Gli ingranaggi bimetallici mostrano prestazioni promettenti e consentono di ottenere riduzioni di peso fino al 40%, rispetto agli ingranaggi tradizionali in acciaio.
Ad oggi, nel settore automobilistico, uno dei metodi più testati ed efficaci per ridurre le emissioni, indipendentemente dal tipo di propulsore, è la riduzione della massa del veicolo.
Gran parte dei progetti di ricerca si sono concentrati sulla riduzione del peso di componenti tradizionali del veicolo, sostituendo materiali tradizionali con soluzioni innovative più leggere e sviluppando nuovi design e geometrie.
Range Rover ne è l’esempio: modelli recenti come la “Sport”, grazie al nuovo telaio in alluminio, permettono una riduzione di peso del 40%, pari a 400 kg, a favore di consumi e agilità su strada.
È dimostrato, quindi, come la massa complessiva del veicolo sia il parametro di progettazione più critico per le valutazioni di efficienza.
Un impatto significativo considerando che una diminuzione di circa il 10% del peso del veicolo migliora l’efficienza nei consumi dal 6 all’8%.
Sebbene alleggerire componenti non strutturali risulti la via più semplice e praticata, basti pensare all’alluminio in sostituzione di ghisa e acciaio per i blocchi motore, col passare del tempo, il potenziale di alleggerimento di strutture semplici si sta esaurendo, occorre pertanto in prima battuta procedere con l’alleggerimento di componenti strutturali per poi focalizzarsi su componenti meccanici ad elevate prestazioni come alberi a gomiti, alberi a camme, cuscinetti e ingranaggi.
Tali componenti sono spesso realizzati con leghe d’acciaio ad elevata resistenza a causa di esigenti requisiti prestazionali ed elevate sollecitazioni.
Alleggerire componenti meccanici fornisce diversi vantaggi: riduzione della massa rotante e dell’inerzia rotazionale nella catena cinematica cui corrisponde un miglioramento delle prestazioni e una riduzione nei consumi superiore rispetto alla semplice riduzione del peso complessivo del veicolo.
Ulteriori vantaggi includono minore usura e ridotta rumorosità durante il funzionamento.
Tali benefici, unitamente alla rapida espansione del mercato degli ingranaggi, che vede una crescita annua pari al 5,6% (sino a 285 miliardi di dollari nel 2024) guidata dall’aumento della domanda di trasmissioni automobilistiche complesse a 7 e 8 velocità, mostrano il potenziale economico della ricerca di soluzioni alleggerite, in particolar modo in quei veicoli in cui il powertrain incide significativamente sul peso complessivo.
L’utilizzo di materiali leggeri nelle zone con stress ridotto di un ingranaggio favorisce un notevole aumento del rapporto resistenza-peso, reso possibile anche dal fatto che le sollecitazioni, in condizioni operative standard, sono molto maggiori nella dentatura piuttosto che nella cartella della ruota.
A tal proposito, la figura 1 mostra un ingranaggio multi-metallo in cui l’anello esterno in acciaio comprende la zona della dentatura, maggiormente sollecitata, mentre l’anello interno viene usato per il fissaggio all’albero, per esempio mediante linguetta
Il resto del volume è ottenuto in lega di alluminio.
Tuttavia, come illustra la figura 2, un problema diffuso nella fabbricazione di ingranaggi bimetallici alleggeriti ottenuti mediante forgiatura è legato alla interfaccia fra i materiali, legata alla necessità di ottenere un legame sufficientemente robusto tra la dentatura in acciaio e il corpo in alluminio.
Vanno quindi condotte una serie di indagini su diversi aspetti della forgiatura al fine comprenderne in modo più approfondito la tecnologia, superarne i limiti e consentirne l’utilizzo ottimale nella pratica, come si descrive nel seguito.
Tecnologie per la produzione di ingranaggi alleggeriti
Come noto, gli ingranaggi trasmettono il moto rotazionale attraverso le dentature e sono comunemente fabbricati con un unico materiale, la cui scelta dipende dall’applicazione.
