Analizziamo caratteristiche e vantaggi della pallinatura, un particolare trattamento atto a migliorare resistenza e funzionalità della lamiera in particolari contesti.
Il trattamento di pallinatura, comunemente indicato anche con il termine inglese shot peening, è un trattamento superficiale utilizzato per migliorare la resistenza meccanica dei materiali e dei componenti meccanici. In particolare, la pallinatura è applicata per migliorare la resistenza a fatica dei componenti meccanici e degli elementi strutturali, la resistenza alla corrosione sotto sforzo, al fretting e in tutte quelle situazioni in cui gli effetti della pallinatura possono contribuire a funzionalizzare la superficie. Questo trattamento superficiale viene ampiamente impiegato nei settori aerospaziale, automobilistico e nella meccanica.
Tuttavia, oggigiorno l’applicazione della pallinatura si sta estendendo anche ad altri settori applicativi, anche in considerazione dei risultati di recenti ricerche relativi ad applicazioni nei settori biomedici, della mobilità elettrica ed altri ancora. Nei paragrafi che seguono, si introducono i concetti fondamentali della pallinatura e se ne descrivono i principali effetti, per poi passare ad analizzare alcuni risultati che mostrano l’efficacia della pallinatura in diverse applicazioni.
Cos’è la pallinatura?
Lo shot peening consiste nel bombardare la superficie di un componente con particelle sferiche o sferoidali ad alta velocità che possono essere realizzate in acciaio, vetro o ceramica, a seconda del materiale da trattare.
Due sono le esigenze da considerare in tal senso; la prima è che le sfere devono avere una durezza superiore a quella del materiale da trattare, per evitare che ad essere trattate siano le sfere stesse e non il componente di interesse, la seconda è che il materiale delle sfere non deve contaminare quello del componente (ad esempio, se si vuole evitare una contaminazione di una superficie di alluminio è bene considerare sfere in vetro o ceramica e non in acciaio). Le sfere possono, poi, avere dimensioni differenti a seconda della geometria del componente da trattare, per evitare che, su dettagli geometrici quali piccoli raggi di raccordo, non sia impedito il contatto nelle zone più critiche, vanificando, quindi, l’effetto del trattamento.
Le macchine
Limitando la trattazione alla pallinatura di tipo convenzionale senza considerare i trattamenti che inducono effetti analoghi ma che richiedono macchinari e, a volte, differenti media (quali ultrasonic shot peening, cavitation shot peening, waterjet peening o laser shock peening), due sono le modalità applicative della pallinatura; la prima utilizza l’effetto centrifugo indotto da una ruota, il secondo considera l’aria compressa come vettore per ottenere le condizioni cinetiche volute, vedi Figura 2.
Il principale vantaggio delle prime è la maggiore produttività e la possibilità di ben inserirle in linee di produzione automatiche. Le pallinatrici pneumatiche, invece, consentono una maggior precisione di lavorazione, permettendo la pallinatura su componenti dalla geometria complessa e ben adattandosi a impianti robotizzati.
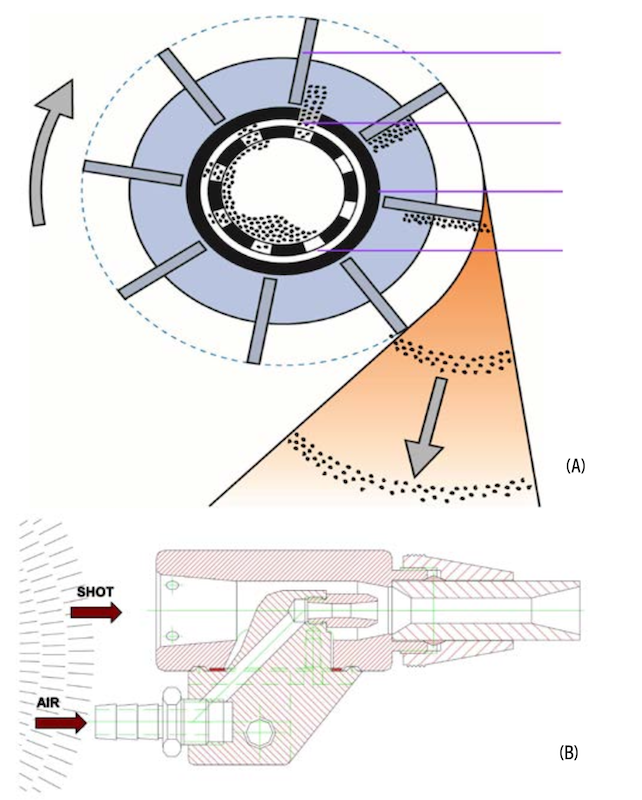
I parametri di pallinatura
Ognuna delle due macchine presenta, chiaramente, dei parametri applicativi particolari e solo ad essa riferibili. Per le macchine centrifughe, ad esempio, si possono considerare la velocità di rotazione della ruota, la geometria delle pale e l’angolo di uscita delle sfere; per le macchine pneumatiche la pressione dell’aria, la distanza tra l’ugello e la superficie da trattare e altri ancora. Tuttavia, la definizione dei parametri legati a una macchina non consente di generalizzare le modalità con cui il trattamento viene eseguito e non è correlabile, almeno direttamente, a quelli che saranno gli effetti indotti dalla pallinatura. Questi ultimi, fissato il materiale da trattare, sono legati (oltre al tipo e al materiale delle sfere) all’energia cumulativa associata alle deformazioni plastiche subite dal componente trattato.
