Le ceramiche strutturali sono materiali avanzati progettati per resistere a carichi elevati, temperature estreme e ambienti chimicamente aggressivi, rendendoli ideali per applicazioni in settori come l’aerospazio, l’industria automobilistica e l’ingegneria di precisione. Al di là delle ceramiche, sta attirando sempre più interesse, in termini di ricerca tecnologica e industria avanzata, anche il nitruro di silicio (Si₃N₄), specie quando combinato con il nitruro di boro esagonale (h-BN), per via delle loro caratteristiche fortemente complementari.
A differenza delle ceramiche tradizionali (come porcellana, terracotta e gres), impiegate principalmente per scopi estetici, edilizi o domestici, le ceramiche strutturali offrono prestazioni meccaniche, termiche e chimiche molto superiori. Questa distinzione deriva sia dalla composizione sia dai processi di produzione avanzati, che migliorano durezza, resistenza all’usura e stabilità termica, spesso a discapito della lavorabilità.
Tra le ceramiche industriali piuttosto diffuse (Fig. 1), è possibile segnalare :
- Allumina (Al₂O₃) è una delle ceramiche tecniche più utilizzate grazie alla sua elevata durezza, resistenza all’abrasione e isolamento elettrico. Viene impiegata in componenti elettronici, cuscinetti ad alta precisione, rivestimenti antiusura e bioceramiche per impianti medicali. È apprezzata per la sua stabilità chimica, ma può risultare fragile e difficile da lavorare.
- Zirconia (ZrO₂) è nota per la sua tenacità alla frattura superiore rispetto ad altre ceramiche, grazie alla capacità di trasformazione di fase che ne impedisce la propagazione delle cricche. Ha anche un’elevata resistenza all’usura e all’ossidazione ed è utilizzata in strumenti da taglio, componenti per motori, protesi dentali e biomedicali. Tuttavia, la sua stabilità termica è inferiore rispetto ad altre ceramiche avanzate.
