Le case automobilistiche pensano e sviluppano oggi le macchine del domani, cercando di anticipare tendenze ed esigenze molto spesso in continuo divenire. Progetti non necessariamente futuristici, ma che devono comunque essere attentamente valutati ed eventualmente modificati per aderire meglio a quanto il mercato potrebbe richiedere, ed entrare così in produzione. In questo contesto la prototipia gioca un ruolo fondamentale, attività nella quale la torinese CO.ST.AT. ricopre dal 1998 un ruolo da sicura protagonista.
L’azienda, con sede a Piobesi Torinese, si occupa infatti del completo ciclo di sviluppo di un prototipo in ambito automotive. «Riceviamo dalle case automobilistiche nostre clienti – spiega l’amministratore delegato e titolare Luca Borella – il dato Cad, ovvero le matematiche in base alle quali l’ufficio tecnico progetta e sviluppa i singoli pezzi, oltre alle attrezzature necessarie per la loro costruzione. E mi riferisco ad attrezzature per lamierati prototipali in acciaio piuttosto che in alluminio».
CO.ST.AT. progetta quindi lo stampo, lo realizza per poi processare al proprio interno il pezzo fisico che può essere un piccolo particolare come una staffa, piuttosto che parti mobili assemblati di grandi dimensioni, pianali, cofani e così via. A garantire qualità, efficienza e prestazioni nelle fasi di lavorazione, partecipano anche frese e mandrineria MMC Hitachi Tool, da tempo ormai parte integrante del processo industriale di CO.ST.AT.
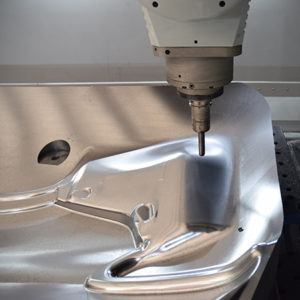
Dal battilastra alle produzioni di serie
Grazie alla propria struttura, CO.ST.AT. è in grado non solo di realizzare prototipi, ma anche piccole produzioni di serie (che rappresentano circa il 10-15% del fatturato), ovvero globalmente fino a 15-20mila vetture all’anno. «Per alcuni clienti – osserva Borella – non è raro realizzare anche esemplari di auto uniche, altamente personalizzate. In questo caso affianchiamo la tecnologia all’abilità artigianale di alcuni nostri addetti. Veri e propri battilastra, capaci di realizzare da un foglio di lamiera i diversi particolari componenti la vettura».
Tradizione e innovazione in sinergia, con una dotazione d’impianti di lavorazione che comprende anche macchine taglio laser (a 2 e 5 assi), robot di saldatura e roto goffratura, numerose presse (fino a 2.500 t) e presso-piegatrici, saldatrici e centri di fresatura. Ed è proprio su questi ultimi centri di lavoro che trovano larga applicazione le frese fornite da MMC Hitachi Tool.
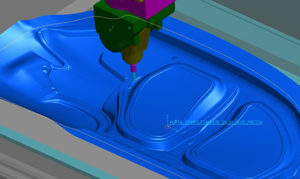
«Il rapporto di collaborazione coi tecnici MMC Hitachi Tool – aggiunge Borella – si è basato sin da subito su un chiaro confronto tecnico su tempi e metodi operativi necessari per raggiungere determinati risultati, in termini qualitativi e prestazionali». Un supporto e un affiancamento continuo, quello offerto dai tecnici MMC Hitachi Tool, coordinati dal responsabile di zona Marco Baldassa, che ha consentito la messa a punto di nuove strategie e di parametri di taglio che hanno permesso all’azienda torinese di compiere passi importanti in termini di competitività.
«Una condivisione costruttiva – prosegue lo stesso Borella – che esula dalla mera fornitura a catalogo, che si è concretizzata nella volontà di uniformare utensili e mandrini su tutti i centri di fresatura attuali e futuri, come quelli a montante mobile che entro l’anno verranno installati presso il nostro stabilimento».
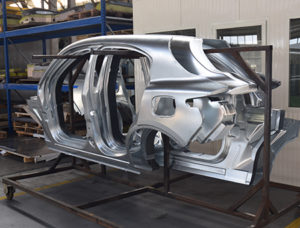
AT. collabora con le più importanti case automobilistiche italiane ed europee.