L’energia di deformazione cumulativa è determinata da due fattori: l’energia cinetica associata al flusso di sfere e il tempo totale di trattamento. I parametri che definiscono la pallinatura, l’intensità Almen e la copertura, fanno riferimento a questi fattori. L’intensità Almen è definita come la freccia residua di una piastrina sottile pallinata su di un solo lato, secondo le modalità illustrate in Figura 3. A seconda della severità del trattamento si possono utilizzare piastrine con 3 spessori differenti (denominate A, C, N): l’intensità viene determinata misurando la freccia residua della piastrina al termine della pallinatura su di una sola faccia e dopo aver raggiunto le condizioni di stabilità nel tempo della freccia residua, secondo una procedura che è dettagliata nelle norme.
La copertura indica la percentuale della superficie che è stata pallinata e viene espressa in funzione del tempo necessario a ottenere la pallinatura dell’intera superficie di interesse. Una copertura del 100% indica il tempo necessario per trattare completamente la superficie, del 200% indica che il trattamento sarà eseguito con un tempo doppio rispetto al 100% e così via. Mentre l’intensità Almen è misurata con un apposito strumento (Almen Gage), la copertura si verifica con strumenti ottici adeguati.
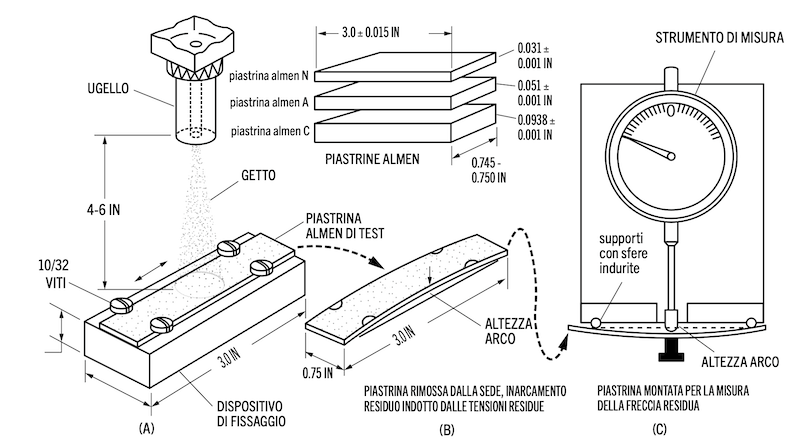
Gli effetti della pallinatura sul materiale
Tre sono i principali effetti della pallinatura sui materiali trattati (Figura 4): l’introduzione di un campo di tensioni residue, di compressione negli strati superficiali di materiale, l’incrudimento superficiale del materiale e la variazione della finitura e della rugosità superficiale.
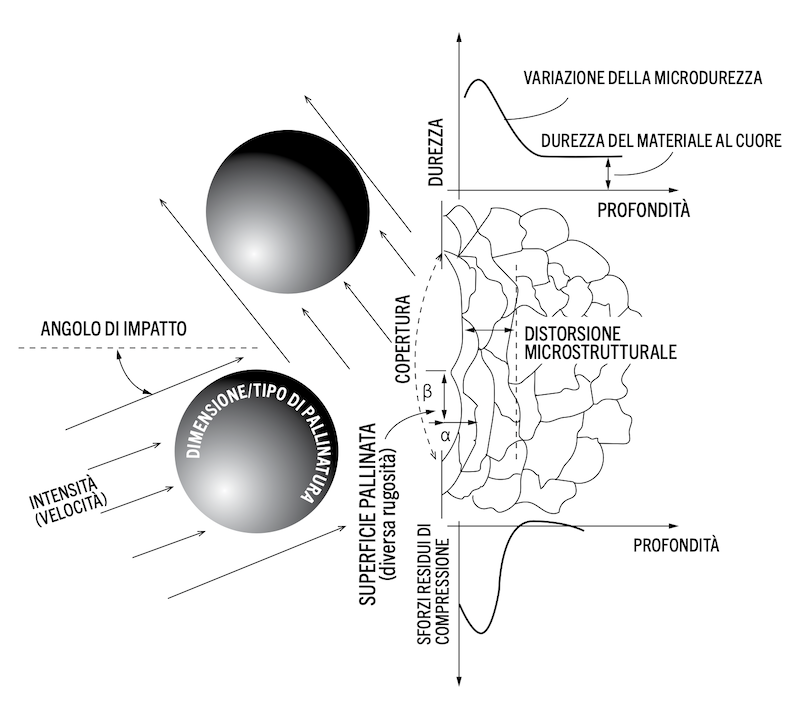
La pallinatura per migliorare la resistenza a fatica
Il miglioramento della resistenza a fatica (il che vuol dire in presenza di carichi ciclici) degli organi delle macchine e degli elementi strutturali è l’applicazione più tradizionale della pallinatura e i primi esempi applicativi risalgono alla prima metà del secolo scorso. Di fatto, i componenti pallinati e poi sottoposti a carichi affaticanti presentano un maggior limite di fatica e, nel capo della fatica a termine, una maggiore durata a pari ciclo di carico. Tali benefici sono dovuti principalmente al campo di tensioni residue e all’incrudimento indotti dal processo. Il primo effetto è quello, ad oggi, più indagato.
