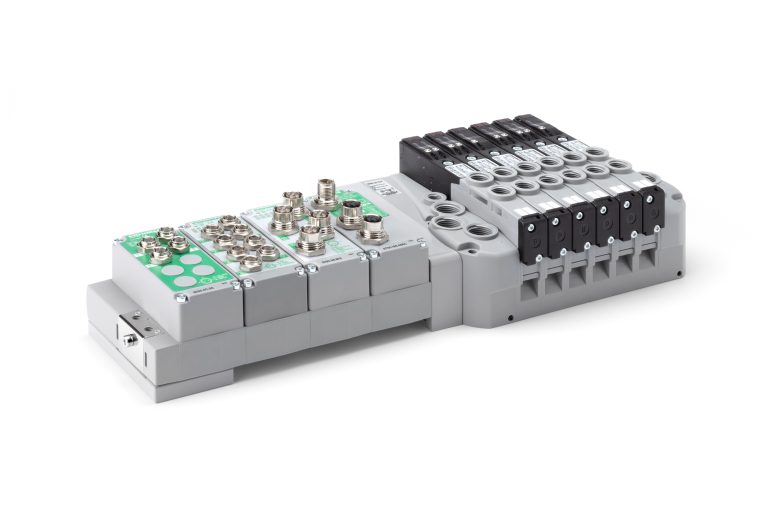
Home » Guida all’elettropneumatica
Condividi
La pneumatica è una branca della fisica che studia il trasferimento di forze mediante l’utilizzo di gas in pressione, molto spesso aria compressa.
Sviluppatasi come scienza ingegneristica a partire dal XVIII secolo, nel tempo la pneumatica ha conosciuto significative applicazioni industriali.
L’utilizzo di controlli logici pneumatici e soprattutto l’uso di relè elettromeccanici ha progressivamente aperto la strada a sistemi integrati comprendenti gruppi pneumatici dedicati all’attuazione e gruppi elettrici/elettronici sia per la sensorizzazione, il controllo e la gestione, che per una parte dell’attuazione.
Questa breve guida si propone di:
È ormai comune trovare integrati nello stesso sistema automatico componenti meccanici, elettromeccanici, pneumatici, elettronici, ottici.
Questi stessi sistemi contengono spesso dispositivi wireless per la trasmissione di segnali tra parti separate dello stesso sistema o per il collegamento alla rete con varie finalità, come:
Questi collegamenti in rete possono servire anche a migliorare l’efficienza energetica degli impianti ad aria compressa.
Se, infatti, si collega una centrale di compressione via Ethernet a un controllo remoto, si possono acquisire in tempo reale tutti i dati operativi ed energetici e confrontarli con quelli di un modello virtuale in modo da verificare in tempo reale lo stato degli impianti, prevedendo ove possibile l’insorgenza di guasti e adottando automaticamente adeguate misure.
In un circuito pneumatico sono presenti vari tipi di componenti:
Come si vede nello schema (schema di un sistema elettropneumatico), i segnali elettrici dell’unità di governo sono convertiti in segnali pneumatici dalle interfacce, sono deviati e indirizzati dalle valvole di controllo di direzione, condizionati dalle valvole di controllo e inviati agli attuatori.
I sensori e i fine-corsa sono ora di tipo elettrico: vengono azionati dai movimenti e inviano i propri segnali di uscita all’unità di governo, chiudendo l’anello a catena chiusa del sistema.
Il progetto di un circuito pneumatico richiede la definizione:
Nelle funzioni di controllo, si diffonde sempre di più l’uso di unità elettroniche programmabili, costituite sia da controllori logici programmabili, o PLC, sia da personal computer opportunamente attrezzati.
La necessità di ricorrere a unità di governo programmabili deriva da esigenze di flessibilità per:
A favore dell’uso di PLC vi sono, poi, fattori di razionalizzazione degli impianti che diventano sempre più evidenti con l’aumento del numero di segnali in gioco.
