprimendo il materiale. In questa fase si ha un grande sviluppo di calore con una usura veloce del tagliente.
Inoltre il materiale del pezzo si incrudisce in superfice modificando la sua struttura.
L’unico vantaggio è che la forza Fh tende a compensare automaticamente gli eventuali giochi della catena cinematica.
Per questo motivo questo tipo di avanzamento si usa prevalentemente con fresatrici di vecchio tipo che non hanno dispositivi di recupero del gioco.
Da notare però che la componente verticale Fv tende a staccare il pezzo dalla tavola e ciò può innescare vibrazioni se il pezzo non è ben bloccato.
Come indicato in figura 6, nella fresatura in concordanza il tagliente attacca il pezzo quando il truciolo ha il suo maggior spessore, quindi il taglio avviene in condizioni migliori perché non ci sono strisciamenti.
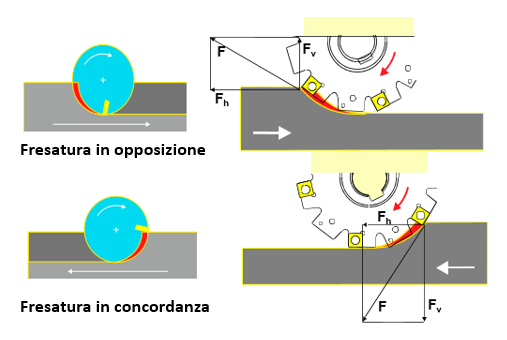
La componente verticale ha, in questo caso, una direzione favorevole, ma se la catena cinematica ha dei giochi si possono avere forti vibrazioni.
Poiché nelle fresatrici moderne la catena cinematica è priva di giochi, risulta evidente che la fresatura in concordanza sarà quella comunemente preferita nelle macchine a Controllo Numerico.
Gli inserti che vengono montati sulle frese sono di vario tipo e differiscono tra loro per la forma, dimensione, angoli di spoglia, materiale e ricoprimento.
Le forme più usate sono quelle triangolari, quadrate ed esagonali, mentre il materiale, è sempre un carburo sinterizzato con un grado che può essere del gruppo P per acciaio, K per ghisa e alluminio e M per ghisa malleabile o altri materiali.
Se si lavorano materiali duri lo spigolo tagliente deve essere protetto con un piccolo quadretto negativo, di larghezza pari o leggermente maggiore al valore dell’avanzamento per dente. Questo per evitare scheggiature precoci.
Per la lavorazione di materiali teneri, quali per esempio l’alluminio, l’angolo di taglio è preferibile sia positivo. Questo si può ottenere con un opportuno rompitruciolo, oppure con inserti che hanno la spoglia inferiore molto grande e che permettono quindi un posizionamento sul corpo fresa che assegna un angolo di taglio positivo.
L’utilizzo di inserti staffati meccanicamente oggi è molto diffuso, si può dire anzi che sia la norma, anche perché con il perfezionamento che hanno avuto i carburi sinterizzati e i vari tipi di ricoprimenti è possibile, in primo luogo, fresare con velocità di taglio estremamente elevate e, nonostante lo sviluppo di una notevole quantità di calore, ottenere durate molto soddisfacenti.
Bisogna notare che i moderni ricoprimenti hanno un coefficiente d’attrito molto basso, intorno a 0,3 che riduce in modo notevole lo sviluppo di calore, ma certi ricoprimenti resistono bene anche a temperature intorno ai 1000°C.
Considerazioni sullo spessore del truciolo
Lo spessore del truciolo in fresatura varia in modo continuo ed ha una forma complessa che dipende da numerosi fattori. È quindi opportuno, per semplificare i ragionamenti parlare di spessore medio del truciolo, elemento questo che dà un’idea dello sforzo di taglio e di quanto la fresa e la macchina siano sollecitate.
