Perchè tribologia e lubrorefrigerazione? Perchè alla lubrorefrigerazione oggi è riconosciuto un ruolo primario: incide sulle prestazioni della macchina, sull’utensile e sulla qualità del processo, definendone l’efficienza.
Le lavorazioni per asportazione di truciolo sono processi complessi, che vedono innescarsi fenomeni di natura meccanica, termica e fisico-chimica, strettamente correlati fra loro e
interconnessi, con conseguenti ricadute-influenze.
La prima influenza riguarda il risultato della lavorazione stessa, sia in termini di performance sia di qualità del manufatto prodotto, intendendo tanto le proprietà che l’estetica. Infatti, dalla lavorazione deriva, oltre all’aspetto estetico (non necessariamente essenziale), il comportamento in esercizio del componente, lungo tutta la sua vita prevista.
Le superfici lavorate giocano un ruolo fondamentale nel determinare le proprietà di contatto, attrito e usura del pezzo, spesso determinandone la durata.
Il compito della tribologia
La tribologia si occupa di analizzare i fenomeni di interazione superficiale e, più specificatamente, studia:
• attrito; influenza le forze e l’energia richieste dal processo, oltre alla qualità e al grado di finitura della superficie.
• usura; porta al degrado le superfici e la geometria dell’utensile, con una ricaduta sulla qualità dei manufatti e sui costi di produzione, causa rilavorazioni e/o scarti.
• lubrificazione; fondamentale in ogni lavorazione meccanica, con il compito di contenere attrito e usura, senza interferire col materiale del manufatto in lavorazione.
Questi fenomeni, spesso interconnessi, contribuiscono pesantemente a determinare la tecnologia produttiva più idonea, con i relativi costi di processo. Guardando i tre fenomeni citati, è noto come l’attrito possa causare usura, e come la lubrificazione possa essere considerata la “cura” perché, riducendo l’attrito, si possono ridurre tutte le cause che portano al degrado di un processo produttivo.
I tre aspetti della tribologia, attrito, usura e lubrificazione, sono quindi strettamente legati, anche se ognuno si presenta con precise peculiarità. La tribologia è pertanto la scienza e la tecnologia delle superfici interagenti.
La presenza di lubrorefrigerante durante una lavorazione per asportazione di truciolo va a modificare proprio come interagiscono le superfici a contatto e in moto relativo.
Nel processo per asportazione, l’interfaccia fra utensile e pezzo in lavorazione è soggetta a molte variabili, tra le quali le più importanti sono:
• la pressione di contatto
• la velocità di taglio
• la temperatura
Se manca l’azione protettiva del lubrorefrigerante mentre le superfici strisciano una contro l’altra, pressione, velocità e temperatura portano a condizioni di attrito e usura, anche molto importanti. Elementi che vanno a causare danni di varia natura, compromettendo sia la qualità del manufatto sia l’efficienza della lavorazione. La ricaduta, come è facilmente intuibile, è di tipo economico.
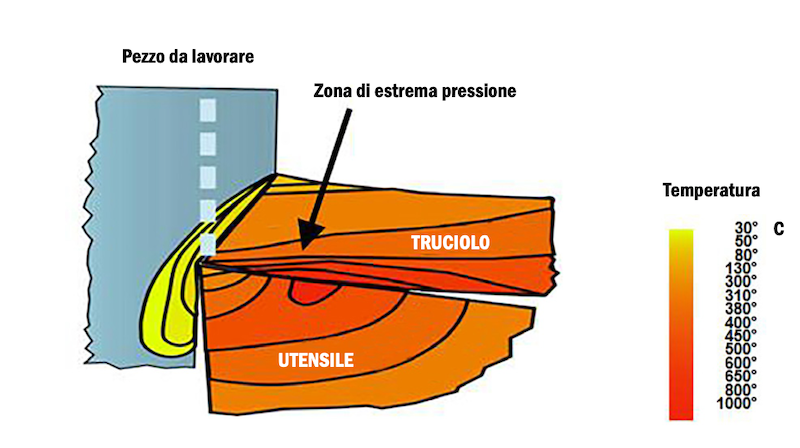
Lubrorefrigerazione: un ruolo da protagonista
La strategicità del sistema lubrorefrigerazione, dal lubrorefrigerante, alla sua pulizia, alla gestione di trucioli ed esausti, è ormai riconosciuta. Questo tipo di impianto ha un ruolo fondamentale tanto nella riuscita della lavorazione meccanica, tanto nella protezione della macchina utensile. Certamente l’investimento più importante di un’azienda manifatturiera.
Il sistema lubrorefrigerazione è da sempre oggetto di studi approfonditi che hanno portato allo sviluppo di nuove formulazioni, nuovi sistemi di filtraggio e nuovi concetti di “gestione del fluido da taglio”. Elementi sviluppati in modo da tenere ben presente la complessità del sistema, con tutte le interazioni connesse.
I più moderni schemi innovativi pongono particolare attenzione al miglioramento delle performance di lavorazione, nel rispetto dell’ambiente e della salute dell’uomo. Vale comunque la pena ricordare quali siano i compiti principali cui deve assolvere un lubrorefrigerante:
• il raffreddamento della zona di taglio, con conseguenti riduzione del rischio distorsioni
del pezzo e aumento della durata dell’utensile;
• la riduzione di attrito e di usura, con conseguente aumento della durata dell’utensile e
miglioramento della qualità superficiale;
• la riduzione delle forze e delle energie in gioco;
• l’evacuazione dei trucioli dalla zona di lavoro;
• la protezione della superficie lavorata da eventuali corrosioni.
