Pochi elementi in natura possono vantare una storia originale come l’alluminio. Si tratta del metallo più diffuso sul nostro pianeta e del terzo elemento più abbondante dopo l’ossigeno e il silicio. Malgrado ciò, l’alluminio è rimasto di fatto sconosciuto fino a tempi molto recenti e, una volta “scoperto”, per lungo tempo è stato considerato addirittura più prezioso dell’oro. Oggi al contrario rappresenta una delle materie prime più utilizzate in assoluto, con uno spettro di applicazioni davvero smisurato.
Dall’allume all’alluminio: storia e impiego di un materiale utilizzato da sempre ma conosciuto da poco
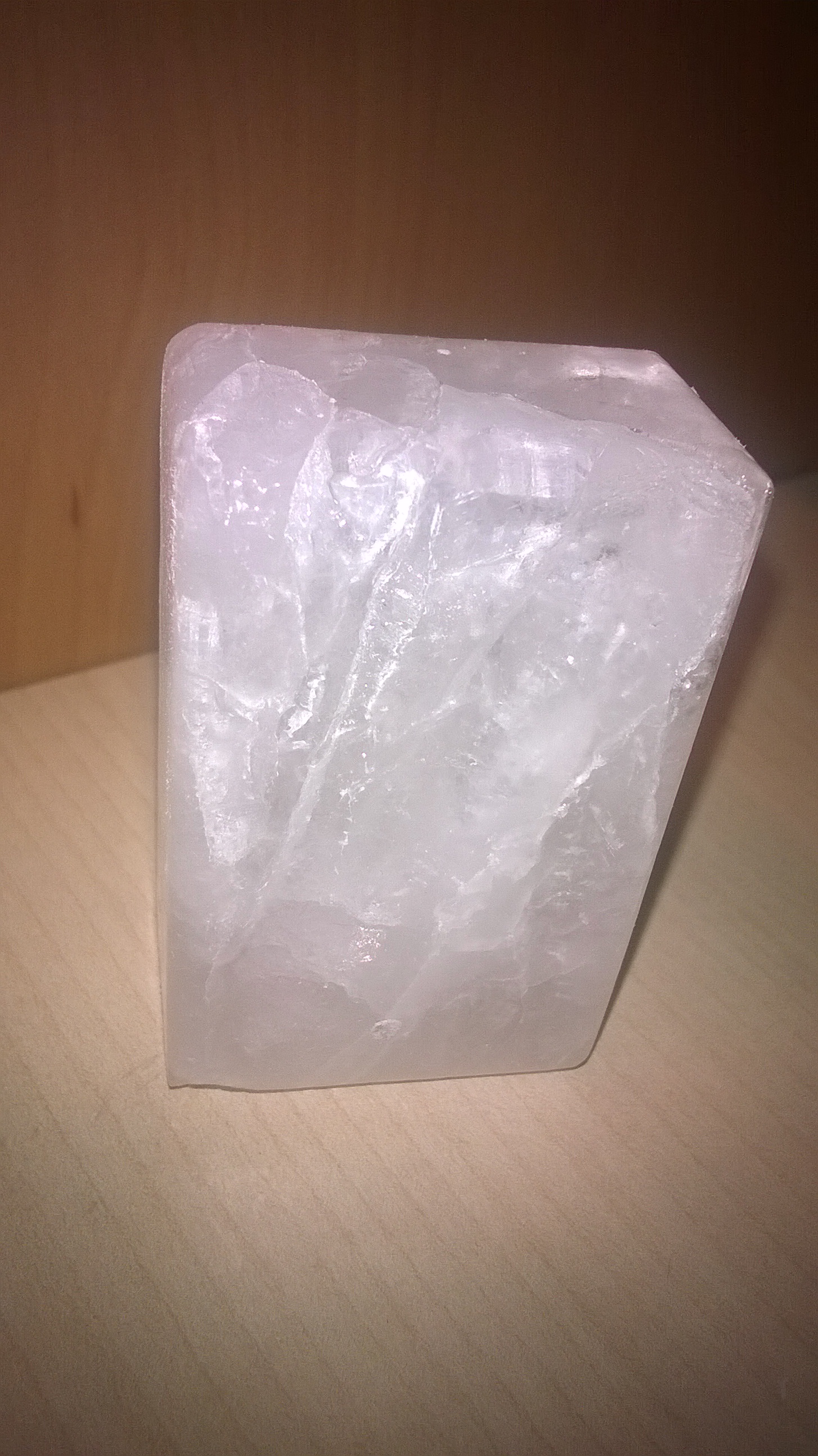
Benché l’elemento puro sia rimasto ignoto all’uomo fino all’800, gli allumi al contrario (sali di doppia formula in cui normalmente è presente l’alluminio) sono noti fin dai tempi antichi. Venivano comunemente utilizzati sia come mordente per fissare i colori dei tessuti, che come sale impiegato nell’imbalsamazione di uomini e animali, sia infine nella concia delle pelli e per rendere ignifugo il legname. Nella sua Naturalis historia Plinio il Vecchio descrive numerose sostanze chiamate collettivamente “aluminis”, di aspetto anche molto differente fra loro e provenienti da diverse aree del bacino del Mediterraneo.
Le contese medievali
In pieno Medioevo, l’allume arrivava principalmente dall’Asia Minore, ricca di giacimenti di alunite, e molte compagnie, principalmente veneziane e genovesi, accumularono fortune ingenti grazie al fiorente commercio di questa materia prima. La conquista dell’Asia Minore ad opera dei Turchi di Maometto II a metà del ‘400, tuttavia, creò inevitabilmente grossi problemi alle industrie europee. Si deve a un italiano, Giovanni da Castro, la scoperta nei monti della Tolfa, a nord ovest di Roma, di formazioni minerali in tutto e per tutto analoghe a quelle da cui veniva estratto l’allume turco. L’occasione per fare