Spesso sottovalutato, il rapporto tra le tecnologie di piegatura e di saldatura, specie nella fase di ingegnerizzazione di un prodotto, è invece strettissimo. Ed è proprio dal loro modo di “parlarsi” che dipende la qualità di una commessa. Scopriamo perché.
La saldatura è un mondo affascinante e sterminato in quanto ad applicazioni su settori estremamente differenti e con materiali talvolta differenti tra loro.
Anche le tecnologie sono molte e chi si avvicina ad essa appassionandosi deve mettere in conto che prima o dopo dovrà decidere una strada per potersi specializzarsi in quanto il “tuttologo” non può esistere.
Da amante della piegatura rimango sempre affascinato dai racconti di alcuni illustri formatori e certificatori che narrano di realtà di nicchia con standard che le fanno somigliare a vere e proprie sale operatorie.
Ma anche di operatori giustamente stra-pagati in grado di saldare tubazioni a tenuta a decine di metri di profondità nell’oceano o veri e propri artisti ambidestri capaci di accoppiamenti perfetti sul titanio in ambito aeronautico.
Tuttavia, se ci concentriamo sulla carpenteria, ci sono molti punti di contatto tra piegatura e saldatura e ciò che è necessario è sicuramente ingegnerizzare il prodotto in funzione di tutti i processi della filiera
Come un buon progettista deve essere in grado di ideare complessivi che ne permettano un montaggio razionale e il più possibile agevole, così chi produce elementi in lamiera piegata deve tenere conto degli aspetti peculiari per l’applicazione dei processi.
Alcune domande tipo: “ci passerà la torcia?” oppure, “ci arriverà il saldatore” o, ancora, “possiamo risparmiare una saldatura piegando?” e, se sì, “quanto complesso diventerebbe realizzarla?” Talvolta mi piace pensare al binomio di lavorazioni piegatura e saldatura come due colleghe che concorrono a realizzare un pezzo: più “lavora” la prima e meno avrà da fare l’altra.
Si tratta ovviamente di una mera semplificazione in quanto a volte scegliere una strada rispetto l’altra serve a evitare i limiti che una delle due lavorazioni presenta.
Un esempio concreto: gli acciai alto-resistenziali
Da qualche decina di anni sono apparsi e si sono diffusi in maniera esponenziale i cosiddetti “acciai alto-resistenziali”.
Sebbene non esista una norma che certifichi esattamente la categoria, si tratta generalmente di acciai aventi una composizione chimica simile agli acciai da costruzione, ma che subiscono una serie di trattamenti termici che ne conferiscono una maggiore resistenza mantenendo il vantaggio della formabilità a freddo.
Se un tempo, infatti, l’unica strada per aumentare la resistenza di un acciaio era inserire elementi leganti adatti allo scopo, aumentando tuttavia la loro fragilità, oggi le loro caratteristiche hanno permesso di raggiungere prestazioni nei manufatti impensabili fino a pochi anni or sono.
A tal punto da “costringere” i progettisti a ripensare profondamente articoli prodotti allo stesso modo da decenni.
È in questo contesto che la piegatura ha assunto un ruolo importantissimo mentre prima era del tutto assente o quasi.
Una delle problematiche tipiche degli alto-resistenziali è quella di patire un drastico calo della resistenza in prossimità delle saldature quando i manufatti sono sottoposti a fatica.
La “fatica”, ricordiamolo, è la diminuzione della resistenza a trazione di un materiale sottoposto ad un ciclo ripetuto di tensioni (come standard si usa 1 milione in quanto la famosa curva di Woheler mostra la stabilizzazione del fenomeno).
Secondo alcuni studi effettuati da SSAB, l’acciaieria che produce tra gli altoresistenziali più noti, il loro prodotto di punta “ad alto limite elastico” subisce una riduzione della resistenza a trazione nelle zone delle saldature fino ad arrivare a quelle di un “banale” S235.
In figura 1 si nota l’evoluzione di una sezione di un braccio di una auto-gru.