Attualmente si assiste ad una profonda integrazione tra attuazione meccanica, pneumatica, elettrica e controllo, soprattutto attraverso l’impiego di una struttura di controllo distribuito con più PLC locali interconnessi da linee di interscambio dei dati.
L’evoluzione dei sistemi automatici rende sempre più importante l’integrazione tra attuazione e controllo, con un uso sempre più ampio di sensori per svolgere funzioni di gestione e di monitoraggio.
Gli attuatori sono gli organi che compiono un lavoro meccanico realizzato dalla traslazione o dalla rotazione di un apposito elemento. Si tratta di cilindri (per spostamenti lineari), di motori rotativi (per rotazioni continue) o di dispositivi oleopneumatici.
I sensori sono gli elementi che trasformano in un segnale elettrico le grandezze meccaniche. La presenza dei sensori è essenziale perché permette di fornire all’unità di governo le informazioni necessarie a procedere nello sviluppo di un ciclo automatico.
I sensori più utilizzati nei sistemi di automazione pneumatica digitali rilevano i movimenti dei gruppi mobili (segnalando, ad esempio, che il movimento di un cilindro ha raggiunto la posizione di fine corsa) oppure la presenza di pezzi che devono essere presi, movimentati, montati.
Lo sviluppo dell’automazione, in tutti i settori industriali, ha notevolmente aumentato la complessità dei circuiti, aumentando anche i tempi di assemblaggio e di cablaggio.
Con lo scopo di ridurre costi di manodopera, sempre più spesso vengono fornite isole di elettrovalvole montate modularmene in batteria, ivi compresi, in molti casi, i collegamenti elettrici.
Il sistema tradizionale prevede collegamenti punto-punto con due fili elettrici per ognuna delle elettrovalvole della batteria. Il vantaggio, in questo caso, è costituito dalla riduzione dei tempi di assemblaggio riferiti solo alla parte pneumatica dell’isola.
Frequentemente, alla batteria, arriva un cavo già assemblato contenente tutti i fili necessari per il collegamento delle singole elettrovalvole, i cui terminali sono connessi ad un connettore a vaschetta con terminali femmina. In questo caso, un connettore multipolare verrà collegato alla batteria con un’unica operazione, con evidente riduzione dei tempi di assemblaggio sulla macchina.
Il passo successivo è rappresentato dal collegamento seriale, in cui, con un unico cavo a due fili, più l’alimentazione elettrica, si è in grado di comandare l’isola con eccellenti risultati.
Come già accennato, si è passati da collegamenti elettrici punto a punto a collegamenti multipolari, per poi arrivare a connessioni seriali capaci di trasmettere segnali normalmente con un cavo a due fili. Il tutto per ridurre e ottimizzare le esigenze di cablaggio.
In generale, si definisce bus (informatico) il mezzo pubblico di trasporto dei dati, mentre il campo è l’area in cui avviene la comunicazione, sia esso complesso industriale o singola macchina. Bus di campo, o Fieldbus, è allora il termine fissato in ambito IEC (International Electrotecnical Commission) per indicare un processo di comunicazione seriale tra diversi dispositivi, definiti nodi.
Attraverso il bus di campo, i dati vengono trasferiti con tecnica seriale, cioè un bit dopo l’altro ad elevata velocita.
I vantaggi di queste soluzioni si possono sintetizzare nei seguenti punti:
Le caratteristiche e le modalità di funzionamento di qualsiasi sistema di comunicazione digitale sono definite da un protocollo di comunicazione, cioè un insieme di regole e comportamenti che due entità diverse devono rispettare per scambiare informazioni tra di loro.
Alla fine degli anni ‘70 ISO (International Standard Organisation) ideò un metodo standardizzato per la definizione di protocolli di comunicazione ed avviò il progetto Open System Interconnection (OSI) con lo scopo di definire un modello di riferimento per lo sviluppo di protocolli orientati alla interconnessione di sistemi aperti. Il risultato finale fu la definizione dello OSI Basic Reference Model come standard ISO 7498.
