Con l’implementazione di una nuova linea combo Fagor, Alluminio di Qualità rafforza la propria posizione nel mercato della trasformazione di semilavorati in lega di alluminio, ampliando capacità produttive e potenzialità tecniche
Nel settore della trasformazione dei semilavorati in alluminio, la competitività dipende dalla capacità di rispondere con precisione e rapidità alle esigenze di mercati sempre più specializzati. In questo contesto, l’innovazione tecnologica non è solo un’opportunità, ma una necessità per mantenere il posizionamento competitivo. Le tecnologie di taglio si sono evolute verso maggiore flessibilità operativa, uso efficiente dei materiali e riduzione degli scarti. Il crescente impiego dell’alluminio in settori tecnologici ha accelerato questa tendenza, imponendo standard più elevati e specifiche più rigorose.
La necessità di lavorare geometrie complesse con precisione su spessori variabili ha spinto lo sviluppo di sistemi di taglio avanzati, capaci di superare i limiti delle tecnologie tradizionali. In questo scenario, Alluminio di Qualità, società del Gruppo Cauvin, ha investito in una nuova linea combo del produttore spagnolo Fagor Arrasate. Una svolta significativa per l’azienda che, con quasi quattro decenni di esperienza, si è affermata tra i principali centri servizi italiani per la distribuzione e la lavorazione di laminati ed estrusi in leghe di alluminio per molteplici settori industriali.
Con sedi a Villafranca di Verona (VR), Vignole Borbera (AL) e Campi Bisenzio (FI), dispone di 14.000 mq e una capacità di taglio annuale superiore alle 15.000 tonnellate. L’acquisizione della nuova linea rappresenta un passaggio fondamentale in una strategia di crescita che combina tradizione ed evoluzione tecnologica, ampliando il raggio d’azione in settori chiave come automotive, aerospace e cantieristica navale.
Ampliamento delle capacità di taglio per nuovi segmenti di mercato
L’investimento nella nuova linea Fagor risponde a precise logiche industriali e si inserisce nel piano di sviluppo di Alluminio di Qualità. La duplice valenza dell’impianto, che integra funzionalità di Cut-To-Length e Laser Blanking con larghezza massima di 2.150 mm, rappresenta una decisa espansione rispetto ai limiti di capacità di taglio standard, fermi a 1.550 mm nella maggior parte dei centri servizi italiani ed europei.