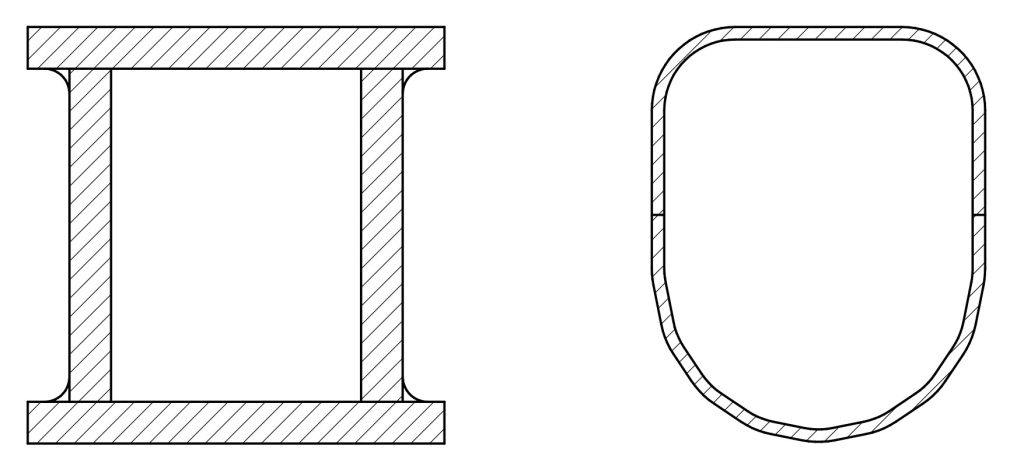
A sinistra il metodo di costruzione tradizionale, privo di piegature ma con ben quattro zone saldate. A destra il metodo odierno, con ampie zone di piegatura e le saldature, oltre che ridotte, spostate nelle zone a minore sollecitazione, in prossimità del cosiddetto “piano neutro”.
È grazie a queste applicazioni che oggi si possono raggiungere sbracci superiori ai 50 metri, misure impensabili qualche tempo fa!
Gli acciai altoresistenziali hanno trovato impiego da un punto di vista cronologico rispettivamente: nell’industria del sollevamento grazie alla presenza di tensioni tutto sommato prevedibili e carichi uni-direzionali, nelle macchine agricole e nell’automotive, soprattutto nel settore dei trasporti che sta vivendo una rapida evoluzione in tal senso.
Basti pensare che i longheroni dei rimorchi dei camion un tempo avevano uno spessore di 10 mm, per arrivare ad applicazioni più raffinate ed estreme a 4-6 mm con il relativo aumento di carico trasportabile.
Anche in questo contesto le saldature rappresentano zone altamente critiche, specie nel cosiddetto “collo di cigno”, la parte che permette al bilico di agganciarsi alla ralla della motrice.
La soluzione è di nuovo quella di spostarle nelle zone meno sollecitate quando non sostituirle con fissaggi a bulloni.
Piegare per non deformare
«La saldatura tira!»
È una delle frasi che da sempre vengono utilizzate nella carpenteria da tempi immemori.
Significa che meno si salda e meno tensioni responsabili di antiestetiche deformazioni si sviluppano.
Ad esempio: se dobbiamo pensare ad un carter di copertura che rimanga a vista, è bene cercare di realizzarlo favorendo la piegatura unendo tutti i lembi possibili e spostando le zone da unire mediante saldatura negli angoli nascosti.
Senza contare che proprio negli angoli è necessario talvolta riprendere in mano il pezzo per la necessaria rifinitura con abrasivi.
Dimmi come saldi e ti dirò come piego…
In base a come è stata prevista la fase di saldatura nella realizzazione di un articolo, è possibile che sia necessario pensare a una sequenza di piega diversa, oppure ad un attrezzaggio specifico.
Prendiamo un pezzo apparentemente identico come in figura 2.
Si tratta di un “vassoio” rettangolare che, da un punto di vista funzionale, può non presentare nessuna differenza pur cambiando le scantonature degli angoli e, quindi, l’accoppiamento dei lembi mediante saldatura.
Nel primo caso la chiusura viene detta in gergo “a spigolo con spigolo”, rimane una zona circoscritta dai due spessori da riempire di saldatura (talvolta con materiale di apporto) e la sequenza di piegatura sarà delle più classiche: “prima le lunghe e poi le corte” con un unico piazzamento tra punzone e matrice (figura 3 e figura 4).
Per una finitura estetica è necessario riprendere le saldature con la mola e il corretto abrasivo.
