Sdoganata la stampa 3D nell’ambito della prototipazione rapida, le tecnologie additive ormai consolidate entrano a buon diritto nei flussi produttivi industriali per la realizzazione di pezzi definitivi.
“Perché conviene integrare la Stampa 3D nel ciclo produttivo?” è il titolo di un webinar organizzato dal Gruppo Editoriale Tecniche Nuove, in collaborazione con HP, al quale hanno partecipato significativi esponenti del mondo produttivo e della ricerca universitaria, portando la loro testimonianza su quello che si può effettivamente fare con la manifattura additiva inserita nell’ambito del processo produttivo.
Ne risulta un quadro incoraggiante, dal quale emerge come la flessibilità dei procedimenti additivi – se ben impiegata, ben inserita nel flusso di produzione e con a monte una logica di progettazione pensata appositamente per la stampa 3D – permetta di ridurre i costi di produzione e il time to market senza rinunciare alla qualità dei tradizionali sistemi sottrattivi.
Con la moderazione di Alessandro Garnero, direttore editoriale di Tecniche Nuove, hanno partecipato all’evento:
- professor Ferdinando Auricchio, responsabile scientifico del Gruppo di Meccanica Computazionale e Materiali Avanzati dell’Università di Pavia e responsabile scientifico della community dedicata alla manifattura additiva all’interno di Afil (Associazione Fabbrica Intelligente Lombardia);
- Artemio Affaticati (amministratore delegato di Scoprega, azienda specializzata in prodotti e accessori per il settore nautico);
- Lorenzo Balli (amministratore delegato di Everex, società specializzata nella progettazione e produzione di strumenti di analisi intelligenti nel settore delle biotecnologie e della diagnostica in vitro);
- Fabio Breviario (responsabile della ricerca e sviluppo in Conductix-Wampfler, società specializzata nella progettazione e realizzazione di sistemi di trasmissione di energia e dati);
- Elia Campetella (amministratore delegato di Campetella Robotic Center, azienda italiana specializzata nella produzione e applicazione di robot industriali e sistemi di automazione per stampaggio ad iniezione delle materie plastiche).
