Durante il processo di lavorazione, gli ingranaggi vengono sottoposti a numerosi controlli che interessano ogni singola operazione. In questo articolo vengono presi in esame i controlli funzionali della dentatura
I controlli di laboratorio degli ingranaggi vengono effettuati con apparecchi altamente sofisticati, a controllo numerico, di grande precisione che ispezionano in particolare i tre parametri fondamentali: il profilo, l’elica e il passo.
Gli apparecchi elettronici dell’ultima generazione sono dotati di softwares molto elaborati che permettono anche il controllo totale automatico della ruota. Per esempio, sull’apparecchio si può montare una ruota qualsiasi, di caratteristiche ignote. Nella prima fase del controllo l’apparecchio tasterà i diametri, misurerà il passo e il numero di denti, misurerà l’elica ed in base a questi dati fondamentali calcolerà le caratteristiche degli ingranaggi. Si imposterà autonomamente per la misura voluta e quindi controllerà il profilo, l’elica ed il passo facendo i diagrammi relativi. Volendo, può fare anche un esame topologico della superficie del dente fornendo sul monitor o stampando, una rappresentazione tridimensionale del dente con i relativi errori.
Tutto ciò richiede del tempo e non è pensabile di eseguire questi controlli dettagliati su tutti gli ingranaggi prodotti: tra parentesi essi non sarebbero neanche di grande utilità.
Controllo in linea degli ingranaggi
Per le produzioni di serie, si può controllare il 100% della produzione con gli ingranometri che permettono un controllo funzionale, chiamato così perché, in certa misura, riproduce le condizioni di impiego delle ruote.
L’ingranometro é un apparecchio di controllo che attraverso la rotazione dell’ingranaggio da controllare accoppiato ad un ingranaggio master, permette di rilevare certi tipi di errore presenti sull’ingranaggio stesso, in tempi relativamente brevi
Si possono considerare almeno due tipi di apparecchi: ingranometri bifianco (con accoppiamento a gioco zero) e ingranomentri monofianco (con accoppiamento con gioco).
Funzionamento dell’ingranometro bifianco
Come si può osservare nella figura 1, l’accoppiamento tra ingranaggio e master avviene con gioco zero, cioè sia il fianco destro che sinistro di un dente sono in contatto.
In queste condizioni, ogni imperfezione di ingranamento obbliga il master a spostarsi in direzione radiale e sono appunto questi spostamenti che saranno rilevati da appositi trasduttori.
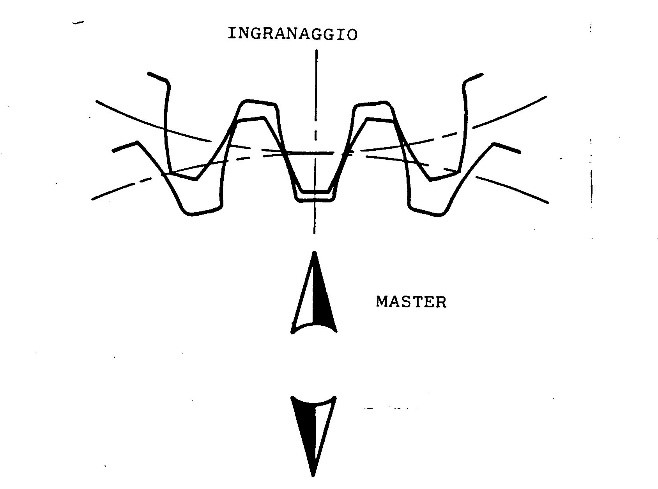
Il limite di questo tipo di ingranometro, che tuttavia resta validissimo per moltissimi impieghi, è costituito dall’inerzia del sistema master-carrello portamaster che non permette di raggiungere sensibilità elevate.
Piccole anomalie, quali ad esempio ammaccature inferiori a 0,01 mm non vengono evidenziate perché sono assorbite dai giochi presenti nelle varie parti mobili e dalla elasticità dei vari organi.