Tuttavia, la scelta di soluzioni multi-materiale consente una riduzione di costi e masse, mantenendo elevate prestazioni e qualit
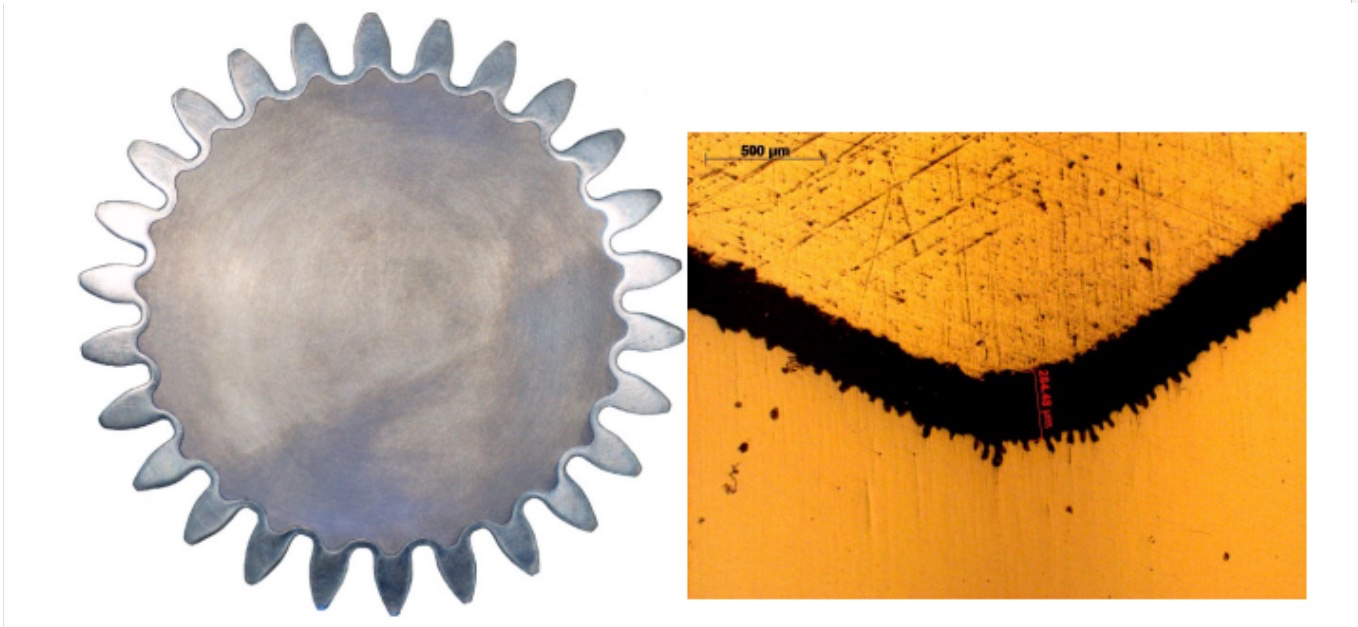
Tra i materiali più utilizzati ci sono le leghe metalliche ad elevata resistenza e i polimeri.
Le prime forniscono elevata resistenza statica, a fatica e a usura, tanto da risultare ottimali per applicazioni più impegnative. I secondi sono invece limitati ad applicazioni a bassa potenza o che richiedono la minimizzazione di costi, rumore e resistenza alla corrosione.
Le tecniche per la produzione di ingranaggi sono molteplici. Come noto, ogni processo influenza le proprietà, le prestazioni e la qualità dell’ingranaggio.
Ingranaggi polimerici sono comunemente stampati a iniezione mentre quelli metallici possono essere prodotti mediante un’ampia varietà di processi, come la fusione, la formatura e la lavorazione per asportazione di materiale.
Tipicamente si tende a distinguere tra processi di taglio e di formatura.
In tempi recenti si fa riferimento alla forgiatura di precisione, in particolare alla forgiatura “flashless”. Un processo tradizionale di forgiatura produce materiale in eccesso detto flash.
Siccome i costi del materiale incidono notevolmente sui costi di produzione (si pensi a un albero a gomiti in cui il flash rappresenta circa il 55% del totale), miglioramenti in processi e tecnologie di progettazione e produzione consentono risparmi significativi di materiale, tempo ed energia.
Altri vantaggi della forgiatura, rispetto al taglio, riguardano maggiore resistenza a fatica, minore impiego di materiale e migliore finitura superficiale.
In tabella 1 sono confrontate le diverse tecnologie di produzione di ingranaggi alleggeriti multi-materiale. Approcci più semplici prevedono la sostituzione di materiali o interventi in fase di progettazione e/o nel processo di produzione.
