L’ispezione dello stato degli utensili è uno step fondamentale nella produzione di ingranaggi conici. Una geometria corretta degli utensili assicura l’ottenimento della forma desiderata del dente. Gli autori propongono una procedura per utilizzare misure condotte su una larga porzione dell’utensile per la valutazione delle proprietà di feature molto piccole. Il metodo si ispira agli standard AGMA/ANSI ISO 1328-1-B14 per la valutazione dell’angolo di pressione e della distanza del tagliente.
L’accuratezza dei profili delle ruote coniche dipende dall’accuratezza degli utensili da taglio. I taglienti derivano da inserti montati su una fresa frontale come mostrato in Figura 1 [2]. L’accuratezza nelle geometrie di taglio viene solitamente verificata analizzando e confrontando le misure (condotte con macchine di misura a coordinate) con quelle nominali teoriche create dal programma di taglio. Ispezioni dettagliate degli inserti sono necessarie a causa della complessità della geometria – Figura 2 [3]. Analisi accurate dei dati rappresentano una vera sfida soprattutto in sezioni molto piccole e in condizioni operative difficili.
Gli autori di questo articolo propongono una procedura che può essere utile per la valutazione e interpretazione dei dati di misure contenenti outlier.
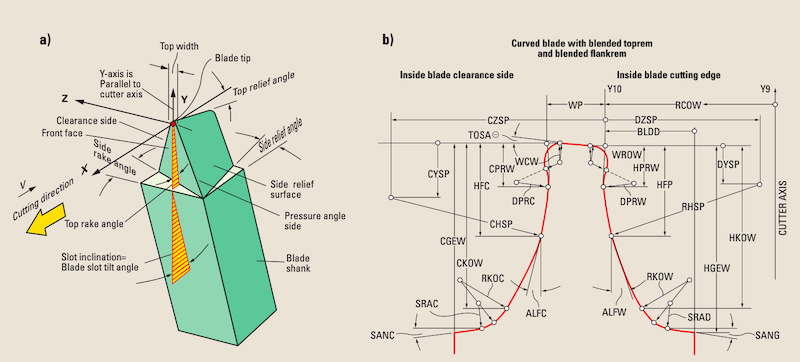
Procedura di misura dei taglienti e relative problematiche
La geometria di un ingranaggio conico è definita attraverso i parametri base e quelli del profilo del tagliente [4, 5]. La forma è definita dalla proiezione del tagliente, posizionato nella sua posizione di lavoro, sul piano di taglio – Figura 3 [6]. La stessa figura mostra anche il numero minimo di punti (cinque) necessari per la valutazione del profilo. Il tagliente consiste in 3 regioni principali (Figura 2a): il lato a contatto, il lato avente gioco e la testa del tagliente. Il lato a contatto può essere ulteriormente diviso in (Figura 2b):
a) raggio: pozione del tagliente che, assieme alla testa, taglia il piede e il raccordo del dente;
b) parte superiore: crea la transizione tra raggiatura e fianco stesso;
c) tagliente principale: taglia la porzione principale del fianco creandone il profilo (tra HPRW e HKOW);
d) parte inferiore: determina la transizione tra fianco e spalla;
e) spalla: determina la transizione tra il fianco e la porzione inferiore dell’inserto.
Le sezioni, definite nel piano di taglio, posso avere una geometria definita da linee rettilinee o da segmenti circolari. Fanno eccezione solo i raggi di raccordo al piede e la spalla che sono hanno sempre profili circolari.
Tradizionalmente l’ispezione dei taglienti viene eseguita manualmente se pur con l’ausilio di macchinari. Tipicamente vengono utilizzate macchine 3D di misura delle coordinate.
Recentemente si è cominciato a utilizzare sistemi laser [6] accoppiati a opportuni sistemi di fissaggio in modo da minimizzare l’impatto delle dimensioni degli oggetti sulle misure e ridurre gli errori legati all’operatore.
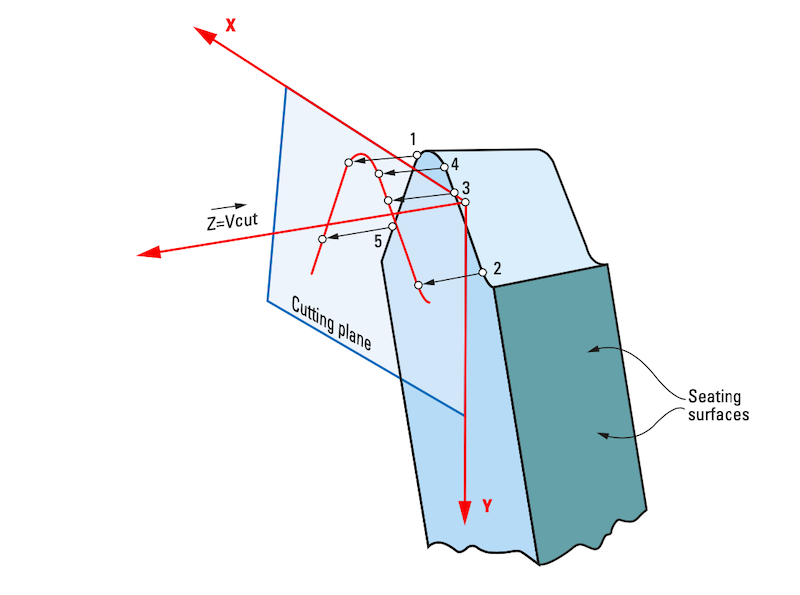
1. vengono create le coordinate teoriche dei punti del profilo assieme alle normali. Questi dati vengono passati alla macchina per il controllo;
2. i taglienti vengono posizionati nella macchina di misura che ne acquisisce le coordinate;
3. i risultati (valori reali) sono confrontati con quelli nominali. In questa fase è possibile definire le azioni correttive.
Le azioni correttive possono includere aggiustamenti della forma come raggi di curvatura e angoli di inclinazione, o della posizione come la distanza tra i taglienti il punto di inizio della feature. Recentemente sistemi ad anello chiuso hanno permesso di introdurre in modo automatico le correzioni. Speciali macchinari permettono anche una riaffilatura dei taglienti in funzione delle misure.
Il metodo di ispezione è molto lineare. Tuttavia, vi sono fonti intrinseche di errore nella procedura. Queste devono essere superate ed evitate al fine di assicurare misure accurate ed ingranaggi con geometrie perfette. Gli errori che possono essere fatti in fase d’ispezione possono essere suddivisi in 3 gruppi in funzione della fonte:
– errori dovuti all’operatore, che possono includere errori nel posizionamento del tagliente;
– errori dovuti all’ambiente, causati dal posizionamento del macchinario all’interno della linea di produzione che si manifestano tipicamente in vibrazioni o presenza di particelle inquinanti;
– errori dovuti alle capacità della macchina, legate alle dimensioni del provino o ai limiti sulla risoluzione della stessa.
La prima fonte di errore è individuabile e facilmente correggibile. Le altre due possono portare a dati che rischiano di essere interpretati in modo erroneo, per cui è importante una revisione accurata delle misure che spesso portano a male interpretare la geometria del tagliente e ad apportare correzioni che possono addirittura peggiorare la situazione. Uno degli aspetti principali dell’elaborazione è riuscire ad eliminare nel modo corretto gli outlier.