Partendo da OSI come modello di riferimento, sono nati decine di bus di campo diversi tra loro. Alcuni di questi si sono affermati sul mercato e sono diventati degli standard.
In un impianto che utilizzi un protocollo standard, anche se i nodi sono realizzati da costruttori diversi, possono comunicare facilmente tra loro.
Nel settore dell’automazione con aria compressa, le batterie di elettrovalvole sono integrate nel nodo ed è possibile inserirle in rete assieme a dispositivi con altre funzionalità, a condizione che il protocollo usato sia il medesimo.
I principali protocolli standard sono: Canopen – Profibus – Ethernet/IP – Ethercat – Profinet – CC-Link IE Field Basic – IO-Link
Nella tabella sono riassunte le principali caratteristiche di questi protocolli.
CANopen | In forte espansione. In una rete CANopen, ad ogni dispositivo deve essere assegnato un indirizzo fin dalla fase di installazione. Ogni costruttore deve fornire un file EDS (Electronic Data Sheet) allo scopo di descrivere le caratteristiche del dispositivo e quali siano gli oggetti implementati. É possibile scollegare un nodo senza che la comunicazione sia interrotta agli altri partecipanti attivi. |
Profibus | È stato sviluppato dall’industria tedesca (soprattutto Siemens) in collaborazione con le maggiori università. Il suo impiego nel settore automazione e in continua crescita. La comunicazione tra master e slave avviene sotto forma di polling. Affinché il master possa inizializzare la rete ha bisogno di un elenco dei nodi partecipanti e della descrizione dei dispositivi. Per questo motivo i moduli di Profibus DPR vengono forniti con un file GSD che elenca le principali caratteristiche dei prodotti. È possibile scollegare un nodo senza che la comunicazione sia interrotta con gli altri partecipanti attivi. |
EtherNet/IP | EtherNet/IP è un protocollo di comunicazione Ethernet industriale per applicazioni di automazione. Si differenzia da altri standard di comunicazione basati su Ethernet per l’implementazione dell’applicazione CIP e del modello di comunicazione TCP/IP. EtherNet/IP supporta Ethernet, protocollo Internet e protocollo TCP o UDP (User Datagram Protocol). Ciò consente la compatibilità con tutti i dispositivi che utilizzano questo protocollo. Questa compatibilità con i protocolli stabiliti consente quindi una perfetta integrazione di EtherNet/IP nelle reti e permette di controllare la continuità tra la rete dell’ufficio e il sistema. La tecnologia EtherNet/IP vi aiuta quindi a controllare e configurare i vostri dispositivi e a raccogliere dati allo stesso tempo |
EtherCAT | EtherCAT è una tecnologia Ethernet industriale deterministica. Il protocollo EtherCAT, pubblicato nello standard IEC61158, soddisfa requisiti hard e soft real-time nell’automazione, in sistemi di test e di misura e in molte altre applicazioni. L’attenzione principale durante lo sviluppo di EtherCAT è stata dedicata a tempi ciclo veloci (≤ 100 µs), jitter contenuto per un’accurata sincronizzazione (≤ 1 µs) e bassi costi dell’hardware. |
Profinet | PROFINET (Process Field Network) è uno standard di comunicazione basato su Industrial Ethernet con una gamma completa di applicazioni. Il bus di campo utilizza standard TCP/IP e IT è in grado di funzionare in tempo reale e consente l’integrazione di sistemi di bus di campo. PROFINET è stato sviluppato da Siemens e dalle aziende associate all’organizzazione degli utenti PROFIBUS (PNO) e viene utilizzato in combinazione con i sistemi di controllo Siemens. PROFINET è stato standardizzato dalle norme IEC 61158 e IEC 61784 e, come tecnologia di comunicazione universale, copre tutti i requisiti della tecnologia di automazione. |
CC-Link IE Field Basic | La comunicazione via CC-Link IE sfrutta la tecnologia Ethernet di base, facilmente adottabile per applicazioni minori che non richiedono controlli ad alta velocità, di facile applicazione e sviluppo. La comunicazione ciclica in una rete fieldbus CC-Link IE si realizza tramite software. Il sistema bus CC-Link IE Field Basic è compatibile con i dispositivi Ethernet da 100 Mbit. |
IO-Link | IO-Link è uno standard di comunicazione aperto nel campo dell’automazione industriale, progettato per consentire la comunicazione bidirezionale e la trasmissione di dati tra sensori, attuatori industriali e sistemi di controllo (PLC o controller). |
Un PLC, per poter svolgere i suoi compiti, deve essere programmato. Il programma può essere scritto utilizzando linguaggi diversi secondo la norma di riferimento IEC 61131-3 “Programmable controllers – Part 3: Programming languages”.