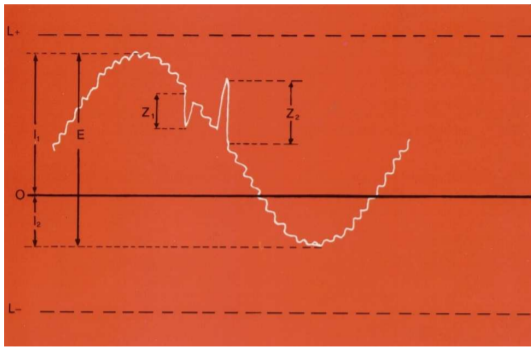
Gli spostamenti radiali del master sono inoltre fortemente influenzati dall’angolo di pressione della dentatura. Infine, naturalmente, non è possibile isolare gli errori relativi ad un fianco da quelli relativi all’altro fianco. Nonostante questi limiti, gli ingranometri a gioco zero hanno molteplici applicazioni nelle linee di produzione.
Per esempio, sono frequentemente usati per controllare gli ingranaggi dopo la dentatura con creatore o coltello stozzatore prima di essere caricati sulla macchina di finitura (rasatrice o rettifica). È un controllo che individua gli ingranaggi con interasse troppo grande, cioè con spessore del dente e quindi con soprametallo eccessivo, oppure con bavature troppo grandi o altre anomalie che possano compromettere la tenuta dell’utensile finitore.
Un’altra frequente applicazione è quella di controllare i pezzi dopo il trattamento termico per individuare i denti con ammaccature che produrrebbero una forte rumorosità sulla trasmissione finita.
Alcuni ingranometri di questo tipo possono essere estremamente semplici; ad esempio, l’ingranometro rappresentato in figura 3 consente di controllare solo la dentatura.
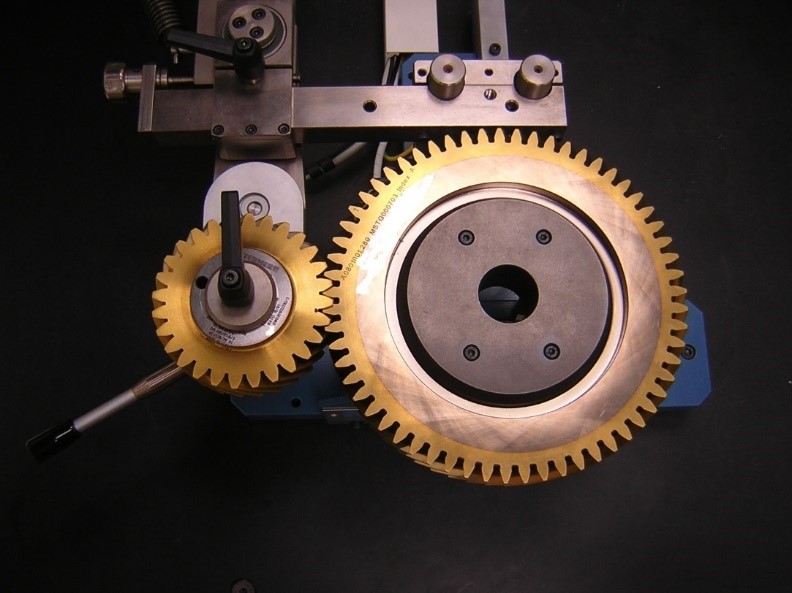
Altri ingranometri, invece, sono più complessi. Nella figura 4 è riportato un esempio di controllo simultaneo di 3 ingranaggi di un alberato.