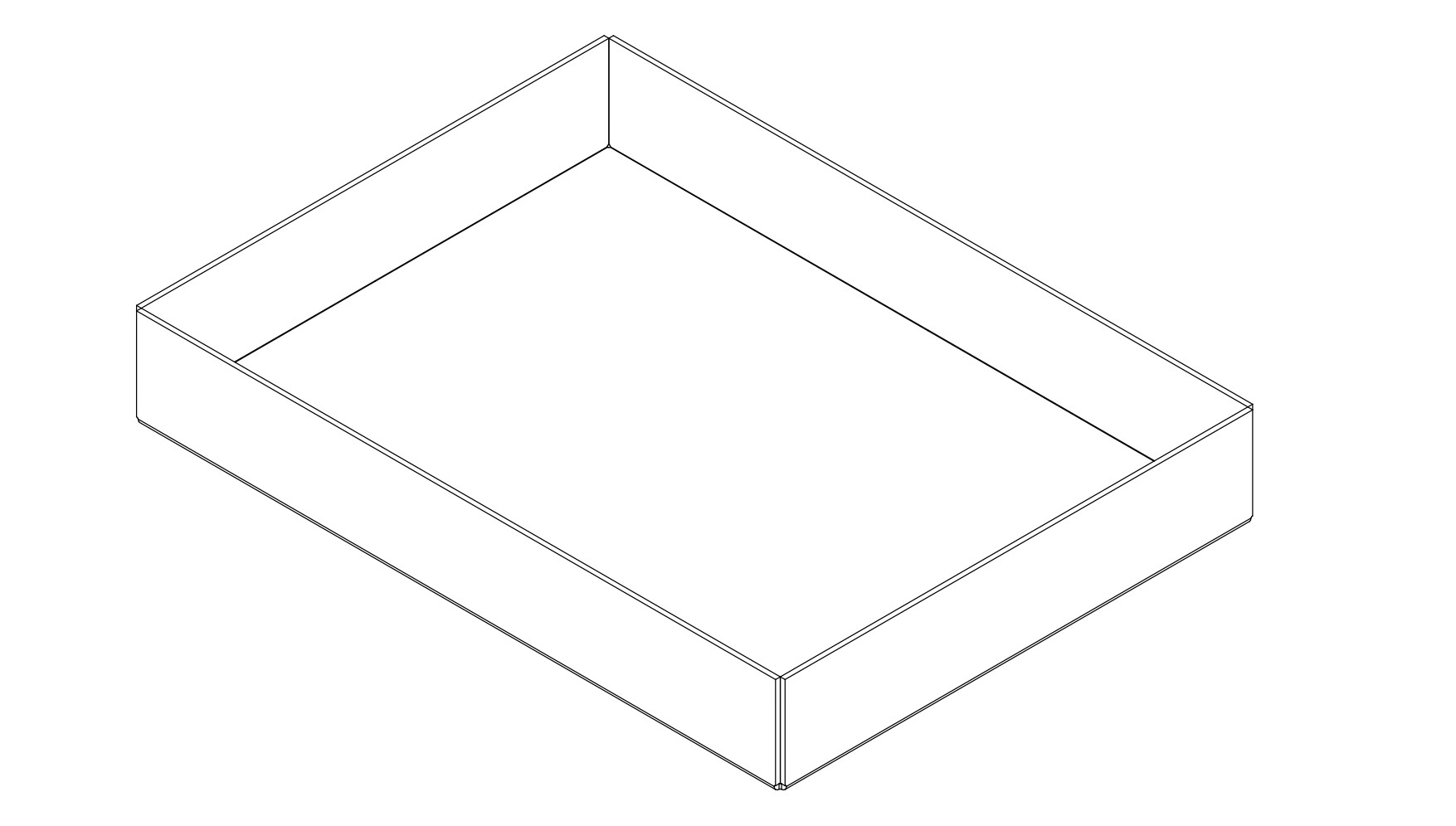
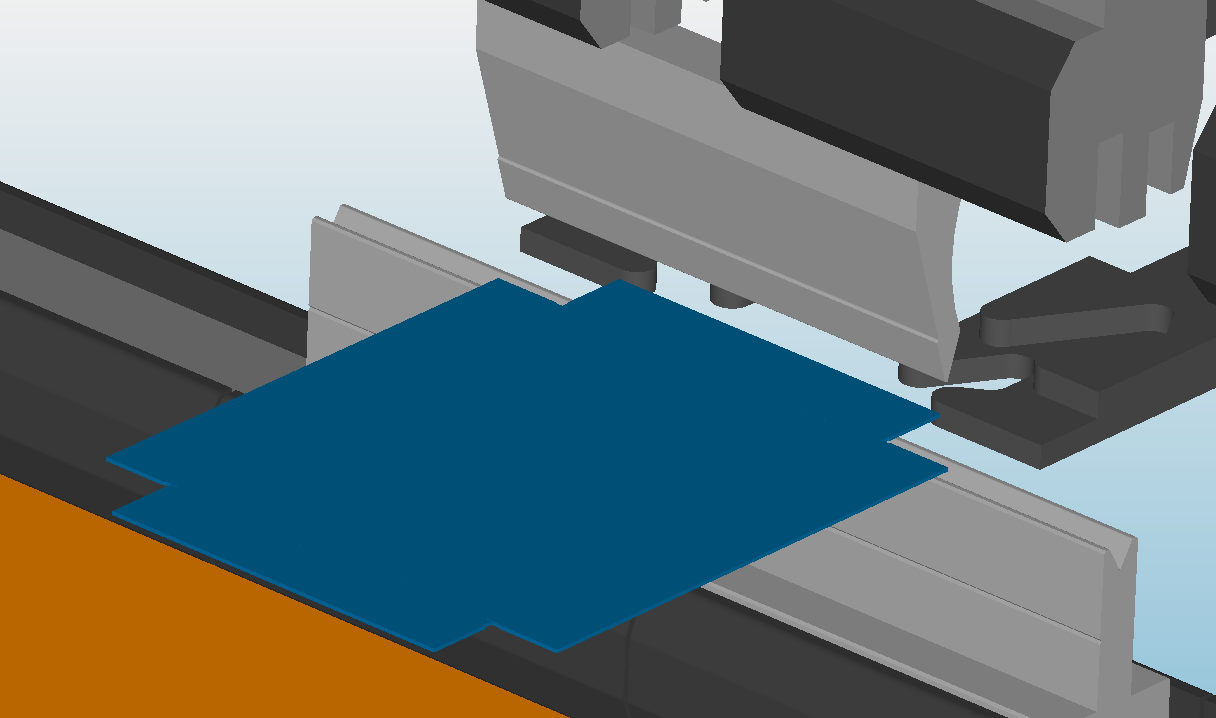
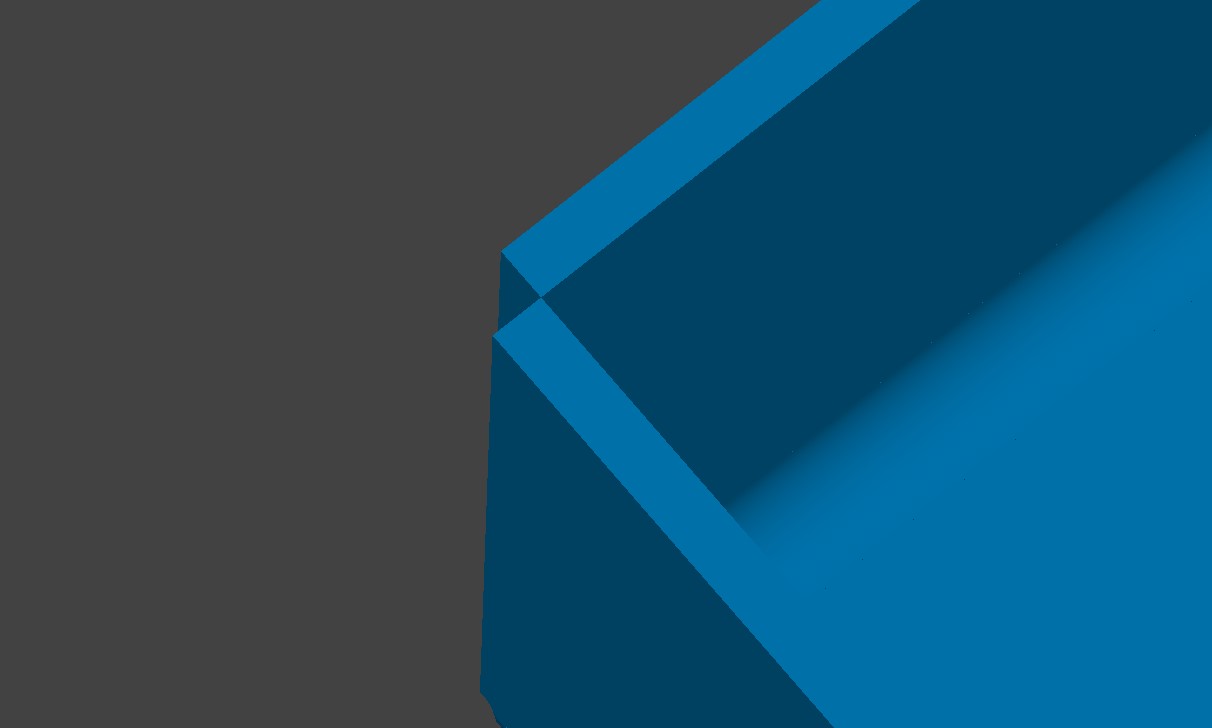
Nel secondo caso, invece, la scantonatura è “a spigolo sormontato”, in particolare con le pieghe più lunghe che sovrastano le corte.
