Tradizionalmente gli elettrodi in grafite vengono lavorati a secco. Oggi si stanno facendo strada anche le lavorazioni ad umido, in grado di dare risultati eccellenti, abbattendo le problematiche legate alla generazione di polveri.
L’elettrodo in grafite, grazie alle performance offerte, è ormai largamente diffuso: buon conduttore elettrico e termico, facilmente lavorabile e costo relativamente contenuto stanno rendendo la grafite un materiale estremamente interessante nei processi EDM. Inoltre, la grafite è presente sul mercato con diversi gradi, quindi, in funzione del tipo di elettrodo da produrre, è possibile scegliere fra i diversi tipi, dalla più grezza, alla più compatta, per gradi di finitura elevati, con conseguenti costi diversi.
Dunque la grafite rappresenta un materiale estremamente interessante per il settore degli stampi, ma la lavorazione all’utensile ha un problema, legato alla struttura del materiale: le polveri! La tradizionale lavorazione a secco prevede l’uso del classico aspiratore che, però, per quanto potente possa essere, risolve il problema solo in parte e obbliga ad avere una macchina dedicata, senza la possibilità di passare eventualmente ad altri materiali.
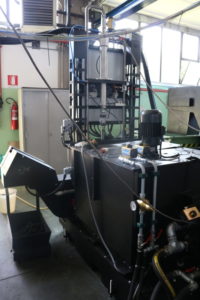
Sala Maurizio Stampi da tempo lavora elettrodi in grafite a secco, accettando la presenza di polveri come una sorta di “effetto collaterale” inevitabile. Recentemente però qualcosa è cambiato, con l’introduzione in produzione dei una nuova macchina, la Mikron VCE 1400, per produrre elettrodi di grandi dimensioni, ma con la possibilità, in caso di necessità, di lavorare anche materiali differenti. Questo ha portato alla valutazione di una soluzione speciale, considerando la lavorazione ad umido e una gestione dei fluidi evoluta, che ha visto coinvolta la friulana RBM, non nuova alla gestione dei reflui che seguono la lavorazione di materiali polverosi.
Lavorazione in campana d’acqua, ovvero a umido
La lavorazione della grafite avviene molto spesso a secco, producendo grossi volumi di polvere estremamente fine che deve essere opportunamente trattata. E’ fondamentale mantenere la macchina pulita in modo da garantirne le funzionalità, evitando il decadimento funzionale e delle performance. Altrettanto fondamentale è la salubrità dell’ambiente, che non può e non deve essere messa a rischio, evitando problemi di salute agli addetti, oltre all’integrità della macchina utensile. La soluzione è in genere rappresentata dai sistemi di aspirazione ma, per quanto possano essere validi, la polvere di grafite è talmente fine che, nel tempo, si infiltra ovunque, andando a sporcare e danneggiare il bene più grande di un’azienda manifatturiera: la macchina utensile. Un differente approccio, che sta dando risposte molto positive, è quello detto “in campana d’acqua“, cioè a umido.
“Lavorando in campana d’acqua, si ha un flusso laminare d’acqua intorno all’area di lavoro – spiega Marco Sala, responsabile della produzione –. In pratica lavoriamo a secco ma la polvere di grafite, proiettata contro la barriera continua di acqua, precipita e quindi viene evacuata col liquido. La pulizia della macchina è importantissima, quindi, per essere sicuri di avere un abbattimento ottimale delle polveri, si provvede ad un lavaggio dell’area di lavoro, lavaggio assicurato da un flusso d’acqua che fuoriesce da apposti ugelli posti sui bordi della macchina“.
La tecnologia in campana d’acqua sfida la capacità filtrante di qualsiasi sistema, mettendolo a dura prova: non è infatti ammissibile che si rimetta in circolo acqua non pulita perché si andrebbe ad intaccare il concetto stesso di velo laminare di liquido, a causa delle disuniformità legate alla presenza di impurezze.
