Presentiamo com’è stato sviluppato e costruito lo stampo della griglia del radiatore della nuova Fiat Tipo, prodotta dal gruppo FCA dal 2015.
I pezzi che compongono un’automobile sono molte migliaia, e ognuno di essi ha una sua “storia produttiva” che, il più delle volte, è di grande interesse tecnologico.
Approfondiamo in questo articolo il tema delle griglie, cioè di quel componente che, posto sulla parte frontale dell’automobile, permette l’areazione del radiatore, che è l’elemento che consente il raffreddamento del motore. Le griglie sono parti in materiale plastico all’apparenza come altri, ma che invece richiedono un elevato grado di specializzazione e tecnologie produttive adeguate.
Per comprendere al meglio il tema, abbiamo fatto la conoscenza della Tekmar S.r.l di Rivoli (TO), realtà attiva da oltre 20 anni nella progettazione e nella costruzione di stampi a iniezione di materiale termoplastico, destinati in massima parte al settore automotive. La società, in particolare, sviluppa e realizza stampi per costruttori come Ford, Lamborghini, Porsche, Opel, Jeep e Iveco destinati alla produzione di componenti di plance, gruppi cassetto, pannelli porta , spoiler, componenti paraurti, e soprattutto di griglie per radiatori.
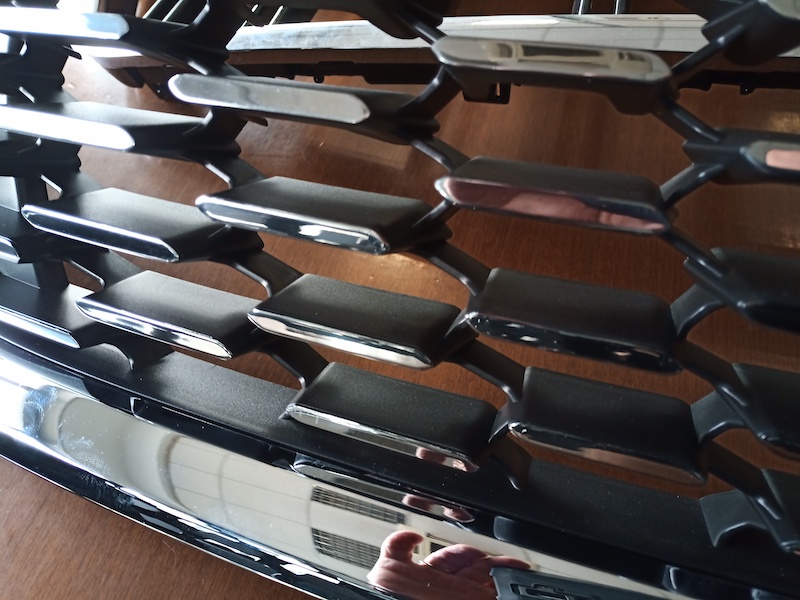
“Gianduiotti” dal profilo particolare
Il manager director di Tekmar, Dario Monici, entra subito nel vivo dell’argomento proponendoci un esempio concreto, e cioè in che modo è stato progettato e costruito lo stampo per griglia del radiatore della nuova Fiat Tipo, vettura prodotta dal gruppo FCA negli stabilimenti di Bursa in Turchia, che fu immessa sul mercato nel 2015 e venne ispirata al modello storico prodotto negli anni ’80 e ’90 dalla casa torinese. «La griglia in questione – Monici –, la cui geometria complessiva ci fu fornita dai tecnici di FCA, doveva essere realizzato in ASA, un materiale termoplastico che contiene gomma e che risulta di grande stabilità, elevata durezza e ottima resistenza chimica e meccanica. La particolarità è che tale griglia doveva essere costituita da una serie di elementi solidi, successivamente da noi denominati “gianduiotti”, componenti la trama della stessa. La particolarità del progetto è che questi gianduiotti dovevano avere un profilo particolare per favorire la successiva operazione di “hot stamping”».
La griglia finita, difatti, prevedeva che le superfici a vista di tali elementi fossero ricoperte da un sottilissimo film di alluminio al fine di risultare lucide e cromate; tale film doveva essere applicato attraverso un processo definito, appunto, “hot stamping” (stampa a caldo). «L’hot stamping – riprende Monici – è un particolare sistema di stampa nel quale un foglio sottilissimo di metallo viene applicato su una superficie mediante lo svolgimento di una bobina e per mezzo della pressione di una matrice a determinate temperature».