concorrenza agli infedeli era ghiotta, e il pontefice dell’epoca, Pio II, intuì immediatamente l’importanza strategica che ne sarebbe derivata, affidando a Giovanni da Castro la produzione dell’allume, su cui gravava ovviamente un’imposta papale. L’allume “cristiano” divenne talmente importante che Paolo II, succeduto a Pio II, impose a tutti gli europei di usare il solo allume papale, pena la scomunica. Poco dopo, grazie a un accordo con Ferdinando II di Napoli (nel cui Regno veniva prodotto allume nella solfatara di Pozzuoli), lo stato Pontificio si garantiva sostanzialmente il monopolio del materiale in Europa. Si trattava di un potere economico così importante da tutelarsi che l’utilizzo di allume non papale fu escluso dalla lista dei peccati condonabili a pagamento dall’indulgenza del 1517 di Leone X. Proprio il documento che porterà nell’ottobre di quell’anno un indignato Martin Lutero a dare il via alla Riforma protestante con le famose 95 tesi sulle indulgenze appese alla porta della chiesa di Wittenberg.
Verso l’industrializzazione
Avvicinandosi ai nostri giorni, bisognerà attendere il 1807 perché il chimico inglese Sir Humphrey Davy ipotizzasse per primo che l’alum fosse il sale di un metallo all’epoca ancora sconosciuto che chiamò, proprio per la sua presenza nell’allume, “aluminum”, successivamente modificato in “aluminium” (peraltro, proprio da questa doppia dicitura deriva il nome anglosassone “aluminum” dato al metallo).
Solo 18 anni più tardi, nel 1825, il fisico danese Hans Cristian Ørsted ottenne le prime gocce di alluminio puro riscaldando un amalgama di alluminio e potassio. Un suo discepolo tedesco, Freidirich Wohler, proseguì le ricerche scoprendo molte proprietà del nuovo metallo, a cominciare dalla sua notevole leggerezza, caratteristica che attirò l’attenzione del mondo scientifico e industriale e portò ad un cospicuo aumento dei fondi destinati alla ricerca.
