Tra i trattamenti termici più conosciuti la tempra ricopre certamente un ruolo da protagonista. Conosciuta fin dall’età del rame e del ferro, ad opera di fabbri che scoprirono, probabilmente per caso, come riuscire a “rendere più duri e resistenti” gli utensili di cui avevano bisogno, scaldando fino a colorazione rosso-ciliegia e poi raffreddando velocemente. Una testimonianza nota, risalente al XII a.C. e ritrovata in Palestina, è un piccone che presenta struttura martensitica
di Adriana Rullo
Tempra
Il trattamento termico di tempra, come è noto, consente di migliorare la proprietà meccaniche e tecnologiche del materiale, modificandone la microstruttura. Il beneficio che si ottiene riguarda l’incremento di durezza del componente sottoposto al trattamento, che comporta una migliore resistenza all’usura e conseguente diminuzione dell’allungamento percentuale.
Il ciclo termico comprende principalmente tre step:
- Riscaldamento ad una temperatura superiore a quella dell’eutettoide (in genere circa 50°C sopra AC3);
- Mantenimento a tale temperatura per consentite la completa trasformazione della struttura in fase austenitica, fino al cuore del componente;
- Raffreddamento rapido (superiore alla velocità critica di raffreddamento) per consentire la trasformazione della microstruttura martensitica.
Per la buona riuscita del trattamento in gioco è fondamentale conoscere innanzitutto la temperatura AC3 per l’acciaio considerato e, di conseguenza, regolare adeguatamente tempo e temperatura dei vari step del processo. Il tempo adeguatamente controllato permetterà di avere uniformità durante la trasformazione in tutto il pezzo, dalla superficie fino al cuore. Mentre la temperatura opportunamente scelta consentirà di evitare un surriscaldamento con conseguente ingrossamento del grano e peggioramento delle proprietà meccaniche.
Il passaggio fondamentale del processo di tempra è quello austenite-martensite che avviene durante il raffreddamento rapido, che dovrebbe iniziare e terminare a basse temperature per ottenere risultati ottimali. In tale passaggio, ricordiamo dalle curve di Bain, che è bene prevedere un raffreddamento tale da evitare di toccare il “naso perlitico” per ottenere una microstruttura totalmente martensitica. La velocità di raffreddamento, infatti, deve essere tale da evitare fenomeni diffusivi e consentire la trasformazione martensitica (non ricostruttiva). In questo passaggio si ha un cambiamento della cella elementare da CFC (cubico facce centrate) dell’austenite a TCC (tetragonale corpo centrato) della martensite, con conseguente aumento di volume. Tale transizione è favorita in presenza di più alte percentuali di Carbonio che rimane “congelato” nel reticolo cristallino dell’austenite in posizione interstiziale, favorendo la trasformazione. Con una presenza importante di C, inoltre, la trasformazione è favorita dall’abbassamento della temperatura di inizio trasformazione della martensite (Ms). Da letteratura si osserva che per 0.6% di carbonio la temperatura di Ms è circa 300°C mentre per un acciaio con 0.9% di carbonio la temperatura di inizio trasformazione della martensite scende a circa 200°C.