Sgrossatura, seminfinitura e finitura
Spicca tra le frese impiegate da CO.ST.AT. per la costruzione stampi quella denominata AHR Mini, versatile nella strategia di programmazione, indicata per sgrossatura e con possibile elevato z-step.
«In precedenza – rileva Borella – per la fase di sgrossatura veniva impiegato un classico inserto torico tondo con buone prestazioni, buoni parametri e qualità di processo, ma con alcuni limiti in termini di versatilità per esempio su lavorazioni in pareti verticali o abbastanza diritte. La nuova fresa AHR Mini assicura invece grande flessibilità consentendo di abbattere notevolmente i tempi di lavorazione in queste tipologie di stampo. È possibile dividere le varie fasi modulando il processo in base alle specifiche geometrie riscuotendo benefici significativi sotto tutti i punti di vista».
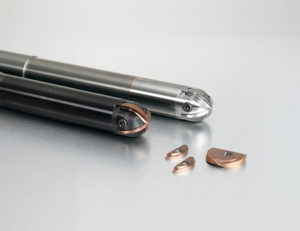
Progettata per ottenere un elevato volume truciolo sia su macchine performanti di ultima generazione, sia su macchine più obsolete soprattutto in relazione a macchine ISO50, BT50, HSK100, la fresa citata permette lavorazioni in 3D garantendo la massima versatilità. Le frese ABP4F sono invece impiegate in CO.ST.AT. per svolgere lavorazioni di semifinitura e finitura degli stampi. Stiamo parlando di un’esecuzione in grado di sopportare elevati avanzamenti grazie alla nuova tecnologia a 4 taglienti che garantisce una velocità di avanzamento doppia rispetto a una normale fresa sferica a due taglienti.
Ultima nata della gamma a inserto della multinazionale nipponica, l’ABPF4 è una fresa unica nel suo genere. Per come progettata e realizzata è infatti in grado di coniugare la precisione tipica del mono-inserto, con la velocità di esecuzione dell’alto avanzamento. Oltre a un mono-inserto centrale monta infatti due inserti laterali che permettono di raddoppiare l’avanzamento, ciò nonostante la precisione dimensionale (±0,01 mm) e geometrica siano uniche nel loro genere. La precisione del riposizionamento degli inserti la rende ottimale per applicazioni di semi-finitura e finitura. I gradi di inserti disponibili e i relativi rivestimenti (Ath e PN) ne garantiscono l’applicabilità su una vasta gamma di acciai e ghise (fino a durezze di 62 Hrc) tipiche del settore stampi a deformazione e plastica di grandi dimensioni.
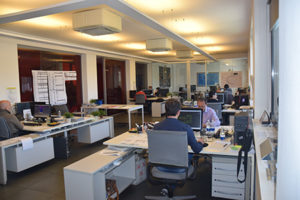
Uniformare per ottimizzare
Oltre alle frese AHR Mini in sgrossatura e ABP4F in semifinitura e finitura, in CO.ST.AT. trovano impiego anche le frese di ripresa per alcune seminifiture serie BCF, oltre alla relativa mandrineria. A sovraintendere questo largo uso, la precisa volontà di uniformare gli utensili, creare di pari passo uno storico per ottimizzare i processi e abbattere tempi ciclo, oltre che poter effettuare lavorazioni senza presidio.
«Oggi – continua Borella – frese e mandrini MMC Hitachi Tool sono presenti su tutti gli 8 centri di fresatura operativi nella nostra unità produttiva. L’importante attività di supporto e consulenza ci ha permesso di costruire uno storico importante ai fini della gestione di tempi e metodi di lavorazione. Riteniamo senza dubbio di aver trovato un partner qualificato e affidabile, capace di affiancarci in un percorso di ottimizzazione di processo continua, al fine di elevare ulteriormente il nostro livello di competitività per vincere nuove sfide di mercato. La stessa modalità da noi perseguita coi nostri clienti».
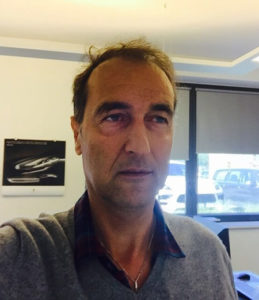
Piobesi Torinese (TO).