Un programma consiste in una rete di funzioni che devono essere eseguite (function) e di blocchi funzionali (function block) che sono gli elementi costitutivi contenenti la struttura portante dei dati e gli algoritmi.
La scrittura di un programma inizia dalla descrizione del comportamento sequenziale del sistema. Questo può avvenire con il metodo del grafcet, cioè con la corrispondente rappresentazione dello schema funzionale in sequenza (Sequential Function Chart o SFC) prevista nella stessa norma IEC 61131-3.
La rappresentazione con stati, o fasi, collegate con le azioni da compiere e le successive condizioni di transizione permette di definire le basi per la successiva programmazione mediante uno dei cinque tipi di linguaggi previsti dalla norma.
Alcuni modelli di PLC possono accettare linguaggi differenti, altri solo un unico modo di programmazione.
I linguaggi di programmazione previsti dalla norma IEC sono riportati nella seguente tabella.
Instruction List, IL o AWL |
Linguaggio macchina, come tale letto e gestito direttamente, più velocemente rispetto ad altri linguaggi. Poco intuitivo, richieste un programmatore specializzato ma consente di sfruttare appieno le possibilità di un PLC. |
Structured Text, ST | Linguaggio testuale di alto livello, adatto a calcoli complessi. Sfrutta anche operatori booleani e istruzioni condizionali |
Ladder Diagram, LD o KOP | Linguaggio grafico derivato dagli schemi a relè |
Function Block Diagram, FBD o FUP | Linguaggio grafico che prevede il disegno di schemi del tipo di quelli che si trovano nell’elettronica digitale. |
Sequential Function Chart, SFC | Linguaggio grafico che rappresenta il funzionamento a passi di un sistema automatico e coincide sostanzialmente con lo schema grafico grafcet |
I linguaggi possono operare:
L’automazione industriale si evolve sempre più verso la digitalizzazione, rendendo prodotti e sistemi sempre più interattivi e comunicanti tra loro e con i sistemi di gestione, secondo il paradigma della cosiddetta quarta rivoluzione industriale (Industria 4.0)
Alcuni tipi di dispositivi possono essere più facilmente integrati in un sistema di monitoraggio, come ad esempio i dispositivi elettrici.
Più complessa può essere la valutazione di un parametro come lo stato di efficienza delle guarnizioni in un sistema a fluido.
In un sistema elettropneumatico, tuttavia, esistono già svariati dispositivi, richiesti dal funzionamento stesso del sistema, che possono diventare i sensori per il monitoraggio dello stesso.
Un esempio per tutti è quello dell’utilizzo dei segnali dei sensori di fine corsa presenti su tutti i cilindri, che diventano importanti per concorrere alla valutazione dello stato operativo del sistema.
L’uso di moduli elettronici per la gestione di reti bus e la disponibilità di sistemi wireless migliorano la gestione dei sistemi automatici.
L’acquisizione dei segnali delle elettrovalvole consente inoltre di monitorare il numero di cicli effettuato da ogni bobina, di misurare vari dati relativi alla funzionalità delle isole di valvole, quali corto circuito, circuito aperto, tensione fuori controllo.