- Carburo di Silicio (SiC) è una ceramica estremamente dura e resistente alla corrosione, particolarmente efficace in ambienti ad alta temperatura e condizioni abrasive. È ampiamente usato in dischi freno per auto sportive, rivestimenti di forni, scambiatori di calore e applicazioni aerospaziali. Grazie alla sua conducibilità termica elevata, è adatto anche per componenti elettronici ad alta potenza.
- Cordierite è una ceramica nota per la sua eccellente resistenza agli shock termici e la bassa espansione termica. È comunemente utilizzata in convertitori catalitici per automobili, forni industriali e piastre refrattarie. Sebbene meno resistente meccanicamente rispetto ad altre ceramiche, la sua capacità di resistere a rapide variazioni di temperatura la rende ideale per applicazioni termiche.
- Mullite è una ceramica con buon compromesso tra resistenza meccanica e stabilità termica, utilizzata in mattoni refrattari, rivestimenti per forni e isolatori ad alta temperatura. La sua combinazione di bassa densità e resistenza chimica la rende un materiale adatto per applicazioni strutturali a temperature elevate.
- Steatite è una ceramica economica con buone proprietà dielettriche e resistenza termica, usata principalmente in isolatori elettrici e componenti per antenne ad alta frequenza. Sebbene meno resistente meccanicamente rispetto ad altre ceramiche avanzate, la sua facilità di lavorazione la rende una scelta pratica per molte applicazioni elettroniche.
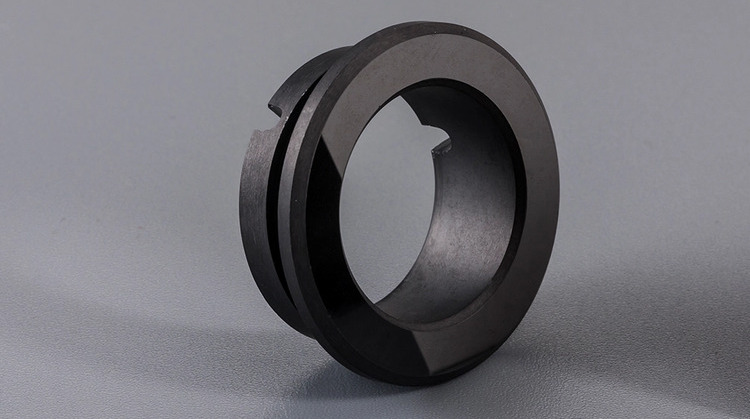
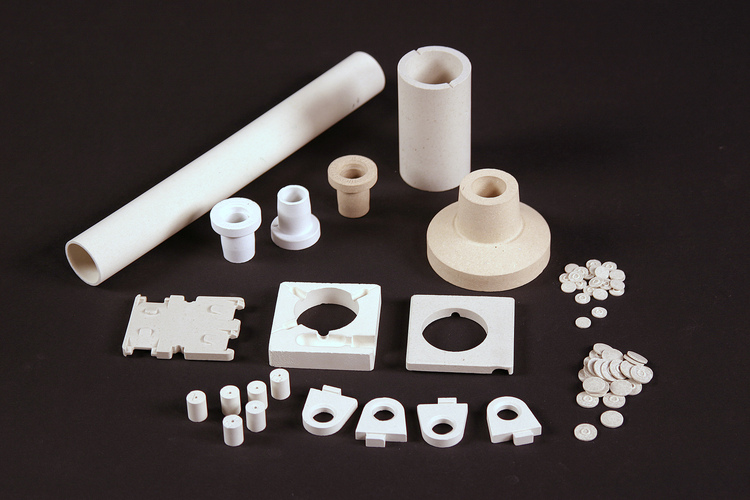
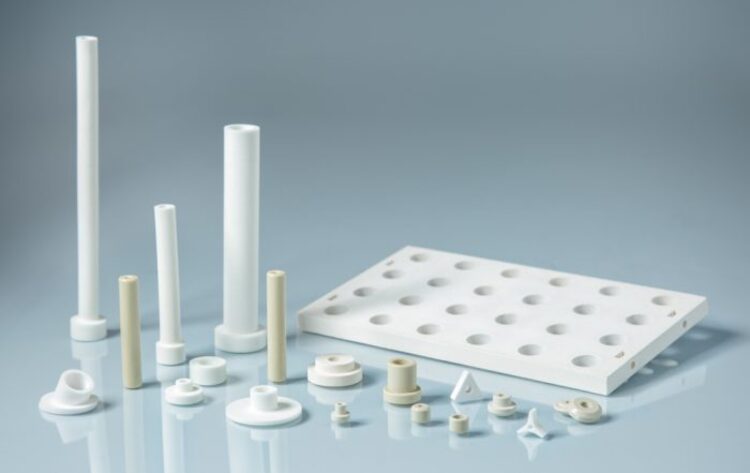
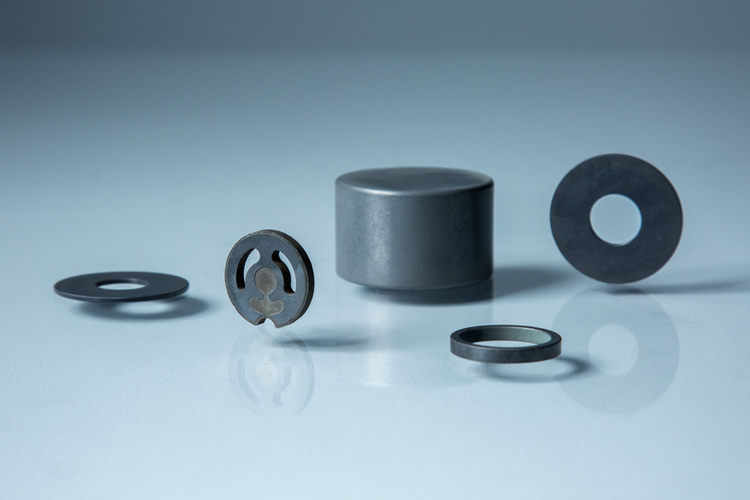
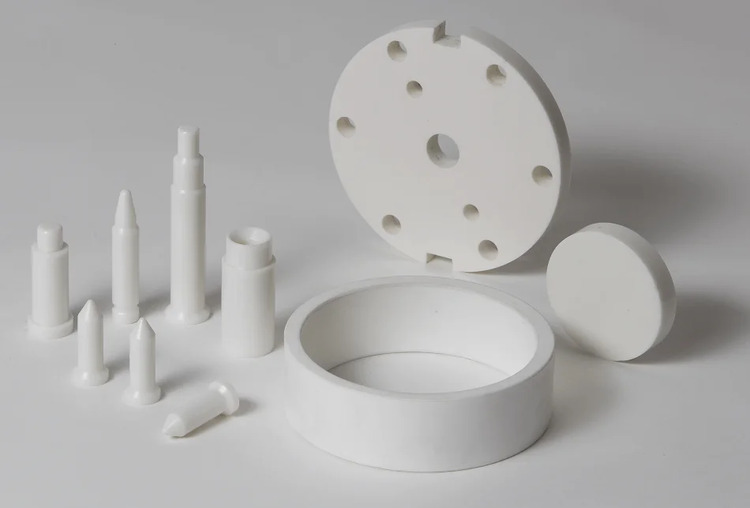
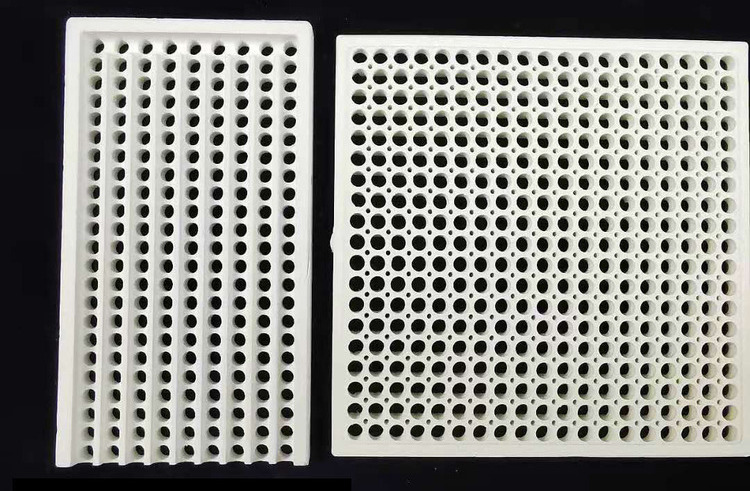
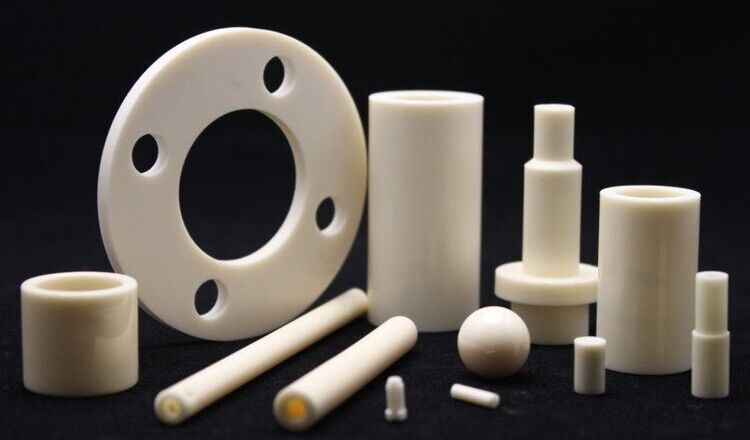
Al di là delle presentate ceramiche, sta attirando sempre più interesse, in termini di ricerca tecnologica e industria avanzata, anche il nitruro di silicio (Si₃N₄), specie quando combinato con il nitruro di boro esagonale (h-BN), per via delle loro caratteristiche fortemente complementari (Fig. 2).