A metà ‘800, il chimico francese Henri Sainte-Claire Deville metteva a punto un processo capace di produrre limitate quantità di alluminio per scopi industriali. La complessità del metodo tuttavia, rendeva il nuovo metallo addirittura più caro dell’oro. Solo verso la fine del secolo, e precisamente nel 1886, l’americano Charles Martin Hall e il francese Paul Heroult scopriranno contemporaneamente, ma in modo indipendente, il processo di fusione elettrolitico in grado di ottenere alluminio metallico dall’allumina. Quello di Hall-Herout è a tutt’oggi il sistema utilizzato per produrre l’alluminio, pur se affinato da ricerche successive.
La più importante a livello industriale è quella dell’austriaco Karl Bayer che nel 1888 brevettò la tecnica in grado di estrarre l’ossido di alluminio dalla bauxite, la fonte ad oggi più importante di alluminio per tutte le moderne produzioni industriali. Benché questo minerale derivi il proprio nome dalla località francese di Les Baux, sui Pirenei, dove fu identificata per la prima volta, la maggior parte dei giacimenti attualmente in uso è localizzata in aree tropicali e subtropicali. L’estrazione è relativamente semplice e i giacimenti sono quasi sempre a cielo aperto.
L’alluminio ai giorni nostri
Oggi sono estratti annualmente più di 100 milioni di tonnellate di bauxite, principalmente in America centrale e Sud America, Australia, Africa (in particolare in Guinea), Asia, Russia e Kazakhistan. In Europa il paese con la produzione maggiore è la Grecia. Quattro tonnellate di bauxite consentono la produzione di due tonnellate di allumina da cui deriva una tonnellata di alluminio primario con l’utilizzo di 14.000 kW/h di energia.
Dal momento che il processo di produzione è sempre stato piuttosto dispendioso in termini energetici, nel corso degli anni la ricerca e il progresso tecnologico hanno cercato costantemente di elaborare sistemi in grado di migliorare le performance produttive: in questo modo nell’arco di cento anni il consumo di energia e le emissioni derivanti per la produzione sono state ridotte di circa il 70%.
Impiego attuale
Secondo stime dell’IAI (l’International Aluminium Institute), attualmente la produzione globale di alluminio ha raggiunto quota 64.34 milioni di tonnellate di cui oltre la metà proviene dalla Cina (36.488 milioni di tonnellate/anno, con una crescita dell’1,6% rispetto all’anno precedente), seguita dai paesi del GCC (Gulf Cooperation Council), con 5.334 mta, dall’Asia extra Cina (4415 mta), dai paesi del centro e est Europa (4.049 mta), Nord America (3.774 mta) e Europa (3.732 mta).
L’industria infatti fa un uso massiccio di alluminio, che viene utilizzato nei settori più disparati. Nei trasporti, è utilizzato nella costruzione di automobili, treni, mezzi pubblici, natanti, aeroplani, biciclette. La navicella Shuttle, per esempio, è costituita per oltre il 90% da alluminio. Diffusissimo anche nell’industria meccanica ed elettrica, oltre che nel settore della telefonia, dell’elettronica e dell’illuminazione, l’alluminio è oramai parte integrante anche del nostro quotidiano.
Lo troviamo diffusamente in cucina, nei tappi dell’acqua minerale come in quelli dell’olio, per avvolgere dadi, cioccolato e caffè, oppure in rotoli per la conservazione dei cibi, nei blister dei medicinali, nei tappi che sigillano yogurt e succhi di frutta, nei tubetti per il dentifricio e per la cosmetica, nelle bombolette spray. Praticamente ubiquitario, insieme alle plastiche condivide il primato tra i materiali a più largo spettro di applicazione.