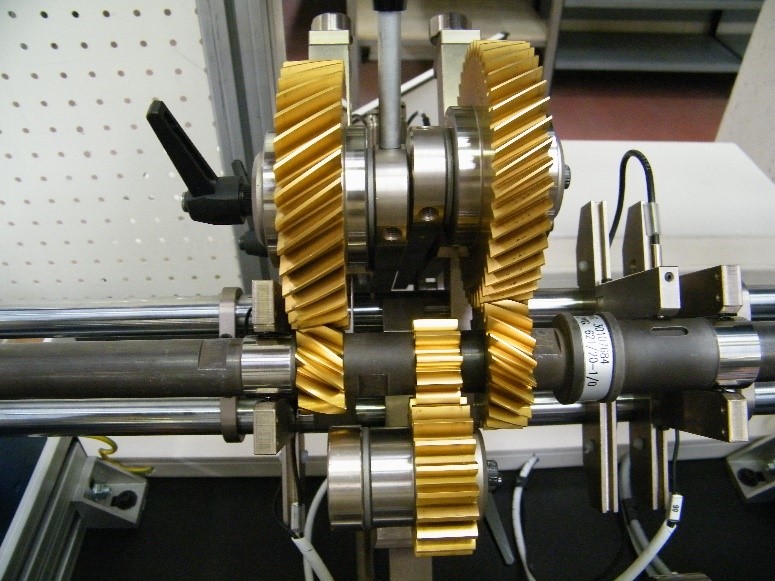
Un altro esempio di ingranometro complesso è quello schematizzato nella figura 5. Oltre al controllo della dentatura si controllano tutti gli elementi della struttura dell’ingranaggio (foro, rasamenti, cono innesto, ecc.), con un totale di 13 trasduttori e una importante strumentazione elettronica.
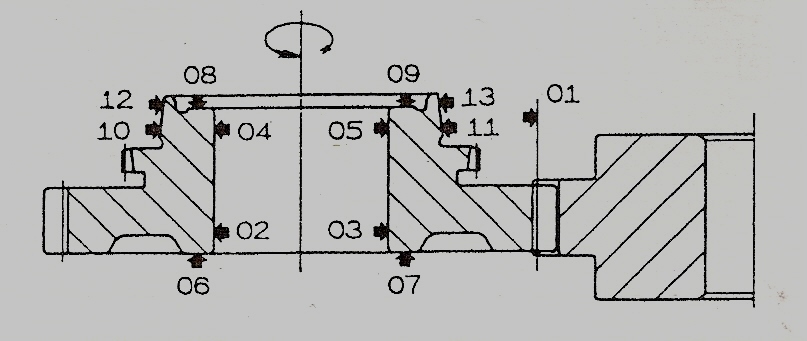
L’ingranaggio master
Abbiamo accennato al master, vediamo che caratteristiche può avere. Il master è un ingranaggio campione che serve essenzialmente per controllare gli ingranaggi prodotti mettendo in evidenza eventuali errori presenti nella dentatura.
Esso viene utilizzato per controllare una vastissima gamma di ingranaggi che possono andare da modulo 0,1 mm a oltre 10 mm e non si limita agli ingranaggi cilindrici, ma si estende anche agli ingranaggi conici e anche alle ruote per viti senza fine.
Senza dubbio però quelli più usati sono quelli destinati agli ingranometri per il controllo di ingranaggi cilindrici a denti dritti o elicoidali. In questo ambito si possono distinguere diversi modi di usare il master.
Quello classico individua sugli ingranaggi gli errori di eccentricità, di interasse e la presenza di eventuali ammaccature generate da urti accidentali. Tutto ciò si fa con gli ingranometri a gioco zero, che sono quelli più comuni e più usati nelle produzioni di grandi serie.
Ci sono poi utilizzazioni più “grossolane”, cioè operazioni in cui non è richiesta una grande precisione dell’ingranaggio campione, perché questo serve essenzialmente come filtro, come barriera, per impedire che ingranaggi che escono da un’operazione di sgrossatura non abbiano gravi imperfezioni che possano danneggiare utensili e macchine nell’operazione di finitura.
