L’utilizzo di normalizzati, di attrezzature standard e di acciai trattati termicamente di alta qualità permette di costruire stampi con precisione assoluta e in tempi molto ridotti.
Quando si sviluppano stampi per pezzi destinati al settore cosmetico, è necessario non solo rispettare alcuni requisiti fondamentali in termini di precisione e di qualità estetica, ma anche essere molto rapidi e puntuali, al fine di rispondere alle esigenze di un ambito particolarmente dinamico e in continua evoluzione. Abbiamo cercato di indagare l’argomento facendo la conoscenza della Bazzana S.r.l. (Agnellengo di Momo, NO), officina operante in molti settori di sbocco tra cui, appunto, quello del packaging cosmetico, in grado di offrire servizi quali la costruzione e il diretto collaudo degli stampi, oltre che lo stampaggio di manufatti in materiale plastico.
Renato Bazzana, attuale titolare assieme alla sorella Adriana, ci propone un esempio concreto, e cioè ci spiega in che modo è stato sviluppato e costruito lo stampo di una ghiera in polipropilene isotattico (Moplen), ovvero la parte interna di un tappo “contagocce” per l’erogazione di un liquido cosmetico. «Il tappo in questione – esordisce – è composto da tre parti, e la ghiera in oggetto è l’elemento in plastica che da una parte sostiene le altre due, in particolare l’elemento esterno contagocce, dall’altra consente l’avvitamento del tappo stesso al di sopra di un contenitore in vetro».
Il cliente, chiaramente, commissionò alla Bazzana la costruzione degli stampi di tutte e tre le parti del tappo contagocce, e a tal fine fornì già le matematiche dei pezzi, sviluppate in modo che il relativo assemblaggio risultasse perfetto. «Noi – riprende – operammo solamente alcuni aggiustamenti con l’obiettivo che tutti e tre i pezzi venissero stampati nel migliore dei modi e che la costruzione degli stampi risultasse la più ottimizzata possibile».
Naturalemente, ogni modifica fu concordata con il cliente che, alla fine, diede il benestare ai disegni definitivi.
Una collaborazione vincente
In merito all’attività di progettazione, Renato Bazzana spiega: «Noi siamo specializzati nella costruzione di stampi di piccole e medie dimensioni, di area massima pari a 600×900 mm, per la cui progettazione ci avvaliamo di software evoluti come VISI di Vero Solutions».
La particolarità dell’attività di sviluppo degli stampi è che, oltre dell’esperienza e della competenza dell’ufficio tecnico, la Bazzana si avvale della partnership avviata con Meusburger, costruttore austriaco di rilevanza mondiale di elementi normalizzati per stampi.
Federico Lanzoni, responsabile vendite di zona di Meusburger, racconta: «Il rapporto tra le due attività è consolidato sin dall’inizio degli anni 2000. La Bazzana fa da largo utilizzo dei prodotti della Meusburger e ciò dipende dal fatto che in noi ha da sempre trovato non solo un’ampia gamma di prodotti, di elevato livello e in costante aggiornamento, ma anche serietà, competenza e velocità di approvvigionamento. Del resto, quando un cliente investe in Meusburger, non acquista solo ottimi normalizzati, ma anche e soprattutto un servizio completo fatto di supporto in caso di necessità, e massima velocità di approvvigionamento in virtù dell’enorme disponibilità di pezzi del nostro magazzino». Bazzana conferma: «La rapidità e velocità di consegna sono uno dei fattori più importanti per avere successo ai giorni nostri sul mercato».
La collaborazione con Meusburger permette all’impresa piemontese di contare su un vasto assortimento di normalizzati e di prodotti per la meccanica, il che snellisce e semplifica l’attività di progettazione degli stampi, e consente anche di effettuare lavorazioni meccaniche in tempi brevi contando su semilavorati di altissima qualità. Bazzana prosegue: «I progettisti, una volta scelti i pezzi in base alle esigenze dimensionali e funzionali, scaricano i file delle matematiche direttamente dal portale della Meusburger che poi possono agevolmente inserire all’interno dei disegni». Questa possibilità semplifica e velocizza notevolmente non solo le fasi di sviluppo dello stampo, ma anche quelle costruttive, dato che i normalizzati selezionati vengono in genere consegnati nel giro di due-tre giorni. «All’occorrenza, inoltre, viene offerto un servizio di assistenza e di supporto tecnico “in tempo reale” nell’immediatezza della richiesta d’offerta», precisa Lanzoni.
