Le vibrazioni, un effetto indesiderato ma tipico delle lavorazioni per asportazione di truciolo. Contenerle è un obbligo.
Ogni tecnico di produzione lo sa: le vibrazioni sono il principale ostacolo all’esecuzione di lavorazioni meccaniche che abbiano la produttività e la qualità desiderata. Ma perché? Perché le vibrazioni influenzano negativamente la velocità di taglio e riducono l’avanzamento, diminuendo la vita degli utensili e costringendo a scendere a fastidiosi compromessi tra la finitura ideale, la perfezione, e il risultato che realmente può essere raggiunto. Infatti, qualsiasi macchina utensile sarà sempre soggetta a vibrazioni, data la presenza di forze motrici variabili che, più o meno marcatamente, deformano i componenti. Alla comparsa di deformazioni è associata la presenza di stati vibratori, che possono manifestarsi anche sotto forma di onde sonore. L’evoluzione tecnologica ha permesso di equipaggiare le macchine utensili con soluzioni atte a eliminare le vibrazioni e i fenomeni di superfici vibrate, ma non è detto che queste siano sempre praticabili o che siano pienamente risolutive. Ostacoli tipici possono essere l’assetto della macchina o il budget. Quindi è d’obbligo “tenersi” le vibrazioni? Chiaramente no.
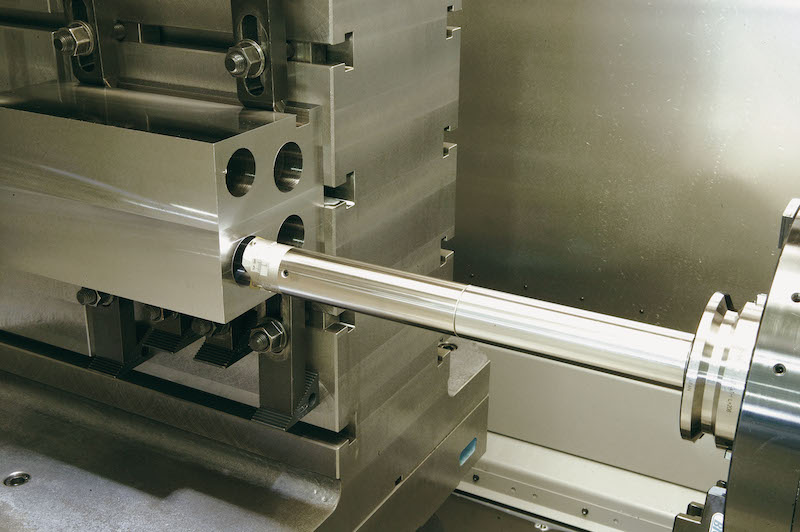
Gli eventi scatenanti…
Prima di cercare le risposte, è sempre bene aver chiaro il perché di ogni situazione. E le vibrazioni non fanno eccezione.
Le cause dello stato vibratorio che si manifesta durante le lavorazioni per asportazione di truciolo possono essere ricondotte a:
• cambi repentini di direzione, continui arresti e riavvii, sia della tavola che dell’utensile. Ciò provoca una deviazione dell’utensile nel momento in cui inizia il taglio;
• presenza di forze divergenti durante la lavorazione. Queste sono dovute, per esempio, ad utensili o pezzi non perfettamente bilanciati, così come l’impiego di frese multi-tagliente, che tendono a produrre una certa risonanza;
• il sovrametallo può ridursi significativamente a causa di una certa instabilità del processo di taglio, di frizioni, o a seguito dell’accumulo di tensioni nella struttura della macchina utensile e nel processo di taglio.