L’efficacia di un fluido da taglio dipende certamente dalla sua “bontà”, ma chiaramente questo non basta. Modalità di applicazione, temperatura, velocità di taglio, tipo di lavorazione, sono tutti fattori che hanno una forte influenza. Questo significa che, come materiali e tecnologia si evolvono, anche la formulazione dei lubrorefrigeranti deve innovarsi, stando al passo sia con le tecnologie di ultima generazione, sia con le esigenze legate all’alta produttività o alla flessibilità. Naturalmente senza tralasciare l’impronta green: sostenibilità ambientale e sicurezza-salubrità, sono oggi caratteristiche imprescindibili, su cui non si può scendere a compromessi.
Le caratteristiche che deve avere un fluido da taglio di ultima generazione sono: stabilità; assenza di schiuma; protezione dei pezzi in lavorazione e della macchina utensile; assoluta osservanza delle normative; compatibilità con un’ampia gamma di materiali; idoneità a lavorazioni secondo le più moderne tecnologie quali l’alta velocità e l’alta pressione. Un prodotto che non abbia queste caratteristiche facilmente porterà a maggior usura degli utensili, instabilità della molecola (quindi il fluido non potrà lavorare come dovrebbe), sostituzioni frequenti ed eventuali criticità-danni alla macchina e/o all’uomo.
L’attrito
Durante una lavorazione meccanica, l’attrito ha una influenza diretta sulle forze e l’energia necessarie per compiere la lavorazione stessa. Il processo è di tipo dissipativo, con una dissipazione irreversibile di energia cui consegue generazione di calore. L’aumento di temperatura ha ripercussioni decisive sulla lavorazione: può compromettere la qualità-integrità della superficie, con la possibile generazione di cricche; può rallentare lo scorrimento relativo utensile-pezzo, scorrimento che, in condizioni estreme, può addirittura essere impedito. L’attrito è quindi considerato “nemico” delle lavorazioni per asportazione di truciolo, ma anche dello stampaggio, sebbene non in tutti i processi tecnologici sia un fenomeno indesiderato, per esempio, senza attrito (controllato) non sarebbe possibile la laminazione. Buona parte dell’energia dissipata per vincere l’attrito viene convertita in calore, con un conseguente aumento di temperatura all’interfaccia. Il riscaldamento è certamente funzione della forza d’attrito, ma non solo, dato che dipende anche dalla velocità, dalla rugosità della superficie e dalle caratteristiche fisiche del materiale (conducibilità termica e calore specifico). L’aumento di temperatura può essere talmente elevato da avvicinarsi pericolosamente alla temperatura di fusione e, in alcuni casi a raggiungerla, portando a parziale fusione entrambi o uno solo dei materiali a contatto, con il rischio di incollaggio. Il riscaldamento ha anche un’influenza sulle proprietà dei fluidi lubrificanti, in particolare sulla viscosità. Infatti, un innalzamento termico può facilmente portare al degrado del fluido, che diventa meno efficiente con conseguenti danni sui risultati della lavorazione, sia in termini di prestazione sia di qualità del manufatto, che può presentare danni superficiali.
Raffreddare e lubrificare, ma… nel punto
Oggi la questione “pulizia” è stata pressoché universalmente riconosciuta come il nocciolo del problema lubrorefrigerazione e, con essa, la filtrazione, per molto tempo trascurata o sottovalutata. È ormai chiaro come scarsa pulizia e filtrazione siano la causa prima di inefficienze più o meno gravi. Tradizionalmente la filtrazione è meccanica, con la classica variante economica rappresentata dai filtri ricambiabili, a cartuccia o a sacchetto, ma, negli ultimi anni, si è passati a sistemi più evoluti in grado di assicurare filtrazioni anche molto spinte (filtrazione fina, microfiltrazione o anche nano filtrazione), costanti nel tempo, non soggette alle fluttuazioni dovute al progressivo intasamento dei filtri. I sistemi più evoluti “lavorano” il lubrorefrigerante secondo un processo di pulizia continuo, ossigenandolo e liberandolo dalla presenza degli oli estranei e delle particelle solide mediamente con dimensioni superiori a 10 μm (alcuni sistemi offrono filtrazioni che arrivano a 5 μm). Il fluido pulito viene rimesso in circolo, senza che siano stati impiegati elemento filtranti, che andrebbero comunque periodicamente sostituiti o puliti, o carte filtranti che andrebbero invece smaltite, o elementi meccanici di separazione con parti in movimento. In questo modo è assicurato un recupero di efficienza e costi, allungando la vita sia agli utensili che al fluido stesso, riducendo i tempi di fermo macchina per pulizia delle vasche e sostituzione del lubrorefrigerante. I sistemi che garantiscono una pulizia costante del fluido da taglio sotto i 10μm hanno aperto le porte alle lavorazioni in pressione. Il getto di lubrorefrigerante risulta privo di inquinanti, in particolare di particelle abrasive, che inevitabilmente andrebbero a scalfire la superficie in lavorazione.