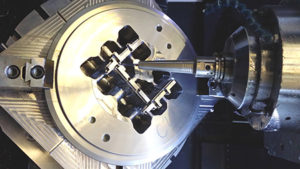
Velocità, ricerca, innovazione e personalizzazione: sono queste le parole chiave che da sempre contraddistinguono la crescita strutturale e organizzativa che ha portato Alumat a crescere e a potenziare la propria capacità produttiva, divenendo punto di riferimento del mercato nazionale e internazionale di matrici.
«Alumat è stata costituita nel 1993 a Ciserano, in provincia di Bergamo – spiega l’amministratore delegato ing. Emanuele Astolfi – grazie all’iniziativa di Piermario Locatelli e Giambattista Viola, ancora oggi soci di riferimento, e grazie alla loro pluriennale competenza tecnica e commerciale maturata nel mondo delle matrici per estrusione di alluminio».
A distanza di una decina d’anni, nel 2004, l’azienda rileva la trentina Almax Mori, costituendo un Gruppo che oggi comprende anche la greca Matrex, per un organico complessivo di un centinaio di persone, chiamate a soddisfare le esigenze del complesso e competitivo mondo dell’estrusione.
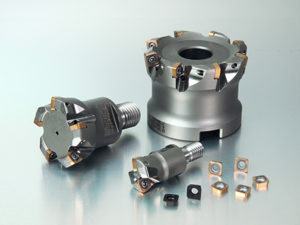
«Aziende che sfruttano questa sinergia di competenze mantenendo comunque la loro identità storica – aggiunge l’ing. Astolfi – col preciso scopo di porsi e differenziarsi sul mercato in modo dinamico, snello, con tempi di risposta rapidi e tempi di consegna delle matrici sempre più brevi. A tutto vantaggio di un trasferimento tecnologico sul quale basare la loro crescita».
Obiettivi perseguiti grazie all’adozione di sistemi evoluti per la progettazione Cad/Cam 2D e 3D, tecnologie avanzate per la lavorazione Cnc dei prodotti, investimenti in formazione continua del personale e in processi di ottimizzazione organizzativa. A questo proposito è in corso da qualche tempo un profondo processo di rinnovamento e di riorganizzazione operativa globale, finalizzata a migliorare ulteriormente l’iter che porta la matrice dal progetto al prodotto. Tutto ciò tenuto conto che annualmente, a livello di Gruppo, si producono circa 12mila matrici/anno (composte a loro volta da 2-3 elementi), per un totale di oltre 30mila pezzi lavorati.
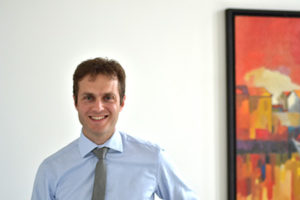
«Gestire in modo efficiente ed efficace tali numeri – sottolinea l’ing. Astolfi – richiede interventi mirati e l’impiego di tecnologie in grado di soddisfare determinati requisiti che possano garantire un posizionamento adeguato sul mercato».
In questo contesto si colloca la partnership instaurata da qualche tempo dal Gruppo con MMC Hitachi Tool, per sviluppare un progetto di ottimizzazione di processo attraverso la fornitura di una diversificata gamma di frese di lavorazione e relativa mandrineria.
Massima efficienza e qualità di processo
«Elemento importante e distintivo della collaborazione instaurata con MMC Hitachi Tool – rileva lo stesso ing. Astolfi – è stato sin da subito il tipo di approccio, basato non su una mera fornitura di prodotto, bensì sulla messa a punto di un progetto deputato a migliorare integralmente e progressivamente i processi, ad adeguare le strategie di lavorazione, e a rendere le stesse più performanti».
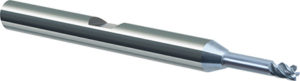
Il supporto, coordinato dal responsabile Gabriele Casanova e dallo staff tecnico di MMC Hitachi Tool, in sinergia con i referenti tecnici di Alumat e di Almax Mori, ha portato all’individuazione delle prime aree operative dove i margini di miglioramento in termini di efficienza rappresentavano una priorità. Più nello specifico la fase legata alle lavorazioni di sgrossatura, dove l’obiettivo è stato quello di restituire una sensibile riduzione dei tempi di lavorazione, con un’affidabilità e stabilità di processo senza compromessi, da replicare su un cospicuo numero di centri di lavoro su più turni.