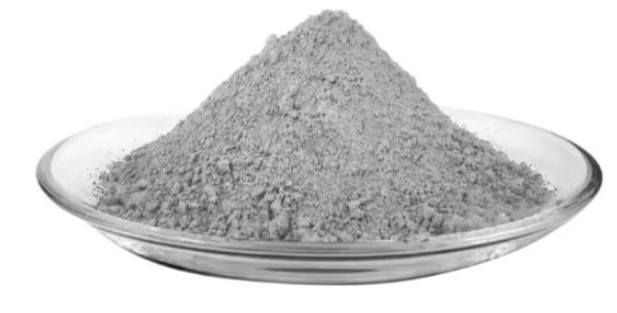
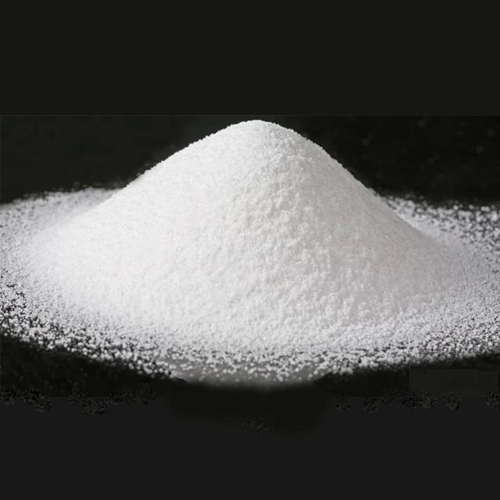
Il nitruro di silicio (Si₃N₄) è noto per la sua elevata resistenza meccanica, la tenacità alla frattura superiore rispetto ad altre ceramiche strutturali e l’ottima resistenza agli shock termici, che lo rende adatto per componenti sottoposti a carichi elevati e variazioni di temperatura improvvise. Il nitruro di boro esagonale (h-BN), invece, possiede una struttura stratificata simile alla grafite, che gli conferisce eccezionali proprietà lubrificanti solide e una maggiore facilità di lavorazione rispetto ad altre ceramiche. L’integrazione di h-BN nei compositi ceramici a base di Si₃N₄ permette di migliorarne la lavorabilità, pur mantenendo un equilibrio tra proprietà meccaniche e tribologiche.
Rispetto ad altre ceramiche, il Si₃N₄ e l’h-BN presentano una combinazione di caratteristiche davvero unica e promettente. L’allumina (Al₂O₃) è apprezzata, ad esempio, come detto, per la sua durezza e resistenza alla corrosione, ma è meno tenace e più difficile da lavorare rispetto al Si₃N₄. La zirconia (ZrO₂), d’altra parte, è molto resistente agli impatti e possiede un’elevata tenacità, ma ha una stabilità termica inferiore rispetto al Si₃N₄. Il carburo di silicio (SiC) eccelle in durezza e resistenza chimica, rendendolo ideale per ambienti corrosivi, ma soffre di una fragilità tipica delle ceramiche tradizionali.
L’obiettivo di questo studio è esplorare il comportamento meccanico e tribologico di compositi ceramici a base di Si₃N₄ e h-BN, analizzandone le prestazioni in termini di resistenza alla flessione, durezza, tenacità alla frattura e lavorabilità. L’uso di materiali ceramici innovativi, ottimizzati per migliorare le operazioni di finitura superficiale e ridurre i costi di produzione, rappresenta una sfida chiave per l’industria manifatturiera avanzata (Tabella 1).
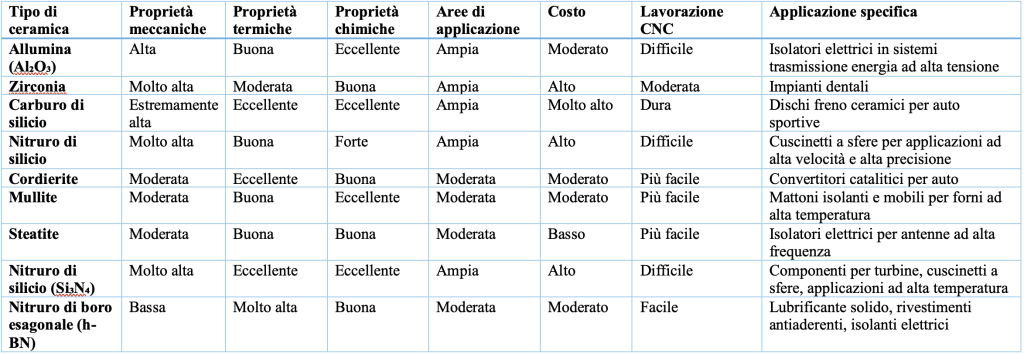
A questo scopo è importante considerare già da subito che il costo finale di un componente in ceramica strutturale è fortemente influenzato dalla fase di lavorazione di finitura necessaria per raggiungere le tolleranze dimensionali richieste, fino ad arrivare a rappresentare il 50% del costo complessivo (Fig. 3). Questo elevato impatto economico rappresenta uno dei principali ostacoli alla diffusione su larga scala di questi materiali nel settore industriale.
