In questo studio si descrive un approccio basato sull’intelligenza artificiale, per ottimizzare i parametri di pallinatura, al fine di massimizzare la resistenza a fatica dell’acciaio AISI 316.
È noto che il cedimento per fatica, ha origine, il più delle volte, dalla superficie libera dei componenti.
Questo giustifica il grande interesse che è stato, ed è ancora oggi, dedicato allo sviluppo di processi e trattamenti atti a migliorare la resistenza a fatica degli strati superficiali di materiali.
In breve, i fattori che contribuiscono a determinare la resistenza meccanica in presenza dei carichi ciclici sono la finitura superficiali, l’incrudimento del materiale e la presenza di tensioni residue che, se di compressione in superficie, danno un rimarchevole effetto per il miglioramento delle prestazioni a fatica dei componenti meccanici.
Tra i trattamenti più utilizzati a tal fine, la pallinatura (o shot peening) è senz’altro tra i più popolari, per l’effetto, la flessibilità, l’applicabilità a una vasta gamma di geometrie, l’assenza di rifiuti tossici e il costo.
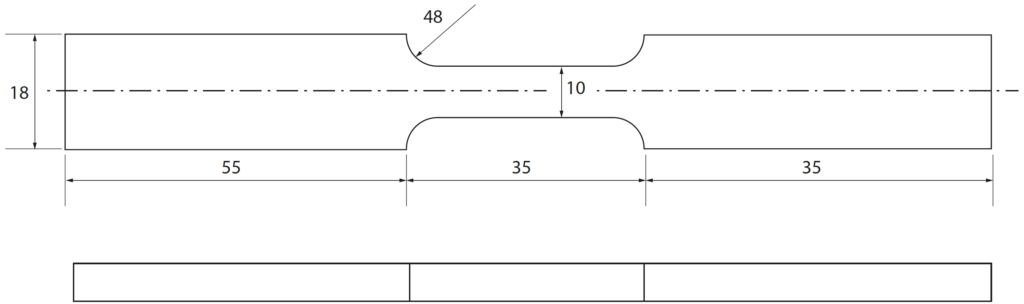
La pallinatura consiste nel bombardare con un flusso di sfere di piccole dimensioni la superficie di interesse.
L’energia del flusso di sfere è tale da indurre, negli strati superficiali di materiale una deformazione plastica non uniforme in profondità, responsabile sia della generazione di sforzi residui superficiali di compressione e l’incrudimento del materiale, sempre negli strati superficiali di materiale.
Un ulteriore effetto della pallinatura è la modifica della finitura superficiale.
Il risultato finale della pallinatura dipende dal valore dei principali parametri che caratterizzano il processo: il materiale e le dimensioni delle sfere, l’energia cinetica con cui sono scagliate contro il bersaglio e la durata del trattamento stesso.
A livello industriale, il trattamento di pallinatura è caratterizzato principalmente attraverso due grandezze, l’intensità Almen e la copertura (coverage).
L’intensità Almen è una misura dell’energia del trattamento, ed è definita come la freccia residua di una piastrina sottile di dimensioni e materiale assegnato pallinata su una sola faccia.
La copertura è una grandezza legata alla durata del trattamento e si misura considerando la percentuale della superficie pallinata rispetto alla superficie totale: una copertura 100% significa che tutta la superficie è stata impattata almeno una volta dalle sfere.
Se si parla di copertura del 200%, si intende un trattamento con una durata doppia rispetto al tempo necessario, e così via.