Di seguito riportiamo alcune testimonianze di chi impiega la manifattura additiva, per la produzione di parti regolarmene in produzione, in sostituzione di parti ricavate con tradizionali sistemi sottrattivi, con quali risultati e quali limiti.
Ferdinando Auricchio
«La stampa 3D come tema strategico per l’intera Università»
Nel doppio ruolo di responsabile scientifico della strategy community per la manifattura additiva di Afil e di docente universitario all’Università di Pavia, Auricchio prima di tutto ha sottolineato come il cluster tecnologico per il manifatturiero avanzato della Regione Lombardia si adoperi per supportare le aziende nel processo di adozione della tecnologia additiva, raccogliendo perplessità, interessi e motivazioni per discuterle e portarle a interlocutori istituzionali.
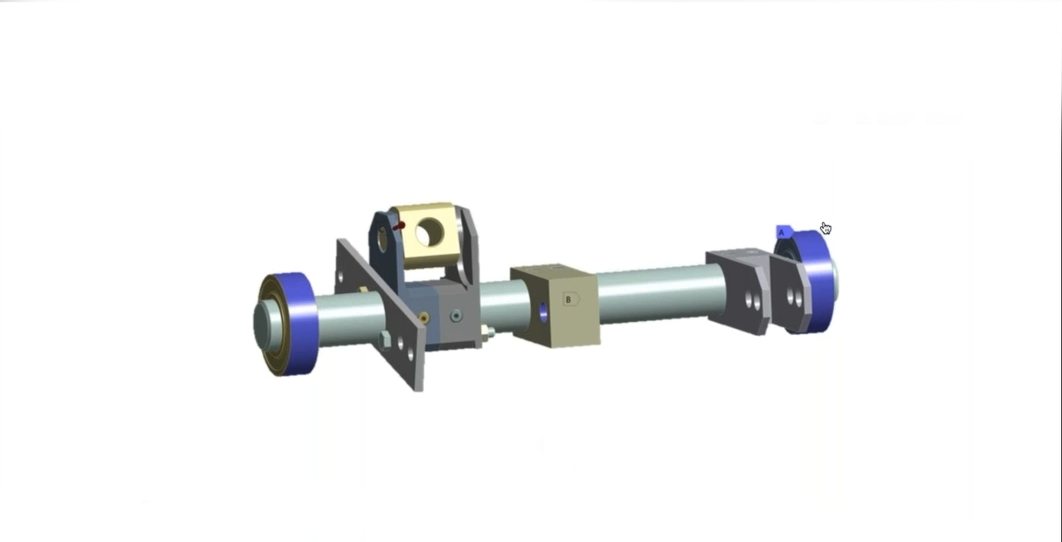
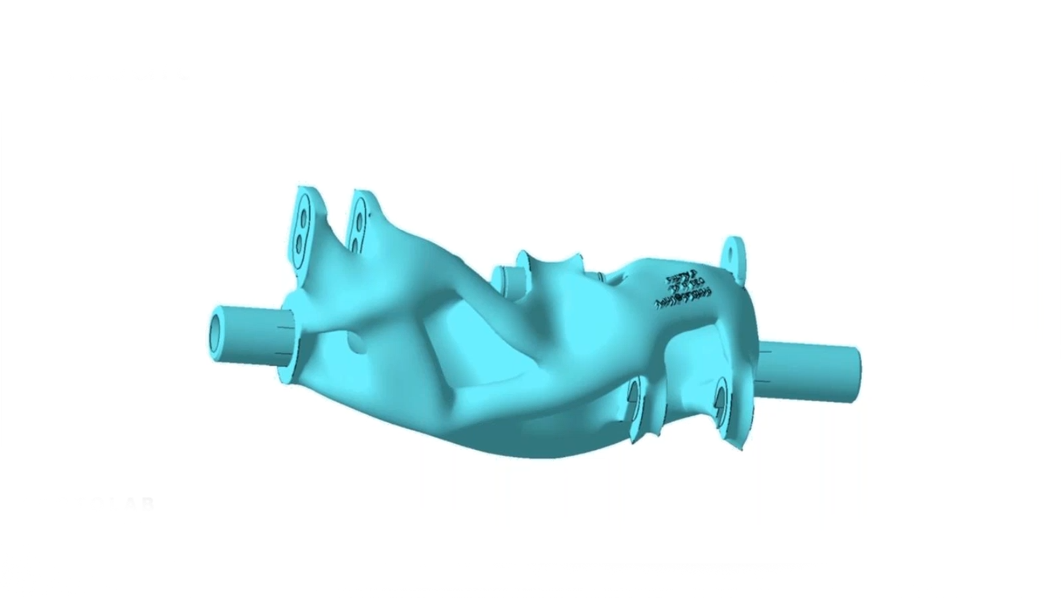
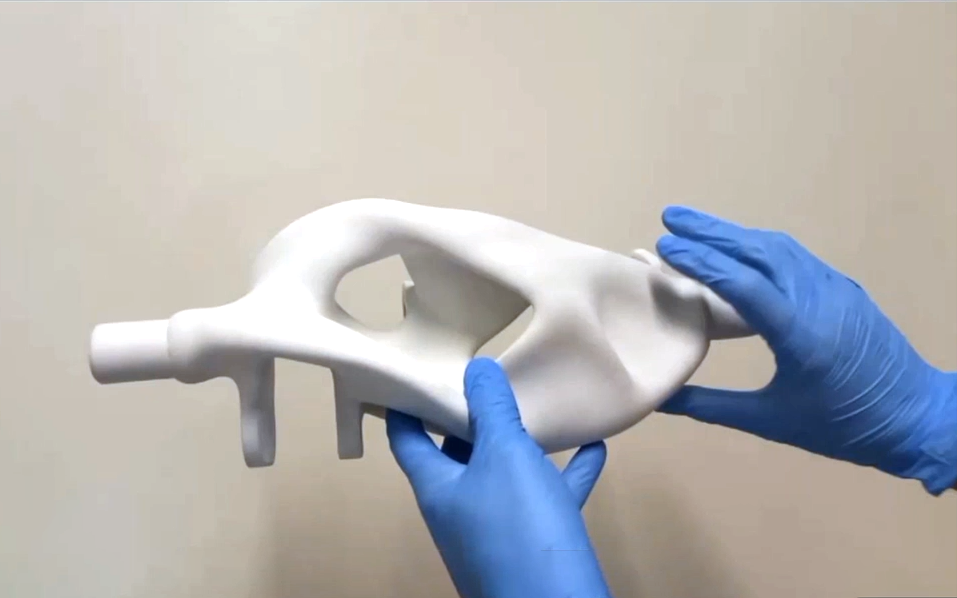
«Per quanto riguarda la mia attività di professore a Pavia – sottolinea Auricchio – nel 2015 abbiamo scelto la stampa 3D come tema strategico per l’intera Università, proponendo un modello basato su pilastri costituiti da modellazione e simulazione, sviluppo dei materiali, laboratori con tecnologie avanzate, applicazioni e studi sull’impatto socio economico delle tecnologie additive.»
Tra i casi che cita Auricchio è particolarmente interessante un progetto portato avanti con Valvitalia, grazie al quale un componente per l’industria del gas, composto da varie parti in acciaio lavorate in sottrattivo, è stato riprogettato e stampato in 3D ottenendo in 40 ore un prodotto con peso dimezzato rispetto all’originale per il quale sono state necessarie sette settimane di lavorazione.
«In questo caso – afferma Auricchio – il componente ottenuto è stato vantaggioso anche dal punto di vista economico.»
Conclude il suo intervento citando una collaborazione con ABB per la riprogettazione di un albero di trasmissione.
«Abbiamo avviato un processo di ottimizzazione del componente considerando i vincoli di progetto, due appoggi e leveraggi imposti, e abbiamo ottenuto un componente che abbiamo stampato con la tecnologia di HP e che ora stiamo testando meccanicamente.»
Secondo Auricchio la stampa 3D, nata per la prototipazione rapida, si sta avvicinando sempre di più alle tecnologie tradizionali.