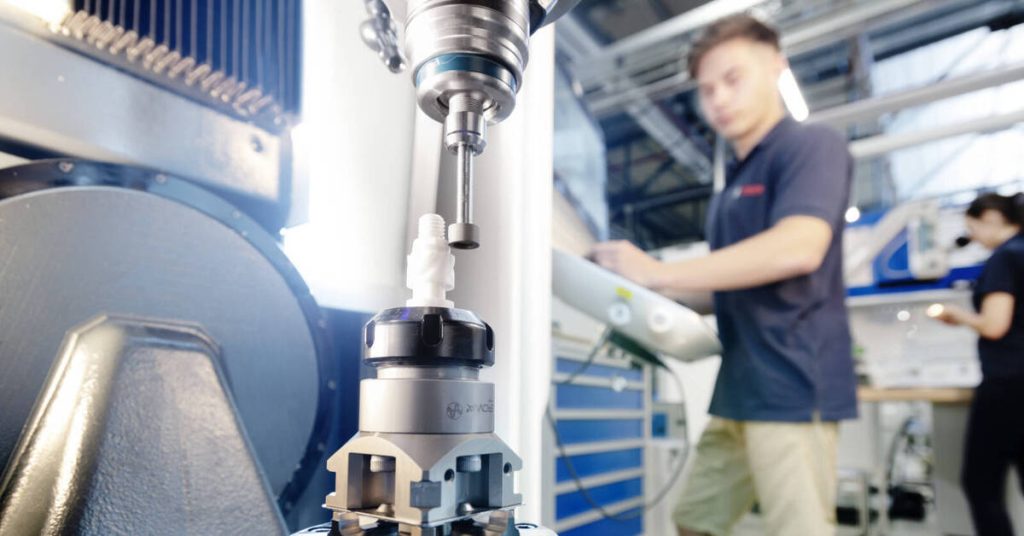
L’alto costo della lavorazione è principalmente dovuto alla straordinaria durezza delle ceramiche strutturali, caratteristica che, se da un lato ne garantisce eccellenti proprietà meccaniche e resistenza all’usura, dall’altro rende necessaria l’adozione di utensili altamente specializzati, come quelli con inserti diamantati. L’uso di tali utensili comporta spese significative, sia in termini di materiali che di tempi di lavorazione, incidendo pesantemente sui costi di produzione.
Una possibile soluzione per mitigare questi costi è rappresentata dall’impiego di utensili realizzati con materiali meno pregiati, come il carburo di tungsteno (WC) verso processi produttivi più efficienti (Fig. 4). Tuttavia, per rendere questa strategia applicabile su larga scala, è necessario migliorare la lavorabilità dei ceramici strutturali, riducendone la resistenza alla lavorazione senza comprometterne in modo significativo le proprietà meccaniche.
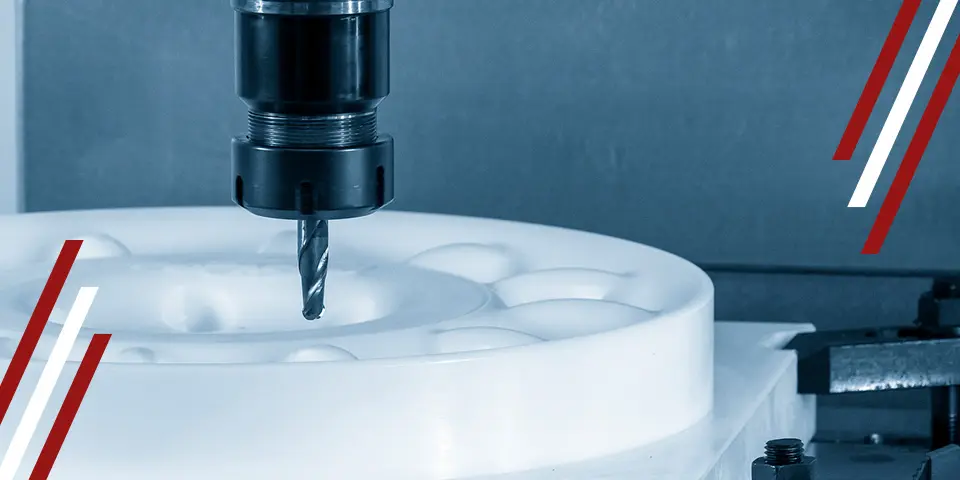
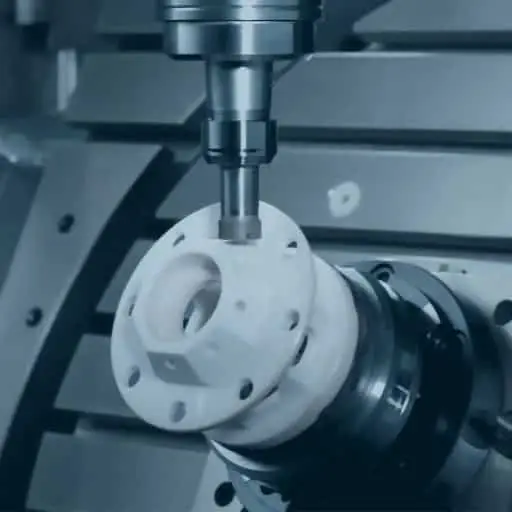
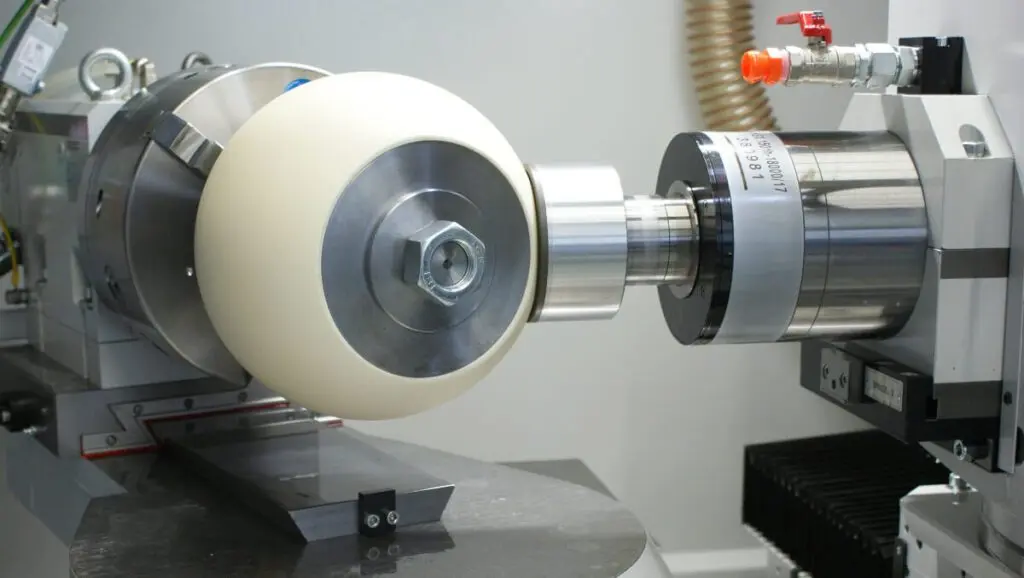
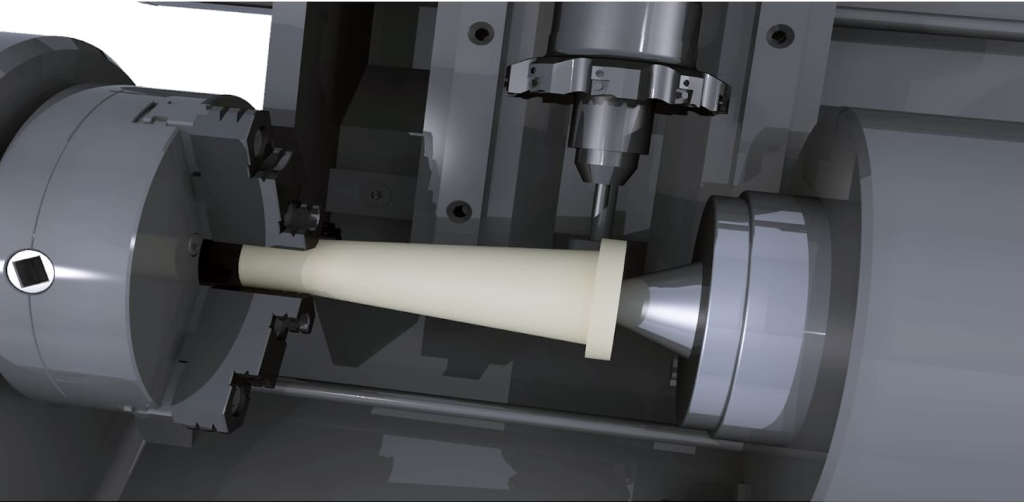
Una delle strategie più promettenti in questo contesto è l’introduzione, all’interno della matrice ceramica, di una fase lubrificante che possa facilitare la lavorazione meccanica. In particolare, l’aggiunta di nitruro di boro nella sua forma esagonale (h-BN) si è dimostrata efficace nel migliorare significativamente la lavorabilità di alcuni ceramici avanzati, come il nitruro di silicio (Si₃N₄). Questo risultato è attribuibile alla struttura cristallina dell’h-BN, che presenta piani di sfaldamento simili a quelli della grafite, conferendo al materiale proprietà di lubrificazione solida (Fig. 5).
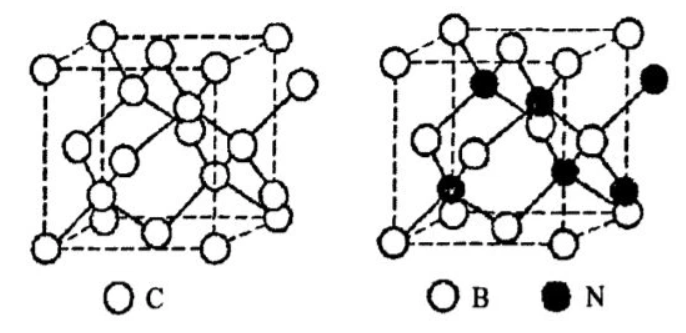