Nel caso della ghiera in esame, lo stampo fu sviluppato utilizzando molti e diversi tipi di prodotti Meusburger, in particolare piastre in acciaio, oltre che colonne, centratori, contacolpi, micro e accessori vari. «La fornitura Meusburger ha rappresentato all’incirca il 15% del valore dell’intero stampo», specifica Bazzana.
Il sistema di iniezione
Per la progettazione dello stampo in oggetto, è importante sottolineare che fu anche eseguita una simulazione del riempimento del materiale plastico fuso, al fine di evitare giunzioni fredde, inglobamenti d’aria e limitare l’ovalizzazione. A seguito della simulazione, fu possibile evidenziare le zone più calde, ottimizzando la termoregolazione e abbattendo il tempo ciclo previsto. Fu infine scelto il sistema di iniezione con canale caldo.
Dall’ufficio tecnico all’attrezzeria
Terminata la fase di progettazione dello stampo, durata all’incirca 15 giorni, l’attività passò all’attrezzeria, dove operano centri di lavoro ad alta velocità della giapponese Makino, a 4 e 5 assi (programmate mediante il CAM Cimatron della 3D Systems), oltre a macchine più tradizionali ed elettroerosioni a filo e a tuffo della Agie Charmilles. «Una volta ricevuto i semilavorati dalla Meusburger – osserva Bazzana – iniziammo con le attività di asportazione truciolo sulle macchine utensili, in particolare di tornitura e fresatura ad alta velocità; poi di rettifica».
In particolare fu progettato e realizzato un sistema per la regolazione rapida della fasatura dell’origine del filetto per tutte le impronte, anche senza la necessità di smontare lo stampo dalla pressa
La difficoltà principale fu quella di garantire la massima precisione possibile, in modo che le impronte presenti all’interno della matrice, 16 in totale, fossero tutte perfettamente identiche, o meglio con tolleranze dimensionali dell’ordine dei 5 centesimi di millimetro.
«La nostra realtà – riprende Bazzana – è specializzata da diversi anni nella progettazione e costruzione di stampi multi-impronta, anche grazie all’utilizzo di un impianto OGP, cioè di un sistema metrologico tridimensionale ottico, in grado di certificare le parti stampanti, così da assicurare la completa intercambiabilità e la sostituzione a distanza di tempo con assoluta ripetibilità». Nel caso in questione, per assicurare la corretta sequenza delle fasi del ciclo di stampaggio e per assicurare la corretta funzionalità in fase di produzione, furono adottati diverse tipologie di sensori per la verifica della completa estrazione e del sistema di svitamento. Seguirono le lavorazioni per elettroerosione a filo, in particolare per l’esecuzione di un anello rialzato per favorire la funzionalità del punto di iniezione.