Questa scelta tecnologica, effettuata da Alluminio di Qualità, nasce dall’evoluzione del mercato dei laminati in alluminio, con produttori che negli anni hanno ampliato la larghezza dei coil fino a 2.500 mm. Tale tendenza è stata principalmente trainata dalla domanda proveniente dai settori aerospace e automotive. La sezione Cut-To-Length consente di tagliare trasversalmente coil in lega di alluminio con spessori compresi tra 0,5 e 6 mm, producendo lamiere con lunghezza fino a 8 metri.
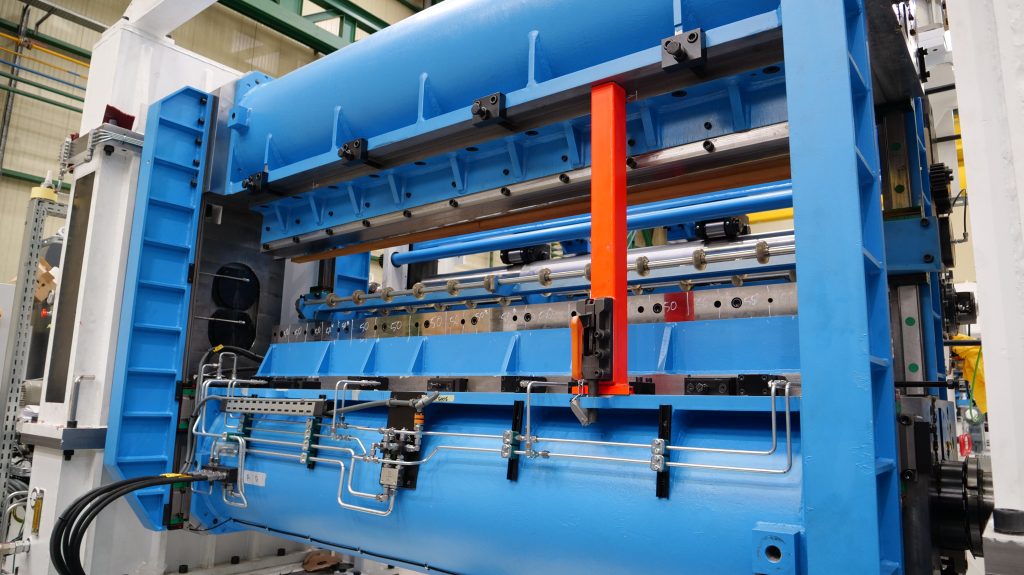
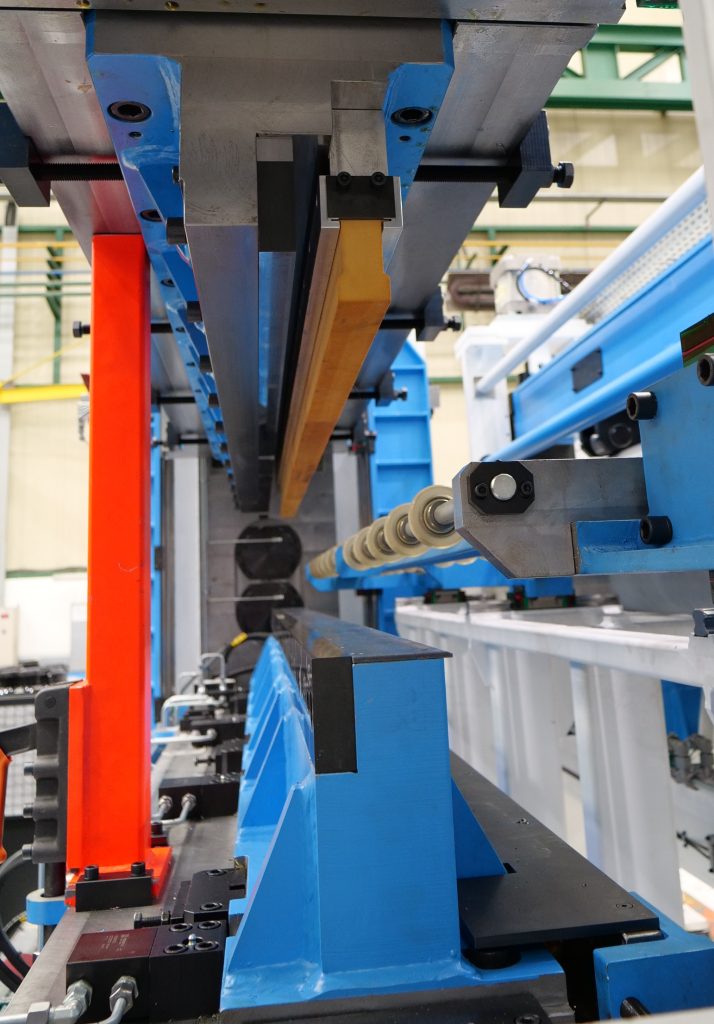
La possibilità di applicare film protettivi in PVC, sia sul lato superiore che inferiore del materiale, eventualmente con carta interposta, permette inoltre di soddisfare le esigenze di una vasta gamma di applicazioni industriali, dal settore automotive fino all’edilizia e alle costruzioni.
La parte funzionale di Laser Blanking rappresenta invece un importante consolidamento del posizionamento di Alluminio di Qualità nel settore automotive italiano, dove l’azienda si distingue come unico centro servizi specializzato nella trasformazione di leghe serie 6XXX a trattamento termico e leghe serie 5XXX, omologate dai principali costruttori automobilistici e fornitori Tier1 e Tier2.
Con una larghezza operativa fino a 2.150 mm e la tecnologia “any shape”, il sistema laser permette di realizzare sagomati complessi senza i vincoli degli stampi tradizionali, fondamentali per la produzione di componenti Body in White (BIW), prototipi e pre-serie. Questa tecnologia laser consente modifiche immediate al design senza costruire o aggiornare costosi stampi fisici.
La rilevanza strategica di questo investimento è ulteriormente evidenziata dal fatto che si tratta dell’unica linea con queste caratteristiche presente in Italia e la terza installata dai Centri Servizi a livello europeo; un asset distintivo, quindi, che rafforza le partnership esistenti e apre ad Alluminio di Qualità nuove opportunità nei mercati esteri.
Vantaggi tecnologici e produttivi del taglio laser da coil
L’implementazione della tecnologia di Laser Blanking offre vantaggi operativi e qualitativi rispetto ai processi tradizionali, che prevedono fasi successive di spianatura del coil, taglio in bandelle, taglio laser foglio a foglio e stampaggio del sagomato. Questa frammentazione implica spesso il coinvolgimento di più attori nella filiera, generando scarti e difficoltà nel realizzare cicli chiusi per il recupero e il riciclo degli sfridi.