La presenza di ulteriori sensori permette di tenere sotto controllo la pressione, di verificare l’usura degli ammortizzatori, di monitorare il consumo di aria compressa.
Tutti questi dati sono utili per valutare lo scostamento rispetto ai valori attesi e possono essere acquisiti in apposite unità di memoria presso l’impianto, oppure possono essere collocati in cloud.
Un livello successivo è quello di passare a sistemi che si autocorreggono; a titolo di esempio la misura del tempo necessario a compiere la corsa di un cilindro può essere usata per modificare la regolazione delle valvole che controllano il flusso, per esempio attraverso valvole a otturatori multipli con sezioni di passaggio differenti.
I PLC sono le unità di governo più diffuse per il comando dei sistemi automatici di ogni tipo, in particolare anche dei sistemi pneumatici.
Si tratta di dispositivi basati su microprocessore, in grado di essere programmati.
Un PLC permette, normalmente, di eseguire numerose funzioni, quali: visualizzazione, memorizzazione ed elaborazioni di programmi, esecuzione di funzioni temporizzate ma anche esecuzione di cicli di autotest, una qualità che si rivela utile nella diagnostica.
Lo schema base di prevede una CPU, che è l’unità operativa del sistema, una memoria M, un gruppo di schede per i segnali di ingresso I, un gruppo di schede per i segnali di uscita U, un bus per i collegamenti interni tra gli elementi del PLC e per i collegamenti esterni verso gli elementi periferici. Vi sono poi adeguati alimentatori, elementi di visualizzazione, pulsanti per funzioni generali.
L’Internet of Things (IoT) è un’infrastruttura connessa in cui quasi ogni tipo di macchina/dispositivo (da sensori e attuatori a dispositivi complessi) dispone di un’intelligenza di base integrata che viene utilizzata per trasferire dati e interagire con altre macchine/dispositivi e, attraverso questi dispositivi, con le persone.
Requisito essenziale per sostenere l’enorme mole e varietà di dati trasferiti, elaborati e archiviati, è una connettività efficiente e di elevate prestazioni, come ad esempio la rete 5G, adatta per dispositivi che richiedono velocità molto elevata, latenza molto bassa, nonché avente la capacità di connettere un numero enorme di dispositivi IoT in un ambiente denso.
Esistono tuttavia molti altri tipi di connessione IoT tra cui scegliere, in base ai requisiti dei dispositivi IoT, all’applicazione, al sistema, al software e ai dispositivi da connettere.
Nella tabella seguente sono riportati alcuni tipi di connettività per IoT.
Bluetooth | tecnologia wireless a corto raggio utilizzata principalmente per lo scambio di dati tra dispositivi fissi e mobili su brevi distanze utilizzando onde radio UHF nelle bande ISM, da 2,402 GHz a 2,48 GHz. |
BLE, Bluetooth Low Energy | BLE offre un consumo energetico ridotto pur mantenendo la portata del classico Bluetooth |
LoRaWAN | è un protocollo di rete per la connessione a internet di dispositivi wireless alimentati a batteria a livello regionale, nazionale o globale. Le velocità di trasmissione variano da 0,3 kbps a 50 kbps. |
NB-IoT, IoT a banda stretta | La durata della batteria di oltre 10 anni è adatta ad un’ampia gamma di casi d’uso |
Sigfox | reti wireless adatte a connettere oggetti a bassa potenza La comunicazione |
Wi-Fi | ha una portata di 20-150 metri e alcune versioni possono raggiungere velocità superiori a 1 Gbps. Rispetto al Wi-Fi 5, le connessioni Wi-Fi 6 aumentano la capacità di trasferimento dati e diminuiscono la latenza. |
Zigbee | Utile per casi d’uso a bassa potenza e larghezza di banda ridotta. La tecnologia è limitata a distanze di trasmissione di 10-100 metri con una linea di vista per mantenere bassi i consumi |