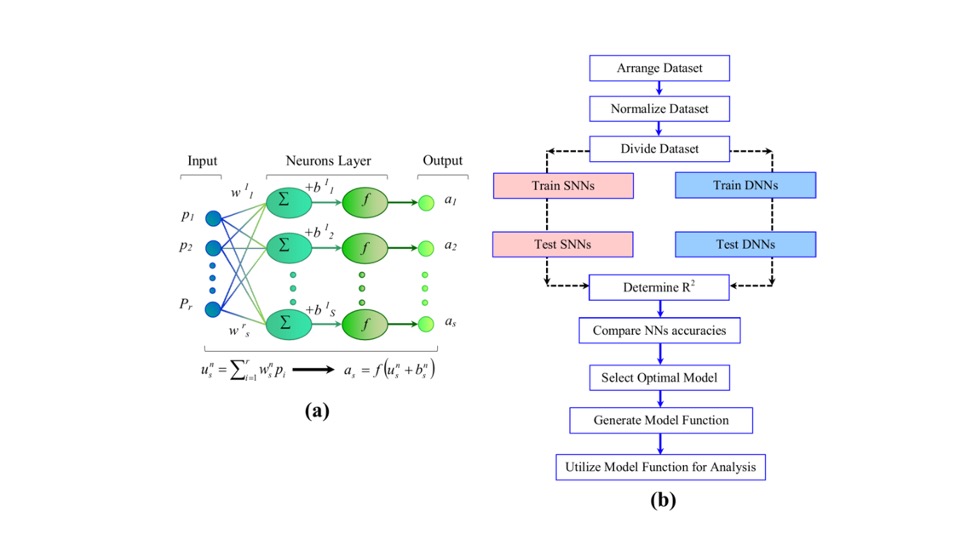
Mentre tradizionalmente, la scelta dei parametri di pallinatura è stata impostata prevalentemente in funzione delle tensioni residue, in anni più recenti si è cominciato a sperimentare trattamenti finalizzati a ottenere, oltre a un efficace campo di tensioni residue, una diminuzione delle dimensioni dei grani cristallini (grain refinement) fino a dimensioni di qualche decina di nanometri, in modo da incrementare anche le caratteristiche meccaniche degli strati superficiali del pezzo.
Ciò può essere ottenuto con intensità e coperture maggiori rispetto a quelle usuali per ottenere quella che viene chiamata pallinatura severa (severe shot peening, SSP).
La messa a punto del corretto trattamento in termini di tipo sfere, intensità e copertura dipende dal materiale e dalla geometria di interesse.
E’ possibile, infatti, incorrere nelle condizioni di over shot peening (OSP), che portano al danneggiamento del materiale e al peggioramento del suo comportamento a fatica.
L’ottimizzazione del trattamento in funzione della particolare applicazione per ottenere, o almeno avvicinarsi, al il miglior beneficio in termini di resistenza a fatica, è, quindi, complessa, in quanto coinvolge molteplici fattori tra loro interagenti con relazioni non sempre note se non qualitativamente.
Manca, in altre parole, un approccio analitico al problema e la ricerca di soluzioni ottimali richiede, quindi, una estesa sperimentazione, onerosa in termini di tempo e costi.
L’avvento e lo sviluppo delle tecniche di ottimizzazione basate sull’intelligenza artificiale e sul deep learning, possono dare un importante contributo alla soluzione del problema, contribuendo alla determinazione delle soluzioni ottimali da implementare sulla base algoritmi capaci di utilizzare i dati che derivano da esperienze precedenti riconoscendo relazioni che, altrimenti, non potrebbero essere evidenziate e, infine, proporre soluzioni in grado di migliorare l’odierno stato dell’arte.
Nel presente studio, gli effetti di diversi trattamenti di pallinatura con parametri che vanno da un trattamento tradizionale (SP) alla pallinatura severa (SSP) sono stati studiati in termini di microstruttura, proprietà meccaniche e comportamento a fatica assiale dell’acciaio inox AISI 316L.
Sono poi proposti un approccio a reti neurali per la modellazione della distribuzione di durezza, degli sforzi residui del loro rilassamento durante l’applicazione di carichi di fatica e, infine, il comportamento a fatica stesso del materiale in funzione del trattamento utilizzato.
Sulla base di questi approcci è stato possibile individuare i trattamenti più efficaci e il sottile confine che separa la pallinatura severa (SSP), che contribuisce positivamente alla resistenza a fatica, dall’over shot peening (OSP), che invece diminuisce le prestazioni in presenza di carichi ciclici.
Materiale, trattamenti e misure sperimentali
Lo studio considera l’acciaio AISI 316L. Quattro diversi trattamenti SP con identica intensità Almen di 21A e copertura di 100, 1500, 2500 e 3000% sono stati eseguiti sui campioni.