Artemio Affaticati
«La stampa 3D è un’arma vincente ma i costi dei materiali sono ancora troppo alti»
«Quando sono entrato in Scoprega – esordisce Affaticati – l’azienda era strutturata con una sede in Cina che si occupava di grandi produzioni di pezzi semplici stampati in plastica e una sede in Italia che si occupava di prodotti più complessi, come i doppiatori per la nautica. Come è noto, lo sviluppo di prodotto nel settore della plastica, con le tecnologie tradizionali, dura troppo. Per mettere a punto uno stampo affidabile e competitivo bisogna costruirlo in Cina e possono passare anche due anni prima di arrivare ad avere il prodotto e in questo modo si perdono opportunità.»
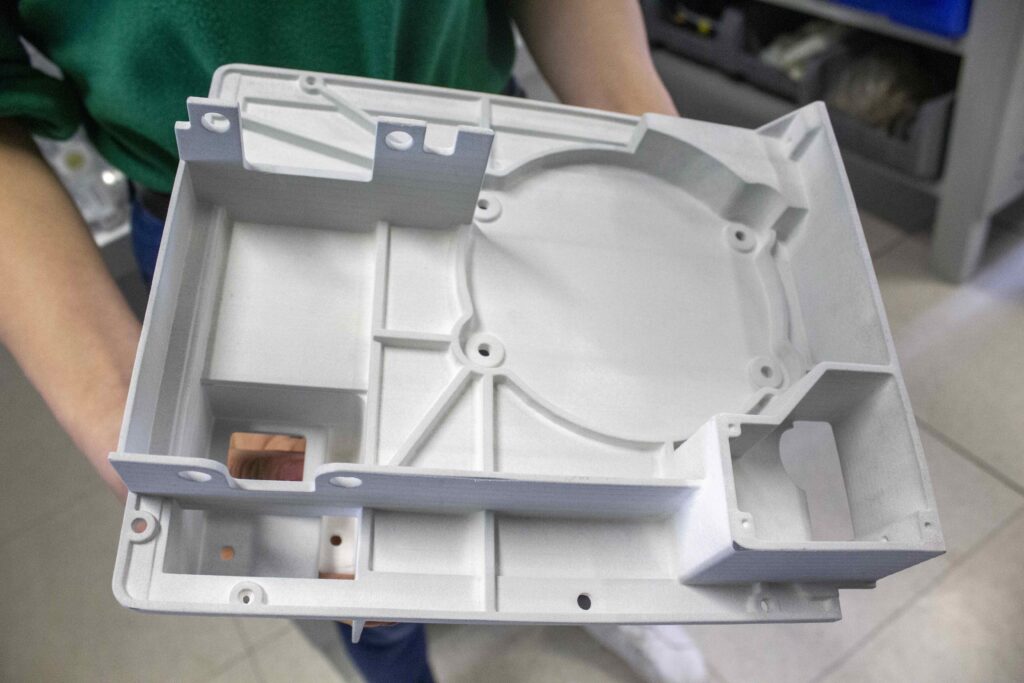
«Avevamo, quindi, un gap pesante dal punto di vista dell’innovazione – prosegue Affaticati – e abbiamo iniziato a pensare alle possibilità offerte dalla stampa 3D. Dal 2018 abbiamo installato le prime macchine di produzione, in modo da poter realizzare autonomamente piccoli lotti.»
«L’esperimento è riuscito – sottolinea Affaticati – grazie alla flessibilità della stampa 3D, che consente di stampare lo stesso pezzo in qualsiasi parte del mondo abbattendo i prezzi della logistica. Si tratta di un’arma vincente, ma che sarà tale solo quando i volumi aiuteranno ad abbassare i costi dei materiali, che sono ancora troppo alti.»
Per il momento in Scoprega la produzione viene effettuata con tecnologia HP e PA 12 come materiale.
«Altri materiali rinforzati con fibra di vetro e fibra di carbonio costano troppo e preferisco chiedere ai miei progettisti di fare un’analisi ad elementi finiti migliore e andare in produzione con il PA 12» conclude Affaticati.
Lorenzo Balli
«Oggi, ogni nostro strumento contiene parti stampate in 3D»
Il primo contatto con la stampa 3D, racconta l’amministratore delegato di Everex, è stato grazie a un fornitore che li ha portati a vedere un sistema per la stampa 3D.
«Ci è sembrata, da subito, sulla carta, un’ottima idea – ricorda Balli – perché i sistemi che progettiamo e costruiamo per analisi diagnostiche vengono prodotti in serie che vanno da 20 a 500 prodotti l’anno e quindi la produzione additiva poteva essere l’ideale per le nostre esigenze.»
I primi passi, affidandosi a un service esterno, non sono stati positivi perché i progettisti di Everex non erano ancora abituati a progettare per l’additivo.
«Nel corso del tempo – prosegue Balli – abbiamo cambiato completamente l’approccio a livello progettuale, con successo. I nostri strumenti sono delle “mini fabbriche” intelligenti formate da zone logiche di funzionamento che sono dei gruppi di lavoro, dei macroassiemi. Grazie al nuovo approccio progettuale abbiamo stravolto questi gruppi di lavoro e oggi praticamente ogni nostro strumento contiene parti stampate in 3D.»
«La manifattura additiva – conclude Balli – ci ha permesso di ridurre considerevolmente le parti che compongono i gruppi di lavoro, riducendo il numero di fornitori esterni, minimizzando gli errori umani, riducendo i tempi di assemblaggio, con una notevole riduzione dei costi.»