L’esperienza maturata da RBM sui sistemi IFDR standard, applicati per la lavorazione di materiali non convenzionali (ceramiche, grafite, fibra di carbonio, marmo…) ha permesso di individuare e implementare delle modifiche che consentissero di rispondere alla specifica esigenza di Sala Maurizio Stampi e della Mikron VCE 1400, installando la versione Precision dell’IFDR 500, che spinge il grado di filtrazione sotto i 5µm. IFDR 500 Precision integra inoltre un sistema di movimentazione del liquido all’interno dell’insieme macchina utensile-impianto innovativo, andando a catturare effettivamente la morchia con dimensioni estremamente ridotte presente all’interno del fluido da taglio.
“Inizialmente la scelta della lavorazione della grafite ad umido ci convinceva, ma ci lasciava anche il classico scetticismo legato a qualcosa di nuovo, in particolare perché stavamo portando qualcosa, l’elettrodo in grafite, lavorato ad umido nella vasca dell’EDM, con la presenza di dielettrico – prosegue Sala –. Abbiamo coinvolto anche il nostro fornitore di lubrorefrigerante, che ci ha consigliato l’uso di una soluzione idrosalina, simile a ciò che si usa in rettifica. Gli elettrodi sono lavorati in maniera ottimale e in EDM non ci sono stati assolutamente problemi. Ad oggi siamo così soddisfatti che stiamo meditando se non sia il caso di passare tutte le lavorazione di elettrodi in grafite a umido“.
Una nota arriva anche da RBM che sottolinea come, per questa tipologia di impianto, dove sono coinvolte più vasche che vanno mantenute in equilibrio per evitare tracimazioni o sbilanciamenti di livello, siano stati utilizzati dei sistemi di misurazione dei livelli specificatamente sviluppati, e gestiti da un apposito software proprietario, che garantisce una lettura completa del liquido presente nella vasca, con la possibilità di definire varie soglie di intervento sul PLC di gestione dell’impianto.
L’ingegneria innovativa di IFDR
I sistemi IFDR nascono per occuparsi della gestione completa del fluido da taglio, il cui ruolo è fondamentale sia per la buona riuscita della lavorazione meccanica, che per il corretto mantenimento della macchina utensile. Sono adatti a qualsiasi tipologia di macchina utensile presente sul mercato che utilizzi emulsione come refrigerante e sono personalizzabili secondo le specifiche esigenze, con la possibilità di essere configurati con un’ampia gamma di pompe disponibili, con pressioni e portate diversificate.
Tutti i sistemi IFDR soddisfano quattro fondamentali necessità della macchina utensile:
• Ripulire il refrigerante dai residui metallici micrometrici altamente abrasivi che si formano durante le lavorazioni;
• Rimuovere tutte le sostanze oleose che stazionano sulla superficie del liquido refrigerante;
• Ridurre la contaminazione batterica dell’emulsione allungandone la vita;
• Rilanciare alla massima pressione richiesta dall’utensile in uso il liquido perfettamente pulito nella zona di lavoro.
Nella configurazione Precision, i sistemi IFDR permettono la lavorazione di materiali non convenzionali come ceramiche, grafite, fibra di carbonio, marmo ed altri materiali nobili, e di materiali che generano polveri come quelli realizzati con tecnologia additiva, senza compromettere la vita della macchina utensile. IFDR Precision garantisce:
• sistema brevettato di filtrazione inferiore a 5 micron;
• sistema integrato di disoleazione dinamica;
• fluido da taglio in alta pressione verso il mandrino;
• riduzione del volume totale di liquido impiegato;
• riduzione dei costi di manutenzione grazie all’assenza di elementi filtranti;
• incremento vita utensili grazie alla riduzione della granulometria inquinante presente nel fluido e alla garanzia di condizioni di pressione e portata prescritte dal costruttore.
L’azienda: Sala Maurizio Stampi
Con sede a Suisio, alle porte di Bergamo, Sala Maurizio Stampi è specializzata nella progettazione e costruzione di stampi per materie plastiche e termoindurenti, in particolare per il settore automotive (interior, exterior, lighting), ma riservando spazio anche per i settori medicale e ottico.
L’officina, nata nel 1979, si distingue per la qualità delle lavorazioni e per una struttura in grado di fornire turnkey projects, gestendo internamente tutto il ciclo produttivo, dalla progettazione, all’ingegnerizzazione, al co-design, alla campionatura, per arrivare al report dimensionale dello stampo. Grazie ad un parco macchine costantemente rinnovato e ad un team tecnico motivato e altamente specializzato, Sala Maurizio Stampi può rispondere ad un’ampia gamma di necessità, arrivando anche a realizzare stampi fino a 20Ton.