Infine, il master può avere una funzione di vero e proprio ingranaggio campione che permette l’esatta regolazione e taratura dell’ingranometro, sia esso a gioco zero o monofianco o perfino di controllare se un più sofisticato apparecchio di misura mantiene la sua precisione nel tempo.
È evidente che per ogni impiego sono necessari master con caratteristiche diverse.
Parlando più specificatamente del master si può dire che il caso più semplice di controllo è quello che si attua dopo un’operazione di dentatura con creatore o con coltello stozzatore e prima di iniziare un’operazione di finitura o con rettifica o con rasatura.
In questo caso è estremamente importante che l’ingranaggio che deve essere finito non abbia gravi errori, come per esempio un dente incompleto o dei raggi di raccordo sul fondo dente troppo grandi, perché in questo caso potrebbe provocare la rottura dei denti del coltello rasatore o gravi danni alla mola di rettifica.
Questi grossi errori possono essere provocati, non molto raramente, da rotture dei denti del coltello stozzatore o da usure anomale sui denti del coltello o del creatore.
Il master destinato a questo controllo, applicato in una semplice apparecchiatura all’entrata della macchina finitrice, non ha particolari esigenze di precisione, ma dovrà essere costruito in modo che durante la rotazione arrivi a toccare tutto il profilo dell’ingranaggio da ispezionare, fino all’inizio del profilo attivo a fondo dente.
Un altro caso di master che non richiede una grande precisione di costruzione è quello che viene usato per il set-up degli ingranometri. In questo caso per la verità si tratta di un vero ingranaggio campione, costruito con le stesse caratteristiche geometriche dell’ingranaggio da controllare. La sola avvertenza è quella di fare il possibile per avere le tolleranze di spessore del dente (o quota sui rulli) a metà tolleranza dell’ingranaggio da controllare, ma in ogni caso è importante sapere quanto è in realtà questo valore, per poter tarare correttamente l’apparecchio di controllo. Per il resto le tolleranze dovrebbero essere all’incirca come quelle dell’ingranaggio o un po’ minori.
Il master vero e proprio, quello che si usa negli ingranometri è invece un ingranaggio molto preciso che si accoppia con l’ingranaggio da controllare. Purtroppo, però, per quanto preciso sia non sarà mai privo di errori.
Questi errori si sovrappongono a quelli dell’ingranaggio introducendo un margine di incertezza nella misura, incertezza che è tanto maggiore quanto meno è preciso il master.
Tralasciando gli errori di profilo e di elica che, nel master, sono solitamente estremamente limitati e praticamente privi di influenza sulla misura degli errori di eccentricità e di interasse, bisogna soffermare l’attenzione su quello che succede nella sovrapposizione dell’errore di eccentricità del master con quello dell’ingranaggio.
La precisione degli ingranaggi, e quindi anche dei master, è definita dalla tabella DIN 3962 e gli errori dipendono dal modulo, dal diametro e dalla classe di precisione che si considera.
Nella tabella 1 sono riportati gli errori di eccentricità ammessi per le classi che possono interessare i master. Vi vede subito intanto che la classe DIN 2 ha degli errori che sono il 50% di quelli di classe DIN 4, ma come si è detto, con le moderne macchine rettificatrici è abbastanza facile ottenere dei master di classe DIN 2.
Modulo | Diametro mm | Classe DIN 2 | Classe DIN 3 | Classe DIN 4 |
1 – 2 | 50 – 125 | 4 | 6 | 8 |
125 – 280 | 5 | 7 | 9 | |
2 – 3,55 | 50 – 125 | 5 | 7 | 10 |
125 – 280 | 5,5 | 8 | 11 | |
3,55 – 6 | 50 – 125 | 5,5 | 8 | 11 |
125 – 280 | 6 | 9 | 12 |
Accoppiamento con gioco
L’accoppiamento tra ruota e controruota, nella quasi totalità dei casi, avviene con gioco.