In questo caso il risultato sarà uno spigolo vivo da saldare anche senza materiale di apporto ma con una sequenza di piega che potrebbe essere stravolta.
In caso di finiture estetiche e materiale con un ritorno elastico importante, è consigliabile eseguire prima le pieghe lunghe e poi le corte con due stazioni distinte di utensili in modo da permettere ai lembi il necessario “overbending” (figura 5 e figura 6).
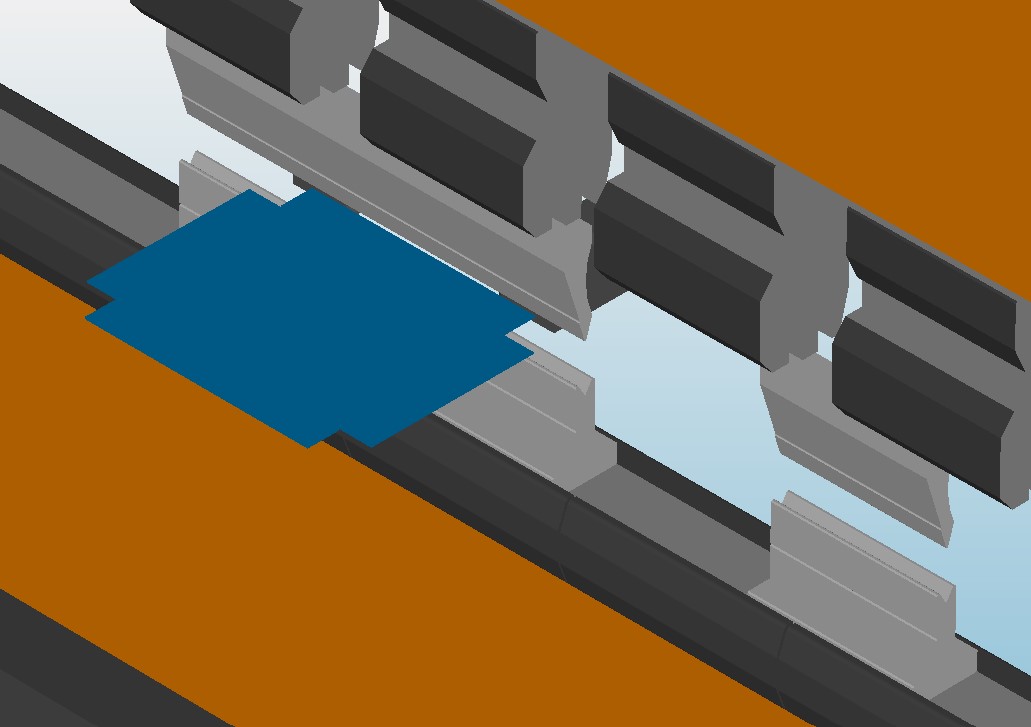
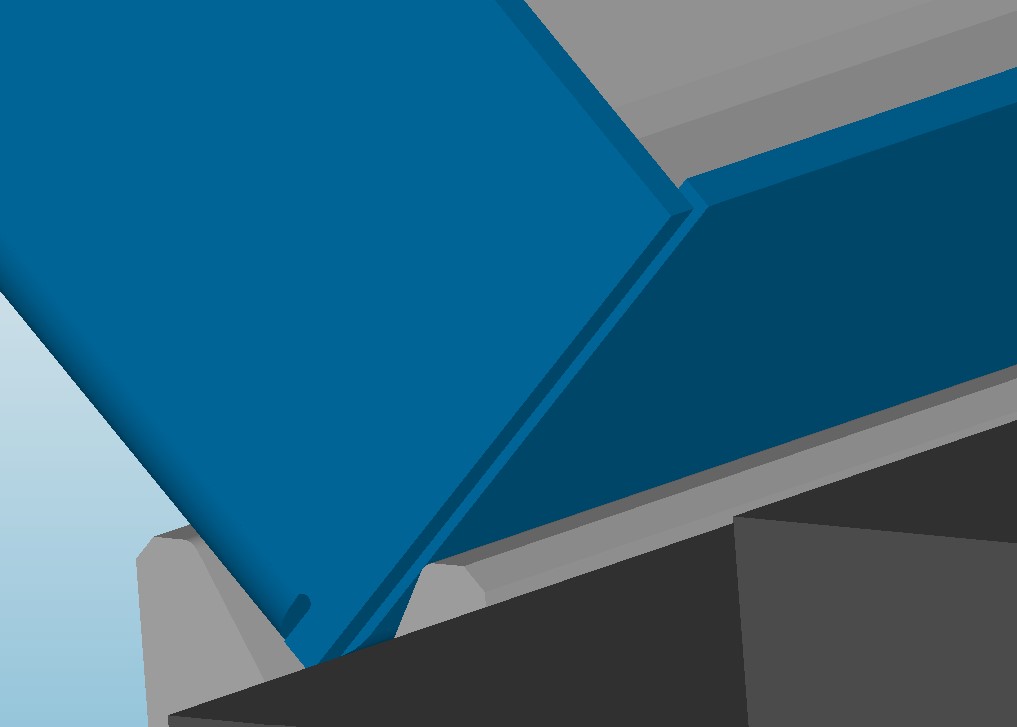
In questo esempio potrebbe non essere richiesta la finitura successiva alla saldatura.
