L’accumulatore fa parte dei “componenti accessori” del sistema oleodinamico, che sono divisi in due gruppi: quelli dedicati alla regolazione del regime di flusso e quelli dedicati al collegamento delle varie parti del circuito. I primi sono gli accumulatori, gli scambiatori, i serbatoi e i filtri: i secondi sono i tubi rigidi e flessibili, la raccorderia e le guarnizioni.
Gli accumulatori si trovano installati su tutti i circuiti idraulici in cui operano fluidi incomprimibili soggetti a variazioni di pressione. Rimanendo nel campo più diffuso dell’oleodinamica, a titolo esemplificativo e non esaustivo, è noto il fenomeno delle brusche variazioni di pressione, che possono essere normalmente indotte dall’azionamento di valvole, da variazioni di carico, dall’arrivo a fine corsa degli attuatori e, non trascurabile, da sovrasollecitazioni dovute al comportamento degli operatori, errori compresi. Essendo l’olio incomprimibile, questi repentini incrementi di pressione determinano quello che in idraulica prende il nome di “colpo di ariete”. L’energia in eccesso impatta su tutto il circuito, causando danni oppure usura precoce.
La funzione fondamentale degli accumulatori è proprio quella di mantenere il più possibile regolare nel tempo l’andamento dei valori di pressione e di portata dell’olio che circola nel sistema oleodinamico, rendendone “fluide” e senza picchi le variazioni: per questo motivo spesso sono detti anche “smorzatori”.
Fisicamente questo compito viene svolto da un fluido comprimibile (gas), tenuto separato dall’olio e in grado di comprimersi e di espandersi in funzione e sincronia con le fluttuazioni di pressione dell’olio stesso.
Accumulatori a membrana e a sacca
Sono i più diffusi sugli impianti oleodinamici: l’olio entra dalla parte inferiore andando a ridurre il volume a disposizione del gas, che viene a sua volta compresso e può restituire il volume d’olio accumulato in caso di calo di pressione. Il punto di installazione ottimale è il più possibile vicino agli attuatori che generano le perturbazioni da controllare.
Tra l’accumulatore e il punto del circuito in cui questo è installato (molto frequentemente sulle centraline) è interposto il blocco di sicurezza, costituito dal manometro, dalla valvola di sicurezza e dalla valvola di esclusione, che permette la manutenzione dell’elemento con impatto minimo o nullo sui tempi di interferenza col funzionamento, a partire dal controllo della pressione di carica gas fino alla sostituzione preventiva o alla riparazione di un guasto dell’elemento stesso. I due tipi di accumulatori sono abbastanza simili, somigliando a una piccola bombola ed essendo accomunati dal fatto che olio e gas compresso sono separati da un elemento in elastomero.
Hanno caratteristiche diverse: quello a membrana infatti è costituito da due metà, saldate di testa dopo il fissaggio della membrana oppure filettate. Quello a sacca è monolitico, senza saldature. Il materiale di costruzione più comune per l’involucro è l’acciaio al carbonio, ma sono normalmente presenti accumulatori in acciaio inox, tecnopolimeri e altri materiali ancora. Anche per sacca e membrana la varietà di elastomeri disponibili è molto ampia, in quanto le condizioni di esercizio sono tra le più diverse.
L’accumulatore a membrana saldato, in caso di rottura della medesima, non è riparabile, mentre quello filettato lo è. L’accumulatore a sacca è sempre riparabile, in quanto la sacca è inserita (con opportune procedure) dalla parte superiore.
La membrana oscilla secondo un movimento indotto dal sistema di fissaggio sul mantello, ma senza, o quasi, deformazioni elastiche, mentre la sacca si espande e si contrae come un palloncino. Infine nella versione a membrana l’otturatore è fissato alla medesima, mentre nella versione a sacca esso è costituito da una valvola a fungo con molla di apertura.
Accumulatori a pistone
In questo caso la variazione controllata di volume è affidata allo scorrimento di un pistone flottante, che funge anche da elemento di separazione tra l’olio e l’azoto. Il principio di funzionamento non cambia. La testa del pistone lato olio (piana o opportunamente sagomata) funge anche da otturatore.