Come anticipato, la forgiatura si dimostra una valida alternativa, preferibile per il basso costo al pezzo e l’elevata resistenza a fatica.
Basso costo derivante in parte dall’elevato tasso di produttività delle attrezzature di forgiatura (si consideri una media di 600 parti/ora), prestazioni estremamente efficienti se confrontate con la lavorazione dei denti mediante processi di taglio.
L’elevata resistenza, invece, si ha grazie al flusso di materiale nel processo di forgiatura, che produce una disposizione e orientazione favorevole dei grani.
Alcuni studi hanno dimostrato come gli ingranaggi forgiati abbiano una resistenza a fatica significativamente superiore rispetto a quelli soggetti a lavorazioni meccaniche (da due a dieci volte superiore).
Forgiatura bimetallica
Numerosi sono i processi di lavorazione che coinvolgono la forgiatura bimetallica di ingranaggi.
In letteratura, la maggior parte degli studi prevede l’utilizzo di una pressa tradizionale, con differenze nella produzione di materiali dissimili e nei metodi di riscaldamento, per ovviare il problema legato alle diverse proprietà termiche dei metalli.
Una panoramica del processo è raffigurata in figura 3.
Il processo prevede l’impiego di preforme, una per strato di materiale impiegato e quindi con caratteristiche di temperatura di formatura ottimale differenti.
Nell’esempio, l’ingranaggio è costituito da tre strati: un anello esterno, un nucleo e un anello interno. Ulteriori strati possono essere aggiunti se necessario.
Le preforme sono collocate all’interno dei rispettivi forni preriscaldati per il raggiungimento della temperatura di formatura ottimale.
Se necessario, è possibile applicare del lubrificante ai materiali o agli utensili per la forgiatura.
Mentre i materiali vengono riscaldati, anche componenti e utensili, come lo stampo e il punzone, possono esserlo.
Appena prima della forgiatura, la preforma di materiale più esterno viene rimossa dal forno e posizionata all’interno dello stampo.
A seguire si inserisce in quest’ultima il nucleo e, al suo interno, l’anello interno. Il processo si ripete in tal modo sino al completamento di tutti gli strati.
Al termine, una pressa esegue l’operazione di forgiatura e si ottiene l’ingranaggio. Utilizzando una lega di alluminio combinata all’acciaio, si può ottenere così una significativa riduzione di massa, sino al 50%.
Processi di lavorazione nella forgiatura di ingranaggi multi-metallo
Numerosi i processi di lavorazione nella forgiatura di ingranaggi multi-metallo, la tabella 2 ne mostra i principali.
Obiettivo comune: superare la sfida legata alle proprietà termiche di ciascun metallo.
Giunzioni fra materiali dissimili
Una delle più grandi sfide per l’integrità strutturale di un componente multi-metallo è la giunzione tra materiali dissimili.
Nel caso degli ingranaggi bimetallici, il legame tra i due metalli dissimili si può formare sia durante il processo di produzione delle preforme sia post-forgiatura.
In letteratura, i giunti tra due materiali ottenuti per formatura (fig. 4) possono essere raggruppati in tre categorie: giunti a flusso impedito (vincolo macro-meccanico); giunti a resistenza per attrito (vincolo micro-meccanico) e giunti metallurgici.
Nel primo caso (a), il flusso relativo di materiale tra due componenti è impedito.
Nel secondo (b), uno stress residuo o altra forza provoca attrito tra le parti, resistendo al loro movimento.
Infine, un giunto metallurgico (c) consiste in un’interfaccia saldata a freddo o per diffusione, dove le parti sono unite a livello atomico.
Se da un lato la giunzione meccanica per deformazione plastica tra materiali dissimili è procedura consolidata in ambito industriale, relativamente facile grazie alla scelta di design appropriati e coerenti parametri di lavorazione, con conseguenti benefici sia nelle prestazioni che nella riduzione di peso dei componenti coinvolti nonché nelle relative applicazioni o aggregati, dall’altro la sfida più grande riguarda, invece, la formazione di un legame metallurgico completo.
Legami metallurgici nella forgiatura a caldo
La creazione di legami metallurgici durante il processo di forgiatura a caldo rappresenta una tipologia di saldatura allo stato solido, comunemente conosciuta come “saldatura a caldo”.
La saldatura a caldo tra metalli, simili e dissimili, è in uso da migliaia di anni, basti pensare al ferro e all’acciaio.