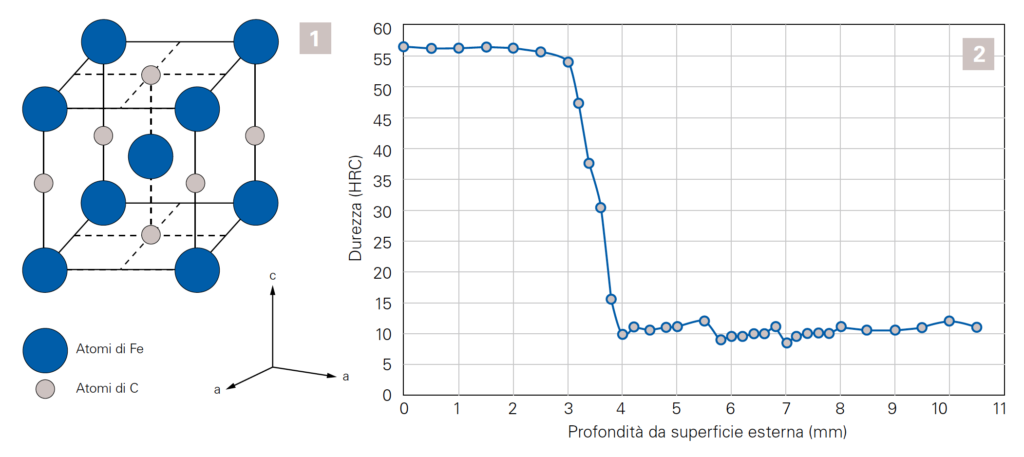
Microstrutture interessate
Ma cosa è in sostanza l’austenite? Si tratta di una soluzione solida di carbonio, insieme agli altri elementi dell’acciaio, nel reticolo del Ferro in fase gamma (cubica faccia centrata), fase in cui si ha una maggior solubilità del carbonio.
La martensite come è definita? Innanzitutto, il nome martensite deriva dal pioniere della metallografia A. Martens e viene attribuito alle strutture aciculari ottenute con la tempra. Il meccanismo di formazione, come anticipato, non prevede diffusione di atomi e procede senza nucleazione. I grani della martensite si sviluppano come piccoli nuclei alla velocità del suono nella matrice dell’austenite. (vedi immagine 1)
Associato al trattamento di tempra vi è il concetto di temprabilità dell’acciaio. Questo indica l’attitudine del materiale ad essere temprato (anche definita come la misura della profondità di tempra che si riesce ad ottenere), in relazione alla quantità di carbonio presente e agli altri elementi di lega, che influenzano in modo differente tale caratteristica. Ad esempio, il Cromo (come il Manganese) comporta una diminuzione della velocità critica di raffreddamento e perciò un aumento della temprabilità. Il Boro, a sua volta, aumenta la temprabilità, anche in piccole quantità (0.002%) modificando le curve TTT dell’acciaio considerato.
Drasticità dei mezzi tempranti
La terza fase del ciclo termico di tempra può essere eseguito in vari mezzi, detti appunto tempranti. Questi vengono scelti in fase di progettazione in relazione alle proprietà che devono essere ottenute con uno specifico tipo di acciaio. In base al tipo di mezzo temprante, infatti, si ottengono dimensioni dei grani differenti, durezze diverse, oltre a deformazioni del pezzo più o meno accentuate, a causa della capacità di raffreddamento del liquido usato. Le variabili in gioco, come la conduttività termica, il calore specifico e il calore di vaporizzazione, la viscosità e la temperatura, influenzano la velocità di raffreddamento e quindi la severità di tempra. Nel dettaglio, quando viene raffreddato un pezzo in un mezzo temprante si susseguono tre fasi, che portano ad una specifica velocità di raffreddamento in relazione alle variabili viste sopra. La prima fase, detta stadio di vapore, si verifica quando il pezzo viene immerso nel liquido temprante e viene avvolto appunto da una coltre di vapore. In questo stadio, lo strato di vapore non permette una buona velocità di raffreddamento, consentendo la rimozione del calore solo per irraggiamento. Un vantaggio è dato sicuramente da un sistema di agitazione, che garantisce un ricambio del liquido avvolgente il pezzo. Subito dopo, quando la temperatura del pezzo si abbassa, lo strato di vapore diviene instabile, generando bolle dalla superficie del componente, inizia la fase di ebollizione. In questo stadio la velocità di raffreddamento è maggiore, per mezzo dei movimenti convettivi che si instaurano e che dipendono dal tipo di mezzo temprante. Continuando in questo processo, il pezzo viene raffreddato fino a quando la sua temperatura eguaglia quella del liquido circostante così che la velocità di raffreddamento diminuisce di nuovo, a causa del trasferimento di calore per convezione (stadio convettivo). Considerando quanto appena detto, si deduce che un fluido ideale dovrebbe consentire un rapido raffreddamento nelle fasi iniziali, per evitare di innescare la trasformazione perlitica, e poi più lento scendendo in temperatura verso la trasformazione martensitica. Il punto critico nel processo di raffreddamento è nella fase di ebollizione, che come detto aumenta il coefficiente di trasferimento del calore dal pezzo, che corrisponde nella maggior parte dei casi alla zona del naso perlitico delle curve TTT e di conseguenza ha un’importanza rilevante nelle deformazioni sul pezzo post tempra.