Gli accumulatori a pistone sono utilizzati per impieghi mediamente più gravosi degli altri e richiedono una lavorazione accurata della camicia di scorrimento; pertanto si usano di norma acciaio al carbonio, acciaio inox e alluminio. Limitatamente alla famiglia degli accumulatori a pistone, lo sforzo antagonista che permette di mantenere l’olio in pressione, anziché da un gas, può anche essere esercitato da dispositivi meccanici, quali molle, dispositivi meccanici proporzionali o anche da un carico costante.
In questo ultimo caso l’assorbimento delle variazioni di portata avviene senza variazioni di pressione. Il contrasto meccanico serve anche spesso per ricavare un segnale di posizione del pistone, utilizzabile per scopi diversi.
Volendo abbinare il controllo di posizione alla funzione principale di accumulatore, la tendenza dominante è quella di dotare il pistone flottante classico di appositi sistemi di controllo senza un contatto diretto, con contrasto a gas in pressione: affidabilità, precisione, compattezza e facilità di regolazione ne traggono indiscutibili vantaggi. Ciò si ottiene grazie all’uso di sensori (trasduttori magnetici, capacitivi…) che dialogano con centraline esterne.
Le modalità e la frequenza di intervento dell’accumulatore risultano monitorabili in continuo, consentendo un controllo in tempo reale della funzionalità dell’accumulatore da parte del servizio manutenzione e di eventuali scostamenti dal range prefissato.
La possibilità di connessione a sistemi di telecontrollo completa il quadro delle potenzialità di diagnostica precoce e remota. Inoltre un apparecchio di questo tipo può essere utilizzato anche in operatività, per le funzioni di commutazione al raggiungimento di determinate posizioni del pistone flottante, posizioni strettamente correlate al raggiungimento di valori “sensibili” di pressione nel circuito.
Come fare la manutenzione degli accumulatori oleodinamici
La buona prassi per la cura degli accumulatori oleodinamici riguarda l’esecuzione di un piano di manutenzione ordinaria, che preveda principalmente il semplice controllo periodico della precarica, cioè del contenuto energetico dell’accumulatore. Infatti un valore errato di questo valore pesa in modo sensibile sull’efficienza dell’impianto oleodinamico e in particolare sull’integrità di questo componente oleodinamico.
La manutenzione ciclica prevede anche la sostituzione delle parti ad usura (sacca o membrana, guarnizioni), di cui sono generalmente note le durate di vita utile. Chiaramente queste attività sono svolte in ottica preventiva, quindi con l’obiettivo di evitarne il guasto. La pressione di precarica dipende principalmente dalla temperatura di esercizio e dalla tipologia del ciclo macchina.
I controlli sono effettuati mediante dispositivi di controllo della precarica, a regime in genere con una frequenza di controllo annuale, anche se le condizioni operative possono indirizzare verso tempistiche differenti. Naturalmente è possibile correggere il valore di precarica, se differente a quello previsto, utilizzando bombole di azoto e accessori flessibili di collegamento.
Strumenti di monitoraggio
Come già detto, il parametro pressione di precarica è l’indicatore fondamentale, per cui è consigliabile dotare gli accumulatori di dispositivi fissi di monitoraggio. Il dispositivo che assolve a questo scopo è un sensore posizionato sulla valvola gas lato olio degli accumulatori, che consente di misurarne la pressione: ne esistono di vari tipi, laser, magnetostrittivi, ad ultrasuoni, utilizzabili a seconda delle esigenze dell’utilizzatore.
Invece il sensore per il controllo della integrità della sacca, montato al suo interno, rileva eventuale presenza di liquido: infatti, normalmente nel dispositivo è presente solo il gas di caricamento ma, se si rompe l’elemento separatore, il liquido entra nel circuito e ne pregiudica il corretto funzionamento.
Accumulatori e normative
Gli obblighi per gli utilizzatori fanno riferimento al Testo Unico sulla Sicurezza del Lavoro (D. Lgs. 81/2008) e alle pubblicazioni INAIL, ma esiste anche una specifica norma di riferimento relativa alla messa in servizio, uso e manutenzione dei dispositivi in pressione: si tratta della UNI 11325, “Attrezzature a pressione e Messa in servizio ed utilizzazione delle attrezzature e degli insiemi a pressione“, nella parte che si riferisce alla verifiche periodiche delle attrezzature e degli insiemi a pressione.