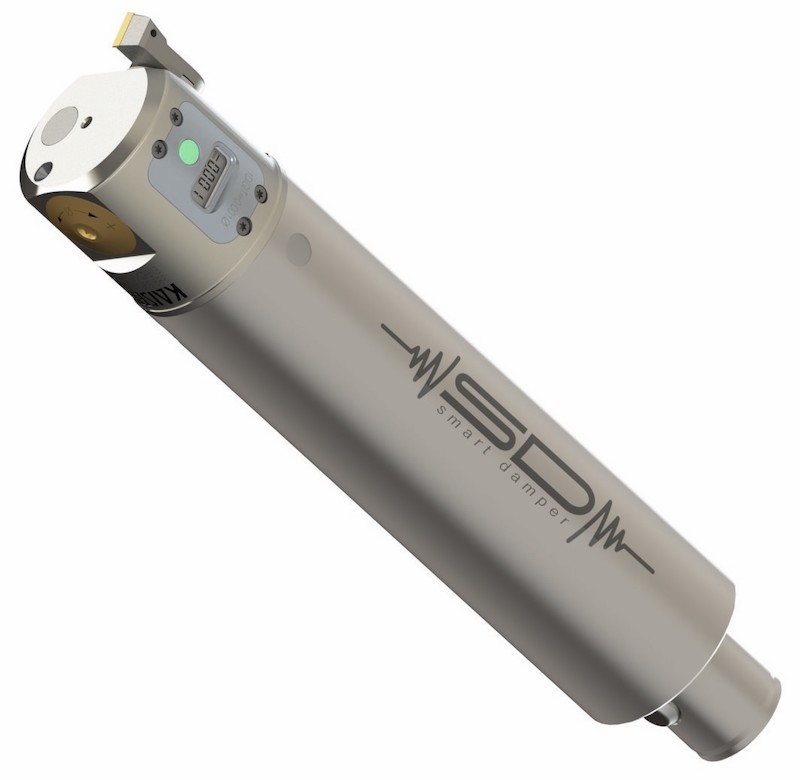
… il ruolo dello staffaggio…
Un altro fattore che influenza la manifestazione di uno stato vibratorio è legato allo staffaggio del pezzo: in questo caso una scelta interessante, e spesso consigliata, consiste in una soluzione di bloccaggio realizzata in materiale minerale. Sia i materiali che le tecniche impiegati per realizzare questo tipo di supporto riducono il peso e incentivano lo smorzamento delle vibrazioni tra la tavola e il pezzo, con il risultato che i tassi di attenuazione possono superare di 6÷10 volte quelli della ghisa. In che modo viene raggiunto questo risultato? I componenti vengono lavorati con precisione, fissati tramite perni temprati e rettificati, riempiti con un composto di particelle minerali e resina epossidica. Da notare come la struttura composita finale è prodotta senza generazione di calore, così da preservare l’integrità delle superfici lavorate di precisione e dei componenti di bloccaggio. Le particelle minerali costituiscono circa il 90% del peso aggiunto, il rimanente è dato da resina e agenti indurenti. Questa struttura composita ha un eccellente rapporto densità/peso, 2,3 kg/dm³, che quindi significa soluzioni più leggere del 50%, in grado di offrire una maggiore produttività e una miglior qualità.
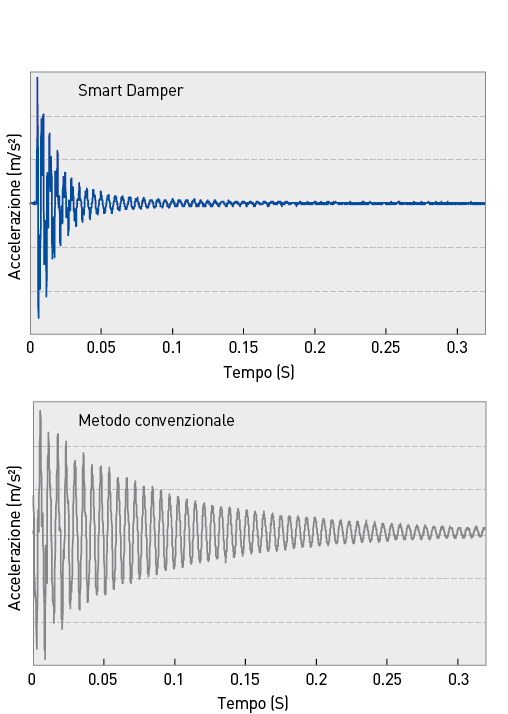
… e della sporgenza
Quando si parla di vibrazione e utensili, la parola chiave è sporgenza, una condizione talvolta nota come rapporto lunghezza-diametro. Infatti, quando la sporgenza aumenta, questa diventa l’anello debole, o l’elemento più delicato, dell’intero processo dato che favorisce l’insorgenza di vibrazioni dannose. Il problema è ben noto e diffuso, soprattutto in settori come la costruzione di stampi, l’industria aerospaziale, l’automotive e l’oil & gas. In linea di massima è consigliabile utilizzare il diametro più grande possibile alla lunghezza minima, l’attrezzatura più leggera e il raggio di inserto più piccolo, anche se, quando i requisiti sono piuttosto impegnativi, le configurazioni ideali non sempre sono fattibili. In queste condizioni, una volta che gli utensili hanno una lunghezza che supera 4 volte il diametro, la deflessione inizia a moltiplicarsi a ritmi notevoli, anche con forze di taglio costanti: il passaggio a utensili con caratteristiche di smorzamento si rivela spesso un’opzione ragionevole.