In Figura 5 [1] è possibile osservare una serie di risultati che permettono di comprendere il diretto legame tra sforzi residui di compressione e la resistenza a fatica. Di fatto tale effetto è legato alla capacità delle tensioni residue di compressione di impedire/ritardare o mitigare la nucleazione e la propagazione di una cricca di fatica. A tal fine la pallinatura risulta molto efficace, in quanto il campo di sforzi residui di compressione si estende al di sotto della superficie per qualche decimo di millimetro.
Nella figura è possibile osservare anche l’effetto dovuto alla applicazione della pallinatura su un pezzo già caricato. Tale modifica della pallinatura, chiamata comunemente strain peening, implica l’esecuzione della pallinatura su pezzi precedentemente sottoposti a un carico in grado di indurre una deformazione residua in misura variabile (nell’esempio della figura +/0.30-0.60%). Si nota che, se la pallinatura è eseguita su superfici già soggette a sforzi residui di compressione (+0.30%, +0.60%), l’effetto della pallinatura risulta ancora maggiore.
In Figura 6 sono illustrati i risultati di analisi microstrutturali eseguite dall’autore del presente articolo e dal suo gruppo [2] su provini sottoposti a diversi trattamenti di pallinatura: NP indica i provini non pallinati, CSP indica i provini pallinati con intensità e copertura convenzionali, SSP indica una pallinatura eseguita con parametri ben superiori a quelli usuali, in particolare in termini di copertura (fino al 1000%).
Si nota che la pallinatura è in grado di indurre una riduzione delle dimensioni dei grani cristallini del materiale, con profondità interessate che aumentano all’aumentare della severità del trattamento. Ciò comporta un deciso incrudimento superficiale e determina un ulteriore miglioramento delle prestazioni a fatica, anche in presenza, a volta, di una accresciuta rugosità superficiale. Nel caso in esame, provini intagliati con pallinatura SSP hanno fatto registrare un miglioramento dell’80% del limite di fatica rispetto ai provini non pallinati, mentre la pallinatura convenzionale ha indotto un miglioramento di circa il 30%.
Facendo riferimento alle moderne tecnologie additive, in particolare al Laser Powder Bed Fusion (LPBF), la pallinatura si è dimostrata un eccellente trattamento per il post processamento di elementi così costruiti. In questi casi, la superficie che si ottiene è ricca di difettosità e caratterizzata da una rugosità elevata, fattori che da un lato riducono enormemente il limite di fatica del materiale nella condizione as-built, dall’altro rendono necessaria la definizione di parametri di trattamento diversi da quelli che si adottano usualmente. Anche in questi casi, tuttavia, la pallinatura si è dimostrata uno strumento efficace per ripristinare valori di resistenza a fatica adeguati.
In [3] vengono illustrati e interpretati i risultati di prove di fatica condotte su provini lisci ed intagliati (Kt=2.3) in lega AlSi10Mg prodotti con LPBF. Le prove hanno evidenziato che nel caso dei provini lisci, il miglioramento del limite di fatica è di quasi quattro volte rispetto al materiale non trattato. Se si considerano i provini intagliati, il miglioramento è ancora maggiore e si passa da circa 10 MPa a circa 100 MPa.
Altre applicazioni della pallinatura
Oltre ad applicazioni finalizzate al miglioramento della resistenza a fatica dei componenti, che costituiscono la maggioranza degli impieghi della pallinatura a livello industriale, ci sono altre applicazioni oggi di interesse, sia a livello di ricerca che per applicazioni industriali, nelle quali si sfrutta la sinergia dei tre effetti indotti (sforzi residui, finitura superficiale e modifiche microstrutturali) per ottenere una superficie funzionalizzata e allo stesso tempo per aumentarne la durabilità. Di seguito si riporta qualche esempio.