L’introduzione di h-BN nella matrice ceramica porta diversi benefici dal punto di vista della lavorazione. Innanzitutto, riduce l’attrito tra l’utensile e il materiale da lavorare, consentendo un’usura minore degli utensili e una maggiore efficienza nei processi di finitura. Inoltre, facilita la rimozione del materiale durante le operazioni di taglio e rettifica, permettendo di aumentare la velocità di lavorazione senza compromettere la qualità del pezzo finito.
Tuttavia, sebbene l’aggiunta di h-BN migliori la lavorabilità, è fondamentale valutare attentamente il suo effetto sulle proprietà meccaniche complessive del composito. Infatti, mentre la presenza di questa fase facilita i processi di finitura, può anche ridurre la durezza, la resistenza meccanica e il modulo elastico del materiale, aspetti che devono essere ottimizzati in funzione dell’applicazione finale. Per questo motivo, la progettazione di ceramici strutturali modificati con h-BN richiede un attento bilanciamento tra miglioramento della lavorabilità e mantenimento delle prestazioni meccaniche necessarie per l’utilizzo in condizioni operative severe.
La struttura cristallina del nitruro di boro esagonale (h-BN) è caratterizzata dalla presenza di piani di sfaldamento facilmente scorrevoli, un comportamento simile a quello della grafite. Questa peculiarità conferisce all’h-BN proprietà di lubrificante solido, riducendo l’attrito tra le superfici in contatto e facilitando i processi di lavorazione meccanica.
L’integrazione di h-BN in una matrice ceramica strutturale offre vantaggi significativi in termini di lavorabilità. In primo luogo, la presenza di questa fase lubrificante riduce il coefficiente di attrito tra il materiale ceramico e l’utensile di lavorazione, contribuendo a un minore surriscaldamento e a una riduzione dell’usura dell’utensile stesso. In secondo luogo, facilita la rimozione del materiale durante la lavorazione, consentendo di aumentare la velocità di taglio e ridurre i tempi di finitura. Questi effetti combinati rendono i compositi ceramici contenenti h-BN particolarmente interessanti per applicazioni in cui la lavorabilità è un fattore critico.