Nel terzo caso, invece, la scantonatura prevede la caratteristica “bandiera”.
Si tratta di un “trucco” che consente in alcuni casi di evitare la saldatura o di prevedere un semplice punto o un tratto lontano dall’angolo con un risultato estetico di pregio e senza più il bisogno di rifinirlo con la molatura.
È un’applicazione che trova il suo impiego nelle lamiere sottili, tipicamente nei mobili in acciaio o nel settore del bianco, ma non solo!
In questo caso particolare la modalità di piegatura è ancora differente e prevede un attrezzaggio ancora più “accorto” in quanto esula dalle logiche classiche per la realizzazione dei pezzi (Figura 7, 8, 9).
Come si può osservare, c’è un filo conduttore, un rapporto strettissimo nell’ingegnerizzazione di un prodotto tra le tecnologie di piegatura e di saldatura.
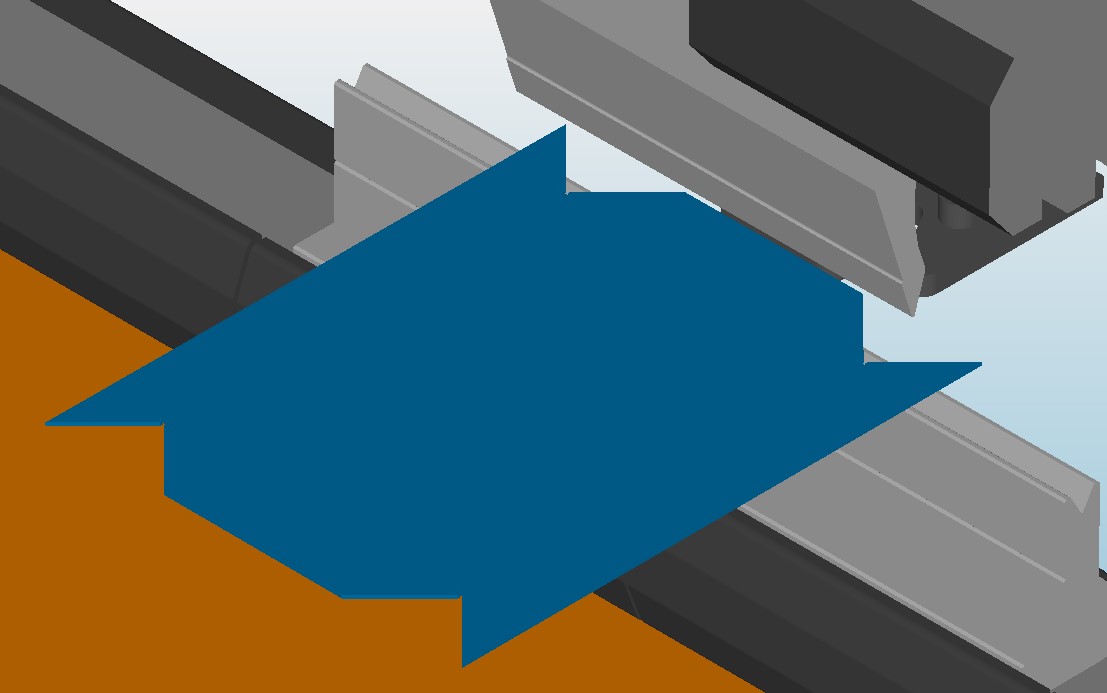
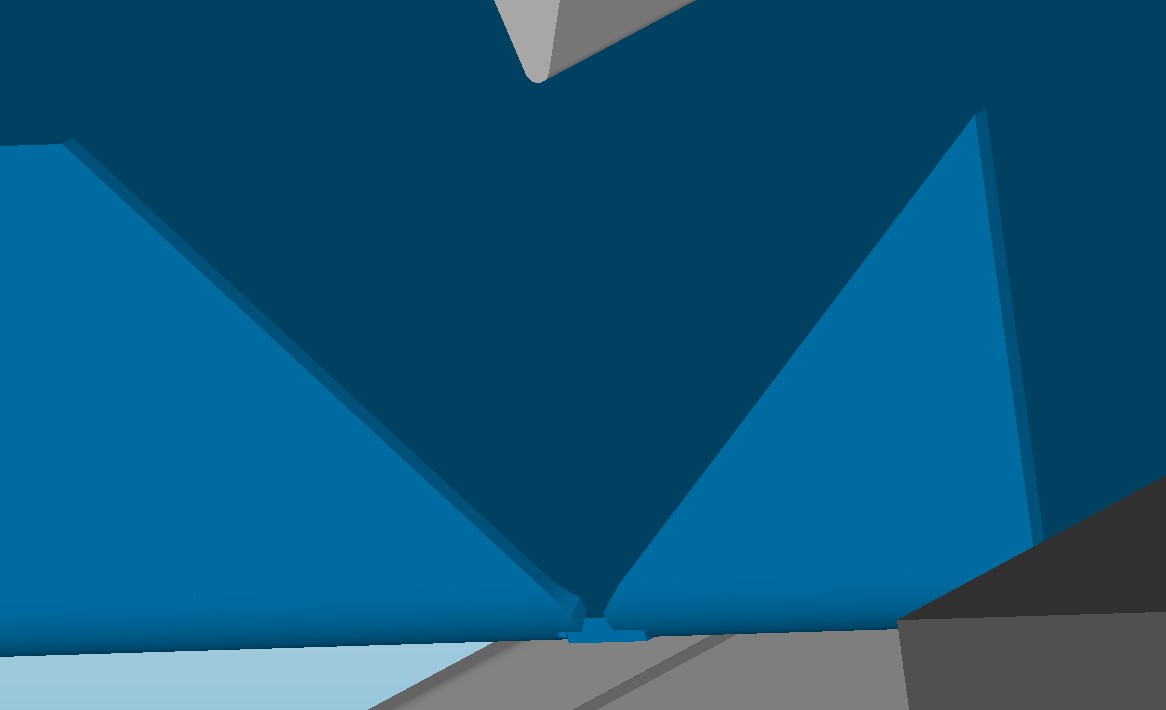
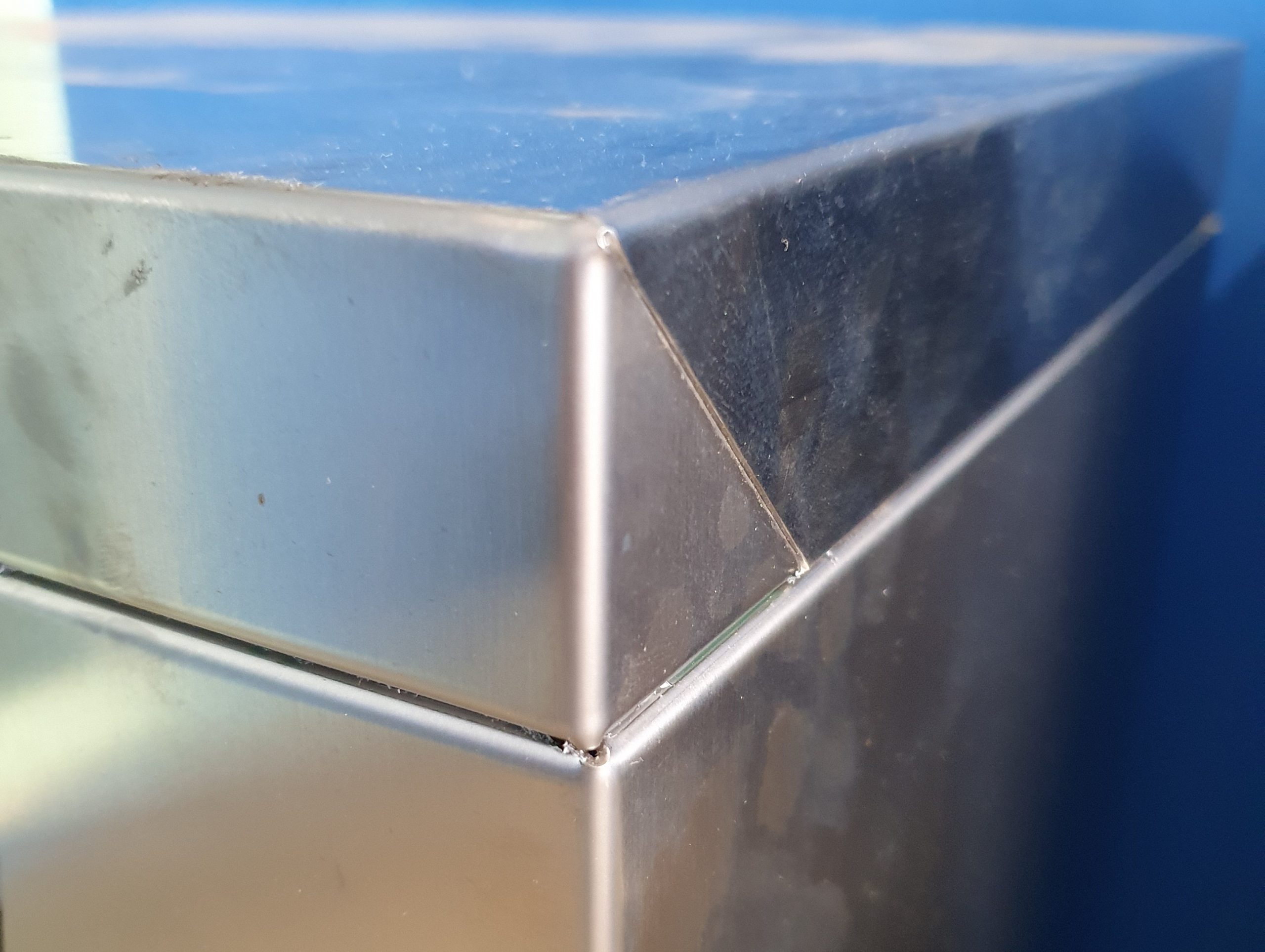
Piegatore e saldatore: due figure “quasi amiche”
