
Da tre generazioni la Modelleria Brambilla realizza prodotti di alta qualità nel settore della “foundry engineering”. Nata nel 1951 a Carpi dalla ventennale esperienza di Eugenio Brambilla, con il passare degli anni, da piccola attività artigianale locale, diventa una realtà che oggi produce ed esporta in tutto il mondo per i più importanti marchi automobilistici.
«Progettiamo e realizziamo – conferma Edoardo Brambilla, responsabile operativo direzione tecnica, nonché rappresentante della terza generazione in azienda – modelli, casse d’anima, conchiglie e altre attrezzature per la costruzione di componenti in alluminio o ghisa. Soprattutto teste cilindri, basamenti motore, oltre a scatole cambio, collettori e altri getti complessi destinati prevalentemente al settore automotive».
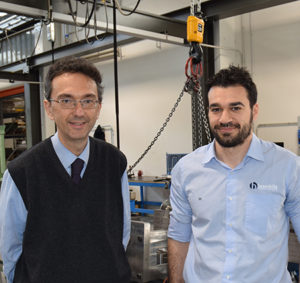
Un’attività che, seppur mantenendo l’estro, la capacità di gestire gli imprevisti e l’adattabilità alle situazioni più complesse, ha nel tempo assunto un’impronta sempre più manageriale, concretizzatasi nel 2014 anche con la quotazione dell’azienda alla borsa di Milano. «Chiave in questo percorso di crescita – aggiunge Brambilla – è stato anche l’ingresso dell’ing. Gabriele Bonfiglioli nel ruolo di general manager e amministratore delegato».
Avvenuto nel 2011, questo nuovo ingresso in organigramma ha determinato una profonda riorganizzazione interna che ha portato alla creazione di figure di riferimento in termini di responsabilità e obiettivi da raggiungere. Una trasformazione che ha permesso all’azienda di raddoppiare in pochi anni il proprio fatturato, passato da 8 milioni di euro del 2011, agli oltre 16 milioni di consolidato del 2016. «Questa riorganizzazione – aggiunge Brambilla – ha riguardato anche la parte più operativa e di processo che accompagna quotidianamente la nostra attività, dalla progettazione alla simulazione, dalla realizzazione di campionature alla produzione, fino al collaudo finale».
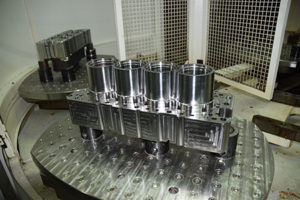
Ottimizzazione della produttività a tutto tondo, attraverso l’adozione di software più performanti, sviluppo di nuove e più mirate strategie di lavorazione, impiego ottimale di utensili e attrezzature. «Da questo punto di vista – sottolinea Brambilla – MMC Hitachi Tool ha rappresentato e rappresenta per noi un partner tecnologico fondamentale. Non un semplice fornitore di prodotti, comunque di elevata qualità, bensì un partner capace di offrire un supporto e una consulenza orientata all’ottenimento di risultati operativi tali da elevare il nostro livello di competitività».
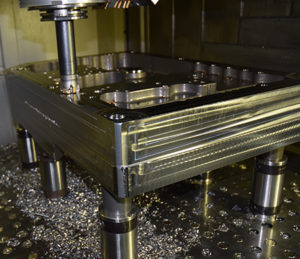
Semplificare i processi per ottenere maggiore efficienza
Partner di lunga data della Modelleria Brambilla, MMC Hitatchi Tool, già nel 2008 iniziò un rapporto di collaborazione in grado di fornire un servizio di consulenza e di supporto ben strutturato. «Partnership che già in quegli anni – rileva lo stesso Brambilla – ci permise di perfezionare tecnologie di utilizzo degli utensili, cercando di ottimizzare prestazioni e durata degli stessi, oltre a massimizzare le potenzialità delle macchine. Sempre nell’ottica di assicurare la massima qualità della lavorazione».
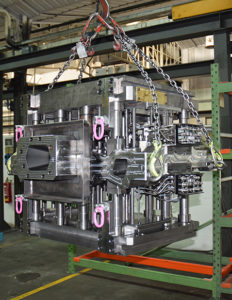
Mattia Bautta, responsabile di zona di MMC Hitachi Tool, ha coordinato tutte le attività necessarie per la messa a punto delle strategie e dei parametri di taglio necessari per l’ottenimento dei risultati attesi. Uno sviluppo integrato proseguito nel tempo e che si è fatto ancora più sinergico negli ultimi anni. «Un sodalizio necessario – aggiunge Brambilla – a fronte di una sempre più elevata complessità dei componenti che ha riguardato sia gli aspetti legati alla programmazione, sia all’affidabilità degli strumenti di realizzazione dei percorsi utensili in macchina».