Per studiare in modo più approfondito l’interazione tra utensili in carburo di tungsteno (WC) e ceramici strutturali contenenti h-BN, sono stati sviluppati materiali compositi nel sistema (Si₃N₄, h-BN). L’obiettivo è generale è quello di valutare le prestazioni tribologiche di questi materiali attraverso test controllati di usura e attrito in presenza di una controparte in WC, al fine di comprendere meglio il comportamento della superficie durante le operazioni di finitura e rettifica. Sono stati realizzati due compositi a base di nitruro di silicio e nitruro di boro, oltre a una matrice di riferimento.
La matrice di partenza, denominata R1, è costituita per il 95% in volume da Si₃N₄ e per il 5% da MoSi₂. L’inclusione di molibdeno disiliciuro (MoSi₂) è nota per il suo effetto positivo sulle proprietà meccaniche del nitruro di silicio, in particolare per l’incremento della tenacità alla frattura e della resistenza all’ossidazione ad alta temperatura. L’uso di MoSi₂ come agente di rinforzo permette di migliorare la stabilità del materiale in condizioni operative severe, riducendo il degrado dovuto all’ossidazione e aumentando la durata dei componenti. Grazie a questa combinazione di elementi, il materiale di base R1 costituisce un riferimento ideale per confrontare le prestazioni dei compositi contenenti h-BN e valutare in che misura l’aggiunta di questa fase lubrificante influisce sulla lavorabilità e sulle proprietà meccaniche complessive.
Per valutare l’influenza della dimensione degli agglomerati di nitruro di boro esagonale (h-BN) sulle proprietà meccaniche e sulla lavorabilità del materiale, sono stati prodotti due compositi con la stessa frazione volumetrica di h-BN, pari al 20%. La differenza tra i due risiede esclusivamente nella dimensione delle particelle di h-BN disperse nella matrice: nel primo composito, denominato C1, la dimensione media degli agglomerati è di 0,7 µm, mentre nel secondo, indicato come C2, essa varia tra 5 e 7 µm.
Questa scelta consente di analizzare l’effetto della distribuzione granulometrica del rinforzo sulla lavorabilità del materiale, poiché la dimensione e l’omogeneità della dispersione delle particelle possono influenzare sia il comportamento meccanico del composito sia la sua risposta ai processi di finitura superficiale. Tutti i materiali sono stati ottenuti a partire da polveri commerciali, evitando metodi di sintesi particolarmente complessi o costosi. L’obiettivo di questa scelta è garantire la possibilità di un’eventuale trasposizione industriale dei risultati, riducendo le difficoltà legate alla scalabilità del processo di produzione.
La densificazione dei materiali è stata realizzata mediante pressatura uniassiale a caldo (hot-pressing), tecnica che consente di ottenere un’elevata compattezza del materiale riducendo al minimo la porosità residua. La matrice di riferimento R1 ha raggiunto una densità pari al 100% della sua densità teorica, mentre i compositi C1 e C2 (con dispersione fine e grossolana, rispettivamente) hanno mostrato valori leggermente inferiori, compresi tra il 94% e il 95%. Questi risultati sono coerenti con l’aspettativa che l’aggiunta di h-BN possa limitare il grado di compattazione rispetto alla matrice pura di nitruro di silicio.
Dai materiali ottenuti, sono stati ricavati, tramite taglio e rettifica, campioni per la caratterizzazione meccanica. I test sono stati eseguiti presso CNR-ISSMC Istituto di Scienza, Tecnologia e Sostenibilità per lo sviluppo dei Materiali Ceramici,nei propri laboratori di Faenza, secondo procedure standardizzate per garantire l’affidabilità dei dati. In particolare, le proprietà meccaniche sono state valutate attraverso le seguenti prove:
- Durezza Vickers (HV): misurata applicando un carico di 9,81 N (Fig. 6).
- Modulo di Young (E): determinato mediante misurazione della frequenza di risonanza in flessione.
- Resistenza alla flessione (σf): determinata su provini di dimensioni 25 × 4 × 3 mm³ mediante prova di flessione a quattro punti, utilizzando un dispositivo con distanze di appoggio di 20 mm (inferiori) e 10 mm (superiori). Il test è stato condotto su una macchina Zwick Z050 con una velocità della traversa di 0,5 mm/min (Fig. 7).
- Tenacità alla frattura (KIc): misurata con il metodo Chevon Notched Bar utilizzando lo stesso dispositivo della prova di flessione, ma con una velocità della traversa ridotta a 0,05 mm/min.
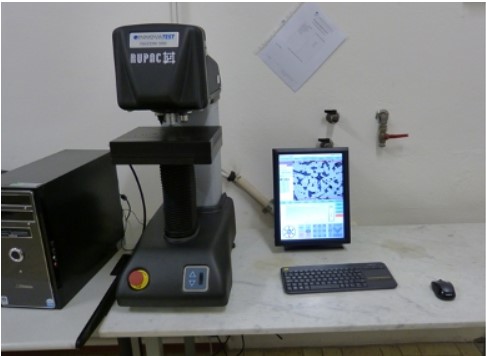
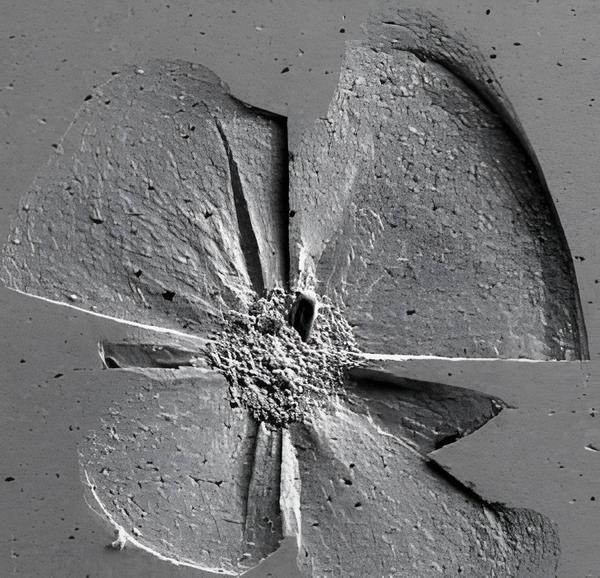
I risultati ottenuti sono riportati in tabella e comprendono il valore medio delle misurazioni, accompagnato da una deviazione standard per fornire un’indicazione della dispersione dei dati. L’analisi di questi dati permetterà di comprendere in che misura la dimensione degli agglomerati di h-BN influisca sulle proprietà meccaniche e sulla lavorabilità del materiale, fornendo indicazioni utili per l’ottimizzazione della composizione e del processo produttivo.