«Concluso con successo questo primo step – prosegue l’ing. Astolfi – siamo passati all’analisi e alle possibili migliorie apportabili in futuro anche alle finiture, con utensili in metallo duro».
Dalle strategie di lavoro, ai percorsi Cam, ai materiali, allo staffaggio, alle attrezzature: un supporto tecnico a 360 gradi, quello messo a disposizione da MMC Hitachi Tool, capace di apportare decisive e mirate scelte migliorative, con il preciso obiettivo di ottenere una sensibile riduzione dei costi di produzione e, di conseguenza, anche maggiori margini operativi.
Differenti esigenze che ricalcano le due grandi macro-aree operative di interesse così identificabili: quella di sgrossatura, dove il materiale viene lavorato prima della tempra; quella di finitura, sempre fatta su centro di lavoro, dove invece il materiale è temprato e dove sono richieste determinate tolleranze e qualità superficiali.
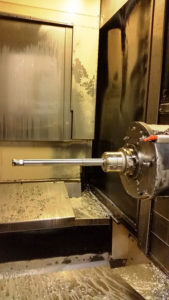
mm impiegate comunemente
nelle lavorazioni ad elevati sbalzi utensile (300 mm).
Dire, fare, sgrossare
Nel processo di rinnovamento tecnologico citato sono stati impiegati e verranno in futuro implementati numerosi utensili MMC Hitachi quali, le frese serie ASRF mini, serie EPSM e quelli appartenenti alla gamma ASR.
Frese ad alto rendimento, grazie ai 4 lati per tagliente, le frese ASRF mini consentono di rendere efficiente e, nel contempo, economica l’operazione di sgrossatura. La particolare geometria dell’inserto, unita al posizionamento nel corpo fresa, contiene gli sforzi di taglio permettendo di lavorare anche con sbalzi utensili molto elevati (rapporto L/D superiore a 10) sia su centri di lavoro ISO50, sia su ISO40. Stiamo parlando di un’esecuzione con la quale è possibile raggiungere carichi al tagliente fino a fz 1,5 mm mantenendo profondità di passata veramente elevate. Gli inserti possono beneficiare di micrograne e rivestimenti MMC Hitachi di ultima generazione, non soggetti a problemi di shock termico e quindi utilizzabili sia con emulsione, sia con aria per adattarsi alle più svariate applicazioni/macchine/materiali.
La sigla EPSM contraddistingue invece una serie di frese in metallo duro integrale rivestite con tecnologia Panacea, rivestimento a coefficiente d’attrito molto basso e con eliche taglienti a suddivisione angolare differenziata. Per come concepita e sviluppata permette sgrossature versatili, dal pieno, a elevata efficienza grazie al “double gash”, ovvero alla doppia gola di scarico, e alla doppia affilatura del tagliente oppure in Z costante alto avanzamento per macchine più dinamiche e meno rigide.
Definiti per eccellenza le frese da sgrossatura alto avanzamento, programmabili con R = 2 mm, gli utensili serie ASR consentono carichi a tagliente molto elevati (fino a fz > 2 mm) e sbalzi notevoli; sfrutta l’ultima tecnologia MMC Hitachi con micrograne e rivestimenti di ultima generazione, anche in questo caso non soggetti a problemi di shock termico.
La soddisfazione espressa da Alumat, ha convinto i vertici dell’azienda a estendere questo processo di rinnovamento tecnologico (che poi riguarderà, a seguire, anche il parco produttivo presente in Almax-Mori) anche alle fasi di finitura. Sono infatti in atto alcuni test su temprato con utensili serie HGOS e HGOH sempre forniti da MMC Hitachi.