I pallini utilizzati sono in acciaio fuso con diametro medio e durezza rispettivamente di 0,58 mm e 50 HRC.
Osservazioni microstrutturali
Sono state eseguite osservazioni su campioni sezionati a livello microstrutturale sia con un microscopio ottico che con uno strumento FESEM Mira 3-XMU.
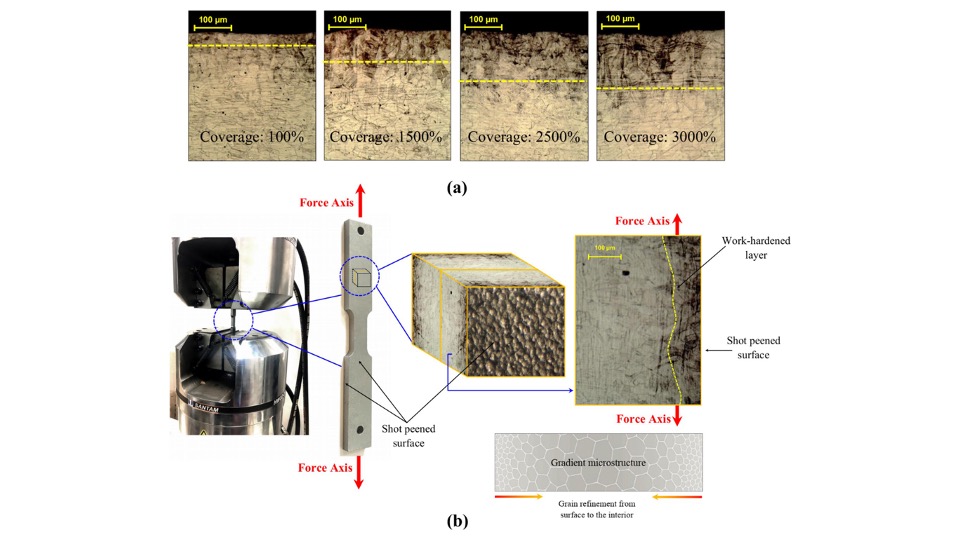
Analisi XRD hanno permesso la determinazione della dimensione dei grani cristallini dopo l’applicazione di trattamenti di pallinatura (diffrattometro a raggi X X’Pert PRO MPD (PANalytical), analizzatore X’Pert High Score Plus (V. 3) associato con MATLAB R2015b).
La diffrazione dei raggi X è anche il metodo utilizzato per la misura degli sforzi residui prima e dopo i trattamenti di pallinatura (diffrattometro XStress 3000).
Infine, sono state effettuate misurazioni della microdurezza Vickers dalla superficie fino a 650 μm di profondità utilizzando Qness GmbH Q30 e misure di rugosità.
In quest’ultimo caso, i campioni sono stati puliti con acetone e acqua distillata in un bagno ad ultrasuoni per 10 minuti per ogni passaggio e poi sono stati asciugati in aria calda.
La rugosità superficiale è stata misurata utilizzando SURFCORDER SE500.
I provini di fatica sono stati lavorati seguendo le indicazioni della norma ASTM E466 (fig. 1).
Il comportamento a fatica del materiale non trattato e dopo i trattamenti di pallinatura è stato investigato con prove assiali condotte a una frequenza di 30 Hz e cicli di fatica con rapporto di ciclo R=0,1.
Sono stati utilizzati 20 campioni per ottenere le curve S–N di ciascuna serie.
Le reti neurali
Ispirate dalle prestazioni del cervello umano, le reti neurali (NN) sono ampiamente utilizzate per comprendere problemi complessi e presentare soluzioni logiche mediante relazioni funzionali.
I sistemi basati sulle reti neurali possono essere impiegati per la modellazione e l’analisi di processi non lineari che dipendono da diversi parametri.
L’architettura schematica di un singolo strato NN alimentato con parametri di input p e di output a rispettivamente, con corrispondenti matrici di peso w, vettori di bias b, il combinatore lineare u e funzione di trasferimento f è illustrata in figura 2a.
La metodologia seguita in questo lavoro è illustrata in figura 2b.
