Come noto, la famiglia delle ghise propone un gran numero di protagonisti, molto diversi tra loro per composizione chimica, caratteristiche fisiche e applicazioni (Tabella 1 e 2). Per questi materiali tutte le proprietà fondamentali risultano regolate, tra l’altro, dalla dimensione, forma e distribuzione delle particelle di grafite. Ad esempio, la resistenza a trazione può variare da 124 a 930 MPa (o anche più), passando da una ghisa grigia ad una sferoidale, dove la grafite assume la forma di noduli sferici. Invece di rappresentare un limite, questa grande variabilità nelle peculiarità ne estende le opportunità di impiego. Consente infatti di ottimizzare materiali e processi a partire dalle peculiarità dei componenti che si andranno a realizzare con questi materiali, con un occhio anche rivolto alle specifiche funzioni e condizioni di utilizzo. Intervenendo sui processi fusori, è possibile ottenere, ad esempio, tanto una ghisa ad alta resilienza e moderata resistenza quanto una lega ad elevata resistenza e basso allungamento. Questo studio sperimentale ricava e pone a confronto le proprietà meccaniche di trazione di due tipologie di materiali da fonderia: una ghisa sferoidale (SGI) e una ghisa a grafite compatta (CGI). Anche se i processi utilizzati per la loro produzione possono apparire, come si vedrà, quasi identici, queste due leghe sono caratterizzate da nette differenze nella forma delle particelle di grafite e, di conseguenza, nelle proprietà meccaniche. Inoltre, mentre la SGI beneficia di un’ampia letteratura scientifica che ne supporto il suo largo utilizzo, la CGI è relativamente inesplorata.
Materiali e metodi
Fusioni in ghisa
Tutti i provini sono stati ottenuti attraverso colata in sabbia (Figura 1): questo procedimento è rappresentivo di oltre il 70% delle fusioni realizzate oggigiorno. SGI e CGI sono state prodotte all’interno di uno stesso processo fusorio, partendo da una stessa base di metallo fuso ed intervenendo opportunamente sugli additivi. Nello specifico, una massa fusa, caratterizzata da un contenuto di zolfo inferiore allo 0.01% (in peso), è stata inoculata con aggiunte di leghe Fe-Si e Fe-Si-Mg fino ad ottenere un primo getto in SGI. A quel punto, è stato aggiunto anche Ti portando alla produzione di un secondo getto in CGI. Lungo tutta la procedura, particolare attenzione è stata rivolta a mantenere inalterate le altre condizioni di processo quali, nello specifico, la stessa temperatura di colata (fissata a 1400 °C).
Prove di trazione
I test di trazione prevedono campioni di materiale sottoposti a carichi di trazione uniassiale aumentati fino alla rottura. I risultati sono utilizzati per selezionare un materiale rispetto a una singola applicazione, ma anche per comprendere come tale materiale reagirà sotto una diversa configurazione di forze. Tramite queste prove possono essere misurate direttamente proprietà quali:
• resistenza a rottura;
• allungamento massimo a rottura;
• riduzione dell’area.
Ma è anche possibile determinare indirettamente proprietà aggiuntive quali:
• modulo di Young (o di elasticità);
• modulo di Poisson (o di contrazione trasversale);
• resistenza a snervamento;
• curva tensione-deformazione.
Nel caso in esame, le prove di trazione sono state eseguite utilizzando una pressa servo-idraulica uniassiale Instron 1343 (Figura 3) e in accordo con la EN 10002-1. Questa norma descrive in dettaglio la procedura di prova andando ad individuare con precisione, tra l’altro, forma e dimensioni dei campioni. Questa forma, conosciuta con il termine di “osso di cane” (Figura 6), permette di avere estremità più ampie, adatte a essere afferrate dalla macchina di prova, a fronte di una sezione centrale ridotta, in modo tale che deformazioni e cedimenti possano concentrarsi solo in tale area. Questa forma è stata ottenuta per lavorazione utensile, a partire dal pieno, seguendo le indicazioni della EN 1563. Tale standard europeo è proprio dedicato alla ghisa sferoidale andando a descriverne i requisiti in termini di proprietà e durezza per una sua classificazione.
Sforzo reale vs ingegneristico
Durante gli esperimenti si è prestata attenzione a distinguere: sforzo ingegneristico, ottenuto presupponendo che l’area di azione della forza resti invariata durante la prova. Non si tiene quindi in conto del fatto naturale che all’allungarsi del provino deve corrispondere una sua costrizione con conseguente modifica della sezione trasversale; sforzo reale, ottenuto considerando tale variazione.
Per calcolare lo sforzo ingegneristico, il carico applicato è diviso per l’area della sezione trasversale originale (area nominale). Al contrario, lo sforzo reale sarebbe da ottenersi dividendo lo stesso carico con l’area della sezione trasversale deformata. Purtroppo, a meno di non monitorare continuamente tanto lo spessore quanto la larghezza dell’area di contatto durante il test, non è possibile ricavare direttamente lo sforzo reale. Tuttavia, si può arrivare a questo risultato appoggiandosi alla teoria che propone una relazione tra valori ingegneristici e reali attraverso il coefficiente di Poisson. Il diagramma tensione-deformazione (o stress-strain) di Figura 4 evidenzia la differenza tra i due concetti di sforzo reale ed ingegneristico. Si può quindi osservare l’andamento, quando espresso in termini di sforzo ingegneristico, mostri un aumento costante e proporzionale della tensione in linea con un aumento costante del carico di prova fino a un certo massimo, corrispondente, in sostanza, al valore della tensione di snervamento.
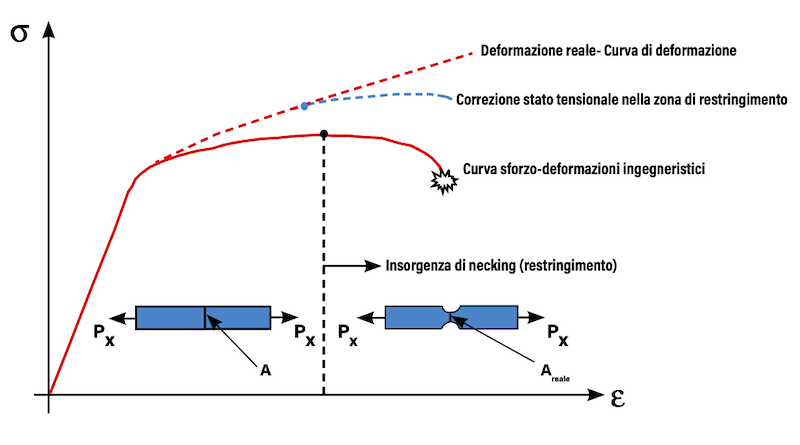
Lo sforzo reale, che misura invece quello che rappresenta il livello reale di stress “subito” dal materiale, appare crescere ininterrottamente. Al di là delle differenze, quello che appare chiaro in figura, è come lo sforzo reale possa anche arrivare a essere significativamente superiore a quello ingegneristico. Di conseguenza, conviene sempre, quando possibile, verificare anche gli effetti dello sforzo reale sulle strutture.