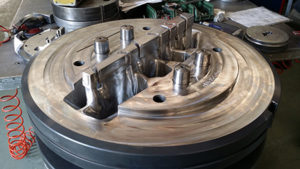
Matrici piane o cave, ma di assoluta qualità
Tecnologia in continua evoluzione, quella messa a punto, al servizio della produzione di stampi in acciaio, intesi come matrici piane e matrici cave (note anche come porthole). Ben più complesse queste ultime, ma verso le quali spicca ed emerge la maggior specializzazione e competitività espressa dal Gruppo.
«Matrici – specifica l’ing. Astolfi – che trovano principale applicazione nell’estrusione di profili di alluminio sia nel settore edilizio, sia nel più diversificato comparto industriale. Per quest’ultimo serviamo con maggiore prevalenza il settore automotive inteso nella sua accezione più ampia e comprendente per esempio matrici per componenti meccanici vari per auto, per sponde di mezzi mobili, fino a strutture di mezzi ferroviari».
Matrici circolari che, in varia misura, sono compresi in un range che va da un minimo di 150 a un massimo di 850 mm. «In Alumat – precisa l’ing. Astolfi – storicamente venivano realizzate matrici in un range dimensionale inferiore rispetto a quello di Almax Mori. La strategia in atto è quella comunque di avere una dotazione in termini di know-how e capacità produttiva che permetta a entrambe le aziende di coprire il range completo».
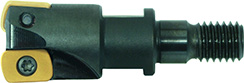
serie ASR-Pico consentono carichi a tagliente molto elevati e sbalzi notevoli.
Dal progetto all’oggetto
Il Gruppo Alumat-Almax è dunque in grado di soddisfare le diverse esigenze assicurando il controllo e la gestione di tutto l’iter di sviluppo di prodotto, dal progetto all’oggetto.
«Un complesso iter – sottolinea l’ing. Astolfi – che inizia con lo sviluppo progettuale, la modellazione Cad, la programmazione Cam, per poi passare in officina con il taglio delle barre, la loro tornitura, la loro sgrossatura, la tempra (che avviene grazie all’apporto di subfornituri esterni ndr), la finitura ai Cnc. Si prosegue poi con la lavorazione dei diversi pezzi nel reparto di erosione a filo per la matrice e a tuffo per il cuore, la loro finitura manuale, l’assemblaggio e il controllo qualità finale. Fasi che si svolgono mediamente in un tempo medio di 7 giorni, dove la pianificazione gioca un ruolo preponderante per il rispetto delle tempistiche previste col cliente, e dove l’affidabilità del parco macchine e degli utensili impiegati deve essere ai massimi livelli».
Da segnalare che tra la fase di sviluppo Cad e Cam, non di rado si ricorre a una fase di simulazione dell’estrusione che permette la realizzazione di uno stampo produttivo sin da subito. Attività, questa, nella quale il Gruppo ha maturato negli anni una notevole esperienza e una posizione di assoluta leadership mondiale. Grazie agli studi, all’implementazione operativa di un software di simulazione dell’estrusione finalizzato al processo di produzione interna, i tecnici sono infatti riusciti a definire le migliori strategie preventive dei più frequenti problemi di estrusione (rotture, flessioni, spostamenti, difetti superficiali).
«Tempi di consegna sempre più rapidi – conclude l’ing. Astolfi – con una produzione sempre più efficiente, grazie anche al supporto e agli utensili MMC Hitachi Tool. In sintesi, matrici di qualità, subito produttive presso il nostro cliente. È questa la sinergia verso la quale ci stiamo concentrando, affinché la stessa possa elevare ulteriormente il nostro grado di competitività e di consolidamento nel mercato, nazionale e internazionale».