Balli cita l’esempio di un piatto porta campioni e reagenti progettato per lavorazioni sottrattive, composto da 418 parti da assemblare, che avrebbe dovuto essere prodotto in 100/150 assiemi all’anno.
Il progetto pensato per tecnologia sottrattiva non ha mai visto la luce, ma lo stesso progetto è stato rivisto in chiave additiva con il risultato che le parti da assiemare sono diventate soltanto 113, con un risparmio del 40% rispetto al precedente.
In un altro caso, un carrello con aghi campionatori, la progettazione additiva ha permesso di passare da 72 parti da assemblare a 45, con un risparmio del 56% rispetto alla stesso prodotto realizzato con tecnologie tradizionali.
In Everex oggi utilizzano internamente due sistemi HP con tecnologia Multi Jet affiancati da centri di lavoro tradizionali per lavorazioni su pezzi che richiedono tolleranze centesimali.
Fabio Breviario
«I nostri progettisti si sono abituati a pensare in additivo»
«In Conductix-Wampfler realizziamo prodotti che servono a portare elettricità e dati all’interno di macchine che hanno sia movimentazione lineare sia rotativa. All’inizio abbiamo impiegato la stampa 3D semplicemente per sostituire alcune parti metalliche, tipicamente in alluminio, dei nostri prodotti con parti stampate in 3D senza riprogettarle ex novo con logica additiva» spiega Breviario.
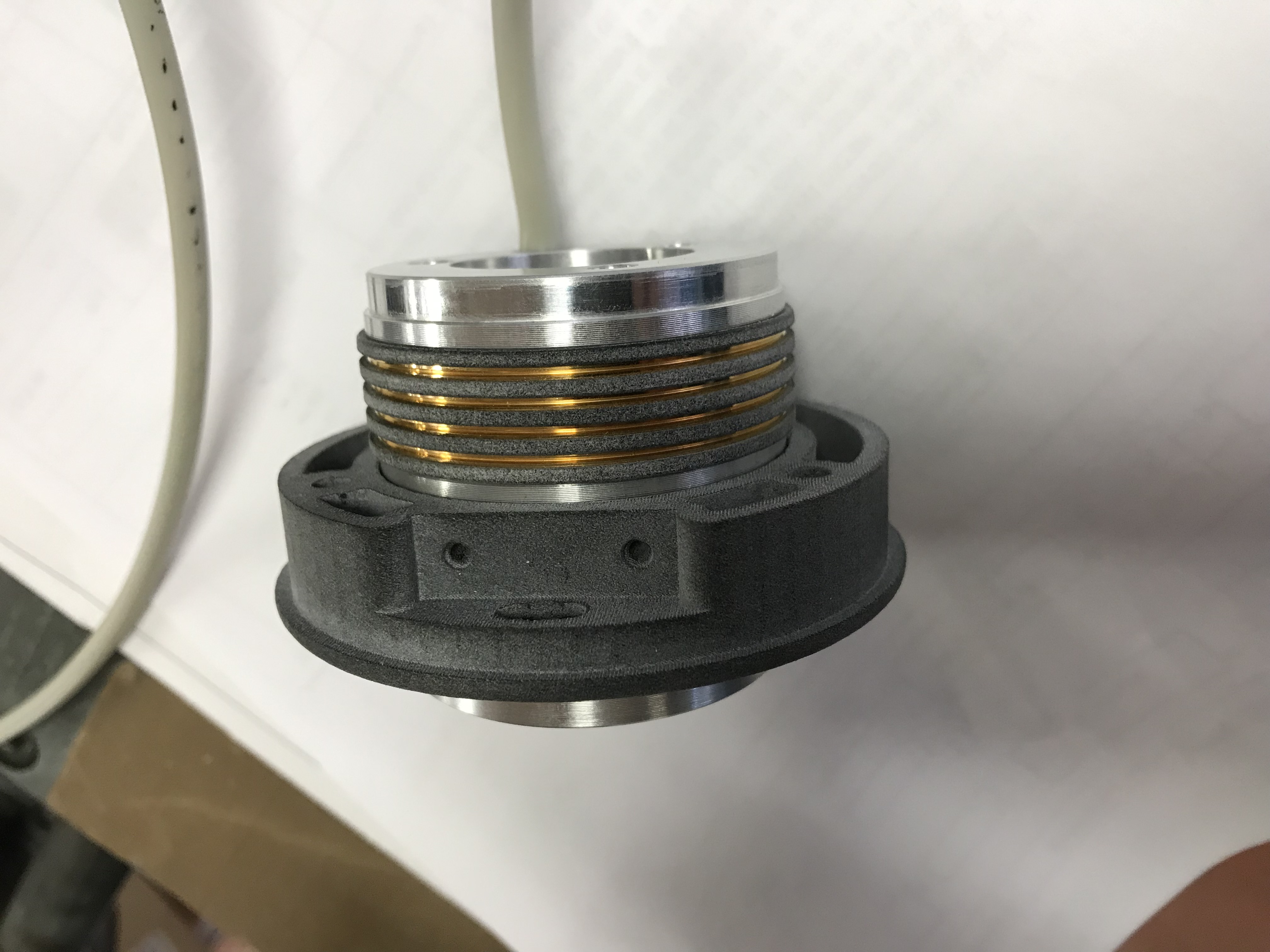
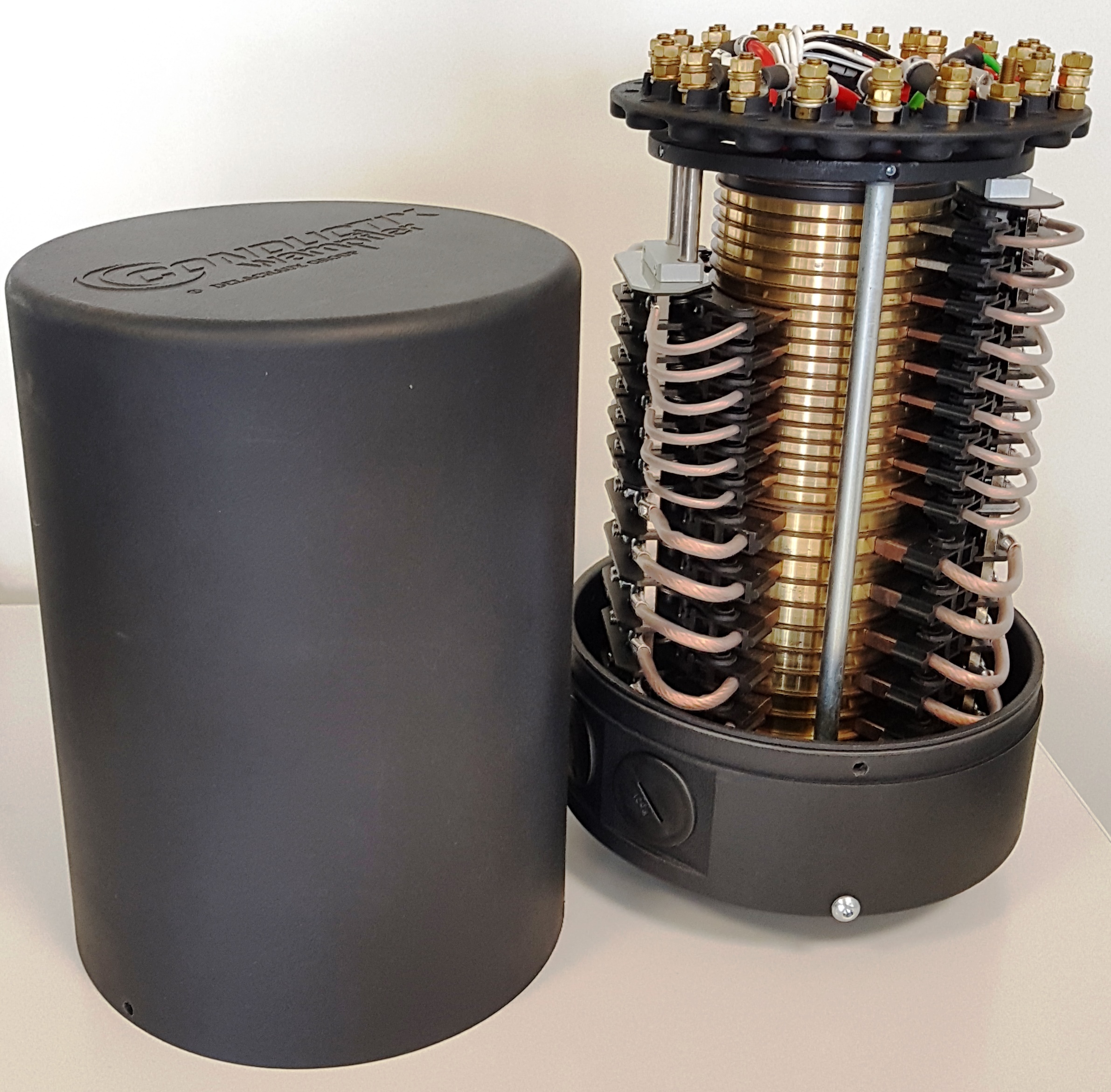
«Ci siamo ben presto accorti che per i nostri prodotti, solitamente in serie limitate (da qualche decina ad alcune centinaia), valesse la pena di incrementare la produzione additiva e di progettare o riprogettare in nostri prodotti ad hoc. Dalla trasformazione, quasi uno a uno, di parti metalliche lavorate tradizionalmente, in parti plastiche stampate in 3D, con la progettazione additiva – sottolinea Breviario – siamo arrivati a integrare più funzioni all’interno di un singolo componente.»
«I nostri progettisti si sono abituati a pensare in additivo, anche se a volte bisogna frenare la loro creatività. I pezzi, infatti, possono essere così tanto integrati che si rischia di arrivare a progettare parti che non sono montabili. Il progettista – tiene a precisare Breviario – deve considerare, in ambito di sviluppo, anche la sequenza e l’ingombro dei singoli pezzi per permetterne la montabilità.»