Sono stati sviluppati diversi sistemi a reti neurali tramite un approccio “trail and error” poiché non esiste una formula esatta per ottenere reti neurali ad alte prestazioni.
Nel presente lavoro, l’80% dei dati raccolti sono stati presi in considerazione per l’allenamento e il restante 20% campioni sono stati considerati al fine di testare e valutare le strutture di rete sviluppate.
Risultati
Risultati sperimentali
Le osservazioni al microscopio ottico dei campioni pallinati, con fattore di ingrandimento pari a 300, sono mostrate in figura 3a.
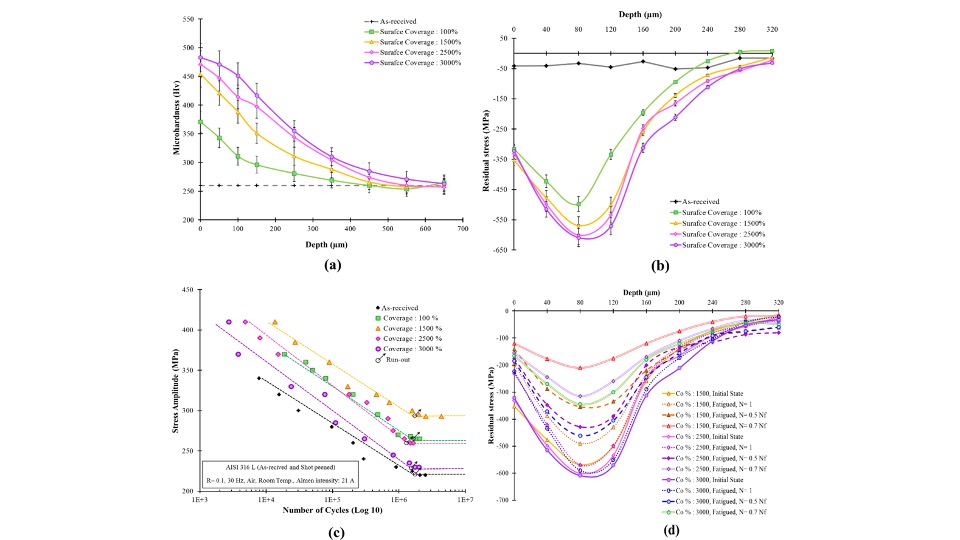
Tale figura rivela il raffinamento delle dimensioni dei grani nello strato superficiale dei materiali trattati e una struttura a gradiente scendendo in profondità. La Figura 3b, invece, mostra l’illustrazione schematica di uno scatto di un provino pallinato durante una prova di fatica assiale.
Per ottenere la dimensione dei cristalliti (dopo l’applicazione di trattamenti con coperture di 1500, 2500 e 3000%, tali da causare una deformazione plastica severa) sulla superficie dei campioni trattati, sono state eseguite ed elaborate analisi diffrattometriche, le quali hanno evidenziato dimensioni dei cristalliti di circa 20nm per coperture superiori a 1500%.
In figura 4 si illustrano, invece i risultati delle misure di durezza, degli sforzi residui (prima e durante le prove di fatica) e le curve di fatica S-N dei diversi trattamenti.
È possibile osservare che, mentre la durezza mostra un andamento sempre crescente all’aumentare della copertura, gli sforzi residui tendono a stabilizzarsi per valori superiori a 2000%.
Le curve di fatica evidenziano che la massima resistenza è ottenuta utilizzando una copertura di 1500%, al di sopra della quale la resistenza e il limite di fatica decrescono per l’effetto di overpeening.
Salendo a 3000%, la curva si avvicina a quella del materiale non trattato, evidenziando, quindi, l’annullamento dei benefici legati alla pallinatura.
Risultati della modellazione con reti neurali
Per ottenere la struttura di NN con le massime prestazioni e per confrontare l’efficienza di SNN, DNN e SADNN sono state sviluppate varie reti con diversa architettura e differenti parametri di rete per ogni modellazione A, B e C.
In tutti i modelli logaritmici sono state utilizzate le funzioni di trasferimento sigmoid (logsig) negli strati “hidden” e “output”, ottenendo un tasso di allenamento di 0.195.