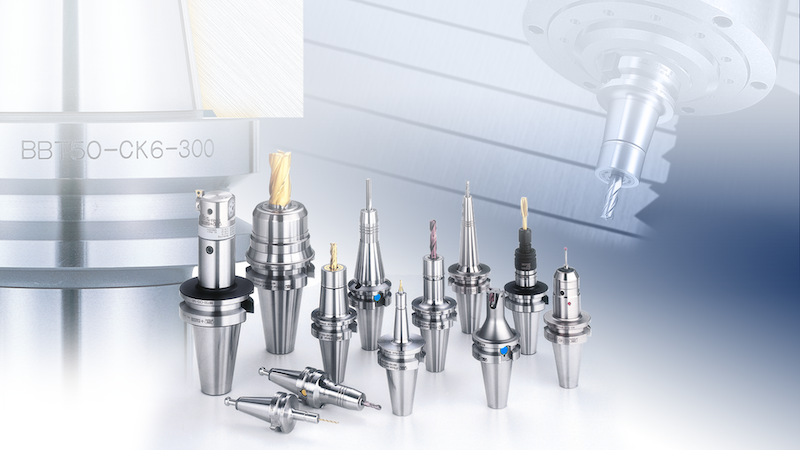
Le opzioni
I costruttori di macchine utensili stanno sviluppando tecnologie sempre più evolute con l’obiettivo di mantenere sotto controllo e ridurre i problemi legati alle vibrazioni. Per esempio, gli accelerometri sono in grado di sopportare le condizioni difficili delle aree di lavoro riuscendo a fornire dati accurati; altre tecnologie si spingono addirittura oltre, raccogliendo i dati direttamente dal tagliente e inviandoli al controllo, dove è possibile modificare la velocità del mandrino ogniqualvolta ci sia il rischio di vibrazione. Inoltre, i costruttori di macchine tentano di affrontare questa secolare sfida anche dal punto di vista strutturale, impiegando per esempio rivestimenti in turcite, un materiale con elevata capacità di smorzamento. L’elenco potrebbe andare avanti all’infinito: mandrini più corti e più compatti; cuscinetti ibridi di precisione; mandrini bilanciati dinamicamente… Un’altra possibilità è quella che prevede l’impiego di un‘interfaccia doppio contatto tra il mandrino macchina e l’utensile, che ne aumenta la rigidità. Negli ultimi 20 anni più di 200 costruttori di macchine utensili hanno adottato questa configurazione, che assicura il contatto simultaneo di flangia e cono. Infatti, aumentare la rigidità offre diversi interessanti vantaggi, oltre a quello di limitare le vibrazioni, motivo per cui il sistema a doppio contatto è andato diffondendosi rapidamente fra i costruttori di macchine utensili. C’è anche un’ulteriore interessante soluzione proposta dal costruttore di utensili svizzero Big Kaiser, ed è il sistema modulare per la fresatura Smart Damper che incorpora un meccanismo di smorzamento passivo in prossimità del tagliente con azione contraria, tramite azione di attrito ad alta risonanza. La capacità di smorzamento del sistema riduce al minimo gli effetti delle oscillazioni a frequenza elevata, assorbendo efficacemente le vibrazioni e garantendo livelli superiori di precisione di lavorazione. Lo smorzamento delle vibrazioni avviene senza l’impiego di lubrificanti, e permette una maggiore precisione e velocità, unitamente a una riduzione dei costi.