«A livello generale la stampa 3D semplifica per molti aspetti la produzione, ma bisogna ancora lavorare per integrarla appieno nel flusso produttivo a livello di ERP. Ovviamente per grandissimi volumi la stampa 3D oggi non è competitiva rispetto alle lavorazioni tradizionali, ma quando scenderanno i costi dei materiali potrebbe limitare molto le lavorazioni sottrattive» prosegue Breviario.
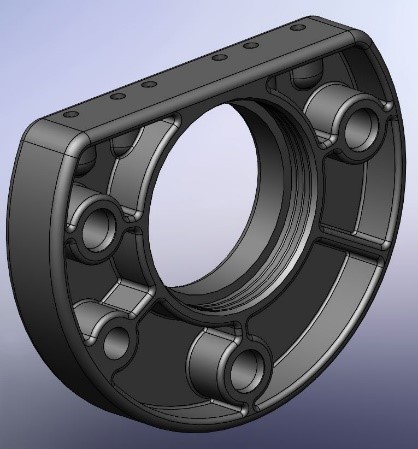
Il nostro interlocutore cita alcuni esempi, partendo dalla sede di un cuscinetto precedentemente realizzato in plastica lavorata con macchine a controllo numerico, con tolleranza -0,01/-0,07 millimetri.
Lo stesso prodotto viene ora prodotto in additivo, con alcuni accorgimenti progettuali che hanno consentito di compensare la minor precisione a livello di tolleranza della stampa 3D.
«Nel pezzo stampato in 3D – conclude Breviario – abbiamo fatto operazioni di alleggerimento e abbiamo creato delle nervature per assicurare la tenuta del cuscinetto nella sua sede, dopo l’inserimento con una piccola pressa».
Breviario cita anche collettore per trasmissione dati che precedentemente veniva realizzato da pieno assemblando una decina di parti, dando luogo a problemi di tenuta IP e che ora viene ottenuto con una sola parte stampata in 3D.