In altre parole, prevedere per tempo eventuali criticità di produzione, prima di arrivare all’esecuzione vera e propria in officina. Miglioramenti che hanno significato negli anni anche una progressiva standardizzazione della fase di programmazione che oggi non avviene più a bordo macchina, ma gestita e generata dall’ufficio tecnico Cam.
«Un vero e proprio team – prosegue Brambilla – chiamato a gestire macchine tutte a 5 assi, multi-pallet con cicli di lavoro ottimizzati sotto ogni aspetto, incluso il cambio utensili e la loro più elevata standardizzazione. Fase, questa, che di per sé potrebbe sembrare non così significativa, ma che in realtà, nell’arco delle 24 ore, ha permesso un’interessante riduzione quotidiana dei tempi di produzione, e maggiore sfruttamento degli impianti».
La standardizzazione degli utensili ha portato ad un ampliamento di gamma fornita, ma studiata e strutturata in base alle reali necessità operative. Il beneficio è stato quello di semplificare il processo, dalla fase di progettazione alla programmazione Cam, dall’attrezzaggio macchina all’approvvigionamento delle frese.
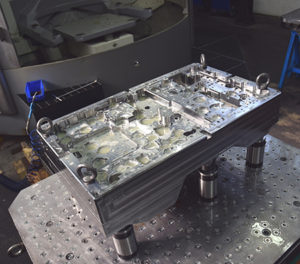
Meno costi, più produttività
Ora è necessario crescere ulteriormente in termini di produttività, riducendo ancor di più i tempi ciclo, mantenendo comunque la più elevata affidabilità di processo. «Una sfida ambiziosa – aggiunge Brambilla – con la quale dobbiamo ottimizzare i tempi ciclo, salvaguardando in ogni caso l’efficienza e la durata dell’utensile, ma sfruttando ancora meglio le tecnologie di cui disponiamo in termini di avanzamenti e così via. E, soprattutto, utilizzando la sinergia macchina-utensili-strategie di lavorazione, in modo ancora più strutturato». Chiaro e concreto esempio di questo approccio, è quanto fatto in officina qualche mese fa. Un test che ha coinvolto solo i parametri di taglio in una fase di sgrossatura dopo-tempra, effettuata con frese serie PICO, impiegate per operazioni di semifinitura di tasselli di medie dimensioni.
«Per questa fase – prosegue Brambilla – abbiamo sempre utilizzato parametri abbastanza standard, per avere un’ottima durata utensile, con avanzamenti nell’ordine dei 7-8.000 mmi/min. Oggi, sfruttando al meglio le nuove dinamiche macchina, è stato possibile raddoppiare questi valori di avanzamento, risparmiando il doppio del tempo e aumentando la vita utensile. Una più accurata analisi del ritorno dell’investimento ha confermato come questa scelta sia orientata all’ottimizzazione cercata».
In questo senso emerge appieno il concetto di produttività che MMC-Hitachi Tool racchiude nella filosofia “Production50”. Applicabile in particolare per il settore stampi e matrici, essa offre la possibilità di tagliare i costi di produzione complessivi sino al 50%. Per il citato settore si può infatti stimare in un valore del 5-7% il costo degli utensili di taglio, attribuire al 25% una quota di costi generali, mentre la restante e più preponderante parte (70%) rappresenta il reale costo di processo. Ed è proprio in quest’ultima che si concentrano i potenziali margini di miglioramento perseguiti.
Il valore aggiunto della migliore pre-finitura
Altrettanto interessanti sono i miglioramenti ottenuti in officina ricalibrando l’utilizzo nella fase di ripresa dei raggi con le frese serie ETM. Analizzate le dinamiche della macchina, riproporzionati i parametri in ottica di ottimizzazione di processo, i tecnici MMC hanno individuato, insieme ai tecnici della Modelleria Brambilla, le condizioni per ottenere, addirittura con utensili di 6 mm di diametro, oltre 60-70 ore di contatto. «Ciò significa – osserva Brambilla – riuscire a portare a termine la lavorazione dello stampo, massimizzando l’uso macchina. Sia essa dotata o meno di multi-pallett».
Un processo di ottimizzazione e standardizzazione in continuo divenire, che porterà in futuro l’integrazione di utensili sempre più mirati a ottenere benefici operativi per incrementare la produttività e l’efficienza globale. Tra i nuovi progetti si preannuncia l’inserimento di nuove frese tra cui anche la nuova esecuzione a barile GF1 di MMC-Hitachi Tool che servirà a dare ancor più peso al concetto di “pre-finish”, ovvero una migliore prefinitura per ottenere una finitura nel minor tempo possibile.