La particolarità di questo processo, che veniva adoperato da poche case costruttrici di automobili e che richiede macchinari appositi, è che gli elementi plastici sui quali viene trasferita la pellicola alluminata devono avere una forma e un profilo molto particolare . Ciò al fine di permettere il taglio perfetto del foglio sugli elementi stessi, per garantire la perfetta aderenza dello strato metallico e per impedire distacchi indesiderati.
Per assicurare l’assoluta riuscita del processo, i progettisti di Tekmar dovettero studiare e definire il profilo dei “gianduiotti” con molta attenzione, disegnando profili secondo linee e angoli ottimizzati secondo le specifiche del processo di “hot stamping”, sempre sotto la stretta collaborazione dei tecnici di FCA, per i quali era indispensabile che il risultato finale, dal punto di vista estetico, rispecchiasse quanto richiesto dal progetto iniziale.
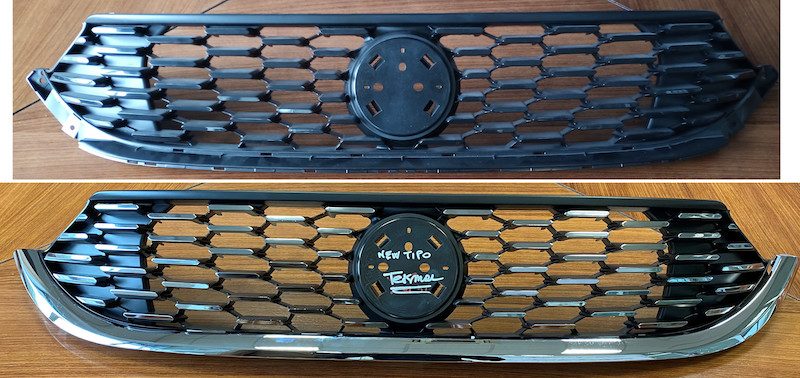
La progettazione dello stampo
Monici spiega: «Mentre definivamo la geometria dei “gianduiotti”, procedevamo in parallelo con la progettazione dello stampo. Sottolineo al riguardo che il nostro ufficio tecnico dispone di CAD/CAM del calibro di CatiaV5 e Work NC e, acquistato di recente, di Moldex3D, software per la simulazione della fase di riempimento delle cavità dello stampo».
Nel caso in questione, i tecnici Tekmar misero particolare attenzione alla definizione del sistema di iniezione, assicurando un riempimento omogeneo della cavità, un raffreddamento costante, e soprattutto che le linee di giunzione si generassero sul lato interno della griglia al fine di non creare problemi dal punto di vista estetico sulla parte frontale. Monici aggiunge: «Lo stampo in oggetto è un’attrezzatura ricca di movimenti quali sciabole e carrelli, che hanno il fine di generare, oltre che le fenditure della griglia, le tipiche “clip” che servono poi ad agganciare il paraurti sul quale la griglia va montata».
L’elettroerosione che fa la differenza
Terminata la fase di progettazione dello stampo, durata all’incirca un mese e mezzo, le attività passarono all’attrezzeria per la fase esecutiva; qui Tekmar dispone di diverse macchine, tra cui 7 frese ad alta velocità, delle quali tre a 5 assi e una a portale, di marche quali Parpas, Rambaudi, Sachman e Correa, una foratrice IMSA, oltre che rettificatrici, alesatrici, tre macchine per elettroerosione a filo e tuffo di brand quali ONA e CDM e un impianto per la saldatura laser. Monici precisa: «La nostra è un’officina meccanica molto evoluta che ci permette di realizzare attrezzature anche molto complesse. Per esempio, l’esecuzione della matrice del nostro stampo, realizzata in acciaio 1.2343, è risultata particolarmente impegnativa a causa delle figure dei famosi “gianduiotti”, trattandosi di cave molto strette e profonde da realizzare con precisione esasperata e raggi di curvatura da 0,2 mm e lucidatura con diamante nell’ordine di 1 micron».
In particolare, il fondo di tali cave doveva risultare pressoché lappato al fine di garantire la perfetta aderenza del film di alluminio (che ha spessore di circa 3 micron) da stampare a caldo sul pezzo in plastica. «Lucidare a specchio il fondo di una cava così stretta e sottile è tutt’altro che banale, ma è l’unico modo per garantire la riuscita dell’hot stamping e quindi per assicurare l’effetto lucido e cromato finale della griglia voluto dal cliente», afferma Monici.
