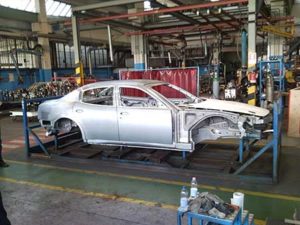
Com’è noto, con il termine “scocca” si intende il “rivestimento esterno” delle automobili, composto in genere da molti elementi (cofano, fiancate, longheroni, ecc.), il cui scopo principale è sia quello di sostenere le parti meccaniche (motore, cambio, trasmissione, ecc.) e fungere da telaio, sia di svolgere funzioni estetiche e di carrozzeria.
Grazie al progresso delle tecnologie di progettazione e di produzione, e grazie all’introduzione di materiali sempre più “performanti”, le case automobilistiche stanno studiando e introducendo sul mercato scocche e componenti sempre più originali e ricercati, al fine di migliorare non solo le prestazioni funzionali, ma anche le caratteristiche estetiche ed ergonomiche generali delle vetture.
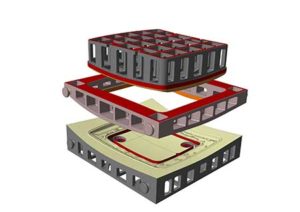
Tra la progettazione e l’immissione sul mercato, tuttavia, vi è una lunga e complessa fase di studio, di realizzazione dei prototipi, di test, di modifica delle matematiche progettuali, ecc., fase necessaria all’ingegnerizzare di tali prodotti e alla relativa valutazione della fattibilità tecnica e commerciale. Le case automobilistiche, nella maggior parte dei casi, si appoggiano per tali attività ad aziende specializzate; si tratta di aziende che devono essere dotate di tecnologie diverse e all’avanguardia, con anni di esperienza nel settore e con personale adeguatamente formato, organizzate inoltre in modo da operare nella maniera più rapida ed efficace possibile.
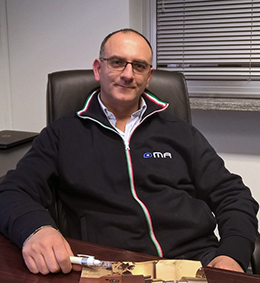
Un’eccellenza italiana
Non sono molte le imprese che vantano requisiti così elevati in tale ambito, ed è per questo che la nostra rivista ha deciso di fare la conoscenza di una delle più importanti aziende del settore operanti in Europa: la OMA S.r.l. di Leinì (TO), realtà che sviluppa soluzioni all’avanguardia nella realizzazione di prototipi per le più importanti case automobilistiche di tutto mondo. Il Managing Director, Gerardo Varriale, racconta: «OMA effettua l’analisi dei modelli matematici preparati dai nostri clienti, cioè dalle case automobilistiche, e realizza i relativi prototipi in lamiera ingegnerizzando e simulando i processi produttivi». Inoltre offre un servizio all’avanguardia anche nell’ambito della progettazione, della costruzione e della messa a punto dei relativi stampi di modellazione a freddo della lamiera. Precisa Varriale –, riusciamo a realizzare non solo le attrezzature per l’esecuzione dei pezzi prototipali ma anche, nel caso in cui il cliente lo richieda, le attrezzature finali, cioè gli stampi definitivi che vengono utilizzati direttamente presso le linee di lastratura del cliente finale per la produzione in serie». Queste attività rendono OMA una realtà con pochi eguali nel mondo automotive, in quanto la maggior parte delle aziende che opera nel settore si ferma in genere all’esecuzione dei particolari prototipali in lamiera. «Gli oltre 150 addetti precisa Varriale – agiscono in stretta sinergia con l‘obiettivo di offrire ai nostri clienti un know-how completo, oltre che soluzioni rapide, efficienti, convenienti e di alta qualità».
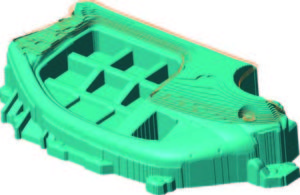
Ingegnerizzazione prodotti
Le case automobilistiche si rivolgono ad aziende come OMA con lo scopo di produrre in serie scocche nuove, o parti di esse, di qualità sempre maggiore e nel più breve tempo possibile, abbattendo i costi, le incertezze e i rischi legati all’ingegnerizzazione di prodotti sempre diversi e alla costruzione delle relative attrezzature. Gerardo Varriale spiega: «Dal momento in cui riceviamo le matematiche dei pezzi da parte delle case automobilistiche, inizia il nostro lavoro. Sono preliminarmente eseguiti studi di fattibilità su ogni singolo componente e, una volta definita la configurazione ottimale, vengono realizzate le attrezzature per la realizzazione dei primi prototipi; l’attività prosegue poi con le lavorazioni di finitura e completamento, come per esempio il taglio laser e gli aggiustaggi manuali, sino alla realizzazione definitiva dei prototipi. Su richiesta, verifichiamo ed eseguiamo anche l’assemblaggio di più parti, realizzando così interi telai o scocche prototipali».