Elia Campetella
«Per noi la stampa 3D ha avuto la dirompenza di un incendio»
«Ci occupiamo della produzione e dell’applicazione di robot industriali e sistemi di automazione per stampaggio a iniezione delle materie plastiche. Macchine, in pratica, che scaricano lo stampo una volta che il prodotto è formato» esordisce Campetella.
«La nostra attività ci porta a sviluppare moltissimi sistemi che integrano le mani robotiche che devono manipolare i pezzi e altri componenti che devono essere movimentati con cicliche molto rapide, come ad esempio quattro metri e mezzo di percorso in meno di due secondi con precisioni di posizionamento del decimo di millimetro.»
«Grazie alla stampa 3D – prosegue Campetella – abbiamo avuto la possibilità di poter integrare molti componenti creando geometrie complesse e uniche, riducendo di molto anche il peso dei componenti di manipolazione dei robot. Per fare un esempio, a parità di funzionalità, siamo riusciti a passare dai 13 chilogrammi di peso delle mani di presa realizzate tramite procedimenti sottrattivi ai 2,7 chilogrammi ottenuti con la stampa 3D.»
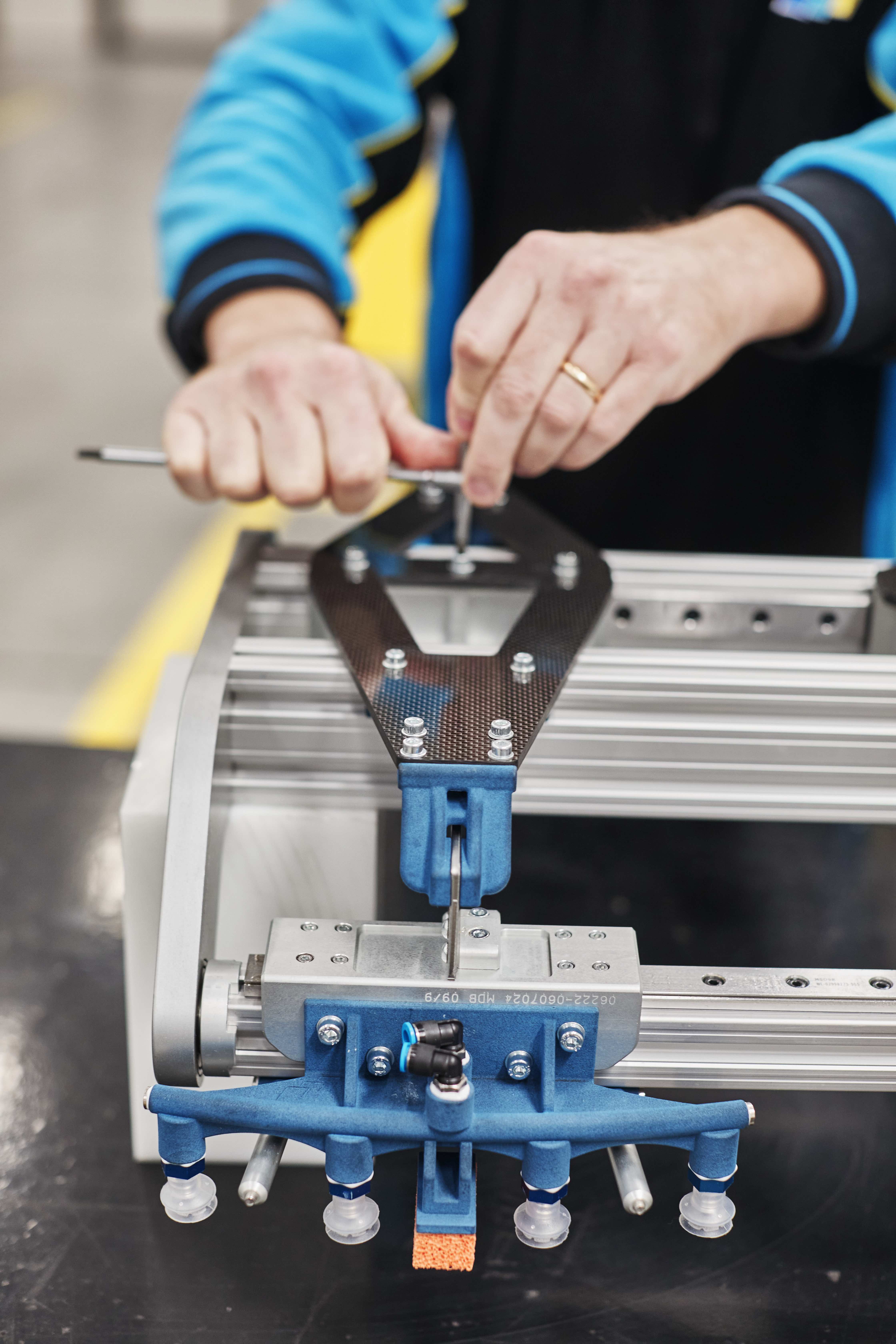
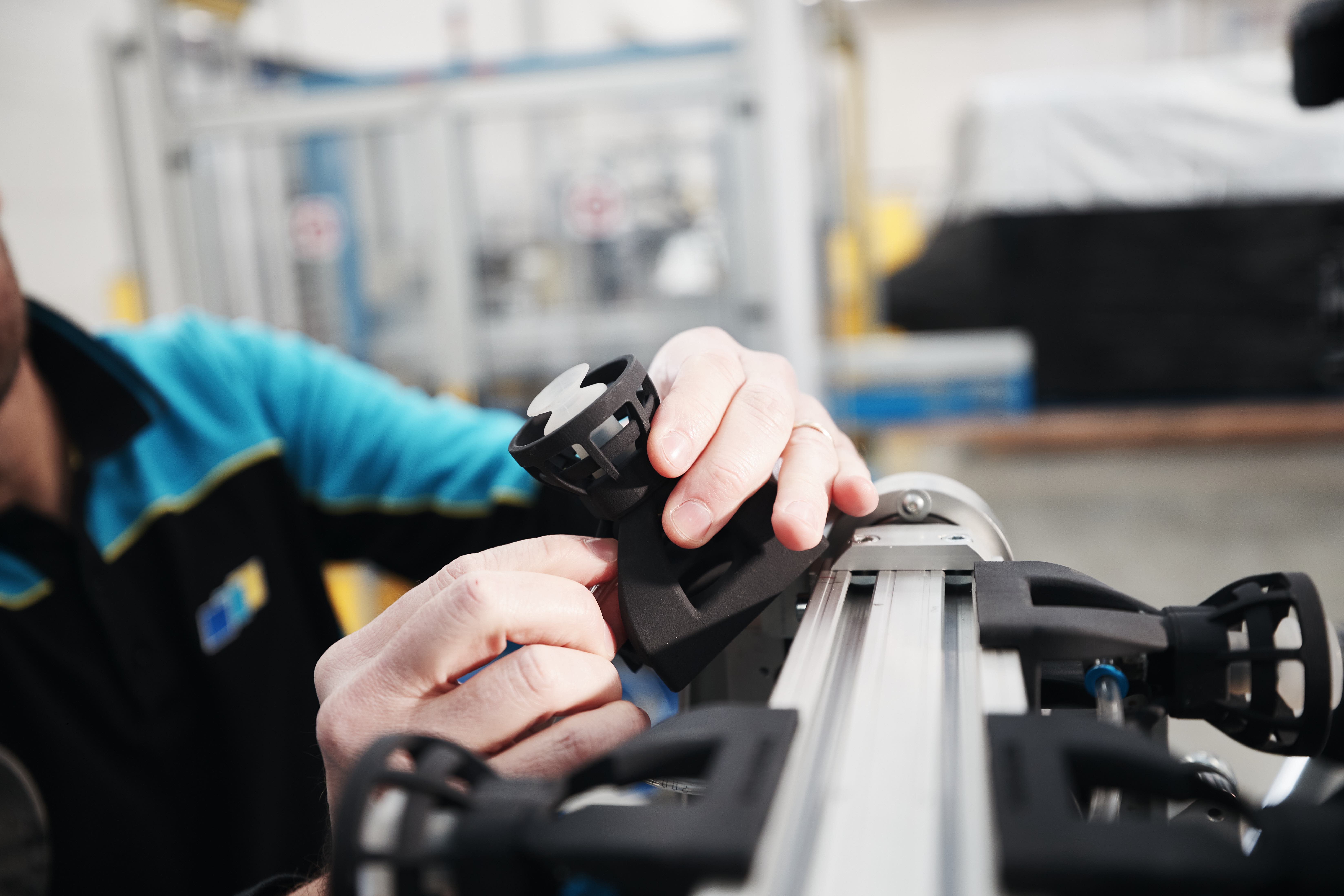