La soluzione Fagor adottata da Alluminio di Qualità integra più fasi in un unico processo, migliorando la gestione dei materiali, attraverso la riduzione degli scarti e il loro completo riciclo in fonderia grazie a cicli chiusi con i produttori, e riducendo i costi di attrezzaggio in fase di stampaggio. Il taglio laser da coil garantisce un bordo di qualità superiore e precisione millimetrica per geometrie complesse, non ottenibili con i tradizionali processi di blanking a pressa.
Dal punto di vista produttivo, questa tecnologia permette di ridurre i tempi di setup, eliminando operazioni di cambio stampo e ottimizzando la lavorazione. L’assenza di utensili specifici rende più rapido l’attrezzaggio e consente cambi di produzione in tempi ridotti, con evidenti benefici in termini di flessibilità operativa. L’impiego di software avanzati per il nesting ottimizza il materiale, riducendo sprechi e incrementando la produttività.
La digitalizzazione dei processi permette un controllo accurato delle operazioni, con monitoraggio continuo della qualità e ottimizzazione in tempo reale. Anche dal punto di vista della sostenibilità ambientale, la nuova linea offre vantaggi significativi, con un consumo energetico inferiore rispetto ai sistemi convenzionali e una riduzione degli scarti di lavorazione.
Questi aspetti si allineano alla politica di sostenibilità adottata da Alluminio di Qualità, che nel 2024 ha pubblicato il suo secondo Bilancio di Sostenibilità, evidenziando l’impegno nella creazione di valore condiviso attraverso una crescita sostenibile.
Opportunità di mercato e prospettive future tra digitalizzazione e sostenibilità
L’adozione della nuova tecnologia apre all’azienda nuove opportunità di mercato, consentendole di ampliare la propria offerta verso settori che richiedono elevata precisione e flessibilità produttiva. Oltre all’impiego specifico nel settore automotive, la Laser Blanking Line trova applicazione in ambiti che prevedono fasi di stampaggio del laminato a freddo in lega di alluminio, in particolare per progetti in fase prototipale o di pre-serie.
In questi contesti, l’utilizzo del taglio laser consente di conseguire importanti risparmi in termini di costi di attrezzaggio e riduzione degli scarti, oltre a semplificare le fasi di terziarizzazione del taglio. La capacità di gestire lavorazioni su misura risponde efficacemente alle esigenze di settori altamente specializzati, dove la richiesta di componenti in alluminio di alta precisione è in costante crescita.
La possibilità di operare con spessori e geometrie variabili rappresenta poi un importante vantaggio competitivo rispetto alle tecnologie tradizionali, aumentando il valore percepito dei semilavorati di Alluminio di Qualità sul mercato e consentendo all’azienda di consolidare la propria presenza in un contesto sempre più sfidante e globalizzato.
L’acquisizione della linea combo Fagor rappresenta dunque solo un primo passo all’interno di una strategia di crescita più ampia, che prevede ulteriori investimenti in tecnologie innovative e digitalizzazione dei processi produttivi. L’adozione di strumenti avanzati per il controllo della qualità e di sistemi automatizzati per la gestione della produzione consentirà di migliorare ulteriormente la competitività aziendale, garantendo livelli di efficienza e precisione sempre più elevati.
In particolare, l’assistente specifico per leghe di alluminio è una tecnologia in grado di valutare la planarità del nastro in tempo reale durante il processo di spianatura, calcolare e regolare automaticamente la bancata rulli per eliminare le incongruenze di planarità, modificando opportunamente l’inclinazione della livellatrice e il posizionamento del supporto. La movimentazione della lamiera nell’area di taglio sfrutta un trasportatore telescopico dinamico, X-GAP, sincronizzato con la testa laser e capace di estendersi fino a 500 mm, per l’evacuazione dei pezzi finiti e dello scarto di lavorazione. Il sistema di scarico dei pezzi sagomati impiega un robot antropomorfo per il posizionamento su doppio box dei componenti fino a 4 m di lunghezza e un impilatore “no-stop” per lo scarico di elementi fino a 8 m di lunghezza. Questo impilatore è stato progettato appositamente per materiali di medio spessore e delicati. I rulli si inclinano verso il basso (e non su un piano orizzontale) in modo da evitare l’attrito tra le superfici dei laminati e proteggere la loro qualità superficiale. La lamiera è sostenuta da ruote in poliuretano che impediscono la comparsa di qualsiasi tipo di segno sulla sua superficie.