In questo studio, ricercatori lituani hanno sviluppato un innovativo processo per aumentare l’efficienza nella formatura incrementale, basato sull’eccitazione della lamiera da lavorare tramite vibrazioni ultrasoniche così da ridurre attriti e forze durante la trasformazione.
Il moderno contesto produttivo ci ha abituati, ormai da diversi anni, a numerose difficoltà in continua evoluzione. Queste complessità devono essere gestite dai produttori che sono obbligati ad aggiornarsi e adeguarsi per meglio rispondere alle esigenze del mercato. Uno dei trend più importanti negli ultimi anni è quello della flessibilità.
Grandi lotti produttivi e richieste stabili da parte dei clienti sono ormai un lontano ricordo. È quindi un imperativo per le aziende manifatturiere la capacità di adattarsi rapidamente.
Per questo risulta particolarmente vantaggioso riuscire a risparmiare su costi fissi come, ad esempio, la produzione di stampi creati ad hoc e i tempi dovuti al setup di macchinari e linee produttive. Le aziende che si orientano verso soluzioni flessibili spesso vengono premiate dal mercato proprio per la capacità di gestire agilmente la mutevole situazione esterna. In questo complesso ambiente alcune soluzioni guadagnano sempre maggiore interesse, proprio per la potenzialità di adattarsi ad ogni esigenza.
Formatura incrementale
Tra i diversi processi di trasformazione della lamiera risulta particolarmente interessante, per le sue doti di flessibilità, il processo di formatura incrementale a singolo punto (Single Point Incremental Forming o “SPIF”). Tale processo sfrutta un punzone semisferico per compiere l’intera lavorazione. L’utensile viene movimentato nello spazio per deformare la lamiera grazie ad un sistema CNC (macchina a controllo numerico) ad almeno 3 assi o grazie a robot antropomorfi.
I movimenti del punzone sono complessi e progressivi, ma se opportunamente definiti permettono di ottenere una grande varietà di forme e geometrie. Il vantaggio più interessante di questo processo è proprio legato alla flessibilità.
A differenza di altri processi tradizionali non servono costosi e complessi stampi, ma è invece necessario solamente un semplice utensile standard. In questo modo è possibile produrre componenti diversi semplicemente riprogrammando il macchinario, riducendo quindi costi e tempi di attesa. Questo processo risulta infatti di particolare successo nei settori in cui sono richieste produzioni di piccole serie di componenti.
Durante la produzione tramite tecnica “SPIF” le forze dovute agli attriti tra l’utensile e la lamiera giocano un ruolo fondamentale per quanto riguarda la qualità del prodotto finito. Diversi studi sono già stati effettuati per approfondire l’usura, le forze in gioco e la rugosità superficiale di prodotti così ottenuti. Dallo studio della letteratura appare chiaro come, per ottenere componenti di qualità, sia necessario ridurre le forze in gioco.
La forza che agisce sul punzone è infatti correlata all’insorgere di difetti e alla qualità superficiale. La soluzione tipicamente utilizzata per risolvere questo problema è l’impiego di lubrificanti.
Essi permettono infatti di migliorare il risultato finale del processo, ma sono nocivi per l’ambiente, rischiano di influenzare la composizione chimica della lamiera lavorata e, non meno importante, richiedono risorse per la pulizia dal componente.
Processo innovativo
Per riuscire a ridurre gli attriti senza utilizzare rischiosi lubrificanti gli autori della ricerca propongono una soluzione innovativa (Figura 1). L’idea è quella di eccitare la lamiera da lavorare tramite vibrazioni ultrasoniche così da ridurre attriti e forze durante la trasformazione. Per sperimentare questa nuova soluzione è stata impiegata una lamiera di alluminio AW1050 delle dimensioni 350 x 350 x 0,5 mm.
L’utensile è un punzone semisferico in acciaio con diametro di 8,5 mm e la lamiera è eccitata da un trasduttore piezoelettrico agente tra 0,5 e 60 kHz di frequenza. La sperimentazione mostra che i migliori risultati si ottengono nel range tra i 28 e i 36 kHz di frequenza. Qui le vibrazioni laterali sul piano XY sono predominanti rispetto a quelle in direzione normale (asse Z) considerando il piano della lamiera.
In questo modo è possibile favorire lo scorrimento dell’utensile, senza andare ad impattare negativamente sulla superficie. La diminuzione degli attriti è più che soddisfacente dato che si ottiene una riduzione superiore all’80 %. Questa soluzione permette di rimanere sempre in regime di scorrimento permettendo di ottenere un notevole incremento dell’efficienza del processo di formatura incrementale.
Sperimentazione
Un semplice componente è stato realizzato per validare il processo innovativo di formatura incrementale (Figura 2). Il macchinario sperimentale costruito dai ricercatori è stato sensorizzato per riuscire a misurare l’attrito tra utensile e lamiera. Queste misure sono state confrontate in tre diverse condizioni: senza lubrificazione e vibrazioni, solo con lubrificazione e solo con vibrazioni.