A valle dell’analisi critica delle modellazioni sviluppate e della loro validazione, sono state eseguite le analisi parametriche delle risposte del materiale al variare della copertura.
In particolare, si è studiato l’effetto del valore della copertura sulla durata e sulla resistenza a fatica.
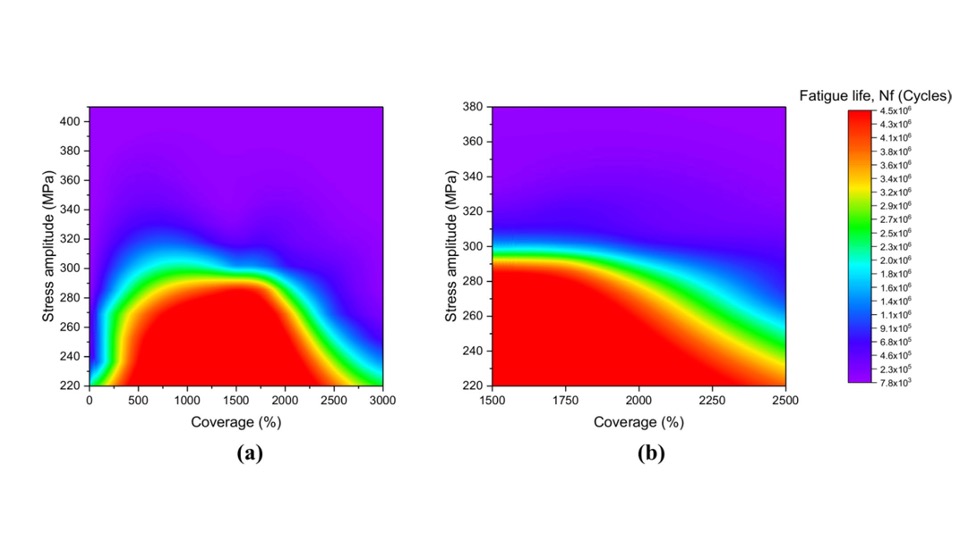
Questi risultati sono esposti in forma schematica nella figura 5, in cui si vede come l’influenza della copertura abbia un andamento piatto per coperture tra 1000% e 1800% per poi diminuire per valori superiori.
Considerando 4,5 milioni di cicli come durata di run-out è possibile osservare la presenza di un massimo per una copertura di 1750%, che può essere considerato il valore ottimale di copertura per il caso di interesse.
L’approccio sviluppato permette, quindi, di ottimizzare il trattamento di pallinatura, permettendo di orientare la scelta dei parametri verso i trattamenti più performanti e, allo stesso tempo, evitando di incorrere nell’over shot peening, condizione caratterizzata da eccessive coperture/intensità e da un danneggiamento superficiale che facilità l’innesco di cricche superficiali, di fatto riducendo o annullando il beneficio legato alle tensioni residue.
Conclusioni
In questo contributo è stato studiato l’effetto di diversi trattamenti di pallinatura a pari intensità e copertura variabile tra 100% e 3000%.
Gli effetti dei trattamenti sono stati studiati attraverso diversi esperimenti, tra cui la caratterizzazione microstrutturale, le misure di microdurezza, la rugosità superficiale e gli sforzi residui, nonché prove di fatica assiale.
I dati sperimentali ottenuti utilizzati per lo sviluppo lì diverse reti neurali, utilizzando un approccio di deep learning.
Il coefficiente di correlazione è il parametro utilizzato per valutare l’accuratezza delle prestazioni delle reti.
I risultati ottenuti per la valutazione delle reti hanno indicato che si può raggiungere una precisione superiore al 0,99 sia nel processo di training sia nella fase di test per tutti i modelli costruiti.
Inoltre, al fine di valutare l’autenticità dei risultati ottenuti dalle reti neurali e anche per ottimizzare il processo SP e trovare il confine tra SSP e OSP, ulteriori validazioni sperimentali hanno permesso di validare tali conclusioni.
Questi risultati rivelano che l’approccio deep learning può essere utilizzato come un metodo alternativo per aprire il percorso per la modellazione dei fenomeni complessi e non lineari come quello qui descritto, utilizzando solo un piccolo set di dati.