I mezzi tempranti utilizzati a tale scopo sono molteplici, dall’acqua alle soluzioni polimeriche a concentrazioni differente (ad esempio PAG) e dall’olio fino ad arrivare ai gas, in genere He o N2 ad alta pressione. In relazione al tipo di acciaio viene scelto uno specifico mezzo temprante, da quello più drastico come l’acqua a quello più dolce come l’olio, che diminuisce il pericolo di innescare cricche da tempra. Il risultato ottenuto dipende ovviamente anche dalla temprabilità dell’acciaio in uso, che influenza la profondità di tempra e quindi la differenza di durezza tra superficie esterna e cuore, favorendo un certo profilo di tempra.
Dopo la panoramica sul trattamento di tempra, facciamo un focus sulla tempra superficiale, più di frequente utilizzata. Nel caso in cui si abbia come obiettivo principale aumentare la resistenza all’usura e alla fatica, con aumento della resistenza all’indentazione, ma mantenendo un cuore tenace, si ricorre certamente alla tempra superficiale.
Il ciclo termico è identico a quello visto sopra per la tempra massiva, con la sola eccezione del riscaldo in fase austenitica che interessa solo la superficie del componente. Il risultato è un elemento con una doppia microstruttura: martensite in superficie e perlite-ferrite in quantità variabili da sotto la superficie verso il cuore (dove si trova la microstruttura dell’acciaio base). Tale trattamento può essere utilizzato con acciai che abbiano un alto contenuto di carbonio, che, come anticipato, formano facilmente martensite. Nel caso, invece, in cui si abbia un acciaio con una percentuale di carbonio di circa 0.16-0.23 è necessario ricorrere alla carbocementazione, prima della fase di tempra.
Esempi di applicazione sono ingranaggi, utensili, cuscinetti, organi vari per il movimento meccanico, elementi di collegamento.
Nel trattamento di tempra superficiale, il riscaldo della superficie avviene mediante effetto joule, tramite induzione elettromagnetica con corrente ad alta frequenza. In sostanza, il pezzo da trattare viene fatto passare entro una bobina che provoca un riscaldamento della superficie, senza alterare la temperatura a cuore (tempra ad induzione). Un’alternativa interessante all’uso della corrente è la tempra alla fiamma con cui si ottiene lo stesso risultato (indurimento della sola superficie), ma utilizzando come mezzo di riscaldamento la fiamma ossiacetilenica. Viene utilizzata per la produzione singola o di serie meccanizzata e favorisce un minor movimento dimensionale grazie al riscaldo localizzato.
La profondità di tempra ottenuta dipende ovviamente anche dalla temprabilità dell’acciaio e la composizione chimica, che influenza anche le durezze ottenibili, oltre al mezzo temprante che gioca un ruolo chiave.
Da quanto visto finora è facilmente comprensibile che il trattamento superficiale produce un gradiente di durezza sul pezzo in oggetto, partendo da una superficie con durezza maggiore e via via diminuendo fino ad arrivare al cuore, dove si ottengono valori tipici dell’acciaio base non trattato. L’andamento del profilo di durezza ottenibile è influenzato dalla composizione chimica e temprabilità dell’acciaio oltre ai parametri di processo. Un esempio di profilo di tempra superficiale è riportato in figura 2.
Il trattamento di tempra superficiale, quindi, rappresenta un’ottima soluzione quando è richiesta resistenza meccanica all’usura ed elevata durezza accompagnate da buona tenacità a cuore, che garantisce maggiore resistenza agli urti.