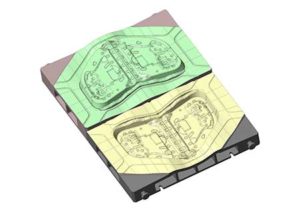
Ogni prototipo viene richiesto in un numero ridotto di esemplari, in genere da poche unità sino a un massimo di qualche centinaio, a seconda delle necessità del cliente; per esempio, possono servire per realizzare alcune vetture di prova o da esposizione, oppure per testare l’avviamento delle linee di assemblaggio delle proprie vetture. Varriale: «Il valore aggiunto della nostra attività, come detto, è che noi possiamo realizzare anche gli stampi definitivi ed eseguire il loro montaggio presso le linee di produzione dei clienti. Possiamo inoltre effettuare direttamente lo stampaggio dei pezzi definitivi all’interno del nostro stabilimento e consegnarli successivamente al cliente, proponendoci così come contoterzisti completi».
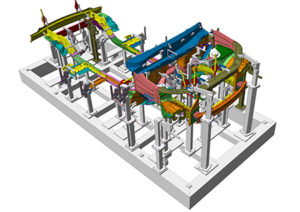
per montaggio e saldatura.
Studio di fattibilità
Entriamo ora nel “dettaglio tecnologico” del ciclo di produzione. La prima fase è quella dello studio di fattibilità. Una volta acquisite le matematiche dal cliente, l’ufficio tecnico della OMA esegue i primi studi teorici; viene, in particolare, simulato il comportamento del materiale durante l’operazione di imbutitura. Varriale: «Cerchiamo di prevedere il comportamento della lamiera durante la fase di deformazione sotto pressa; ciò viene effettuato al calcolatore mediante software di calcolo assai evoluti e specifici, come per esempio quelli della AutoForm Engineering e VISI Progress della Vero Solutions. Cerchiamo di prevedere i “ritorni” elastici del materiale, gli eventuali punti di rottura, i problemi estetici, se vi sono parti fuori tolleranza, ecc. Valutiamo di conseguenza eventuali modifiche e migliorie, variando forme e materiali. Ovviamente, qualsiasi modifica deve essere concordata e autorizzata dal cliente». In questa fase è fondamentale, soprattutto, valutare la “risposta” dei materiali proposti dal cliente, materiali che possono essere acciai speciali e leghe di alluminio di nuova concezione, per cui non è semplice prevederne il comportamento sotto pressa. Varriale: «Il nostro lavoro è quello di validare le proposte delle case automobilistiche. In caso di simulazioni e test non soddisfacenti o di impossibilità di raggiungere i risultati sperati, non possiamo che consigliare al cliente l’utilizzo di materiali differenti».
Una volta completati gli studi di fattibilità mediante le simulazioni di imbutitura, si passa alla realizzazione dei prototipi per il riscontro definitivo su pressa. Se in fase di stampaggio insorgono nuovi problemi non immediatamente evidenziati nella fase di simulazione al calcolatore, il processo viene iterato fino al raggiungimento del risultato ottimale. A questo punto le matematiche dei pezzi vengono “congelate” per passare alla realizzazione delle attrezzature, cioè degli stampi necessari alla realizzazione dei prototipi.
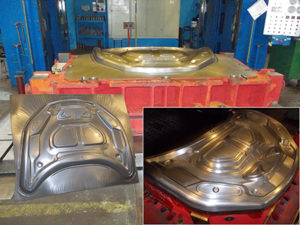
Realizzazione degli stampi “leggeri”
«Quelli che noi realizziamo – puntualizza Varriale – sono “stampi leggeri”, cioè attrezzature velocemente costruibili rispetto a quelle normalmente adoperate per la produzione in serie, essendo destinate alla produzione di pochi particolari. Nel nostro mestiere le date di consegna dei prototipi sono categoriche e non contrattabili, e dunque è per noi fondamentale costruire stampi di imbutitura e flangiatura in maniera veloce al fine di rispettare i tempi di consegna, tempi che in genere sono veramente stretti».