Caratteristiche e potenzialità dell’alluminio
Sono molteplici le caratteristiche che rendono l’alluminio particolarmente appetito dall’industria. La sua grande resistenza alla corrosione, dovuta alla sua immediata ossidazione a contatto con l’aria che lo protegge sia dall’acqua che dall’aggressione di diversi agenti chimici, lo rende molto utilizzato sia nei trasporti che nell’edilizia. La sua alta conducibilità elettrica poi fa si che sia il materiale più gettonato per i conduttori ad alto voltaggio. Ma la prerogativa che ne sta determinando maggiormente il successo negli ultimi anni è la leggerezza. A parità di volume, l’alluminio pesa infatti circa un terzo di rame e acciaio. Proprio per queste ragioni per esempio nei moderni aerei la percentuale di alluminio arriva circa all’80% (in particolare in quelli da trasporto). Il mondo dell’automotive da tempo utilizza questo materiale per diverse parti del veicolo (o per l’intera carrozzeria). Rispetto alla metà del secolo scorso, quando in un’auto erano presenti in media 40 kg di alluminio, oggi questo valore è quasi raddoppiato (70 kg).
Ma è senza dubbio l’aumento deciso nella produzione dei veicoli elettrici (cresciuti del 64% ad inizio 2019 rispetto all’anno precedente) a favorire l’impiego di alluminio nel prossimo futuro, e più in generale a rivoluzionare il mercato mondiale dei metalli. Se i primi a beneficiare del cambio di rotta nel settore automobilistico sono infatti i materiali quelli utilizzati per la realizzazione delle batterie dei veicoli (cobalto e litio su tutti), anche l’alluminio è sempre più usato grazie appunto alla sua estrema leggerezza, caratteristica che consente alle automobili di viaggiare utilizzando una minore quantità di energia (la riduzione del consumo ad oggi è stimata intorno all’8%).
Produzione e trasformazione dell’alluminio
Il metallo, allo stato liquido, viene ricavato dall’allumina attraverso il processo elettrolitico Hall-Hèroult che avviene ad una temperatura di circa 950 °C in un bagno fluorinato attraversato da corrente elettrica ad alta intensità. Da qui, subisce processi di trasformazione ulteriori che si differenziano a seconda dell’uso cui verrà destinato. Tra di essi, la colata continua e semicontinua, da cui si ottengono vergelle e, tramite la trafilatura, fili, lastre, billette. Per ridurre invece lo spessore si utilizza la laminazione, che può avvenire sia a caldo che a freddo, e che consente di produrre fogli di alluminio che possono arrivare a soli 4 μ di spessore. Il classico foglio di alluminio è assai diffuso come imballaggio grazie all’impermeabilità ad aria, luce e umidità, caratteristiche che lo rendono ideale per la conservazione delle merci deperibili.