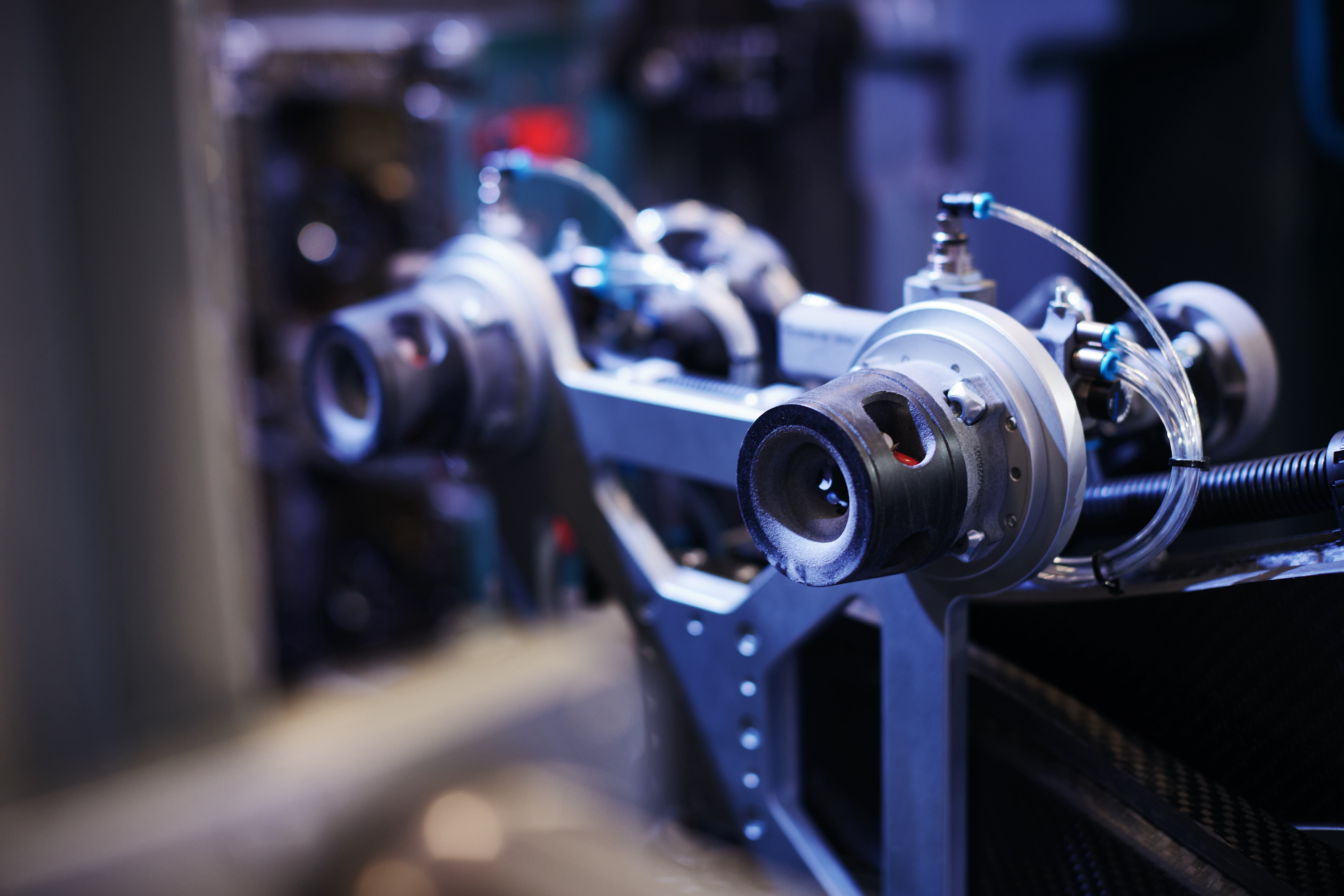
«Grazie a questa riduzione di peso possiamo usare robot di taglia più piccola e, soprattutto, ridurre notevolmente la loro manutenzione visto che devono operare con carichi più piccoli. Grazie alla stampa 3D – puntualizza Campetella – siamo riusciti anche a ridurre le perdite di carico nelle mani di presa pneumatiche perché abbiamo potuto creare i canali all’interno delle geometrie anziché ricorrere ai classici raccordi pneumatici sul corpo delle mani di presa.»
«Si è ridotto considerevolmente lo spreco d’aria e sono aumentate le performance perché con la stampa 3D non ci sono limitazioni nelle sezioni utilizzabili. Infine – concluse Campetella – grazie alla produzione additiva, possiamo corredare i nostri robot di kit stampati in 3D che contengono tutto quello che serve per la specifica attività a cui verranno destinati. La customizzazione della mano di presa è fondamentale perché ogni prodotto viene progettato e costruito in base a quello che dovrà manipolare.»
Anche in Campetella Robotic Center vengono utilizzati la stampa 3D di HP e il materiale PA12. E anche loro non impiegano i materiali rinforzati con vetro o carbonio perché ritenuti troppo costosi.