L’azienda in pillole
Nata nel 1998, CO.ST.AT. di Piobesi Torinese (TO) è una family company specializzata nella prototipia in ambito automotive, servendo le più importanti case automobilistiche italiane ed europee. «Collaboriamo – precisa l’amministratore delegato e titolare Luca Borella – con tutti i più noti marchi automobilistici, dal gruppo Audi-Volkswagen, a Bmw, a Daimler, come anche più specificatamente in Italia con il gruppo Fca, Ferrari. Lamborghini e Ital Design». Un rapporto di collaborazione non solo esecutivo, di pura fornitura, bensì in co-design finalizzato all’ottenimento del miglior risultato operativo. «Un supporto di qualità – prosegue Borella – col quale il nostro ufficio tecnico non solo accoglie le specifiche esigenze per trasformarle in soluzioni, ma fornisce suggerimenti e miglioramenti di progetto, laddove strategici oltre che necessari per la buona riuscita». Ufficio tecnico composto da una quindicina di addetti, ai quali si affiancano oltre 70 persone per uno staff completo che ad oggi supera le 90 unità, per un fatturato che lo scorso anno ha superato i 14 milioni di euro. «Con una previsione per il 2017 – aggiunge Borella – di superare i 16milioni di euro». Una crescita che coinvolge l’impiego di nuove maestranze e l’integrazione del già vasto parco macchine di nuovi impianti previsti entro quest’anno. «Mi riferisco a due frese a montante mobile di grandi dimensioni – rileva Borella – che ci permetteranno anche di ampliare i nostri orizzonti operativi a nuovi settori, quali l’energetico,trasporti e l’aeronautico». Una nuova divisione di lavorazione meccanica che rafforzerà ulteriormente i servizi che CO.ST.AT. è in grado di offrire al mercato, e che le consentirà di consolidare ulteriormente la propria posizione in ambito nazionale e internazionale.
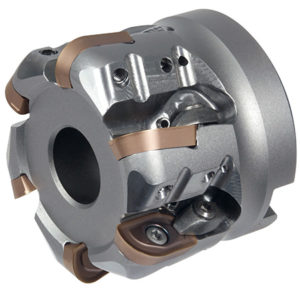
Mini fresa, maxi prestazioni
La serie di frese AHR Mini è stata specificatamente creata e realizzata da MMC Hitachi Tool col preciso obiettivo di ridurre i tempi di sgrossatura su macchine non dotate di alte prestazioni in termini di dinamica. Il volume di truciolo, quindi, viene raggiunto grazie a un rapporto tra avanzamento e profondità di passata calibrato maggiormente su quest’ultima. La geometria dell’inserto permette infatti delle passate assiali fino a 15 mm rendendola ottimale per esempio su sgrossature di superfici con grezzo non uniforme. Sfruttando mandrini dotati di particolare potenza (che in genere equipaggiano macchine con poca dinamica) questa fresa raggiunge prestazioni molto elevate in termini di efficienza se applicata su sgrossature a terrazzamento tipiche nel caso di stampi a deformazione di grandi dimensioni. La gamma di gradi disponibili la rende particolarmente indicata anche in settori quali energia e oil & gas dove, spesso, i macchinari utilizzati hanno a disposizione molta potenza ma scarsa dinamicità. La gamma molto ampia dei corpi fresa (da D32 a D125) la rende potenzialmente molto competitiva in svariate applicazioni.
Al fianco del cliente per vincere nuove sfide
MMC Hitachi Tool, uno dei più innovativi produttori di utensili per i settori della costruzione stampi e lavorazioni meccaniche generali, offre un ampio e diversificato programma di frese da un diametro minimo di 30 µm (0,03mm) le quali, grazie alle loro perfette geometrie di taglio, consentono di raggiungere la migliore performance nei materiali di fabbricazione. In questo segmento di mercato la multinazionale nipponica è così riuscita nel tempo a determinare gli standard, sia per l’ampiezza e la profondità del suo assortimento, sia per la capacità di fornitura. Presente in Italia sin dal 2004 con una propria filiale diretta a Iseo (BS) dove operano attualmente una ventina di persone (di cui una quindicina sono figure tecnico-commerciali), mette a disposizione un’ampia scelta di soluzioni di prodotto, abbinata a un’individuale consulenza applicativa. Approccio che ne fanno un affidabile partner sul quale contare per vincere nuove sfide in tutti i campi dalla costruzione stampi fino alle lavorazioni di meccanica generale; come nel caso di CO.ST.AT., con la quale si è stabilito un solido e costatante rapporto di collaborazione.