Soprattutto nelle aziende terziste si manifesta ancora una volta l’importanza di un dialogo tra gli operatori che occupano i differenti stadi della filiera, nonché di sistemi della standardizzazione di processo.
La qualità, è noto, deve partire già dall’ufficio tecnico con strategie mirate a “imbastire” il lavoro nel migliore dei modi a partire dal calcolo degli sviluppi.
Se tra le competenze di un piegatore, già numerose, ci devono essere anche quelle di “sistemazione” di geometrie non proprio perfette, oltre ad avere bisogno di super-tecnici, l’azienda patirà flussi di lavoro meno fluidi, errori e necessarie rilavorazioni.
Un pezzo sviluppato male o senza i necessari accorgimenti atti a contrastare le fisiologiche problematiche che emergono durante la piegatura, sarà un pezzo più difficile da saldare, specie se a farlo sarà un robot…
Ma non basta.
Anche i singoli operatori alle presse piegatrici devono essere innanzitutto formati ma anche messi nelle condizioni di realizzare manufatti di alta qualità ripetibile nel tempo.
La svista può sempre capitare, ma il mercato di oggi, con la sua frenesia cronica, mal digerisce il fatto che lo stesso articolo possa essere svolto in tanti modi differenti quanto sono i piegatori e che debba essere sistemato manualmente per essere saldato.
Banalizzando ironicamente potremmo dire che “meno si sente martellare e più siamo stati bravi” perché ogni misura torna, ogni angolo combacia permettendo al saldatore di fare il mestiere per cui è qualificato!
Lo scoglio che dobbiamo abbattere è forse quello più complesso: la nostra mentalità.
Per poter raggiungere quel “settaggio mentale” verso la qualità totale, quella che non fa necessariamente costare di più un pezzo fatto bene rispetto ad uno fatto in maniera approssimativa.
Ogni singolo operatore è un ingranaggio fondamentale di un meccanismo chiamato impresa e, come dicono gli esperti di Lean, ogni collega che ricopre un ruolo successivo nella filiera rispetto al nostro va visto come “il cliente interno”.
Emiliano Corrieri