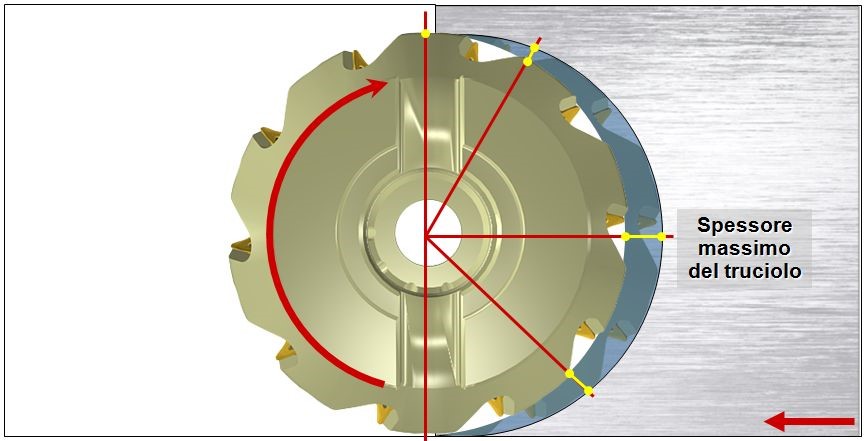
Per iniziare facciamo riferimento alla figura 7 che mostra una fresa che lavora con un impegno del 100%, condizione questa al limite e da evitare quando possibile perché i taglienti sono in contatto con il pezzo per tempi lunghi e quindi si scaldano molto.
Si può osservare intanto che lo spessore varia da zero ai bordi del pezzo fino ad un valore massimo in corrispondenza dell’asse della fresa.
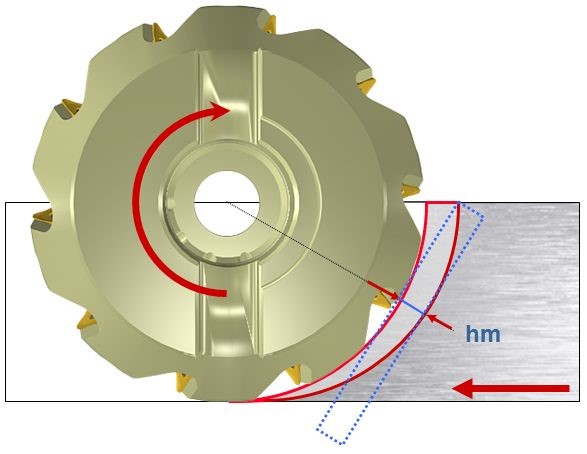
Nella situazione illustrata in figura 8, l’arco di contatto è ridotto della metà, ma lo spessore massimo del truciolo non varia, mentre varia il tempo di contatto e quindi la fresa lavora in condizioni migliori. Il valore dello spessore medio del truciolo hm è uguale al caso precedente.
Se l’arco d’impegno diminuisce si riduce anche lo spessore medio del truciolo come si può osservare in figura 9.
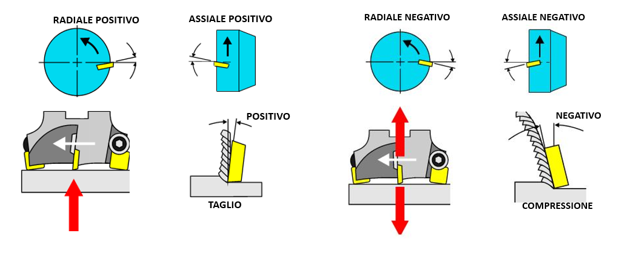
In base alle figure precedenti e alle notazioni seguenti, sono valide le seguenti formule:
D = Diametro esterno della fresa (mm)
ae = Profondità di taglio in direzione radiale (mm)
ap = Profondità di taglio in direzione assiale (mm)
Z = Numero di taglienti della fresa
Vc = Velocità di taglio (m/min)
N = Numero di giri al minuto
fz = Avanzamento per dente (mm)
f = Avanzamento per giro della fresa (mm/giro)
Vf = Velocità di avanzamento (mm/min)
Ψ = Inclinazione del tagliente periferico
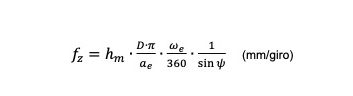
Si può usare una formula semplificata nel caso che il rapporto ae/D sia di 0,4 – 0,3.
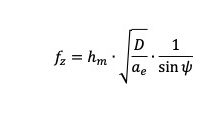
Vuoi approfondire? www.gianfrancobianco.com