Grafite: generalità
La grafite è una forma cristallina del carbonio, con una struttura stratificata di piani basali o fogli di atomi di carbonio compatti. Il colore va dal grigio scuro al nero, con riflessi quasi argentei e lucentezza metallica.
La grafite è fragile, con elevata conducibilità sia elettrica che termica, ottima resistenza agli shock termici e alle temperature elevate, sebbene inizi ad ossidarsi a 500°C; in controtendenza rispetto ad altri materiali, la resistenza e la rigidezza della grafite aumentano con la temperatura. Queste caratteristiche la rendono industrialmente interessante in molteplici settori, dall’industria dei materiali refrattari, ai lubrificanti, all’indurimento dell’acciaio, nelle matite (in combinazione con l’argilla), ma viene anche impiegata nelle spazzole dei motori elettrici e come materiale per gli elettrodi; grazie alla sua resistenza agli agenti chimici, può essere utilizzata come filtro per fluidi corrosivi. Oggi sta acquisendo sempre maggiore importanza l’utilizzo di grafite come fibra nei materiali compositi e nelle plastiche rinforzate.
E’ generalmente accettata la classificazione in ordine decrescente della dimensione del grano, con proprietà meccaniche tanto migliori quanto più piccolo è il grano, con una suddivisione in 3 macrofamiglie: grani industriali, grani fini e micrograni. Sul mercato è disponibile in blocchi di varia sezione (quadrata, rettangolare o circolare) e diverse dimensioni.
La grafite è in genere lavorata per stampaggio, formatura o cottura in forno, con successiva lavorazione per asportazione di truciolo per l’acquisizione della forma finale.
Grafite: i vantaggi nell’EDM
Elettrodi in grafite per l’EDM: perché?
• E’ facilmente lavorabile
• Resiste bene agli shock termici
• Ha un basso coefficiente di dilatazione termica, circa un terzo di quello del rame; ciò garantisce la stabilità della geometria dell’elettrodo durante il processo di elettroerosione
• E’ disponibile in blocchi anche di grandi dimensioni
• Non fonde ma, a 3400°C, passa direttamente allo stato gassoso, permettendo quindi di contenere l’usura dell’elettrodo
• Ha una densità molto inferiore a quella del Rame: gli elettrodi sono sensibilmente più leggeri
• Ha una velocità di rimozione del metallo maggiore di quella del rame, con un’usura molto bassa, 1/3 ÷ 1/10 meno del rame
• Ha un tasso di usura che decresce all’aumentare della corrente di cresta
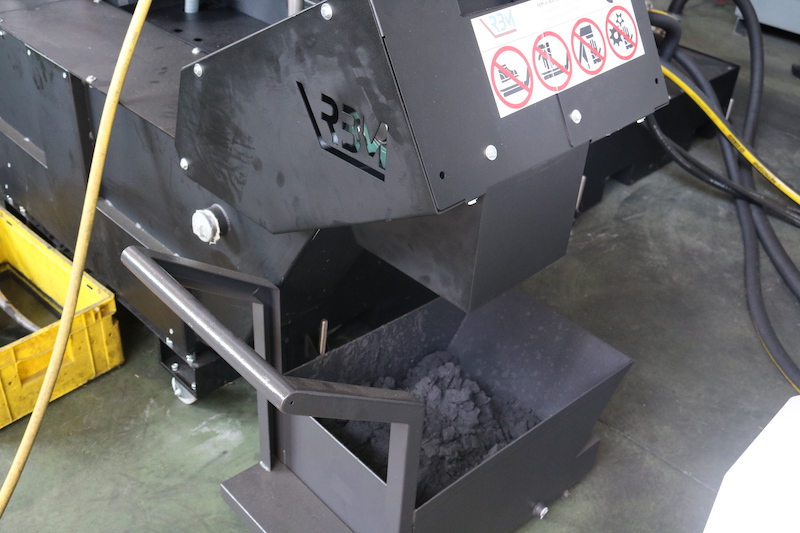
di Daniela Tommasi