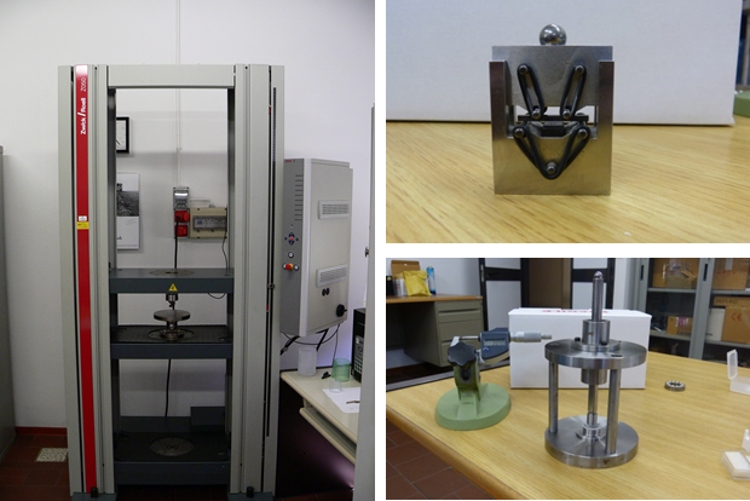
Come è possibile osservare in Tabella 2 e graficamente in Figura 8, l’introduzione del BN penalizza, rispetto alla matrice R1, tutte le proprietà meccaniche, influenzando poco la tenacità (KIc) ma molto la durezza (HV), il modulo di Young (E) e la resistenza alla flessione (σf).
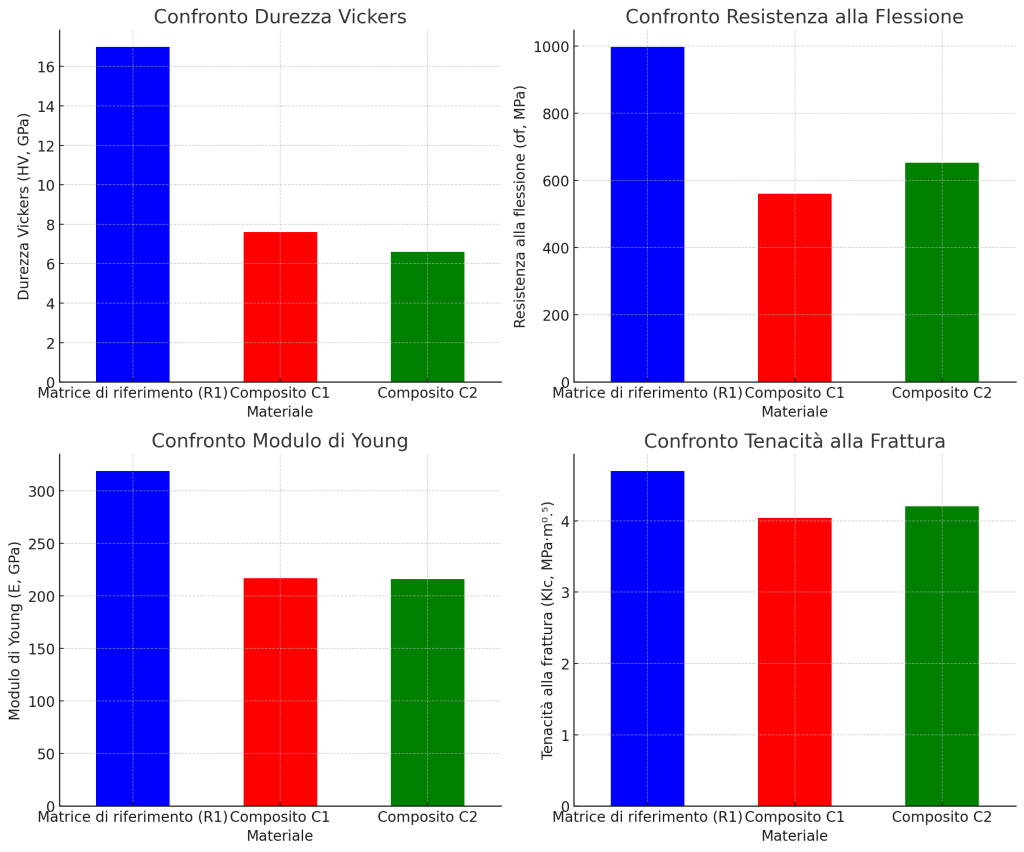
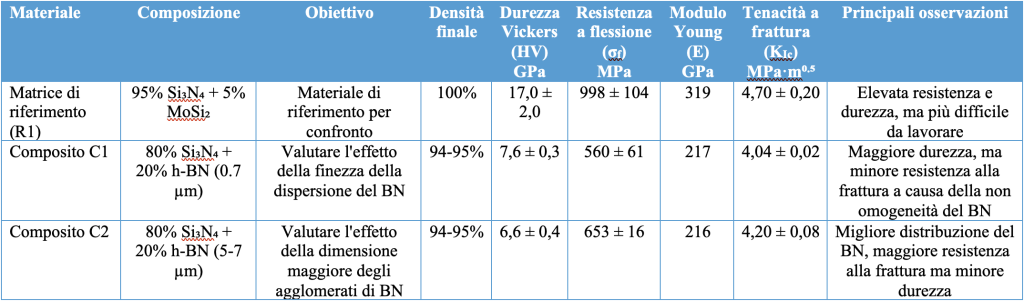
Gli effetti della dimensione degli agglomerati di BN sulle proprietà meccaniche dei due compositi non sono univoci. Il composito C1, quello con gli agglomerati di BN più piccoli, ha resistenza alla frattura e tenacità statisticamente inferiori al composito C2, quello con gli agglomerati di BN più grandi, ma durezza superiore. Dal punto di vista microstrutturale, si è osservato che il composito C1 ha una dispersione non omogenea del BN presentando diverse zone di accumulo di BN con dimensioni molto maggiori della media. Ciò è dovuto alla loro ridotta dimensione iniziale che li fa tendere quasi naturalmente all’agglomerazione. Questo giustificherebbe la maggior durezza rispetto a C2: essendo il BN non omogeneamente distribuito, i test di durezza, eseguiti su scala molto piccola, dimensioni dell’impronta di pochi µm, hanno saggiato volumi di materiale con una frazione volumetrica di BN inferiore a quella nominale. Inoltre, la non omogenea distribuzione del BN è anche responsabile del basso valore di resistenza alla frattura di C1 rispetto a C2: i difetti all’origine delle fratture sono stati identificati da analisi frattografica come agglomerati di BN con dimensioni di decine di µm.