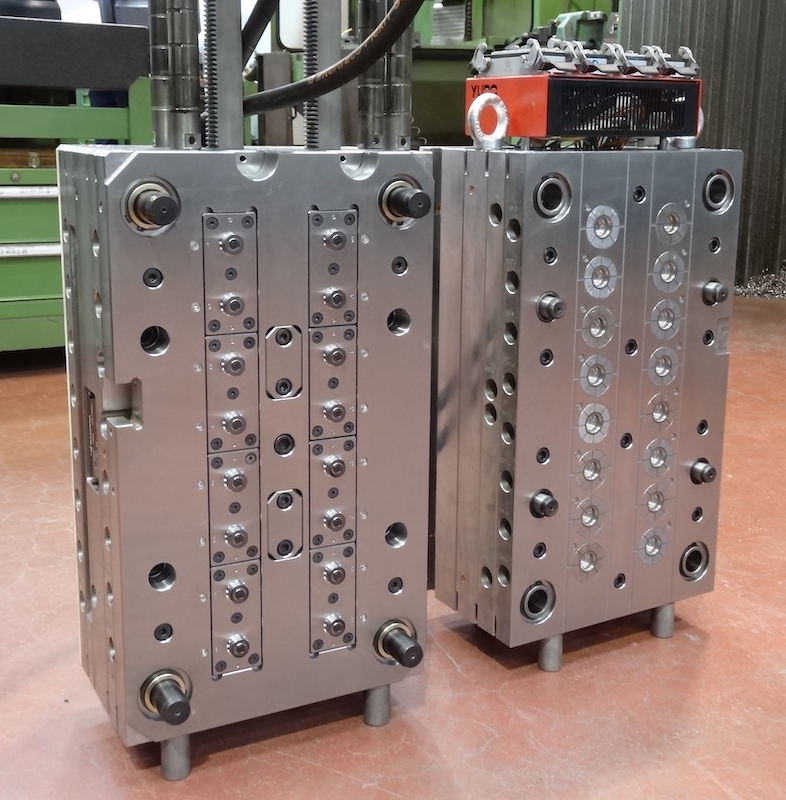
Il valore aggiunto del laser
In attrezzeria, la Bazzana si avvale anche in due macchine laser, una Sisma e una più recente GF Machining Solutions per la marcatura e la texturizzazione superficiale, una delle quali a 5 assi: «Grazie a queste due macchine innovative, riusciamo a effettuare lavorazioni supplementari molto utili per i nostri clienti, per esempio incisioni o la realizzazione di effetti superficiali molto complessi – chiarisce Bazzana –. Nello stampo in questione, numerammo come consuetudine ogni impronta della matrice con numero di profondità pari a circa 2 centesimi di millimetro, quanto basta affinché sia leggibile; eseguimmo inoltre, sempre mediante asportazione laser, le alette antirotazione evitando così la costruzione di elettrodi, soggetti a minore ripetibilità».
Qualità e velocità
Conclusa la fase costruttiva e quella di assemblaggio, durata all’incirca due mesi, lo stampo fu testato sulle presse del reparto stampaggio interno dove avvenne la produzione, nel luglio 2019, delle prime campionature; dopo il benestare finale, fu consegnato al cliente per la messa in produzione definitiva. Bazzana tira le somme: «Abbiamo lavorato con precisione e velocità, centrando gli obiettivi che ci eravamo prefissati. Il rispetto delle tempistiche, il cui parte del merito va certamente attribuito anche a Meusburger, è risultato forse l’aspetto più apprezzato dal nostro committente il quale, dall’estate scorsa, utilizza lo stampo per la produzione della ghiera, e più in generale del tappo contagocce, in continuità e senza mai interrompere la produzione».
Il segreto della “distensione”
Lanzoni sottolinea: «Uno degli aspetti maggiormente apprezzati da Bazzana e più in generale dai clienti Meusburger è la grande stabilità dimensionale delle nostre piastre. Questa è assicurata non solo dall’altissima qualità dell’acciaio, che per essere utilizzato deve superare rigorosi test e selezioni, ma anche dall’elevata qualità del trattamento di distensione termica». Quest’ultimo viene eseguito da Meusburger all’interno di tre forni dedicati, e conferisce ai materiali caratteristiche importanti. Lanzoni aggiunge: «Il trattamento di distensione dei grezzi permette di ridurre le tensioni residue presenti negli acciai generatesi a seguito delle precedenti fasi di laminazione e di raffreddamento. Ciò consente di ridurre al minimo le distorsioni dimensionali nelle successive lavorazioni meccaniche». Nei fatti, la distensione termica assicura la produzione di stampi di elevata precisione, di durata maggiore, e tempi di lavorazione più brevi grazie al sovrametallo ridotto. Bazzana conferma: «Le piastre e i componenti che riceviamo dalla Meusburger sono molto stabili, non si deformano in maniera significativa a seguito delle lavorazioni e necessitano quindi di lavorazioni di riprese minime, se non nulle». Lanzoni precisa: «Alla Meusburger, l’intero processo di distensione avviene in un forno chiuso ed ha una durata di circa 24 ore. Si tratta raffreddamento molto lento e costante a 35°C/h, che permette un raffreddamento proporzionale del nucleo e dei bordi e che impedisce la formazione di ulteriori tensioni, oltre che l’alterazione della struttura e della resistenza meccanica del materiale».