Il processo tradizionale prevede l’aumento di rugosità e la pulizia delle superfici di accoppiamento, il riscaldamento della regione di accoppiamento al 50-90% del punto di fusione del materiale, l’applicazione di un flusso di polvere per la rimozione degli strati di ossido e il mantenimento della superficie pulita, seguita da riscaldamento continuo, sovrapposizione delle superfici di accoppiamento e formatura.
Quando due superfici entrano in contatto, la rugosità microscopica superficiale determina una unione in corrispondenza delle asperità, con significativa deformazione plastica, con conseguente deformazione delle asperità stesse e aumento della superficie di contatto effettiva.
Tali processi possono generare un legame atomico allo stato solido tra i metalli posti a contatto.
A livelli significativi di deformazione plastica (cioè espansione delle superfici di accoppiamento), l’adesione è iniziata e il legame è stabilito.
A temperature di formazione più elevate e con tempistiche più lunghe, la diffusione diventa un meccanismo di saldatura sempre più significativo, riscontrabile in cambiamenti nella microstruttura metallica.
Il meccanismo di unione nella saldatura allo stato solido è la combinazione tra adesione e teoria della diffusione.
Adesione
L’adesione è l’unione dovuta alla forza esercitata tra le molecole di due materiali diversi posti a contatto.
In particolare, l’adesione è intesa come attaccamento tramite interazione chimica (adesione chimica) e forze intermolecolari (adesione per dispersione).
La prima si verifica quando le superfici di accoppiamento dei materiali interagiscono chimicamente tramite legame covalente, ionico o metallico.
L’adesione per dispersione consiste, invece, in legami idrogeno e legami di van der Waals come risultato di forze intermolecolari (forze di attrazione secondaria).
Tali forze, più deboli rispetto a quelle dell’adesione chimica per la mancanza di scambio di elettroni, interagiscono su distanze significativamente maggiori.
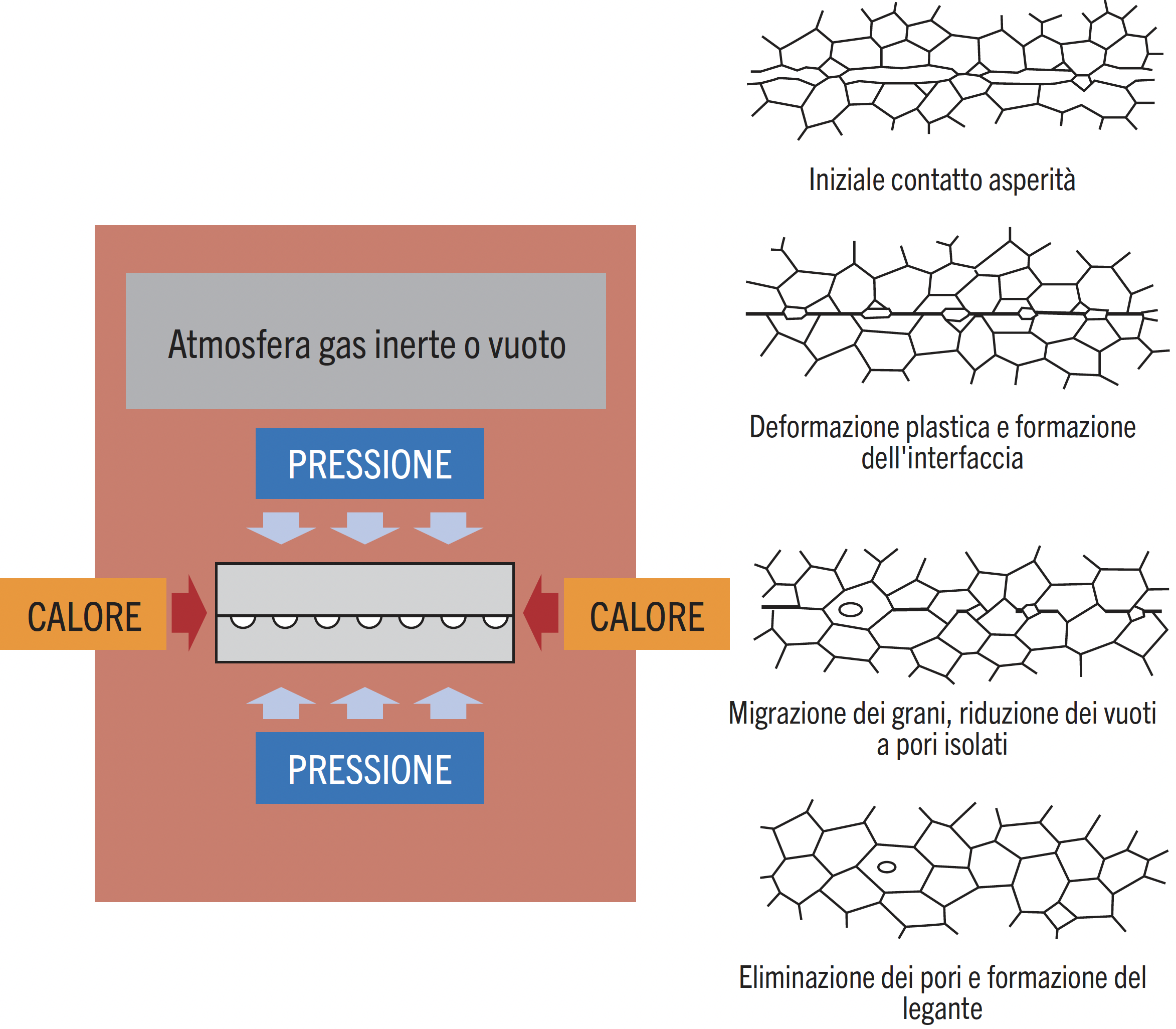
Tra i legami classificati sotto l’adesione dispersiva, il legame idrogeno risulta il più forte, seguito dai vari legami di van der Waals.
In metalli sfusi, in mancanza di composti contenenti idrogeno, il legame ha scarso se non alcun effetto.
Altri parametri che influenzano l’adesione sono, oltre a tipo di materiali e condizioni dell’interfaccia, la temperatura, la struttura cristallina di ciascun metallo (la struttura cubica dell’alluminio la favorisce), la solubilità reciproca (con scarsa adesione per metalli insolubili) ecc.