In [4] si descrivono prove di adesione cellulare e batterica eseguite su provini di acciaio AISI 316 trattati con pallinatura convenzionale e pallinatura severa. I risultati hanno indicato un effetto positivo della pallinatura, soprattutto severa, nel migliorare l’adesione delle cellule e nel diminuire quella batterica. In Figura 7 si riporta un grafico comparativo con l’area di adesione cellulare dopo un giorno di coltura.
In [5], invece, si considerano le batterie agli ioni di litio allo stato solido (ASSLiB) con elettroliti solidi inorganici (SE), caratterizzate dall’avere un elevato grado di sicurezza grazie alla non infiammabilità dell’elettrolita solido inorganico. Queste batterie sono considerate con interesse per equipaggiare i veicoli elettrici di prossima generazione. Tuttavia, per l’uso pratico in un veicolo elettrico, la batteria deve raggiungere una densità di energia e una potenza di uscita più elevate rispetto alle batterie agli ioni di litio esistenti con elettroliti organici liquidi. Al di là delle promettenti caratteristiche di questo tipo di batterie, punti critici per pensare a un loro utilizzo di massa restano la resistenza dell’interfaccia anodica e la densità di corrente critica di cortocircuito (CCD), che devono essere migliorate per ottenere una batteria ad alte prestazioni adatta ad applicazioni ad alta tecnologia.
A tal fine si usa rivestire la superficie di interfaccia con sottili film d’oro ottenuti per sputtering (spruzzamento catodico). Lo studio focalizza, invece, l’attenzione sull’importanza di modificare le caratteristiche morfologiche e meccaniche dell’interfaccia per migliorare le prestazioni dell’elettrodo. In particolare, viene proposto di applicare la pallinatura per modificare la finitura superficiale all’interfaccia e promuovere una migliore conducibilità elettrica.
I risultati mostrano che la pallinatura ha una grande influenza sulle prestazioni dell’elettrodo. Inoltre è possibile osservare come la pallinatura influenza positivamente le diverse proprietà considerate nello studio, dalla densità di corrente di corto circuito alla resistenza di interfaccia, migliorando le prestazioni rispetto al provino non trattato e anche rispetto a quello rivestito d’oro. In particolare, è interessante notare l’effetto sinergico della pallinatura applicata prima del rivestimento in oro: in tali condizioni le prestazioni dell’elettrodo raddoppiano rispetto ai casi in cui si considerano i singoli trattamenti.
Infine, la pallinatura è stata utilizzata per ottenere delle superfici con texture particolari [6], grazie alla costruzione e all’impiego di sfere con texture particolari, come quelle illustrate in Figura 8, in cui si nota come al variare del tipo di sfera sia possibile ottenere delle superfici con texture differenti che possono essere sfruttate sia a livello estetico che per ottenere proprietà funzionali particolari su lamiere o anche su materiali polimerici.
Conclusione
La pallinatura rappresenta oggi una tecnologia essenziale per l’industria moderna, in grado di migliorare significativamente le proprietà meccaniche e la durata dei componenti metallici. Oltre agli effetti sulla resistenza a fatica, sono oggi di interesse anche nuove applicazioni di questo trattamento che sfruttano la combinazione degli effetti indotti dal trattamento e che possono estenderne l’applicazione anche a nuovi settori industriali. Alcune di queste nuove possibili applicazioni sono state presentate in queste righe ma non esauriscono le potenzialità della pallinatura, trattamento che, a differenza di altri processi per il trattamento delle superfici, risponde alle moderne esigenze di sostenibilità ambientale.
Bibliografia
[1] J. Almen Residual Stresses and Fatigue in Metals. McGraw-Hill (1963).[2] S. Bagherifard et al. Nanoscale surface modification of AISI 316L stainless steel by severe shot peening. Materials&Design, 102 (2016) 68–77.
[3] E. Maleki et al. Fatigue behaviour of notched laser powder bed fusion AlSi10Mg after thermal and mechanical surface post-processing. Materials Science & Engineering A 829 (2022) 142145.
[4] S. Bagherifard et al. The influence of nanostructured features on bacterial adhesion and bone cell functions on severely shot peened 316L stainless steel. Biomaterials 73 (2015) 185-197.
[5] M. Kodama , K. Takashima , S. Hirai. Improvement of lithium-metal electrode performance of all-solid-state batteries by shot peening on solid-electrolyte surface. Journal of Power Sources 537 (2022) 231556.
[6] A. Heydari Astaraee et al. Adapting Shot Peening for Surface Texturing Using Customized Additive Manufactured Shots. Adv. Eng. Mater. 25 (2023) 2201730