Gli accumulatori sono considerati “attrezzature di lavoro” ai sensi del testo unico sulla sicurezza, esattamente come una macchina operatrice, per cui sono oggetto di verifiche periodiche di funzionalità e sicurezza: sono esclusi i recipienti in pressione minore di 25 litri.
Verifiche periodiche di funzionalità e sicurezza
Durante il ciclo di vita di un accumulatore sopra i 25 litri, sono previste le verifiche di funzionamento e di integrità:
1. Verifica di funzionamento: frequenza triennale documentale (documentazione di impianto), dei parametri operativi e funzionalità accessori di sicurezza istallati.
2. Verifica integrità decennale: stato di conservazione, controllo della documentazione di impianto, esame visivo esterno e interno (endoscopio), controllo spessimetrico, eventuale prova di pressione.
La prima verifica viene eseguita dall’INAIL, le successive sono svolte da un soggetto preposto, autorizzato dal Ministero del Lavoro, quindi da uno studio tecnico oppure da un libero professionista abilitato.
In caso di riparazione della sacca o delle guarnizioni di un accumulatore, l’utilizzatore può sostituire con un ricambio equivalente. In caso di modifica l’utilizzatore deve informare il soggetto preposto, che provvederà alle verifiche.
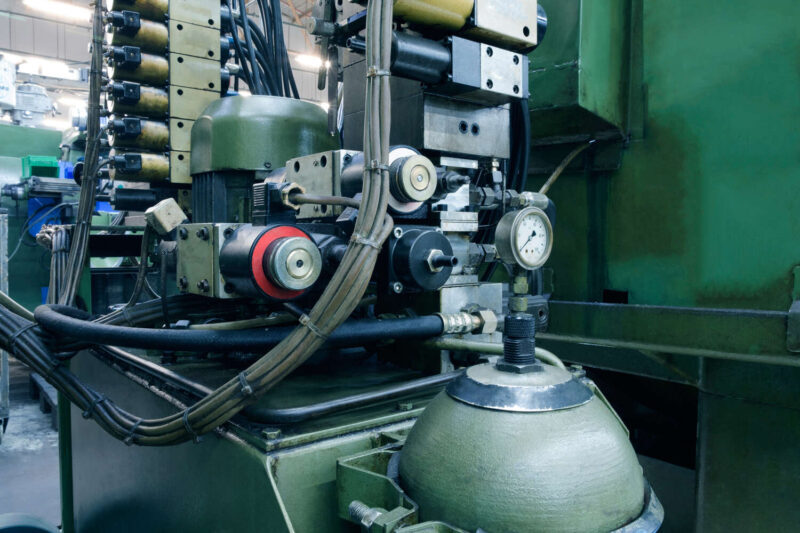
Alcuni suggerimenti e considerazioni
1. Perché la pressione varia il giorno successivo alla precarica? Quando si fa una carica del gas se ne aumenta la pressione, che comporta anche un aumento della temperatura: il giorno successivo la temperatura si abbassa e di conseguenza la pressione, che quindi dovrà essere controllata ed eventualmente corretta.
2. Uso dell’azoto: si tratta di un gas particolarmente valido, in quanto inerte, quindi antiesplosione, atossico, di costo basso, facilmente reperibile e trasportabile.
3. L’inserimento di una valvola di sicurezza su un accumulatore è una valida manutenzione migliorativa, ma non è una modifica del sistema, in quanto non varia le caratteristiche funzionali, ma ne aumenta efficienza e sicurezza.
4. Nel caso di impiego di un disco di rottura, è interessante sottolineare che, come indicato nella norma UNI 11325, per un sistema di sicurezza a frattura prestabilita, non è prevista la verifica di funzionalità, in quanto non realizzabile senza metterlo fuori uso: è necessario pertanto avere la documentazione del costruttore e verificarne il controllo, attraverso una semplice visione del suo stato generale di conservazione e integrità.