Questi risultati suggeriscono che i compositi Si₃N₄-hBN potrebbero essere particolarmente adatti per applicazioni in cui è richiesta una lavorabilità migliorata, senza sacrificare eccessivamente la resistenza meccanica offrendo un valido compromesso per rafforzare la diffusione dei componenti in ceramica strutturale. Alcuni settori potenzialmente interessati includono, ad esempio:
- Industria aerospaziale – Componenti strutturali che richiedono leggerezza, resistenza al calore e buona lavorabilità, come nel caso di parti dei propulsori di razzi (Fig. 9A).
- Meccanica di precisione – Cuscinetti e parti di macchinari ad alta velocità, dove è necessario un equilibrio tra resistenza meccanica e facilità di fabbricazione.
- Utensili e rivestimenti antiusura – Dove le proprietà lubrificanti dell’h-BN possono ridurre l’attrito e migliorare le prestazioni tribologiche, come nel caso dei cuscinetti (Fig. 9B).
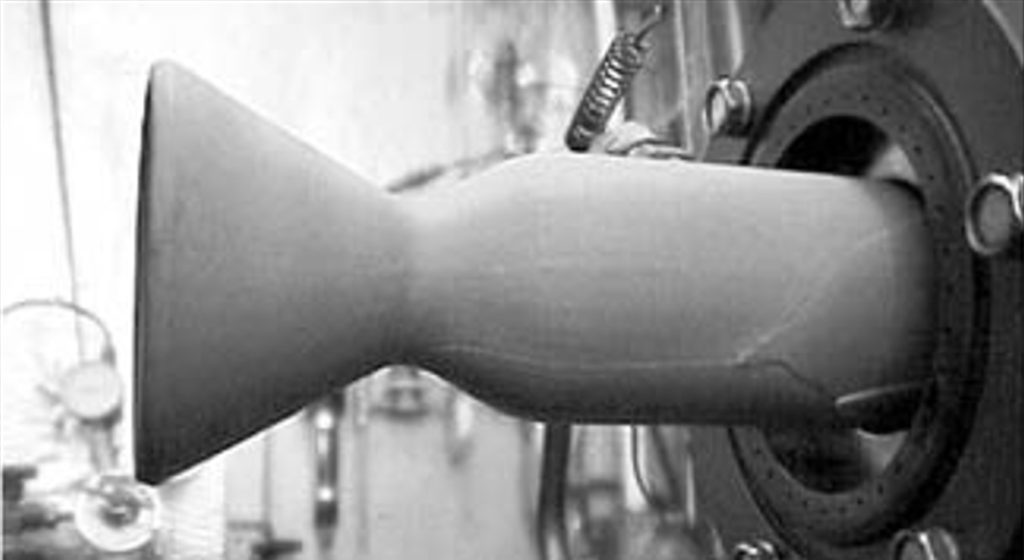
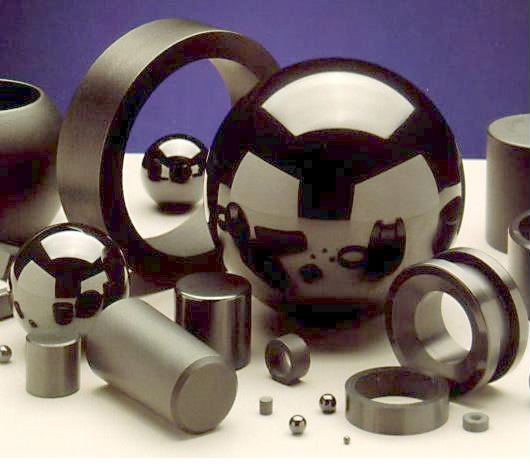
Tuttavia, l’ottimizzazione della distribuzione delle particelle di BN rimane un aspetto chiave per migliorare ulteriormente le prestazioni di questi materiali. Un’eventuale direzione futura potrebbe essere l’impiego di tecniche avanzate di dispersione o la combinazione di differenti dimensioni di h-BN per migliorare contemporaneamente durezza e tenacità alla frattura.
L’integrazione di questi materiali nella produzione industriale dipenderà infine da un’attenta valutazione del rapporto costo-beneficio, considerando che la riduzione dei costi di lavorazione potrebbe compensare in parte la diminuzione delle proprietà meccaniche.
Riferimenti
Studio preliminare realizzato dal CNR-ISSMC (ref. Dott. S. Guicciardi), per conto del MATMEC, Laboratorio sui Materiali Avanzati dell’Emilia Romagna. Maggior dettagli disponibili in
- V. Medri, et al., “Influence of different BN grades on sintering behaviour, microstructure and properties of machinable Si3N4-MoSi2-BN composites. Advanced Engineering Materials.