A tal fine furono effettuate operazioni di elettroerosione a tuffo, con elettrodi in grafite per una prima lavorazione di sgrossatura, e successivamente con elettrodi in rame per la finitura conclusiva; quest’ultima operazione, in particolare, necessitò il ricorso a un macchinario di elettroerosione con tecnologia di superfinitura di un fornitore esterno. Ma non basta: «Per ottenere la rugosità richiesta del fondo delle cave, dovemmo provvedere con un’ulteriore lavorazione di diamantatura eseguita manualmente con utensili speciali di piccole dimensioni – ricorda Monici –. Con la realizzazione delle prime campionature, ci rendemmo conto di aver svolto un buon lavoro e di essere riusciti a ottenere la rugosità desiderata».
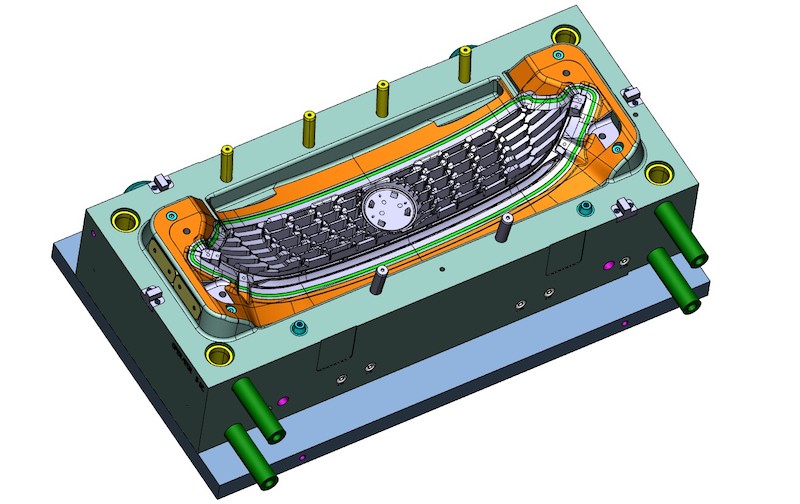
L’avvio della produzione
Dopo la fase di costruzione e di assemblaggio, durata all’incirca quattro mesi, lo stampo fu messo a punto e collaudato su una delle presse presenti nello stabilimento di Rivoli, dopodiché fu spedito allo stampatore in Turchia che avviò la produzione su una pressa da 1.000 tonnellate. Monici conclude: «Grazie alla messa a punto preventiva, lo stampo entrò sin da subito in funzione, con una produzione di circa 1.200 griglie al giorno. La qualità era quella desiderata da FCA, difatti i pezzi stampati risultavano perfettamente idonei alla successiva lavorazione di “hot stamping”. La soddisfazione del cliente fu tale che nel giro di pochi mesi dovemmo costruire un secondo stampo uguale al primo al fine di raddoppiare la produzione».
Dallo stampo allo stampaggio
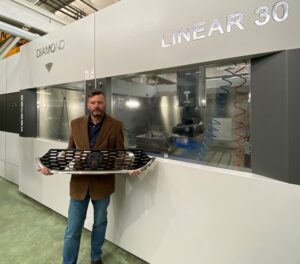
Tekmar S.r.l. (Rivoli, TO) nasce nel 1996 come officina meccanica di precisione e, nel corso degli anni, si è specializzata nella produzione di stampi per plastica per il settore automotive, spinta dalla “vocazione automobilistica” che storicamente contraddistingue Torino e il Piemonte. Oltre all’ufficio tecnico e all’attrezzeria, l’officina dispone di alcune presse a iniezione per il collaudo degli stampi, equipaggiate con robot a 3 assi e con forza di chiusura compresa tra 350 e 1.300 tonnellate. Monici spiega: «Grazie a queste macchine e all’acquisto di altre quattro presse, due BM Biraghi e una Sandretto, con forza di chiusura tra 100 e 300 tonnellate, e di una pressa della Krauss Maffei “a cubo”, cioè a due iniezioni, da 1.600 tonnellate, costituiremo a brevissimo un reparto di stampaggio indipendente. Tekmar sarà dunque in grado di effettuare produzioni in serie proponendosi sul mercato come realtà ancora più completa e competitiva».
Stampo e stampaggio: carta d’identità
Pezzo finito: griglia del radiatore della nuova Fiat Tipo
Stampista: Tekmar S.r.l., via Acqui, 10 – Rivoli (TO)
Materiale matrice: acciaio 1.2343
Dimensioni stampo: (1370x800x1.051) mm
Tempo progettazione stampo: 1,5 mesi
Tempo realizzazione stampo: 4 mesi
Software progettazione: CatiaV5, Work NC
Tecnologie di produzione: frese ad alta velocità a 3 e 5 assi, Rambaudi, Sachman, Correa; rettificatrici e alesatrici; elettroerosione a filo e tuffo ONA, CDM
Produzione: 1.200 pezzi/giorno
di Vittorio Pesce