La qualità innanzitutto
La Bazzana S.r.l. (Agnellengo di Momo, NO) è una realtà specializzata nella costruzione di stampi in gran parte a iniezione plastica e, in misura minore, a iniezione-soffiaggio o per silicone; l’impresa si occupa anche della realizzazione di campionature o serie complete mediante attività di stampaggio. Nello stabilimento di Agnellengo di Momo operano macchine e tecnologie avanzate e d’ultima generazione, che permettono alla Bazzana di realizzare stampi di alta qualità e con precisione dell’ordine del centesimo. L’azienda, che conta attualmente di 24 dipendenti, al fine di soddisfare le sempre più esigenti richieste qualitative dei manufatti finiti, prevede, lungo l’intero percorso produttivo, stretti controlli mediante costanti verifiche dimensionali ed estetiche, avvalendosi di tecnologie all’avanguardia, effettuate da personale appositamente formato nell’ambito del sistema qualità.
La ricetta? Realizzare stampi complessi
La visita allo stabilimento di Agnellengo di Momo è anche l’occasione per scambiare alcune parole con i nostri interlocutori circa l’attuale fase economica. Secondo Bazzana, «negli ultimi anni il mercato è divenuto più incerto, nel senso che è sempre più difficile individuare nuovi clienti e ottenere nuove commesse, che risultano poche rispetto al numero di preventivi». Gli fa eco Lanzoni: «Il mercato, effettivamente, vive una fase di incertezza. Le decisioni vengono prese con calma e molto spesso le trattative si arrestano al preventivo. Motivazioni? Sicuramente pesano la flessione dell’industria tedesca e in generale del comparto automotive, ma anche la fase di stallo di altri mercati. Riteniamo tuttavia che si tratti di una normale fase di rallentamento e che l’andamento del mercato stesso sia ciclico». Un altro spunto di riflessione riguarda la concorrenza cinese a basso costo di manodopera che, secondo Bazzana, «è ancora molto forte. Forse la tendenza alla delocalizzazione è addirittura in aumento allorché si richiedono stampi di basso contenuto tecnologico. Per gli stampi più complessi, invece, il risparmio nel rivolgersi alla concorrenza cinese in termini di prezzo è piuttosto contenuto, nell’ordine del 20%, e spesso il gioco non vale la candela». «È vero – puntualizza Lanzoni –. Risparmiare il 20% può non essere così vantaggioso se, sull’altro piatto della bilancia, vi sono possibili problemi in termini di lontananza, di difficoltà comunicativa, di impossibilità nell’effettuare modifiche in tempi brevi, di qualità dei materiali non garantita… In tal senso, è spesso decisiva la figura del responsabile acquisti che deve saper individuare le soluzioni migliori sul lungo periodo e non quelle che determinano un risparmio nell’immediato ma grandi problemi nel seguito».
Carta d’identità dello stampo
- Pezzo finito: ghiera di un tappo “contagocce” per l’erogazione di liquido cosmetico.
- Materiale del pezzo finito: polipropilene isotattico (Moplen).
- Cliente finale: confidenziale.
- Portastampi ed elementi normalizzati: Meusburger Georg GmbH & Co KG.
- Dimensioni: 346x596x435 mm (asse Y = 1.430 mm considerando il sistema idraulico)
- Peso: 685 kg
- Durata della progettazione/costruzione stampo: 2 mesi e mezzo
- Fabbricante: Bazzana S.r.l., Agnellengo di Momo (NO), 28015 – Via Regina Margherita 14 Tel.: +39 0321 926470; email: info@bazzanasrl.it; www.bazzanasrl.it.
- Software CAD/CAM: Vero Solutions VISI, 3D Systems Cimatron.
- Tecnologie di costruzione: centri di lavoro Makino a 4 e 5 assi ad alta velocità; elettroerosioni a filo e a tuffo Agie Charmilles; laser Sisma e GF Machining Solutions; macchine tradizionali.
- Tempo ciclo stampaggio: 18 secondi circa.
di Vittorio Pesce