Crescita continua, insieme ai propri partner
Le strategie di crescita pianificate dal management della Modelleria Brambilla sono chiare e ben definite. Ma non si limitano a un miglioramento interno. L’azienda, infatti, si avvale di partner esterni ai quali affida alcune lavorazioni. «Tra queste anche la realizzazione del portastampo – specifica Brambilla – le cosiddette strutture, sostegno delle cavità dello stampo». Un indotto che incide circa il 15% del fatturato totale, sul quale l’azienda ha intrapreso delle azioni di affiancamento e di supporto con l’obiettivo di portare criteri e logiche operative e di qualità già adottate al proprio interno. Altrettanto sfidante è l’attività di costante incremento di automazione delle varie fasi del ciclo produttivo, secondo i canoni dell’Industria 4.0.
«Abbiamo preso precisi impegni coi nostri azionisti – conclude Edoardo Brambilla – che si possono sintetizzare nella volontà di proseguire il nostro trend di crescita attraverso attività che coinvolgono ogni aspetto dell’iter produttivo. Dalla progettazione alla simulazione, dalla produzione sino al collaudo finale. La ricerca della migliore sinergia tra macchina, utensili e strategie di lavorazione, rappresenta uno step importante che contribuirà, senza dubbio, a elevare ulteriormente la nostra competitività sul mercato a livello mondiale».
L’azienda in pillole
Con sede a Correggio (RE), 65 dipendenti e una forte vocazione internazionale (80% del fatturato realizzato all’estero), Modelleria Brambilla rappresenta una delle realtà più importanti nel settore della componentistica di precisione per l’industria automobilistica. Fondata nel 1951 da Eugenio Brambilla e sviluppata a partire dagli anni 60 dai figli Aldo e Giancarlo, la società realizza e commercializza attrezzature per la produzione di teste cilindri, basamenti motore, scatole cambio, collettori e altri getti complessi per il settore automotive. Le importanti risorse dedicate alla ricerca e all’innovazione tecnologica, unitamente allo studio del design e alla progettazione realizzata con il cliente, hanno consentito all’azienda di diventare partner di riferimento e fornitore strategico, tramite le fonderie, delle più importanti case automobilistiche a livello mondiale (BMW, Ferrari, FCA, Volkswagen, Ford, GM, Chrysler). Presente sul mercato indiano tramite Italian Foundry Engineering, ufficio tecnico di progettazione con sede a Goa, e Brambilla India Private Ltd (New Delhi), JV paritetica con Continental Engines Ltd (Baxi Group), è anche quotata dal 2014 sul mercato AIM Italia (organizzato e gestito da Borsa Italiana).
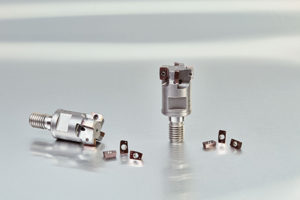
Fresa a inserti con profilo a barile
GF1 è la particolare fresa a inserti con profilo a barile che MMC Hitachi Tool ha recentemente introdotto sul mercato. Si tratta di un’esecuzione progettata e sviluppata per soddisfare esigenze di produttività sempre più elevate, qualità di processo, ottimizzando costi ed efficienza. Presto integrata anche sui centri di lavoro della Modelleria Brambilla, questa fresa non monta inserti stampati, bensì composti da un’ultra-micrograna in metallo duro rivestito. Due i rivestimenti disponibili: uno è il grado Panacea, caratterizzato da un coefficiente d’attrito molto basso per i materiali più tenaci o comunque sticking material; il secondo è invece il rivestimento TH, con durezza Vickers superficiale e una temperatura di ossidazione più elevate, indicato quindi per i materiali temprati. La fresa, oggi fornibile in 3 differenti diametri (16, 20 e 25 mm, con raggio barile di R20 e R30), si distingue anche per essere disponibile con inserti a 2 diverse geometrie: “basic type”, barile simmetrico, prevalentemente adatto per tutte le lavorazioni a 3-5 assi; “offset type” (con inclinazione a 12° e 19°), maggiormente indicato per lavorazioni a 5 assi pure. Le principali applicazioni dove la fresa GF1 può esprimere al meglio le proprie potenzialità riguardano le semifiniture e le finiture ad alta efficienza di pareti, tasche e guide di stampi dove, la geometria periferica a barile, assicura un risparmio di tempo dell’ordine del 70%.

Frese in metallo duro integrale
La famiglia di frese ETM e ETMP di MMC-Hitachi Tool nasce come soluzione di riferimento nel mondo del metallo duro ad altissime prestazioni, come scelta prioritaria in fase di sgrossatura dal pieno, ripresa e fresatura diretta. Mantenere un elevato volume di truciolo è infatti fondamentale nelle fasi di ripresa e nervatura sia su materiali bonificati che temprati fino a 60 HRC, rappresentando mediamente oltre il 50% delle operazioni di fresatura di uno stampo. Utilizzate in alcune fasi di processo anche dalla Modelleria Brambilla, queste frese vantano una particolare affilatura ovale antivibrante e sono disponibili in diametri da 1 a 12 mm, diritte o sformate a 0,9° oppure 1°.