Ciò vuol dire che l’interasse tra i due ingranaggi è leggermente maggiore di quello teorico e quindi il contatto avviene solo su un fianco del dente.
I due fianchi dei denti di un ingranaggio si identificano in pratica come fianco in tiro e fianco in ritorno, secondo che il contatto su quel dente avvenga durante la trasmissione normale del moto o nella fase di decelerazione della trasmissione. Il motivo per cui gli ingranaggi lavorano in queste condizioni deriva dalla necessità di compensare certi errori di costruzione dell’ingranaggio, primo fra tutti l’errore di eccentricità.
Se supponiamo di lavorare con interasse fisso teorico, cioè con i due fianchi a contatto, anche una piccola eccentricità di una delle due ruote creerebbe una interferenza tale da bloccare la trasmissione.
Anche una leggera maggiorazione dello spessore dei denti procurerebbe lo stesso inconveniente.
Il valore del gioco sui fianchi varia molto da caso a caso e dipende dal tipo di trasmissione, dalla potenza trasmessa, dal modulo, ecc. Per i cambi automobilistici l’entità del gioco non si discosta molto da 0,1 mm.
È importante quindi disporre di uno strumento che indichi se l’accoppiamento in queste condizioni avviene in maniera corretta, uno strumento cioè, che simulando le condizioni di funzionamento, evidenzi gli errori di ingranamento.
Bisogna precisare che in realtà durante il funzionamento della trasmissione i denti dell’ingranaggio sono soggetti a forze che modificano la condizione di un puro rotolamento come avviene nel caso del controllo con l’ingranometro monofianco.
Quindi, la simulazione del controllo è solo approssimativa e serve solo per evidenziare alcuni errori geometrici; non va intesa come prova di funzionamento, anche perché molte altre condizioni non sono rispettate, come ad esempio la velocità di rotazione dell’accoppiamento.
Il rumore generato da una coppia di ingranaggi che ingranano girando ad una certa velocità, dipende da una serie di fattori non tutti ancora ben identificati.
In sostanza si tratta di vibrazioni provocate da anomalie nell’accoppiamento, cioè di variazioni istantanee della velocità angolare. La frequenza e l’ampiezza di queste vibrazioni determinano rispettivamente l’acutezza del rumore e la sua intensità.
L’analisi con il metodo di Fourier delle vibrazioni generate da una coppia di ingranaggi in moto mette in evidenza che ogni singola onda di vibrazione è la sovrapposizione di onde di varie frequenze, il che significa che molte differenti irregolarità entrano in gioco provocando il rumore.
Se durante la trasmissione del moto, ad una certa velocità angolare W1 dell’ingranaggio conduttore corrisponde sempre, in ogni singolo istante, una velocità angolare W2 dell’ingranaggio condotto, la trasmissione è silenziosa.
Ma se sul fianco di un dente è presente una irregolarità tale da far variare per un istante la velocità W2, tale irregolarità diventa una fonte di vibrazioni e quindi di rumore. Nella figura 6 è indicato quello che succede nell’istante Δt.