Tali stampi, normalmente di medie e grandi dimensioni, vengono progettati mediante CAD/CAM d’ultima generazione come per esempio VISI Modelling di Vero Solutions; e sono costruiti all’interno dello stabilimento, nel quale lavorano fresatrici a CNC di grandi dimensioni, tra i quali quali spiccano alcune macchine della Mecof e della Forest.
Varriale: «Ciò che rende uno stampo “leggero” è, in genere, il metodo di progettazione ed il materiale con cui viene costruito. Noi scegliamo i materiali valutando di volta in volta sia il tempo di approvvigionamento sia i costi di lavorazione». In genere, i punzoni che tranciano la lamiera o che devono eseguire deformazioni gravose, sono realizzate in acciaio; le parti che invece eseguono deformazioni meno spinte o che costituiscono l’involucro esterno dello stampo vengono realizzate in ghisa. In caso in cui occorre grande velocità di esecuzione, gli stampi sono lavorati dal pieno, in quanto il materiale grezzo può essere reperito con maggiore facilità, a fronte tuttavia di maggiori costi di lavorazione. Nel caso invece in cui le tempistiche lo permettano, i pezzi vengono lavorati da semigrezzi fusi. Varriale osserva: «Un semigrezzo da fusione ha una forma molto vicina a quello dello stampo definitivo, quindi la relativa lavorazione meccanica risulta assai più economica rispetto a quella dal pieno. Tuttavia, i tempi di approvvigionamento di una fusione sono assai più lunghi, non inferiori alle 4 settimane, dato che è necessario rivolgersi a ditte esterne per l’esecuzione del modello in polistirolo e alle fonderie specializzate per la realizzazione del fuso vero e proprio».
Insomma, nella costruzione di un “soft-tooling” occorre valutare più fattori, quali il tipo di deformazione da imprimere, la qualità dei materiali, i tempi di approvvigionamento, i costi delle lavorazioni, ecc., e trovare di volta in volta soluzione migliore in termini di garanzia dei risultati, velocità ed economicità.
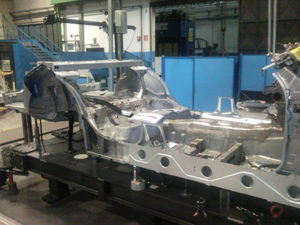
Stampi da fusione: l’importanza del polistirolo
Per realizzare una fusione, le attrezzerie si rivolgono ad aziende specializzate nella produzione di modelli in polistirolo. Tali aziende, partendo dalle matematiche a loro consegnate, definiscono la forma e le dimensioni del modello in polistirolo cercando di approssimare il più possibile la sagoma dello stampo finito. In tale attività, si avvalgono di software speciali per definire i “tagli” del materiale, per evitare i sottosquadra e per definire i “sovrametalli”, i quali sono in genere compresi tra i 10 e i 20 mm e possono variare a seconda del tipo di stampo e del livello di avanzamento (“step”) del progetto generale della vettura: più lo step è avanzato, più accurata può essere la fusione e minore il sovrametallo. Il modello in polistirolo, lavorato mediante macchine utensili specifiche e successivamente assemblato è pronto per essere consegnato alla fonderia. Qui è trattato superficialmente con particolari vernici che ne induriscono la superficie; viene poi staffato all’interno di una forma che sarà riempita di una sabbia speciale resistente alle alte temperature. Una volta indurita anche la sabbia, il metallo fuso viene colato all’interno della forma; il metallo fonde il polistirolo e, raffreddandosi, ne assume la forma. In tal modo è ottenuto un elemento metallico (di ghisa o acciaio) corrispondente al modello iniziale di polistirolo, il quale a sua volta rappresenta la sagoma dello stampo. Tale elemento metallico viene quindi consegnato alla attrezzeria, che, mediante lavorazioni d’asportazione truciolo, lo trasformerà nello stampo richiesto.
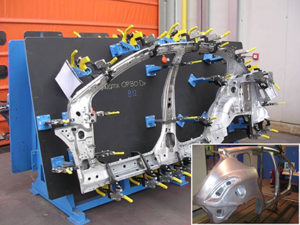
Stampaggio e lavorazioni finali
Lo stampo, una volta realizzato, è posizionato su pressa per la realizzazione dei pezzi tranciati e imbutiti. Tale attività viene svolta all’interno dello stabilimento della OMA, in cui sono installate diverse presse di stampaggio a freddo della lamiera, tra cui una pressa Müller da 2.000 ton, una Gigant da 1.200 ton, una Rovetta da 1.000 ton e altre presse più piccole da 500 e 250 ton. «Nell’eseguire lo stampaggio, ovviamente, utilizziamo le lamiere del materiale “definitivo” scelto dalla casa automobilistica; in genere si tratta di acciai di qualsiasi tipo, anche alto-resistenziali, e leghe di alluminio» continua Gerardo Varriale.