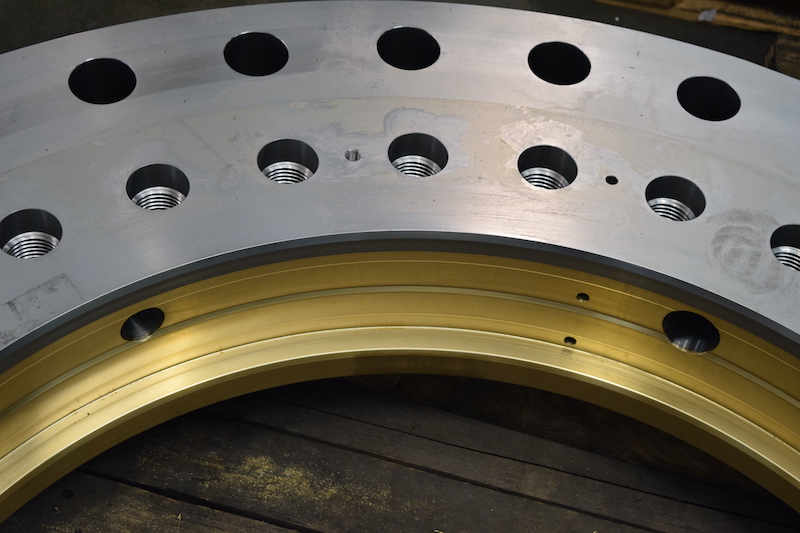
Il sistema Smart Damper
Smart Damper di Big Kaiser è un sistema per la sgrossatura o la finitura, con meccanismo antivibrazioni integrato. La testa di sgrossatura a due taglienti semplifica l’esecuzione rapida di barenature profonde nel ferro e nell’acciaio, senza alcuna vibrazione né fenomeni di superfici vibrate. In questo modo è possibile conseguire una maggiore produttività e realizzare lavorazioni più veloci e silenziose, a vantaggio della riduzione dei costi di processo. SW Smart Damper può raggiungere una velocità di taglio di oltre 200 m/min per l’acciaio ad una lunghezza di 8xD, senza vibrazioni: un risultato 4 volte migliore rispetto alla velocità massima senza vibrazioni (50m/min) consentita senza l’ausilio della barra. Big Kaiser ha potuto raggiungere questo risultato grazie al brevetto della struttura di Smart Damper, costituita da un corpo in metallo con speciali ammortizzatori in gomma interni, e che non prevede l’utilizzo di lubrificanti. Quando la barra vibra, i pesi metallici, o gli ammortizzatori ad attrito, compensano le vibrazioni modificando la loro posizione, e ogni componente è libero di muoversi in maniera indipendente. Inoltre, Smart Damper può eseguire due lavorazioni di sgrossatura senza dover sostituire alcun componente. Un inserto viene impiegato per assicurare una elevata velocità di lavorazione (gli inserti sono sullo stesso diametro e lunghezza), mentre l’altro rimuove grandi quantità di materiale (gli inserti vengono montati con offset del diametro e dell’altezza). Questo è possibile perché il corpo dell’utensile fornisce un supporto perfettamente stabile per i portainserti, di diverse altezze e lunghezze.
Precisione è collaborazione
Lavorare superleghe come l’Inconel richiede accortezza ed esperienza; se poi i pezzi da produrre sono unici e destinati ad un settore dagli standard elevati come quello energetico, allora si tratta di una vera e propria sfida. E per vincerla è indispensabile unire le competenze e collaborare come partner tecnologici. Covis è un gruppo di riferimento a livello globale per realtà nazionali e internazionali del settore petrolchimico, energetico, navale e siderurgico. Fondata nel 1994, la società progetta soluzioni su misura rispettando tempi di consegna e standard di qualità, gestendo e certificando l’intero ciclo produttivo delle tre sedi operative. Per l’oil & gas Covis realizza componenti di dimensioni medio-grandi con diametri che vanno da 500 a 2.500 mm e forature profonde su materiali esotici e trattati quali acciaio, Inconel, Duplex e Super Duplex e altre leghe speciali. La durezza del materiale da lavorare, scelta obbligata per resistere agli stress ossidativi, corrosivi e di temperatura dell’applicazione, comporta alcune problematiche – prima fra tutte le vibrazioni – che influenzano negativamente la concentricità del foro e la qualità della superficie finita.
«La prima fase del processo è data dalla preparazione del pezzo, la sgrossatura – spiega Fabio Soprana, Technical Dept. manager di Covis –. Segue il riporto di materiale, che molto spesso è Inconel 625, Stellite, Duplex e Super Duplex, vari gradi inossidabili. Infine, l’ultima parte è data dalla finitura di precisione».