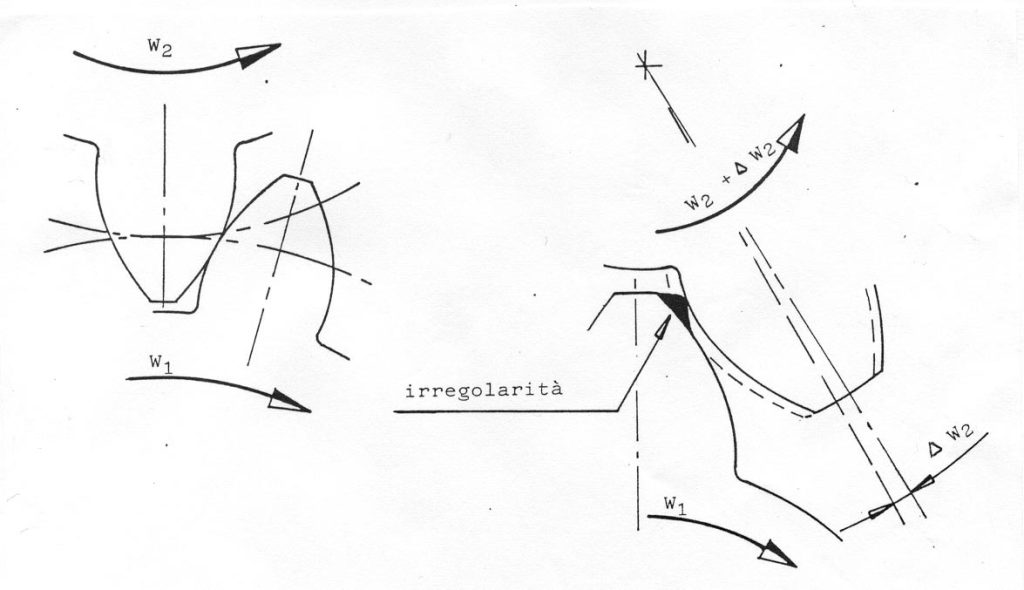
Funzionamento dell’ingranometro monofianco
L’ingranometro monofianco, che lavora come indicato in figura 7, ha una sensibilità molto maggiore perché mette in evidenza gli scostamenti angolari del master rispetto alla rotazione teorica.
Ci si rende subito conto che in primo luogo l’inerzia è molto minore e quindi maggiore sarà la velocità di risposta del sistema ed in secondo luogo che i giochi nei vari collegamenti possono, in questo caso, essere ridotti quasi a zero, elevando la sensibilità della misura.
Tutte le imperfezioni che si evidenziano in questo modo sono quelle che saranno presenti nel funzionamento dell’ingranaggio montato nella scatola cambio, tenendo sempre presente però che le condizioni reali sono alquanto diverse (forze, velocità ecc.).
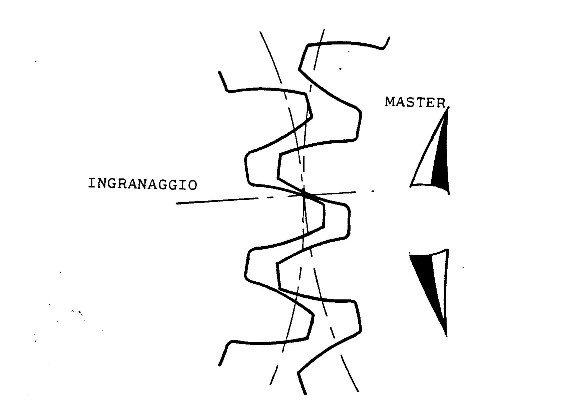
Se il controllo di questo tipo non mette in evidenza errori, significa che l’ingranamento è corretto e quindi, in assenza di altre cause, il funzionamento è silenzioso.
Questo controllo cumulativo permette di saltare il controllo metrologico completo dell’ingranaggio, con evidenti vantaggi di tempo. L’ingranometro monofianco rileva, come si è detto, con particolare precisione, su un fianco alla volta i seguenti errori:
- errore composto tangenziale (sommatoria di errori di divisione, errori di profilo, distorsione, ecc.);
- valore del gioco con un interasse prefissato;
- entità delle ammaccature.
Esistono diversi tipi di ingranometri di questo tipo sul mercato, ma tutti i sistemi si basano sul principio di confrontare la rotazione teorica dell’accoppiamento con quella effettiva ed evidenziarne le differenze.
La comparazione tra rotazione teorica e reale può avvenire in molti modi; ad esempio, impiegando la tecnologia dei controlli numerici, oppure misurando la velocità di rotazione del master e dell’ingranaggio con dischi ottici.