Il processo per la formazione del legame di diffusione
Il legame a diffusione è un metodo di adesione che si realizza con la formazione di legami a livello atomico, risultato del processo in figura 5.
Riscaldamento dei metalli e applicazione di pressione consentono di produrre un pezzo perfettamente incollato.
A livello microscopico:
- Deformazione delle micro-asperità: difetti superficiali molto piccoli (asperità sulle due superfici) entrando a contatto si deformano plasticamente, formando interfacce tra le superfici stesse.
- Trasporto della massa controllato dalla diffusione: temperatura e pressione elevate provocano uno scorrimento accelerato nei materiali; i grani e la materia prima migrano e gli spazi tra le due superfici si riducono a pori isolati.
- Migrazione delle particelle metalliche attraverso l’interfaccia: il materiale inizia a diffondersi attraverso il confine delle superfici adiacenti dei due materiali, con la ricristallizzazione i pori vengono eliminati e si crea un legame.
I principali parametri di diffusione sono la temperatura, la pressione e il tempo di mantenimento del legame. La loro identificazione e controllo durante il processo di forgiatura può favorire un legame di diffusione ottimale.
Inoltre, qualsiasi materiale interposto tra superfici metalliche può impedire un’adeguata diffusione è necessaria quindi in prima battuta la lavorazione delle superfici al fine di rimuovere il più possibile agenti contaminanti o altre inclusioni.
Principali ostacoli alla giunzione fra metalli dissimili
La figura 6 mostra come una superficie apparentemente pulita possa contenere elevate quantità di contaminanti (grasso, acqua, vapore acqueo) e strati di passivazione (ossidi), impedendo il contatto dei materiali a livello atomico, una barriera per la formazione di un legame di diffusione di qualità.
Sebbene strati di grasso e vapori possono essere facilmente rimossi con benzina o solventi (cosiddetta sgrassatura), uno strato di sostanze organiche di spessore compreso tra 1 e 5 μm può comunque rimanere.
Allo stesso modo, anche il trattamento con solventi rilascia un film di grasso con spessore compreso tra le 10 e le 100 molecole.
Strati di ossido invece risultano assai più complessi da rimuovere.
Velocità e la profondità di ossidazione dipendono da tempo e temperatura.
