I processi di fabbricazione additiva (AM) rappresentano una soluzione innovativa a costi contenuti per la produzione di ruote dentate alleggerite (ingranaggi ibridi).
Le ruote dentate, in gergo “ingranaggi”, sono i componenti più utilizzati, essenziali per la trasmissione di potenza in ogni settore della meccanica, da quelli tradizionali dell’automotive e dell’aerospazio, ad altri di più recente innovazione tecnologica come quello agricolo, dell’industria marina, delle centrali elettriche, dei generatori eolici e dell’industria mineraria.
Data l’ampia gamma di applicazioni coinvolte, in commercio sono disponibili diverse tipologie di ruote dentate. Rispetto al passato, le esigenze delle soluzioni attuali richiedono ingranaggi leggeri e affidabili, dalle eccellenti prestazioni meccaniche e, se possibile, dai costi contenuti. Nel settore automobilistico, la riduzione del peso dei componenti favorisce la riduzione delle emissioni inquinanti.
I ricercatori si sono concentrati in prevalenza sulla riduzione del peso di componenti tradizionali del veicolo, proponendo soluzioni innovative alleggerite e sviluppando nuovi design e geometrie. Sebbene alleggerire componenti non strutturali sia una strategia frequente, il margine legato a questo tipo di ottimizzazione si sta esaurendo, rendendo necessario intervenire sulla massa anche di componenti strutturali, inclusi gli ingranaggi.
La riduzione del peso degli ingranaggi può essere ottenuta, ad esempio, mediante l’introduzione di fori nelle regioni scarsamente sollecitate, ad esempio della cartella della ruota. Purtroppo, riduzioni significative di peso sono difficili da ottenere senza intaccare l’affidabilità e le prestazioni delle ruote. Inoltre, l’uso di materiali diversi dai metalli non è sempre applicabile.
Qualora sia consentito, è chiaro che materiali leggeri applicati a zone con stress ridotto favoriscono un notevole aumento del rapporto resistenza-peso. Ciò è reso possibile anche dal fatto che le sollecitazioni, in condizioni operative nominali, sono molto maggiori nella dentatura piuttosto che nella cartella della ruota.
La figura 1 mostra un esempio di modellazione numerica agli elementi finiti (FEM) che evidenzia le aree di maggiore stress in prossimità della dentatura di due ruote ingranate.
Idealmente, le specifiche in termini di prestazioni, affidabilità, peso e costo possono essere soddisfatte da un progetto di ruota avente proprietà personalizzate, mediante, ad esempio, l’impiego di materiali ad elevata resistenza e densità nelle zone maggiormente sollecitate e materiali a bassa resistenza, densità e costo nelle zone meno critiche.
In figura 2 (a) si mostra lo schema di un tipico ingranaggio ibrido multi-metallo caratterizzato da un anello esterno in acciaio, comprendente la zona della dentatura, maggiormente sollecitata, e un anello interno, usato per il fissaggio all’albero, per esempio mediante linguetta. Il resto del volume è ottenuto in lega di alluminio.
Le figure 2(b) e 2 (c) rappresentano invece in dettaglio due possibili soluzioni di ingranaggi ibridi a confronto.
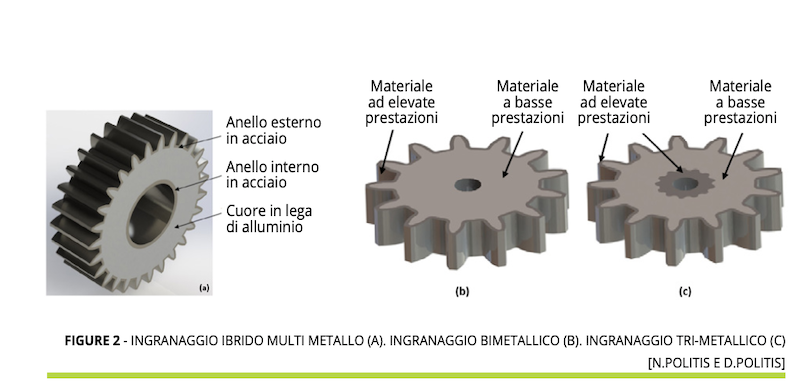
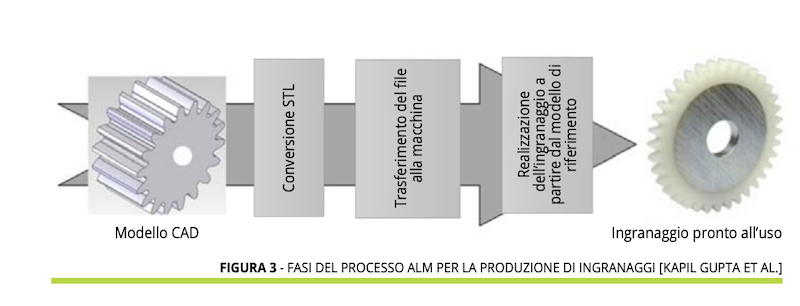
Additive manufacturing per la produzione di ingranaggi ibridi
I processi di fabbricazione additiva AM (additive manufacturing) rappresentano una soluzione a costi contenuti per la produzione di ruote dentate ottimizzate. La figura 3 illustra le principali fasi di un processo AM a layer sovrapposti (ALM, Additive Layer Manufacturing). Un approccio bottom up, insieme alla deposizione di materiale strato per strato, consente la realizzazione di geometrie complesse.
Il punto di partenza è la realizzazione del modello CAD dell’ingranaggio, successivamente convertito in formato STL, e trasferito alla macchina per la realizzazione del componente vero e proprio.
Tra le tecnologie ALM maggiormente diffuse vi sono: la stereolitografia, la modellazione FDM (Fused Deposition Modeling), la sinterizzazione laser SLS (Selective Laser Sintering) e la stampa a getto di inchiostro (inkjet).
Esse consentono la produzione di ingranaggi di varie forme, dimensioni e materiali, dalle materie plastiche alle polveri metalliche, sino ai compositi e ai materiali ceramici.