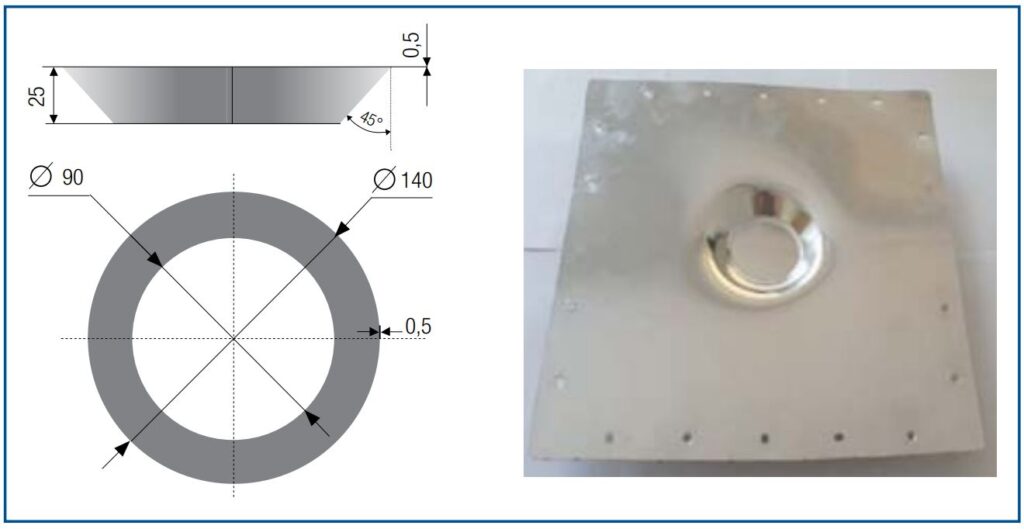
Le forze di attrito vengono drasticamente ridotte quando viene utilizzata una contromisura, così da efficientare il processo e migliorare la qualità finale del prodotto. L’utilizzo delle vibrazioni permette di ottenere risultati molto simili alla lubrificazione tradizionale dal punto di vista delle forze in gioco. Questa soluzione alternativa permette però di risolvere il problema ambientale evitando il problema dello smaltimento di sostanze nocive e non richiede la pulizia delle superfici.
Sono state inoltre effettuate delle misure di rugosità superficiale sul prodotto finale. La superficie del componente ottenuto tramite il processo con vibrazioni presenta Ra = 0.18–0.25 µm, quindi ottimi risultati rispetto alle soluzioni alternative.
Risultati
Il processo innovativo proposto dai ricercatori lituani risulta essere particolarmente interessante. La tecnica di formatura incrementale a singolo punto (abbreviata come “SPIF”), già particolarmente interessante per la sua flessibilità, viene ulteriormente migliorata grazie all’introduzione di un’eccitazione ultrasonica.
Per ottimizzare il problema delle forze di attrito durante la lavorazione è possibile, in alternativa alla lubrificazione tradizionale, introdurre vibrazioni ultrasoniche in grado di migliorare lo scorrimento dell’utensile sulla lamiera.
Gli autori hanno lavorato ad ottimizzare i parametri della trasformazione, ad esempio, ottimizzando il range di frequenza delle vibrazioni e hanno studiato una sperimentazione con l’obiettivo di mostrare le potenzialità di tale processo. I risultati così ottenuti sono più che soddisfacenti: le forze sono state ridotte di oltre l’80% e la finitura superficiale del componente finale risulta eccellente.
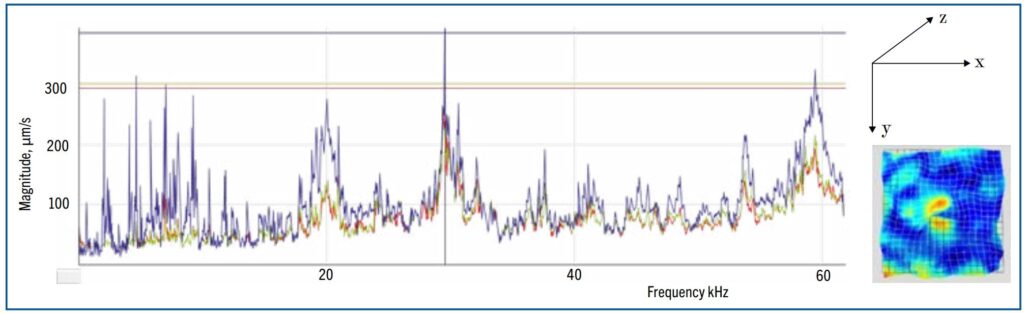
I vantaggi riguardano inoltre l’esclusione di lubrificanti che sono solitamente nocivi per l’ambiente e necessitano ulteriori lavorazioni per la pulizia del componente. Il paper dell’università lituana mostra un’interessante integrazione di brillanti soluzioni produttive. L’innovazione è data proprio dalla combinazione di due tecnologie che permettono di ottenere risultati concreti nel contesto produttivo. Questa soluzione ad oggi è ancora in fase di studio ed ottimizzazione, ma i presupposti sono ottimi per un’introduzione in ambito industriale.
Le aziende manifatturiere sono infatti sempre più alla ricerca di soluzioni flessibili ed efficienti sia dal punto di vista produttivo che energetico ed ambientale. Lo scopo della ricerca è infatti proprio quello di offrire nuove soluzioni, cercando di rimanere in linea con le attuali necessità del mondo industriale, così da sostenere una crescita produttiva sostenibile.
A cura di Stefano Grulli
Fonte: Ostasevicius, V., Paleviciute, I., Paulauskaite-Taraseviciene, A., Jurenas, V., Eidukynas, D., & Kizauskiene, L. (2021). Comparative analysis of machine learning methods for predicting robotized incremental metal sheet forming force. Sensors, 22(1), 18. https://doi.org/10.3390/s22010018