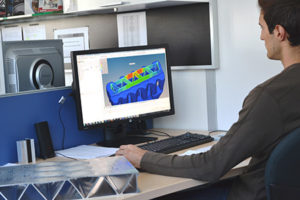
Specialisti in matrici per l’estrusione di alluminio
Alumat nasce a Ciserano (BG) nel 1993, divenendo in breve tempo protagonista del mercato nazionale e internazionale di matrici. Tra gli step decisivi di crescita dell’azienda risulta chiave il 2004, anno nel quale nasce l’alleanza strategica con la trentina Almax-Mori, della quale rileva la maggioranza delle quote. Due realtà che ancora oggi uniscono le loro forze per giocare fianco a fianco la sfida di soddisfare una clientela sempre più esigente per qualità e tempi di consegna. Uno scambio trasversale di competenze e know-how che permette ai clienti di poter contare su validi e qualificati partner chiamati a migliorare costantemente la tecnologia dell’estrusione e del suo potenziale. Due aziende che costituiscono oggi un gruppo composto da circa un centinaio di dipendenti, egualmente suddivisi, che svolgono la stessa attività ma che, per precisa scelta strategica, hanno deciso di mantenersi indipendenti su diversi aspetti per potersi distinguere grazie all’elevata flessibilità e snellezza operativa. Quindi una strategia non basata sull’accentramento, ma sul mantenimento della propria identità per valorizzare tutte quelle competenze maturate negli anni. Un approccio che ha consentito al Gruppo di ampliare le aree di mercato, consolidando al tempo stesso la presenza in termini di continuità storica. Insistenza su mercati di riferimento che per il 65% della produzione significa un’esportazione destinata oltre confine, per un fatturato globale che si attesta sui 16milioni di euro. Dall’Europa all’America, all’Asia, al Nord Africa e Medio Oriente, le aziende portano un know-how tutto italiano in tutti i principali Paesi, mostrando una vision imprenditoriale nella quale confluiscono i benefici di una gestione famigliare e un’impronta manageriale. A garanzia di questa continuità gestionale si inserisce, nel 2013, l’incarico all’ing. Emanuele Astolfi in qualità di amministratore delegato in Alumat. Innesto al quale segue nel 2014 l’apertura di Matrex, unità di servizio sita a Salonicco, in Grecia, dove operano una decina di dipendenti che presidiano dal punto di vista tecnologico e operativo l’area balcanica. La neonata Matrex vanta comunque al suo interno tutti i reparti produttivi, dalla progettazione a macchine di lavorazione, che le consentono in autonomia di realizzare il prodotto finito. Rafforzamento manageriale e di organizzazione produttiva, dunque, quale spinta propulsiva per vincere nuove sfide di mercato seppur mantenendo, come già sottolineato, identità indipendente delle aziende del Gruppo.
Un partner qualificato e affidabile per la fresatura di stampi e matrici
Multinazionale giapponese operante nel settore della produzione di utensili, MMC Hitachi Tool si rivolge ad aziende che svolgono lavorazioni meccaniche e, soprattutto, a realtà produttrici di stampi per offrire una gamma di utensili in grado di coprire tutte le fasi del processo produttivo. Presente in Italia sin dal 2004 con una propria filiale diretta a Iseo (BS) dove operano attualmente una ventina di persone (di cui una quindicina sono figure tecnico-commerciali), mette a disposizione un’ampia scelta di soluzioni in grado di soddisfare le più diverse esigenze. Nel proprio settore, grazie al know-how e all’esperienza sviluppata nel tempo, l’azienda è riuscita a determinare gli standard, sia per l’ampiezza e la profondità del suo assortimento, sia per la capacità di fornitura. La qualità dei prodotti abbinata a una specifica attività di consulenza e supporto applicativo, ne fanno un affidabile partner sul quale poter contare in tutte le fasi di fresatura di stampi e matrici. Esempio concreto di tale approccio è testimoniato anche dal rapporto di partnership intrapreso con il Gruppo Alumat-Almax raccontato in queste pagine.
Una risposta
Buon giorno ing. EMANUELE ASTOLFI mi congraturo con Lei per la capacità dimostrata per ottenere una qualiutà decisamente elevata ividiata ad molti
questo non è un pensiro di contorno ma è realtà
Sono commerciale della t.t.valtemper azienda di trattamento termico, sarebbe un onore cooperare con Voi sicuro di personalizzare il tratatmento termico alla vostra produzione e qualità con consegne più volte durante la giornata
possiamo anche valutare un prezzo molto vantaggioso
Ringrazio cordiali saluti
Franchi tel 3927512575
I commenti sono chiusi.