L’impatto dell’ossidazione sull’adesione e sul legame di diffusione è specifico del materiale: nel caso del ferro, una quantità estremamente ridotta di ossido determina una significativa perdita di adesione, per il rame è necessario invece molto più ossigeno.
Un ulteriore fattore che influenza la forza del legame è la formazione di composti intermetallici, riscontrata ad esempio nel processo di incollaggio di leghe di acciaio e alluminio.
Migliorare i legami metallurgici nella forgiatura di più metalli
La formazione di forti legami intermetallici, come detto, è favorita da temperatura, pressione, scorrimento del materiale e massimizzazione del tempo di contatto, variabile, quest’ultima, assai complessa da gestire nell’industria, dove si tendono a minimizzare i tempi di produzione.
A temperature elevate l’adesione è favorita dall’aumento di energia superficiale che consente l’accelerata diffusione di elettroni e atomi.
Anche la duttilità del materiale aumenta, promuovendo così la rottura degli strati di passivazione.
In generale, un aumento della pressione migliora la saldatura, limitatamente a pressioni pari al doppio dello sforzo di flusso dei materiali uniti.
Grandi deformazioni, invece, si sono dimostrate vantaggiose per una serie di processi di saldatura allo stato solido, come quella a pressione a freddo.
Ciò è dovuto all’ampio scivolamento superficiale che interrompe gli strati di ossido/passivazione prima della saldatura statica. Alcuni studi dimostrano come, per rompere gli strati di ossido, sia necessaria una deformazione plastica di circa il 40%.
In tabella 3 sono illustrate le principali soluzioni per ottimizzare il legame multi-metallo.
Conclusioni e scenari futuri
Gli ingranaggi bimetallici mostrano prestazioni promettenti, con riferimento agli ingranaggi tradizionali in acciaio si ottengono riduzioni di peso fino al 40%, riduzione di rigidezza compresa tra il 9 e il 38 % e aumento di sollecitazioni limitate tra il 4 e il 20%.
Pertanto, è dimostrato il sostanziale risparmio di peso con impatto accettabile sulle prestazioni meccaniche.
La forgiatura bi-metallica sembra essere un candidato eccellente per l’adesione tra metalli; tuttavia è un processo assai impegnativo.
Per la produzione di un singolo pezzo multi-metallo, è infatti necessaria una lavorazione significativa pre-forgiatura, cruciale per il successo della stessa e l’ottimizzazione dell’integrità dell’ingranaggio in cui la più grande sfida è rappresentata dalla forza del legame metallurgico.
Sebbene la letteratura si sia spesso concentrata su coppie di materiali e geometrie uniche, rendendo quindi difficile confrontare direttamente tutti i metodi con valori di riferimento comuni, è comunque possibile trarre lezioni preziose sulla progettazione del pezzo, il riscaldamento, la forgiatura e il rafforzamento del legame.
La compatibilità dei materiali è cruciale per minimizzare l’impatto della corrosione galvanica e promuovere l’incollaggio, materiali interstrato sono raccomandati per limitare eventuali ulteriori effetti avversi.
Tuttavia, la selezione di qualsiasi metodo, o combinazione di metodi, per produrre un ingranaggio forgiato multi-metallo dipende dalla geometria e dal materiale e quindi, la presenza di vincoli dimostra l’assenza di un unico percorso di lavorazione ottimale.
Ci si aspetta che, nel prossimo futuro, sistemi esperti ottimizzino il processo di forgiatura di ingranaggi alleggeriti multi-metallo: tecnici specializzati potranno così caricare geometrie e requisiti di ciascun materiale e, dal confronto con casi studio memorizzati in database, ottenere soluzioni adeguate al percorso di lavorazione più efficiente.
Riferimenti
- Politis, D.J., Politis, N.J. & Lin, J. Review of recent developments in manufacturing lightweight multi-metal gears. Prod. Eng. Res. Devel. 15, 235–262 (2021). https://doi.org/10.1007/s11740-020-01011-5.
- Nicholas Politis. Forging Lightweight Bi-metal Gears. A Thesis submitted to Imperial College London For the Degree of Doctor of Philosophy. Mechanics of Materials Division Department of Mechanical Engineering Imperial College London, 2017.
di Giorgio De Pasquale, Dipartimento di Ingegneria Meccanica e Aerospaziale, Politecnico di Torino, Smart Structures and Systems Lab, Elena Perotti, Senior data analyst.