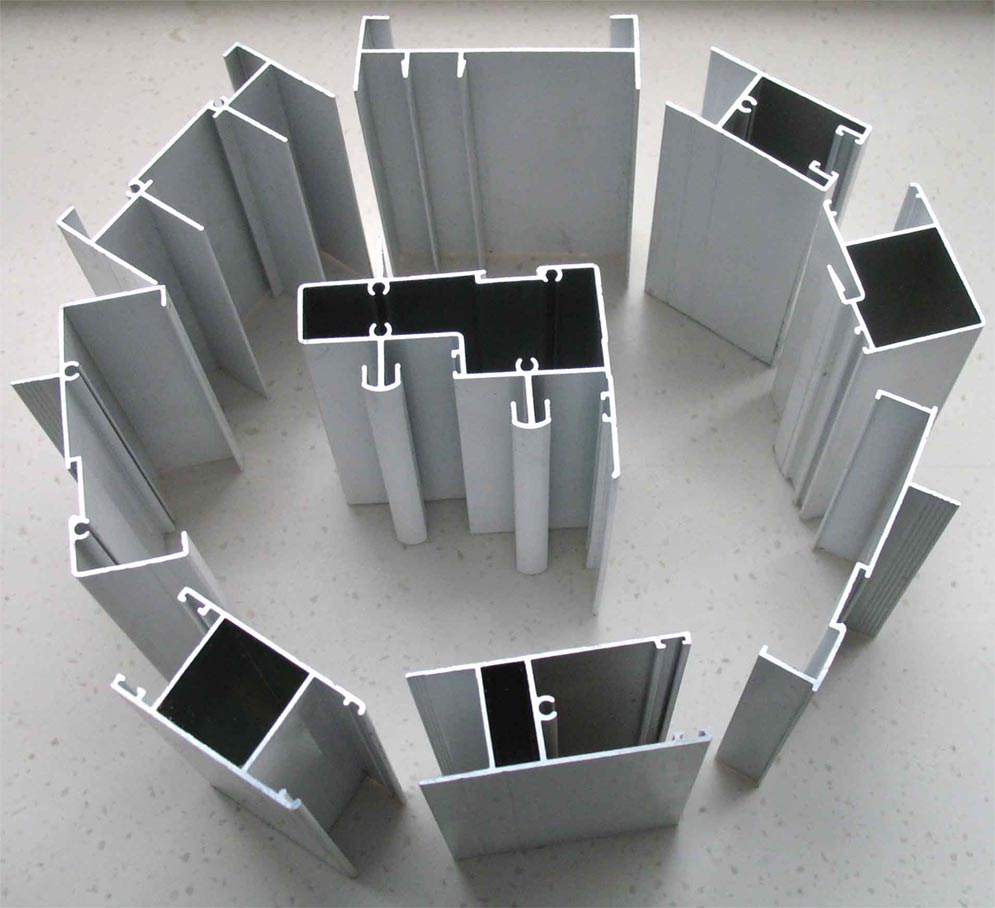
Attraverso l’estrusione invece una billetta di alluminio, utilizzando una matrice di acciaio, viene trasformata in un profilato a sezione costante. È tipicamente un processo utilizzato per produrre porte, finestre, tubi, ma anche carrozzerie, parti di aerei e navi. La forgiatura invece parte da una pastiglia di metallo caldo che viene compressa in uno stampo ed è utilizzata per realizzare pezzi fino ai 100 kg di peso. La combinazione di queste due lavorazioni è denominata estrusione per impatto: vengono realizzati così ad esempio i tubetti per dentifrici, creme da barba, prodotti cosmetici.
Nell’industria automobilistica al contrario si utilizza frequentemente la tecnica dei getti di fusione, in cui l’alluminio fuso viene colato in stampi per ottenere pezzi quali pompe, pistoni, collettori e molti altri. Un ultimo procedimento utilizzato industrialmente è quello della trafilatura, con la quale il pezzo di alluminio viene fatto passare attraverso uno stampo che gli conferisce la forma definitiva. Con questo metodo si producono in particolare fili e tubi di piccolo calibro, utilizzati nei campi più disparati.
Riciclo
Oggi l’alluminio impiegato nell’industria si divide in due tipologie: quello primario, derivante dalla lavorazione della bauxite, e quello secondario, proveniente dal recupero e riciclo dei rottami di alluminio. Questa seconda modalità è estremamente interessante in quanto ben il 95% dell’energia utilizzata nella produzione primaria viene conservata nell’alluminio. Ottenere pertanto alluminio a partire da materiali di riciclo consente un dispendio di energia pari a solo il 5% rispetto a quella utilizzata con l’elettrolisi.
Il processo di produzione dell’alluminio riciclato è relativamente semplice. I rottami e gli imballaggi vengono passati al vaglio di un separatore che li divide da eventuali residui di materiali diversi, compresi metalli magnetici (l’alluminio infatti non ha caratteristiche magnetiche).