Oltre a coinvolgere materiali ostici, il calore generato dalla lavorazione viene scaricato tutto sull’utensile, che subisce quindi forti sollecitazioni e stress. Le velocità di taglio sono basse, i tempi di contatto sono lunghi e i tempi di lavorazione estesi. Per questo motivo, è necessario utilizzare sistemi per lo smorzamento delle vibrazioni, così da assicurare la massima precisione nella finitura del pezzo, nonostante il contesto gravoso. Inoltre, la profondità dei fori da finire è considerevole, e le tolleranze da rispettare sono molto strette, con gradi di finitura spinti fino a 0,4~0,2 di rugosità. Fondamentale quindi affidarsi a un partner di utensili come Big Kaiser capace di assicurare sempre la massima precisione e ripetibilità, e di eliminare il problema delle vibrazioni che potrebbe inficiare la qualità richiesta al pezzo. Oltre a bareni, teste di sgrossatura di Big Kaiser, Covis utilizza il sistema modulare per lo smorzamento delle vibrazioni Smart Damper. Le barre Smart Damper hanno permesso di effettuare forature profonde con finiture di precisione su valvole con riporti in Inconel, con risultati che, in passato, con gli utensili di altri fornitori, non era stato possibile raggiungere, garantendo precisione di concentricità fino a 8-9xD (45×420 – 53×480). Inoltre, tutti i centri di lavoro presenti in officina sono equipaggiati con l’attacco Big Plus, l’unico sistema al mondo a garantire il doppio contatto simultaneo cono-flangia tra mandrino e macchina, un altro importante aiuto per tenere sotto controllo le vibrazioni dando più rigidità alla macchina.
«Lavorando con forature profonde e barre antivibranti è importante aggiungere ulteriore rigidità alla macchina – conferma Soprana –. Dopo diversi anni che usiamo le soluzioni Big Kaiser che smorzano le vibrazioni, oltre al sistema doppio contatto Big Plus, posso dire che insieme abbiamo fatto le scelte più corrette. Con Big Kaiser si lavora in macchina insieme, e ogni volta è una sfida riuscire a mettere a punto quello che è stato ideato in fase di progettazione». E Soprana non ha dubbi: «Con Big Kaiser sappiamo che le sfide saranno vinte».
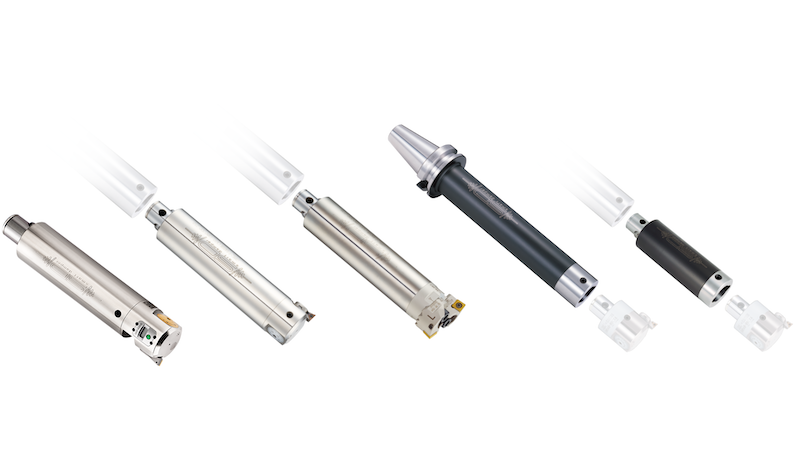
Conoscere Big Kaiser Precision Tooling
Fondata nel 1948, Big Kaiser sviluppa, produce e commercializza utensili sofisticati e soluzioni per lavorazioni meccaniche di alta precisione destinate al settore automobilistico, militare e aerospaziale, dell’energia e delle microlavorazioni, come medicale, elettronica e orologeria. Big Kaiser ha sede principale a Rümlang, in Svizzera, e filiali in Germania e negli Stati Uniti. La gamma di prodotti, realizzata al 100% in Svizzera e in Giappone, comprende più di 20 mila utensili di precisione, conformi ai più severi standard di qualità. Fiera di aver sempre anticipato le tendenze di mercato in termini di precisione, prestazioni, innovazione e servizio, Big Kaiser produce autonomamente i display digitali e i sistemi di misura elettronici utilizzati all’interno delle sue teste d’alesatura di precisione digitali, per garantire la accuratezza assoluta delle regolazioni ed eliminare le possibilità di errore degli operatori. Big Kaiser è parte del gruppo Big Daishowa, che impiega 900 dipendenti nel mondo.
di Daniela Tommasi