Una volta imbutito, il particolare viene tagliato con l’ausilio dei laser e lavorato su eventuali successivi stampi di flangiatura. Varriale: «Disponiamo di due Optimo, cioè due macchine di taglio laser a CO2 di Prima Power, con le quali eseguiamo eseguiamo le attività di rifilatura e foratura dei particolari.». Successivamente, i pezzi vengono ripresi dai battilastra, operatori specializzati “alla vecchia maniera” nella lavorazione a mano della lamiera. «L’aspetto artigianale nel nostro lavoro è ancora fondamentale – racconta Varriale – soprattutto nell’esecuzione di scocche di un numero limitato di veicoli sperimentali, i cosiddetti “mulotipi”, per esempio per allestimenti fieristici o saloni espositivi, in cui l’industrializzazione è un aspetto meno rilevante. L’abilità manuale è parte integrante del nostro know-how».
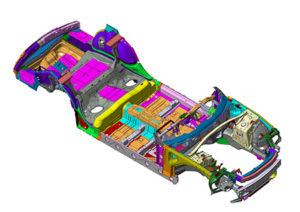
Controllo qualità e assemblaggio
Una volta realizzati, i componenti prototipali devono superare la fase di controllo qualità all’interno del reparto metrologico, in cui sono presenti macchini di misura a coordinate manuali ed automatiche. Varriale: «La fase di misura e controllo è fondamentale in quanto i pezzi, pur essendo prototipi, devono essere uguali, per dimensioni, precisioni ed estetica, ai pezzi che successivamente saranno prodotti in serie. Quindi occorre verificare che rispettino le stringenti tolleranze del progetto».
Successivamente, se richiesto dal cliente, viene eseguito il montaggio delle parti: «L’assemblaggio è un’attività da svolgere nel minor tempo possibile e per nulla semplice, soprattutto se si tratta di insieme complessi. Si pensi per esempio a una fiancata: la “pelle esterna” è un pezzo unico, ma se viene richiesto l’intero componente, occorre montare anche le piccole sottoparti prototipali interne, che sono circa una quarantina, ognuna delle quali va realizzata secondo il procedimento prima descritto». Per la realizzazione di una scocca intera possono essere sviluppati e montati addirittura diverse centinaia di pezzi, tutti diversi l’uno dall’altro, costruendo le relative attrezzature. Varriale: «Dalla ricezione delle matematiche alla consegna dei primi pezzi possono passare 3-4 settimane per i componenti singoli, e fino a 5 mesi per la realizzazione di una scocca completa». Senza contare che se la casa automobilistica, durante gli step e i continui aggiornamenti progettuali della vettura, varia anche solo un piccolo elemento, occorre ridisegnare, adeguare e riprodurre pressoché tutti gli altri elementi costituenti l’insieme e le relative attrezzature. Gerardo Varriale conclude: «È un lavoro davvero difficile ed è per questo che serve efficienza, tecnologia, organizzazione interna e flessibilità. È questa la nostra forza, è questo il nostro valore aggiunto».
Qui nascono vetture “celebri”
Diverse sono le vetture “celebri” che OMA ha contribuito a realizzare mediante la fornitura di scocche complete e componenti. Tra le quali, ricordiamo la nuova Panda FIAT, il fuoristrada Lada Niva e, soprattutto, la Ghibli Maserati «Abbiamo lavorato sulla Ghibli per diversi mesi– racconta Gerardo Varriale –. I primi mulotipi sono stati realizzati addirittura a mano mediante stesa di speciale resina in fibra di carbonio. Poi abbiamo eseguito tutti i centinaia di pezzi prototipali in lamiera e le relative attrezzature. Davvero un bel lavoro».
Una finestra sul mercato
Gerardo Varriale commenta l’attuale fase di mercato: «Il periodo è di buona crescita. I nostri clienti sono le maggiori case di costruzioni di automobili del mondo, e cioè FIAT, Alfa Romeo, Maserati, Daimler, PSA Peugeot Citroën, BMW, ecc., e i più importanti fornitori di componentistica per automobili, quali Magma Group e Gestamp. Attualmente, lavoriamo poco per l’industria italiana, mentre sembra più frizzante quella tedesca; non a caso stiamo sviluppando molti componenti per BMW e per i diversi marchi di Daimler, tra cui Mercedes. In questa fase, l’industria tedesca costituisce circa i due terzi del nostro fatturato».