Le balle così ottenute vengono portate in fonderia dove, dopo un primo trattamento a 500 °C per eliminare ulteriori sostanze estranee, viene fuso a 800 °C. Considerato che la produzione di un kilogrammo di alluminio richiede un dispendio energetico di circa 13 kW/h e che l’analogo proveniente dal riciclo ha un costo energetico di meno di un kilowatt, è facile comprendere l’importanza crescente dell’industria del recupero di questo metallo e il fatto che ad oggi è ancora utilizzato il 75% di tutto l’alluminio da sempre in circolazione nel mondo. Questo grazie anche al fatto che il metallo può essere riutilizzato all’infinito, senza che questo comporti la perdita delle sue caratteristiche originali.
Un settore, quello del recupero dell’alluminio, in cui il nostro paese è un’eccellenza mondiale. L’Italia infatti è, insieme alla Germania, il terzo paese al mondo per quantità di alluminio riciclato, dietro solo a Stati Uniti e Giappone. E se l’Europa detiene il primato per la maggior quantità di alluminio riciclato pro capite, addirittura l’intera produzione nazionale proviene dalla seconda vita del materiale.
Mercato, andamento, prezzi
Nel periodo 2013 – 2016 la richiesta del metallo è cresciuta mediamente del 2,7%, e la tendenza sembra destinata a confermarsi e ad aumentare. Nel 2017 la domanda di alluminio è aumentata addirittura del 14%, in particolare come conseguenza della crescente richiesta proveniente dall’industria automobilistica cinese. Le sanzioni statunitensi della primavera 2018 nei confronti della Rusal (il più grande produttore di alluminio al mondo al di fuori della Cina), motivate secondo Washington dall’interferenza di alcuni oligarchi e società russe nelle elezioni americane, hanno provocato inizialmente una crescita nel prezzo del metallo, che ha raggiunto un picco di 2.133 dollari la tonnellata, ma i mercati in breve tempo hanno assorbito il colpo, tanto che l’annuncio della rimozione delle sanzioni non ha smosso più di tanto le quotazioni. Al London Metal Exchange le oscillazioni sono state davvero contenute, e l’alluminio, che a dicembre 2018 aveva già toccato i minimi degli ultimi 16 mesi, si sono attestate intorno ai 1920 USD.
In effetti, sui mercati continua a prevalere una certa prudenza. Vero, le quotazioni si stanno riprendendo dopo una fase di stagnazione, ma anche se il miglioramento dei rapporti USA – Cina alimentano un certo ottimismo, la contrazione dell’economia cinese, che ha influenzato molti altri settori oltre a quello dei metalli, continua a essere motivo di preoccupazione. Secondo stime recenti l’industria cinese prosegue nel suo rallentamento, e i riflessi sulle quotazioni dell’alluminio e di altre materie prime si è fatto subito sentire, in particolare per la frenata del settore automotive.
Per gli analisti, la riduzione delle sanzioni a Rusal prima ricordate dovrebbero incrementare significativamente le disponibilità di alluminio sul mercato, con una conseguente stabilizzazione dei prezzi, ma allo stato attuale il surplus di produzione (anche del metallo derivante dal riciclo), che riguarda anche il prezzo dell’allumina, potrà essere controbilanciato solo da una ripresa complessiva dell’economia mondiale. A beneficiare della situazione è il business dei rottami di alluminio.
Secondo una ricerca del Wall Street Journal, la guerra commerciale USA-Cina ha determinato un boom nel settore, tanto che il 2018 è stato il primo anno in cui l’alluminio riciclato ha rappresentato la prima fonte di approvvigionamento per l’industria americana. Resta da capire come evolverà la situazione nei prossimi mesi ma una cosa è certa: l’alluminio continuerà ad essere uno dei protagonisti indiscussi dell’industria per i prossimi anni.